Aluminum Oxide Improves Tungsten Trioxide SCR Denitration Catalyst Activity
- Details
- Category: Tungsten Information
- Published on Monday, 28 March 2016 15:56
Tungsten Oxide Supplier: Chinatungsten Online www.tungsten-oxide.com | Tel.: 86 592 5129696; Fax: 86 592 5129797;Email:sales@chinatungsten.com |
Tungsten News & Prices, 3G Version: http://3g.chinatungsten.com | Molybdenum News & Molybdenum Price: http://news.molybdenum.com.cn |
CsxWO3 Influence on NIR Shielding Property
- Details
- Category: Tungsten Information
- Published on Friday, 25 March 2016 19:40
Near-infrared(NIR, IR-A DIN), is defined by the water absorption, and commonly used in fiber optic telecommunication because of low attenuation losses in the SiO2 glass (silica) medium. Image intensifiers are sensitive to this area of the spectrum. Examples include night vision devices such as night vision goggles.
Recently, shielding not only ultraviolet rays but also infrared rays has been attracted attentions in terms of saving resource and energy and creating comfortable life space. Cs doped tungsten bronze (CsxWO3) which has suitable amounts of free electrons in crystal is one of the candidate materials of inorganic infrared rays shielding materials, since it can shield ultraviolet and infrared rays by interband transition and plasma oscillation of free electrons, respectively. Nanoparticles of CsxWO3 particles were synthesized by solvothermal reaction of WCl6 and CsOH・H2O in ethanol and ethanol aqueous solutions at 200 ℃ for 12-47 h. After that, CsxWO3 particles were heated in 500 ml/min NH3 gas flow at 400 ℃ for 1 h. Sheet-like and rod-like nanopartricles of CsxWO3 were synthesized in ethanol and 42.9 vol% ethanol aqueous solution at 200 ℃, respectively. The samples formed in 42.9 vol% ehanol aqueous showed higer crystallinity but lower Cs/W atomic ratio than those in ethanol. Sheet-like particles showed higher visible light transparency, while rod-like particles showed more excellent infrared shielding properties, indicating that rod-like particles were more suitable for shielding infrared rays. Moreover, the visible light transparency and infrared shielding properties could be improved by improving the dispersion state of the particles by agitating with ZrO2 beads. The electric conductivity of the pressed pellet of rod-like particles could be increased by heating in NH3 gas atmosphere at 400 ℃.
Tungsten Oxide Supplier: Chinatungsten Online www.tungsten-oxide.com | Tel.: 86 592 5129696; Fax: 86 592 5129797;Email:sales@chinatungsten.com |
Tungsten News & Prices, 3G Version: http://3g.chinatungsten.com | Molybdenum News & Molybdenum Price: http://news.molybdenum.com.cn |
Cs(x)WO3/ZnO Nanocomposite as Smart Coating
- Details
- Category: Tungsten Information
- Published on Friday, 25 March 2016 19:33
A novel CsxWO3/ZnO smart coating was proposed to achieve multiple functions, such as heat insulation, photodecomposition of toxic NO gas, blocking of harmful UV light, etc. In this composite coating, CsxWO3 nanorods were used as a NIR and UV light shielding material while ZnO nanoparticles were utilized as a photocatalyst and a material to enhance visible light transmittance and block UV light. When the mass ratio of CsxWO3/ZnO was 1, the composite coating possessed a very good visible light transmittance of over 80% and an excellent UV-shielding ability. This novel coating showed heat insulation that is superior to the ITO coating and photocatalytic decontamination of NO gas that is superior to the standard TiO2 (P25). The proposed CsxWO3/ZnO smart coating is a promising material not only for energy saving but also for environmental cleanup.
Tungsten Oxide Supplier: Chinatungsten Online www.tungsten-oxide.com | Tel.: 86 592 5129696; Fax: 86 592 5129797;Email:sales@chinatungsten.com |
Tungsten News & Prices, 3G Version: http://3g.chinatungsten.com | Molybdenum News & Molybdenum Price: http://news.molybdenum.com.cn |
CsxWO3 Nanoparticles Content Effect
- Details
- Category: Tungsten Information
- Published on Friday, 25 March 2016 19:30
Tungsten Oxide Supplier: Chinatungsten Online www.tungsten-oxide.com | Tel.: 86 592 5129696; Fax: 86 592 5129797;Email:sales@chinatungsten.com |
Tungsten News & Prices, 3G Version: http://3g.chinatungsten.com | Molybdenum News & Molybdenum Price: http://news.molybdenum.com.cn |
Tungsten Bronzes Near Infrared Cut-Off Characteristics
- Details
- Category: Tungsten Information
- Published on Friday, 25 March 2016 19:24
The various nanoparticles have been investigating the continuous and new methods to reduce solar heat as it ensures a potentially low-cost and high-productivity solution. Not only does it needs high transmittance of ultraviolet radiation but also achieves complete shielding of infrared solar radiation can be used for solar control windows. In the other word, an effective IR absorbent should have high absorbance as well as a broad working wavelength. A well known the kinds of materials to realize the purpose is the nanoparticles of transparent oxide conductors with heat-ray cut-off effect such as tin doped indium oxide (ITO) and antimony doped tin oxide (ATO). They also are well known to provide highly transparent solar filters to absorb heat-ray by the effect of the plasma vibration of the free electrons, as typically observed in gold and silver nanoparticle solution. However, ITO can only shield the IR wavelength ranges longer than 1500 nm as well as indium is an expensive metal resource. In recent years, for practical application, tungsten bronzes actively have been investigating due to their interesting electro-optics, photochromic, electrochromic, and superconducting properties. Tungsten trioxide (WO3) has a wide band gap of 2.6-2.8 eV5 and is transparent in the visible and NIR ranges. A metallic conductivity and a strong NIR wavelength absorption can be induced when free electrons are introduced into crystals by either decreasing the oxygen content or by adding ternary elements. The oxygen deficiency in tungsten oxides leads to a complex-ordered structure known as the Magneli structure, while the ternary addition of the positive ions leads to the tungsten bronze structure. In other words, tungsten bronzes MxWO3 with doping small ions such as H+, Ag+, Li+, Na+, K+ and Cs+ into WO3 have better optical and electrical properties. It has been reported that the tungsten bronzes with the hexagonal phase are of particular interest in the application of electrochromic devices owing to the relatively high diffusion coefficients of hydrogen ions and metal ions compared with those of the orthorhombic phase and pure WO3.
Tungsten Oxide Supplier: Chinatungsten Online www.tungsten-oxide.com | Tel.: 86 592 5129696; Fax: 86 592 5129797;Email:sales@chinatungsten.com |
Tungsten News & Prices, 3G Version: http://3g.chinatungsten.com | Molybdenum News & Molybdenum Price: http://news.molybdenum.com.cn |
Tungsten Carbide Staggered-edge End Mill (2/2)
- Details
- Category: Tungsten Information
- Published on Friday, 25 March 2016 17:38
Generally, due to the cutting force of down milling, the workpiece is pressed against the table so that it is a priority, unless there is a thread gap or other problems considering up milling. Based on this theory, the relevant researchers have proposed the idea of tungsten carbide staggered-edge end mill. Compared with conventional D-edge end mills, tungsten carbide staggered-edge end mill has D-proximal portion, near the handle L-interleaved design, which the original design concept is intended to apply to new carbon fiber composite material. The specific design schematic diagram shown as follow:
From the schematic above we can clearly see that tungsten carbide staggered-edge end mill has two parts, the workpiece processed should be in the middle area between the two cutting edges. Due to the cutting edge is used in the proximal portion of the edge right-handed, left-handed edge near the handle of the staggered design, the lower section of the right-handed cutting edge of the lower surface of the workpiece can be milled, while at the same time under the surface but also by the upward the cutting force; on the contrary, the upper surface of the upper left-hand cutting edge end mill for milling a workpiece and produces its downward cutting force.
In the overall cutting process, the mill closely pressed against the workpiece and feed, so the fiber layer top and bottom surfaces of the material are more likely to be cut off, which effectively avoid the workpiece upper and lower surfaces tears, burrs and other processing defects. In addition, Since the upper and lower surfaces of the workpiece by the cutting force component perpendicular to the contrary, the axial force is reduced and the overall direction of the cutting force is moderate, toward the inside of the workpiece, which is conducive to smoothly throughout the cutting process, but also inhibit stratified of the inner portion of the workpiece. It is possible to improve processing quality carbon fiber composite material to a certain extent. The milling test shows that under the same cutting conditions, grain wear is the main pattern of tungsten carbide staggered-edge end mill. And compared with conventional tungsten carbide end mills, it has better wear resistance and service life.
Tungsten Carbide Supplier: Chinatungsten Online tungsten-carbide.com.cn | Tel.: 86 592 5129696; Fax: 86 592 5129797;Email:sales@chinatungsten.com |
Tungsten News&Tungsten Prices, 3G Version: http://3g.chinatungsten.com | Molybdenum News & Molybdenum Price: http://news.molybdenum.com.cn |
Tungsten Carbide Staggered-edge End Mill (1/2)
- Details
- Category: Tungsten Information
- Published on Friday, 25 March 2016 17:35
Tungsten carbide staggered-edge end mill is usually composed of tungsten carbide (WC) + cobalt (Co) and other additives by compacting and sintering. Tungsten carbide mills has broad scope of application, such as CNC machining, engraving and some ordinary milling machining for hard material with simple shape of heat-treated material. According to the shape of edge, it can be specifically divided into integrated tungsten carbide mills, tungsten carbide cylindrical mills, tungsten carbide facing mills, tungsten carbide shank-groove mills, tungsten carbide helical mills, tungsten carbide staggered-edge end mills, tungsten carbide side cutter, tungsten carbide end mills, tungsten carbide saw blade mills, tungsten carbide angled mills and so on.
Generally, tungsten carbide staggered-edge end mill used for stepped surface machining grooves and other parts. The edge located in the circle and surface, which can not be fed in the axial direction only when the legislation is available on the cutter and the axial center of the edge through the end of the feed. This makes the milling edge design focus shifted to how to reduce the axial thrust generated by the tool in the cutting process in case of restraining layer, tear and burrs. Viewed from the direction of feeding and rotating of tungsten carbide mills for the workpiece, it mainly includes two kinds, one is up milling, the other is down milling. The so-called up milling means that the feed direction of the rotational direction of the cutter and cutting the same at the beginning of the milling cutter on the workpiece until the last; while the opposite direction of feed milling cutter rotation and the cutting, before beginning the milling cutter must be some slippage on the workpiece, cutting thickness from scratch when cutting until the end of the maximum thickness.
Tungsten Carbide Supplier: Chinatungsten Online tungsten-carbide.com.cn | Tel.: 86 592 5129696; Fax: 86 592 5129797;Email:sales@chinatungsten.com |
Tungsten News&Tungsten Prices, 3G Version: http://3g.chinatungsten.com | Molybdenum News & Molybdenum Price: http://news.molybdenum.com.cn |
Factors Affect Tungsten Trioxide SCR Denitration Catalyst Activity
- Details
- Category: Tungsten Information
- Published on Friday, 25 March 2016 14:46
Tungsten Oxide Supplier: Chinatungsten Online www.tungsten-oxide.com | Tel.: 86 592 5129696; Fax: 86 592 5129797;Email:sales@chinatungsten.com |
Tungsten News & Prices, 3G Version: http://3g.chinatungsten.com | Molybdenum News & Molybdenum Price: http://news.molybdenum.com.cn |
Preparing Tungsten Trioxide Contained Denitration Catalyst Active Mother Liquor
- Details
- Category: Tungsten Information
- Published on Friday, 25 March 2016 14:44
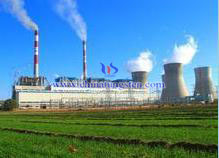
Tungsten Oxide Supplier: Chinatungsten Online www.tungsten-oxide.com | Tel.: 86 592 5129696; Fax: 86 592 5129797;Email:sales@chinatungsten.com |
Tungsten News & Prices, 3G Version: http://3g.chinatungsten.com | Molybdenum News & Molybdenum Price: http://news.molybdenum.com.cn |
Tungsten Trioxide Controls SCR Denitration Catalyst Deactivation
- Details
- Category: Tungsten Information
- Published on Thursday, 24 March 2016 17:26
Tungsten Oxide Supplier: Chinatungsten Online www.tungsten-oxide.com | Tel.: 86 592 5129696; Fax: 86 592 5129797;Email:sales@chinatungsten.com |
Tungsten News & Prices, 3G Version: http://3g.chinatungsten.com | Molybdenum News & Molybdenum Price: http://news.molybdenum.com.cn |