MnOx/WO3/TiO2 Denitration Catalyst
- Details
- Category: Tungsten Information
- Published on Wednesday, 06 April 2016 16:16
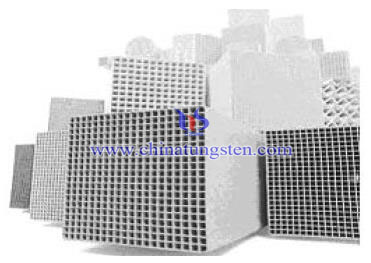
Tungsten Oxide Supplier: Chinatungsten Online www.tungsten-oxide.com | Tel.: 86 592 5129696; Fax: 86 592 5129797;Email:sales@chinatungsten.com |
Tungsten News & Prices, 3G Version: http://3g.chinatungsten.com | Molybdenum News & Molybdenum Price: http://news.molybdenum.com.cn |
WO3 SCR Denitration Catalyst Facing Technical Difficulty--Low Temperature Denitration
- Details
- Category: Tungsten Information
- Published on Wednesday, 06 April 2016 16:12
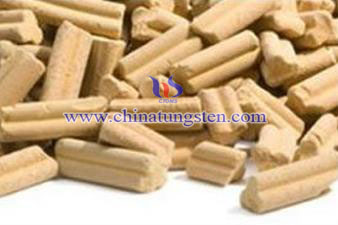
Tungsten Oxide Supplier: Chinatungsten Online www.tungsten-oxide.com | Tel.: 86 592 5129696; Fax: 86 592 5129797;Email:sales@chinatungsten.com |
Tungsten News & Prices, 3G Version: http://3g.chinatungsten.com | Molybdenum News & Molybdenum Price: http://news.molybdenum.com.cn |
Recover Vanadium from WO3 SCR Denitration Catalyst
- Details
- Category: Tungsten Information
- Published on Wednesday, 06 April 2016 16:09
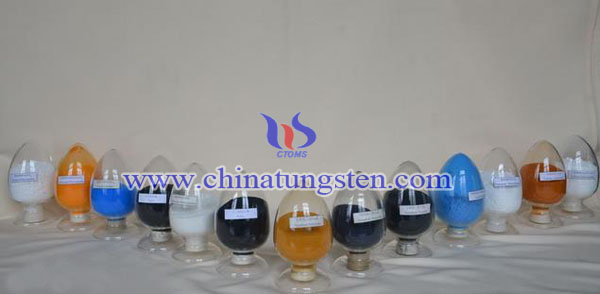
Tungsten Oxide Supplier: Chinatungsten Online www.tungsten-oxide.com | Tel.: 86 592 5129696; Fax: 86 592 5129797;Email:sales@chinatungsten.com |
Tungsten News & Prices, 3G Version: http://3g.chinatungsten.com | Molybdenum News & Molybdenum Price: http://news.molybdenum.com.cn |
Tungsten Copper Sintering Technologies Comparison (2/2)
- Details
- Category: Tungsten Information
- Published on Wednesday, 06 April 2016 16:05
In order to improve mixed-pressing, relevant scholars uses activated agent (Ni, Pd and other activated elements) to increase the solubility of W in liquid phase, which is beneficial for the sintering process. However the additives have a bad influence on the electrical and thermal conductivity of tungsten copper products. Pressure sintering is a kind of secondary processing after sintering, especially for the conditions that one-step forming can not meet the requirements. Although hot pressing, repressing and re-sintering and HIP (Hot Isostatic Pressing) can remarkably improve the properties of tungsten copper composite material, they are limited by the costs and the efficiency. In addition, using hammering or cold rolling of tungsten-copper composite material for secondary processing can greatly increase the density and mechanical properties of the material. But when the content of W is higher, the ductility of tungsten copper will decrease and the difficulty of machining will increase.
Spark Plasma Sintering (SPS), which is also known as Plasma Activated Sintering (PAS) or Field Assisted Sintering Technology (FAST). According to different powder media, SPS can be divided into conductive and non-conductive, there is a big difference in mechanism between them. Generally, conductive SPS will produce a large amount of Joule heat generated by DC pulse current graphite mold; and the current through the powder will induce electric discharge between powder particles and arouse plasma. With the increasing density of plasma, High-speed reverse movement of the particle surface of the particles have a greater impact, so that the gas adsorption of escape or break an oxide film, so that the surface to be purified and activated, will be conducive to sintering. However, instantaneous high temperature generated by the discharge causes evaporation and melting of the grain surface, the grain at the point of contact to form sintered neck.
Tungsten Copper Supplier: Chinatungsten Online tungsten-copper.com | Tel.: 86 592 5129696; Fax: 86 592 5129797;Email:sales@chinatungsten.com |
Tungsten News & Prices, 3G Version: http://3g.chinatungsten.com | Molybdenum News & Molybdenum Price: http://news.molybdenum.com.cn |
Tungsten Copper Sintering Technologies Comparison (1/2)
- Details
- Category: Tungsten Information
- Published on Wednesday, 06 April 2016 16:03
There are many kinds of tungsten copper sintering technologies, such as conventional infiltration, mixed-pressing, pressure sintering and new SPS (Spark Plasma Sintering), etc, which have their own advantages and disadvantages. Next, we analyze these different sintering technologies by the principle and the applications. First of all, infiltration, which is called melt immersion, is the most widely used in tungsten copper products currently. It is obtained by adding a small amount of tungsten powder or copper powder compacts made of tungsten powder and tungsten and copper infiltrated compacts stacked together, and thereafter sintered at a temperature above the melting point of copper and under reducing atmosphere or vacuum.
In the process of sintering, copper in a molten state to rely on capillary action infiltrated tungsten skeleton, two sintering and infiltration step can also be performed separately. Infiltration has many advantages, such as high density, excellent sintering properties and electrical and thermal conductivity, good arc ablation resistance. But liquid copper barely rely on capillary forces infiltrated tungsten skeleton, this will lead to coarse and uneven distribution of copper particles sintered tungsten particles at high temperatures easily grew up together. In addition, after infiltration machined to remove excess copper and will increase costs and reduce the yield.
Mixed - pressing sintering process is one of the most conventional powder metallurgy, which basic process is preparation →ball milling → compacting →sintering. Sintering can be also divided into two parts, one is solid phase sintering (temperature lower than the melting point of Cu), the other is liquid phase sintering (temperature higher than the melting point of Cu). Since the solid solubility in the liquid phase W Cu is small, the material can not be conveyed by dissolution and precipitation particles rounded manner, and tungsten and copper infiltration is poor, it is difficult to achieve densification.
Tungsten Copper Supplier: Chinatungsten Online tungsten-copper.com | Tel.: 86 592 5129696; Fax: 86 592 5129797;Email:sales@chinatungsten.com |
Tungsten News & Prices, 3G Version: http://3g.chinatungsten.com | Molybdenum News & Molybdenum Price: http://news.molybdenum.com.cn |
Tungsten Alloy Shielding For Radiation Pasteurization
- Details
- Category: Tungsten Information
- Published on Tuesday, 05 April 2016 18:51
Tungsten alloy shielding for radiation pasteurization is used for shielding the radiation released from the process of radiation pasteurization. Radiation pasteurization is a technology that uses ionizing radiation to kill the causative agent (including virus) to achieve the purpose of toxicity elimination. Its radioactive source is Co60 radioactive source which can release γ rays from a decay. The pests and bacteria hided in the fruits and vegetables would suffer from the physiological function changes and lost the ability to grow and develop after being exposed to these γ rays. So far, radiation pasteurization is widely used for the disinfection of various kinds of medical apparatus and instruments, such as catheters, cannulas, bandages, dressings, suture materials, surgical instruments, injection equipments, blood transfusion equipments, artificial kidney dialyzer, biological tissues for transplantation. It also can be used in pharmaceutical, food, agricultural products and customs, etc.
Co60 is a radioactive isotope of cobalt with a half-life of 5.27 years. Co60 decays by beta decay to the isotope nickel-60. The activated nickel nucleus emits two gamma rays with energies of 1.17 and 1.33 MeV. After entering a living mammal, some of the Co60 are taken up by tissues, mainly the liver, kidneys, and bones, where the prolonged exposure to gamma radiation can cause cancer. Low levels of gamma rays cause a stochastic health risk, which for radiation dose assessment is defined as the probability of cancer induction and genetic damage. High doses produce deterministic effects, which is the severity of acute tissue damage that is certain to happen.
Tungsten alloy shielding for radiation pasteurization is mainly used for shielding the β and γ radiation released from the process of radiation pasteurization. Tungsten alloy shielding mainly uses high gravity alloy which has the characteristics of high density and innocuity. Therefore tungsten alloy shielding for radiation pasteurization has excellent shielding performance to shield the β and γ radiation generated during the process of radiation pasteurization, to avoid resulting in radiation damage. In addition, tungsten alloy shielding for radiation pasteurization is more environmentally friendly than some traditional shielding materials, such as lead, and will not pollute the environment.
Tungsten Alloy Supplier: Chinatungsten Online www.tungsten-alloy.com | Tel.: 86 592 5129696; Fax: 86 592 5129797;Email:sales@chinatungsten.com |
Tungsten News & Prices, 3G Version: http://3g.chinatungsten.com | Molybdenum News & Molybdenum Price: http://news.molybdenum.com.cn |
Tungsten Alloy Nuclear Radiation Detector
- Details
- Category: Tungsten Information
- Published on Tuesday, 05 April 2016 18:47
Tungsten alloy nuclear radiation detector, also known as tungsten alloy detecting element, is used to detect nuclear radiation and its properties(including the types, strength ,the energy and nuclear lifetime of nuclear radiation) by utilizing radiation rays to interact with substances to induce a series of effects(such as luminescence phenomenon, ionization effect, physical and chemical changes).It usually made up of a detector, a display unit, a measuring element and a power source, and mainly includes semiconductor detector, gas ionization detector and scintillation detector. Tungsten alloy nuclear radiation detector is widely used in public places, laboratories, quarries, metal processing plants, oil fields and oil pipeline equipment and other departments, for inspection of the radioactivity of underground drill pipe and equipment and building materials, local radiation leakage and contamination and landfill and garbage dump which has the risk of nuclear radiation.
Nuclear radiation, also known as ionization radiation, is a microscopic particle released from the process of a nucleus changes from a structure (or an energy state) to another kind of structure (or another energy state) to cause ionization or excitation material. The types of nuclear radiation include gamma rays, α rays and βrays. Gamma ray is extremely high-frequency electromagnetic radiation and thus consists of high-energy photons. It is penetrating, and can lead to damage at a cellular level, resulting in diffuse damage throughout the body;α rays are generally produced in the process ofα decay. It can enter the body to destroy the human tissues by being inhaled, ingested or injected, αradiation is the most destructive form of ionizing radiation; β rays are able to penetrate living tissues to a certain extent and can change the structure of struck molecules(such as DNA molecules). In most cases, such change can be considered to be damage, with results possibly as severe as cancer or death.
Tungsten alloy nuclear radiation detector uses the tungsten alloy material with high density. Because the radiation shielding capability of a metal material increases with the increasing of its density, so the tungsten alloy nuclear radiation detector has excellent radiation shielding capability. When using a tungsten alloy nuclear radiation detector, the tungsten alloy can absorb and shield the nuclear radiation in a high degree to avoid them doing harm to human body while reaching the goal of nuclear radiation detection.
Tungsten Alloy Supplier: Chinatungsten Online www.tungsten-alloy.com | Tel.: 86 592 5129696; Fax: 86 592 5129797;Email:sales@chinatungsten.com |
Tungsten News & Prices, 3G Version: http://3g.chinatungsten.com | Molybdenum News & Molybdenum Price: http://news.molybdenum.com.cn |
Tungsten Alloy γ-Ray Level Gage
- Details
- Category: Tungsten Information
- Published on Tuesday, 05 April 2016 18:43
Tungsten alloy γ-ray level gage, also known as tungsten alloy γ-ray content gauge or tungsten alloy γ-ray material level meter, is a measuring instrument for mass level by using its characteristic of the strength of rays suffered by detector is various from the levels. It is also an isotope material level meter. Tungsten alloy γ-ray level gage mainly consists of radiation source, detector and transducer. Generally, the radiation source is Co60 or Cs137 radioactive source contained by tungsten alloy container. The function of detector is to detect the rays, and then change the light signals produced by it into electrical signals. While the electrical signals are transformed into contact signals or standard current signals and output to the DOS and other peripheral equipments by transducer. At present, many advanced tungsten alloy γ-ray level gage collectively call detector and transducer as detector.
Tungsten alloy γ-ray level gage has the characteristic of easy operation, simple structure and high measurement accuracy, is particularly useful for measurement of stuff level in harsh conditions(including high pressure, high temperature, high viscosity, high corrosivity, high toxicity and smoke concentration, boiling conditions)or in complicated conditions where general instruments can't or is difficult to use, or for liquid level measurement in the high pressure container which exists liquid drop and liquid surface fluctuation. The material to be measured can be powder, granular solid or liquid. Tungsten alloy γ-ray level gage is mainly used in papermaking, petrochemical engineering, coal industry, mining, steel, thermal power industry, etc. It is only applies to the measurement of two-phase interface.
Due to theγ rays released from theγ-ray level gage can cause DNA and cellular damage, chromosome aberration, chronic and acute radiation sickness, cancer induced. Theγ-ray level gage usually is tungsten alloy γ-ray level gage whose radiation source container is tungsten alloy container. Tungsten alloy γ-ray level gage has high density and great radiation shielding performance, which make it absorb and shield γ rays in a high degree, reducing the harm on human body, to protect the human from the radiation. Moreover, it is environmentally friendly.
Tungsten Alloy Supplier: Chinatungsten Online www.tungsten-alloy.com | Tel.: 86 592 5129696; Fax: 86 592 5129797;Email:sales@chinatungsten.com |
Tungsten News & Prices, 3G Version: http://3g.chinatungsten.com | Molybdenum News & Molybdenum Price: http://news.molybdenum.com.cn |
Typical Recovery Process of Waste WO3 Cellular SCR Denitration Catalyst
- Details
- Category: Tungsten Information
- Published on Tuesday, 05 April 2016 18:09
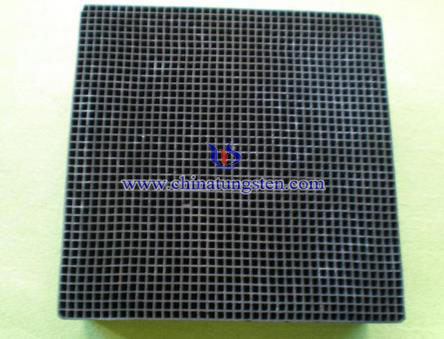
Tungsten Oxide Supplier: Chinatungsten Online www.tungsten-oxide.com | Tel.: 86 592 5129696; Fax: 86 592 5129797;Email:sales@chinatungsten.com |
Tungsten News & Prices, 3G Version: http://3g.chinatungsten.com | Molybdenum News & Molybdenum Price: http://news.molybdenum.com.cn |
WO3 SCR Waste Denitration Catalyst Recovery Process
- Details
- Category: Tungsten Information
- Published on Tuesday, 05 April 2016 18:06
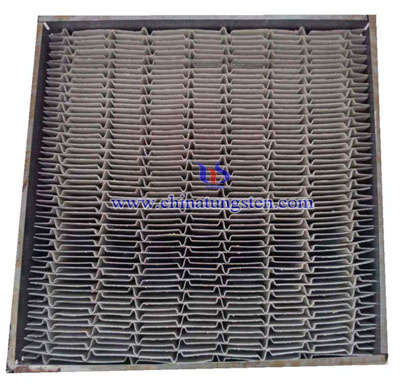
3. Two times of electrolysis with strong electrolyte solution→ adjust pH with ammonium to precipitate vanadium. The industrial application and energy consumption of this process is unknown; besides, W, Ti and other components cannot be separated for recycling.
Tungsten Oxide Supplier: Chinatungsten Online www.tungsten-oxide.com | Tel.: 86 592 5129696; Fax: 86 592 5129797;Email:sales@chinatungsten.com |
Tungsten News & Prices, 3G Version: http://3g.chinatungsten.com | Molybdenum News & Molybdenum Price: http://news.molybdenum.com.cn |