Why Does the Cold Resistance of EB Tungsten Filament Unqualified?
- Details
- Category: Tungsten Information
- Published on Thursday, 14 April 2016 17:36
In China, the main material of EB (electron beam) tungsten filament is Double spiral wire. Double spiral wire can heating the cathode evenly. What’s more, the Double spiral wire can eliminate the influence of the magnetic field which is cause by the cathode electron beam. However, the process to make the Double spiral wire is more complex, if the users cannot operate dissolution of molybdenum correctly, it will cause a lot of substandard products. Against to the unqualified phenomenon of the cold resistance of EB tungsten filament, people should try to improve the process of molybdenum core wire dissolution.
Molybdenum core wire dissolution is a pure chemical reaction process. Molybdenum has a strong chemical stability, so that people used a mixture of concentrated sulfuric acid, concentrated nitric acid and water as an etching solution. During the reaction, the temperature and time of the reaction should be to control by a strict operation. In addition, people should also pay attention to the phenomenon of the reaction, the reaction speed would change for the different temperature and the seasons. Due to the low temperatures in winter, the reaction is difficult to control the, it is more likely to cause the cold resistance of EB tungsten filament unqualified.
There exist the remaining acid in the surface of EB tungsten filament without washing cleanly. Oxidation would make the tails of EB tungsten filament become black. Molybdenum wire of cold resistance of EB tungsten filament is mainly caused by the incomplete reaction.
The cold resistance of EB tungsten filament unqualified will produce a lot of waste, causing serious environmental pollution. Therefore, people need to understand the reason to reduce pollution and improve the ecological environment.
Tungsten Metals Supplier: Chinatungsten Online www.tungsten.com.cn | Tel.: 86 592 5129696; Fax: 86 592 5129797;Email:sales@chinatungsten.com |
Tungsten News & Prices, 3G Version: http://3g.chinatungsten.com | Molybdenum News & Molybdenum Price: http://news.molybdenum.com.cn |
Maintenance of EB Tungsten Filament of SEM
- Details
- Category: Tungsten Information
- Published on Thursday, 14 April 2016 17:33
SEM (scanning electron microscope) of the electron microscope has a lower degree of vacuum, and a large beam current. Therefore, the life time of tungsten filament of SEM is limited. Generally speaking, it can last for only a few dozen hours. The life time of tungsten filament of SEM has a direct impact on the cost of the instruments operation and the effective time of operation. Consequently, it would cause more pollution and other adverse consequences. Therefore, the tungsten filament of SEM needs a regular maintenance or repair. Users can take the following measures to maintain tungsten filament and extend the life time of instruments.
Firstly, check the condition of tungsten filament, if possible, users should put the component of tungsten filament on the dissecting microscope to check again. The rate of evaporation of the filament surface is related to the temperature of the filament, users can adjust a higher height to decrease the temperature of the filament. The material can choose a thick filament gasket. And then users should adjust the current of tungsten filament. During the maintenance of tungsten filament of SEM, users should check the saturation of the filament timely. Under an unsaturated condition, current of tungsten filament should be adjusted to the saturated condition. Finally, keep the vacuum degree of Scanning electron microscope lens.
Other measures to maintain tungsten filament of SEM are: 1. Before exchange the filament, users should remove dampness and air of the new filament. 2. Do not switch filament frequently in the daily work.
Tungsten Metals Supplier: Chinatungsten Online www.tungsten.com.cn | Tel.: 86 592 5129696; Fax: 86 592 5129797;Email:sales@chinatungsten.com |
Tungsten News & Prices, 3G Version: http://3g.chinatungsten.com | Molybdenum News & Molybdenum Price: http://news.molybdenum.com.cn |
Tungsten bronze (TB) Crystal Material Molecular Design
- Details
- Category: Tungsten Information
- Published on Thursday, 14 April 2016 17:31
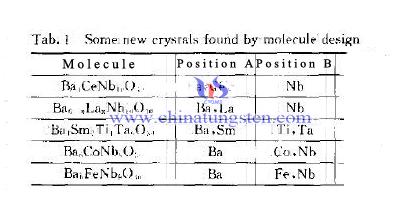
Tungsten Oxide Supplier: Chinatungsten Online www.tungsten-oxide.com | Tel.: 86 592 5129696; Fax: 86 592 5129797;Email:sales@chinatungsten.com |
Tungsten News & Prices, 3G Version: http://3g.chinatungsten.com | Molybdenum News & Molybdenum Price: http://news.molybdenum.com.cn |
Prevent WO3 Waste Flue Gas Denitration Catalyst Regeneration Pollution
- Details
- Category: Tungsten Information
- Published on Thursday, 14 April 2016 17:15
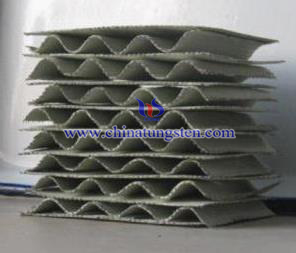
Tungsten Oxide Supplier: Chinatungsten Online www.tungsten-oxide.com | Tel.: 86 592 5129696; Fax: 86 592 5129797;Email:sales@chinatungsten.com |
Tungsten News & Prices, 3G Version: http://3g.chinatungsten.com | Molybdenum News & Molybdenum Price: http://news.molybdenum.com.cn |
Commercial Recovering Value of Waste WO3 Denitration Catalyst
- Details
- Category: Tungsten Information
- Published on Thursday, 14 April 2016 17:12

Tungsten Oxide Supplier: Chinatungsten Online www.tungsten-oxide.com | Tel.: 86 592 5129696; Fax: 86 592 5129797;Email:sales@chinatungsten.com |
Tungsten News & Prices, 3G Version: http://3g.chinatungsten.com | Molybdenum News & Molybdenum Price: http://news.molybdenum.com.cn |
What is JEOL EB Tungsten Filament?
- Details
- Category: Tungsten Information
- Published on Thursday, 14 April 2016 15:34
The full name of JEOL is Japanese Electron Optics Laboratory. After decades of exploration and research by the world’s top scientific instrument manufacturers, they create the brand JEOL. Nowadays, JEOL products are widely applied in the fields of medicine, biology, biochemistry, agriculture, material science, metallurgy, chemical, petroleum, pharmaceuticals, semiconductor and electronics. EB (electron beam) tungsten filament of JEOL is known to the Chinese businessmen. So far, there are more than 2000 users of JEOL in China. In China, EB tungsten filament of JEOL is used by a key laboratory sciences sector, research institutes, universities, medical institutions, government agencies and enterprises.
EB tungsten filament of JEOL has a strong vacuum system, which is widely applied in a SEM (scanning electron microscope). EB tungsten filament of JEOL uses the newest electro-optical systems to enhance the image quality scanning electron microscope. The main specifications of EB tungsten filament of JEOL are 0.55mm of mosquito type, 0.65mm of mosquito type, 0.8mm of mosquito type, 0.8mm of eccentric type and 0.55mm of half-moon type. EB tungsten filament of JEOL has a strong plasticity in maintaining electron gun and optical coating.
EB tungsten filament of JEOL is made of tungsten with a high-grade. Its features are high melting point and low coefficients of thermal expansion. This kind of tungsten is the best material for EB tungsten filament. The main types of EB tungsten filament of JEOL is K type. The diameter of its ceramic plate is 28.0 mm, the pin diameter is 1.2 mm, and the distance of center pin is 8.0 mm.
Tungsten Metals Supplier: Chinatungsten Online www.tungsten.com.cn | Tel.: 86 592 5129696; Fax: 86 592 5129797;Email:sales@chinatungsten.com |
Tungsten News & Prices, 3G Version: http://3g.chinatungsten.com | Molybdenum News & Molybdenum Price: http://news.molybdenum.com.cn |
Tungsten Copper Powder CIP Process
- Details
- Category: Tungsten Information
- Published on Thursday, 14 April 2016 15:31
Compared with HIP (Hot Isostatic Pressing) process, CIP (Cold Isostatic Pressing) is a kind of molding process that commonly all directions sealed in plastic mold material simultaneously even pressure at room temperature, and more for powdered metal or non-metallic materials, molding, which provides a pre-sintered compacts for sintering. Tungsten copper is a kind of psudoalloy consists of W and Cu mutually soluble and has a great difference in physical and chemical properties. So it is difficult to prepare by conventional methods, which must be prepared by PM (Powder Metallurgy) process. According to different pressure transmission fluid, including cold isostatic wet bag method and the dry bag method isostatic pressing and soft mode.
Since the conventional molding method between the powder and the powder, powder and punch and die wall there is a certain friction, so that during the pressing force distribution and transmission of certain changes occur, and also resulted in various parts of the compact density and intensity distribution uneven; by comparison, CIP has more uniform forming pressure, which can ensure under lower pressures have pressed leather uniform density and integrity of shape and small loss of mold, high molding efficiency.
In addition, it should be noticed that pressing speed controlling is also a significant factor of the blank density during CIP process. It not only affects the state of friction and work hardening powder particles, but also affects the case of gas escaping. If the compression speed is too fast, the gas can not escape easily, which left in the blanks in the relatively more in the subsequent sintering process are correspondingly difficult to eliminate left voids or pores. Furthermore, pressing too fast will make the inside of the powder aggregate greater stress, resulting in relief the compacts elastic aftereffect. Therefore, in the process of compacting, reduce the speed and extend the dwell time appropriately can ensure that pressure transmission fully, air between powders have sufficient time to escape and be beneficial for density distribution.
Tungsten Carbide Supplier: Chinatungsten Online tungsten-carbide.com.cn | Tel.: 86 592 5129696; Fax: 86 592 5129797;Email:sales@chinatungsten.com |
Tungsten News&Tungsten Prices, 3G Version: http://3g.chinatungsten.com | Molybdenum News & Molybdenum Price: http://news.molybdenum.com.cn |
Tungsten Carbide Transferring Ball
- Details
- Category: Tungsten Information
- Published on Thursday, 14 April 2016 15:30
Tungsten carbide transferring ball, as the name suggests that it is a kind of flexible sphere can run in all directions. So it also has been called universal ball, transferring roller or bull’s eye, etc. Due to the flexibility universal ball rolling, the work bench or other original material quality or bulky workpiece can be more portable to slip, which also greatly reduces the labor intensity of the operator. Universal ball is suitable for transporting the items with smooth and strong surface of bottom, such as cardboard boxes, plastic crates, pallet parts, and surface roughness of the steel sheet-like object. In addition, according to different load requirements, it can adjust the density distribution of transferring ball, or can choose transferring ball with different materials and carrying capacity.
Commonly transferring ball materials includes steel ball, stainless steel ball, carbon steel ball, bearing steel ball, galvanized steel ball, plastic steel ball, tungsten carbide ball and so on. By comparison, tungsten carbide transferring ball has the better properties among them. Tungsten carbide is composed of WC and Co, WC has higher hardness and Co added improves the toughness, strength and wear resistance. It by carbide ball and the support base with the completion of transfer of the workpiece. Tungsten carbide transferring ball has higher machining accuracy and the surface without secondary treatment.
The surface toughness of common steel ball can not meet the requirements, which electrically galvanized or chrome effect will be affected. And secondary processing if the grinder be polished, dimensional accuracy will be affected to some degree. Except surface quality, there are several evaluation parameters of universal ball overall quality, such as flexibility, noise and dimensional accuracy. Generally, plate with your fingers on the ball was moving moment of inertia of the ball more than three seconds for qualified. The noise is related with ball accuracy and the quality, tungsten carbide ball has higher accuracy and quality so its noise is lower and the rotation is smoother and more uniform.
Tungsten Carbide Supplier: Chinatungsten Online tungsten-carbide.com.cn | Tel.: 86 592 5129696; Fax: 86 592 5129797;Email:sales@chinatungsten.com |
Tungsten News&Tungsten Prices, 3G Version: http://3g.chinatungsten.com | Molybdenum News & Molybdenum Price: http://news.molybdenum.com.cn |
Tungsten Trioxide Denitration Catalyst Selection of High Ash Working Condition
- Details
- Category: Tungsten Information
- Published on Wednesday, 13 April 2016 18:31
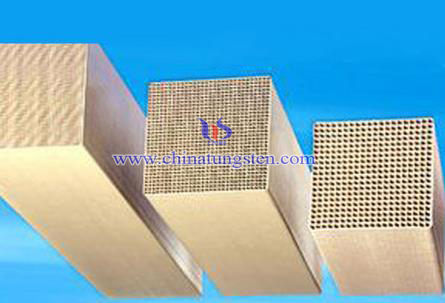
Tungsten Oxide Supplier: Chinatungsten Online www.tungsten-oxide.com | Tel.: 86 592 5129696; Fax: 86 592 5129797;Email:sales@chinatungsten.com |
Tungsten News & Prices, 3G Version: http://3g.chinatungsten.com | Molybdenum News & Molybdenum Price: http://news.molybdenum.com.cn |
WO3 Denitration Catalyst Uses Titanium Dioxide
- Details
- Category: Tungsten Information
- Published on Wednesday, 13 April 2016 18:29
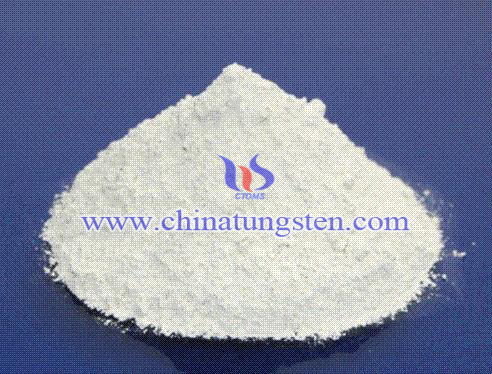
Tungsten Oxide Supplier: Chinatungsten Online www.tungsten-oxide.com | Tel.: 86 592 5129696; Fax: 86 592 5129797;Email:sales@chinatungsten.com |
Tungsten News & Prices, 3G Version: http://3g.chinatungsten.com | Molybdenum News & Molybdenum Price: http://news.molybdenum.com.cn |