Tungsten Electrode Welding Performance
- Details
- Category: Tungsten Information
- Published on Tuesday, 22 March 2016 15:16
Tungsten electrode is widely used in TIG welding, plasma welding and other welding areas. The welding performance will directly affect their work performance and applications range. With the development of science and technology, not only has more stringent requirements on the electrode property, and environmentally friendly electrode material is an important evaluation criteria.
Compare arcing performance, high temperature burning performance and static characteristic curve of different electrodes to understand the performance of different welding electrodes.
Experimental electrodes are cerium tungsten electrodes (Ce-W electrode), zirconium tungsten electrode (Zr-W electrode), tungsten electrodes doped with three rare earth oxides (La-Ce-Y) and E3 electrode (15% La-0.8% Y-0.8 % Zr).
Arcing performance testing: After arcing performance testing found when I = 30A, tungsten electrodes doped with three rare earth oxides have all arcing. It has the minimum arc current, indicating having low work function, high electron emission capability. Ce-W electrode and Zr-W electrode arcing current is 35A and 40A, having medium work function and electron emission capability. But the E3 electrodes at I = 40A has not been successful arcing, and the data distribution is more dispersed, indicating unstable electron emission capability and high work function.
Burning loss experiment: four kinds of tungsten electrode after 20min arcing occur in varying degrees of oxidation. Ce-W electrode appeared slight rim ring, and E3 electrode tip burned significantly. After 30min minute burning treatment, Ce-W electrode and a Zr-W electrode has varying degrees rim. Pluralistic tungsten electrode has stable morphology. But the original shape of the E3 electrode has been completely destroyed.
After comparison can be found, tungsten electrodes doped with three rare earth oxides has better arcing performance, anti-burning performance and high temperature stability performance than E3 electrode, Zr-W electrode and Ce-W electrode, having better overall performance. The Ce-W and Zr-W has medium welding performance, and E3 electrode welding performance is the worst.
Tungsten Metals Supplier: Chinatungsten Online www.tungsten.com.cn | Tel.: 86 592 5129696; Fax: 86 592 5129797;Email:sales@chinatungsten.com |
Tungsten News & Prices, 3G Version: http://3g.chinatungsten.com | Molybdenum News & Molybdenum Price: http://news.molybdenum.com.cn |
Tungsten Trioxide Prepares Plate SCR Denitration Catalyst
- Details
- Category: Tungsten Information
- Published on Tuesday, 22 March 2016 13:51
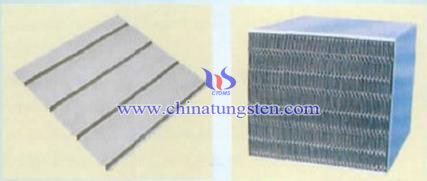
Tungsten Oxide Supplier: Chinatungsten Online www.tungsten-oxide.com | Tel.: 86 592 5129696; Fax: 86 592 5129797;Email:sales@chinatungsten.com |
Tungsten News & Prices, 3G Version: http://3g.chinatungsten.com | Molybdenum News & Molybdenum Price: http://news.molybdenum.com.cn |
SCR Denitration Catalyst Active Ingredient—Tungsten Trioxide
- Details
- Category: Tungsten Information
- Published on Tuesday, 22 March 2016 13:45
Tungsten Oxide Supplier: Chinatungsten Online www.tungsten-oxide.com | Tel.: 86 592 5129696; Fax: 86 592 5129797;Email:sales@chinatungsten.com |
Tungsten News & Prices, 3G Version: http://3g.chinatungsten.com | Molybdenum News & Molybdenum Price: http://news.molybdenum.com.cn |
Sulfur Dioxide Affects Tungsten Trioxide SCR Denitration Catalyst Activity
- Details
- Category: Tungsten Information
- Published on Monday, 21 March 2016 21:23
Tungsten Oxide Supplier: Chinatungsten Online www.tungsten-oxide.com | Tel.: 86 592 5129696; Fax: 86 592 5129797;Email:sales@chinatungsten.com |
Tungsten News & Prices, 3G Version: http://3g.chinatungsten.com | Molybdenum News & Molybdenum Price: http://news.molybdenum.com.cn |
Tungsten Trioxide Prepares Efficient Denitration Catalyst-- Dipping Method
- Details
- Category: Tungsten Information
- Published on Monday, 21 March 2016 21:20
Tungsten Oxide Supplier: Chinatungsten Online www.tungsten-oxide.com | Tel.: 86 592 5129696; Fax: 86 592 5129797;Email:sales@chinatungsten.com |
Tungsten News & Prices, 3G Version: http://3g.chinatungsten.com | Molybdenum News & Molybdenum Price: http://news.molybdenum.com.cn |
Tungsten Bronzes
- Details
- Category: Tungsten Information
- Published on Monday, 21 March 2016 18:27
Tungsten Powder Supplier: Chinatungsten Online tungsten-powder.com | Tel.: 86 592 5129696; Fax: 86 592 5129797;Email:sales@chinatungsten.com |
Tungsten News & Prices, 3G Version: http://3g.chinatungsten.com | Molybdenum News & Molybdenum Price: http://news.molybdenum.com.cn |
Cesium Tungsten Bronze Hydrothermal Synthesis
- Details
- Category: Tungsten Information
- Published on Monday, 21 March 2016 18:25
Tungsten Powder Supplier: Chinatungsten Online tungsten-powder.com | Tel.: 86 592 5129696; Fax: 86 592 5129797;Email:sales@chinatungsten.com |
Tungsten News & Prices, 3G Version: http://3g.chinatungsten.com | Molybdenum News & Molybdenum Price: http://news.molybdenum.com.cn |
Tungsten Oxide Inorganic Ceramic Film
- Details
- Category: Tungsten Information
- Published on Monday, 21 March 2016 16:57
Tungsten oxide inorganic ceramic film has high efficiency, high temperature resistance, high performance and stable chemical property. It has wide application field. Compared to organic film, it has following characteristics:
1.Tungsten oxide inorganic ceramic film has small pore size distribution which shows as normal distribution, 80% of them has error within ±10%. For example, the 0.05um film, among which 80% of pores are 0.049um-0.051um, it insures the stability of the applied film. This has a big difference from organic film which the pore size distributes uniformly.
2.Porosity of tungsten oxide can reach 35%-40% which ensures film flux.
3.Tungsten oxide inorganic ceramic film departure structure is more reasonable, there are supporting layer and separating layer, pore size is 5-10、1.0、0.6、0.2um, it becomes really gradient films which improve pollutant-resistance of film. The separating layer is even thinner which is easier to clean and wash. On the contrary, organic film is symmetric film, entry of film needs strict pre-treatment.
4.Tungsten oxide inorganic ceramic film has higher strength, it can resist pressure to 16bar, the supporting part can resist pressure to 30bar. It can ensure the dealing effects and stability in quality.
5.Tungsten oxide inorganic ceramic film has high insulating property.
6.Service life of tungsten oxide inorganic ceramic film is more than 5 years, however the organic film is only 3~6 months.
7.Chemical stability and thermal stability of tungsten oxide inorganic ceramic film is better than organic film, the strong acid, alkali and oxidizing agent can be used as detergent, steam sterilization can be applied directly. However, organic film can not be operated under the above mentioned conditions.
Tungsten Oxide Supplier: Chinatungsten Online www.tungsten-oxide.com | Tel.: 86 592 5129696; Fax: 86 592 5129797;Email:sales@chinatungsten.com |
Tungsten News & Prices, 3G Version: http://3g.chinatungsten.com | Molybdenum News & Molybdenum Price: http://news.molybdenum.com.cn |
Tungsten Copper Heat Sink Electrical Conductivity (2/2)
- Details
- Category: Tungsten Information
- Published on Monday, 21 March 2016 16:41
Under the intervention of external electric field, the outermost valence band electrons gain a little extra energy without violating the exclusion principle to reach many empty places within the band near. Compared with thermal excitation out-of-order, Excited electrons by the electric field and the field in the direction opposite to the momentum, it will produce a collective motion in the crystal, thereby forming current. For tungsten copper heat sink, due to different equivalent orbital and atom distance of W and Cu atoms, the band (or empty) overlap, constitutes a full conduction band, and has excellent electrical conductivity. For copper with divalent, its valence band is full band, which the valence band and a higher band overlaps, filled with electrons can occupy the vacated belt so that it has good conductivity; while tungsten with hexa-valence, its valence band is not full and the electrical conductivity is lower than copper phase. So this is a good proof of the conductivity of tungsten copper heat sink materials or conductivity depends on copper content.
The other influencing factor is porosity, which will hinder the movements of electrons. In other words, the higher porosity, the lower tungsten copper heat sink electrical conductivity. Due to tungsten copper is a kind of pseudo alloy, which composed of two kinds of metals with a big difference, there are a lot of interface and porosity between W and Cu grains. The experiment shows that tungsten copper composite material and its electrical conductivity were positively correlated with the density, the lower the density, the lower the conductivity. In addition, sintering temperature controlling is also important, electrical conductivity of tungsten copper has a sharp decline when it over-burnt. The main reasons comprise two, one is inside W phase has severe segregation and porosity, and as the main medium and Cu conductive phase may also undergone some degree of segregation, such that its penetration to the surface, the conductivity decreases with the decreasing content of Cu inside.
Tungsten Copper Supplier: Chinatungsten Online tungsten-copper.com | Tel.: 86 592 5129696; Fax: 86 592 5129797;Email:sales@chinatungsten.com |
Tungsten News & Prices, 3G Version: http://3g.chinatungsten.com | Molybdenum News & Molybdenum Price: http://news.molybdenum.com.cn |
Tungsten Copper Heat Sink Electrical Conductivity (1/2)
- Details
- Category: Tungsten Information
- Published on Monday, 21 March 2016 16:39
Except Rockwell hardness (HRB) of detection, it is essential that electrical conductivity measuring in tungsten copper composite materials as heat sink materials. Electrical conductivity is an important indicator to measure ability to conduct electricity of tungsten copper heat sink, which directly affects the final properties of products. The stronger ability to conduct electricity, the smaller electrical resistance, on the contrary, electrical resistance is greater. For hardness testing, if tungsten copper material over-burning, the inside Cu phase will exude and lead to the emergence of the hole, making the overall decrease in hardness; while the precipitation of Cu phase of segregation occurred, and thus will make the hardness not dropped significantly. Based on the theory, the relevant researchers have concluded that the most likely two factors tungsten copper electrical conductivity of heat sink, one is copper content, the other is the porosity.
Theoretically, tungsten copper composite material is composed of tungsten (W) and copper (Cu). W phase has higher hardness and melting point, lower electrical conductivity; on the contrary, Cu has lower hardness and melting point, but it has excellent electrical conductivity. Therefore, it can be speculate that electrical conductivity of tungsten copper heat sink material depends on how much copper content, the higher the copper content, the corresponding tungsten-copper composite conductivity is higher. From chemical energy band, different metal has different equivalent orbital and atom distance, which band (or empty) overlap, constitutes a full conduction band, and easily to have a metallic conductivity. So as long as there is not full of the conduction band, whether it itself is not full band, or the empty band and full band formed by overlapping unfilled band, under the action of external electric field will form a directional flow of electrons, thereby such that the material has conductivity.
Tungsten Copper Supplier: Chinatungsten Online tungsten-copper.com | Tel.: 86 592 5129696; Fax: 86 592 5129797;Email:sales@chinatungsten.com |
Tungsten News & Prices, 3G Version: http://3g.chinatungsten.com | Molybdenum News & Molybdenum Price: http://news.molybdenum.com.cn |