Maintenance of Carbon Sulfur Analyzer
- Details
- Category: Tungsten Information
- Published on Tuesday, 19 April 2016 16:03
While analyzing for the carbon and sulfur of steel materials, most of users would choose carbon sulfur analyzer. It is the most commonly instruments for analyzing the carbon and sulfur. Carbon sulfur analyzer is also adopted for some reliability tests of industrial products. In addition, the tungsten granule is an indispensable flux for carbon sulfur analyzer. The fluxing effects of tungsten granule can improve the accuracy of measurement results of carbon sulfur analyzer. However, due to long hours of working, carbon sulfur analyzer will accumulate a lot of sediment, which will reduce the stability of the measurement results. Therefore, the users should always check the work state of carbon and sulfur analyzer, and repair analyzer regularly or make maintenance daily.
The followings are some details about the maintenance for carbon sulfur analyzer. 1. Clean dust in electric arc furnace and clean carefully the inside of the furnace body and precipitator every day. If find that there exist a breakage of dust paper, users should exchange it a new one immediately. Remember not to use any paper napkins or other papers. 2. Two electrodes in the measuring cylinder and buret cannot be contact with each other in any cases, otherwise the process of carbon sulfur analyzer would not function properly. 3. The rubber stopper of buret must be open a notch to make sure that the titration solution can be added. 4. The function of silicone oil in the sensor is to prevent the sensor from corroding. 5. Carbon and sulfur analyzer should be placed on a stable and dry place. 6. Remember to close the master valve of oxygen and the power of instrument if you don’t need to use the analyzer any more in a day. If analyzer has time to rest, on the one hand, it can extend the life time of carbon sulfur analyzer. On the other hand, it benefits to save energy and protect the environment. 7. As the most commonly flux, the quality of tungsten flux should be strictly checked in order to avoid some unnecessary problems during the analysis. 8. Clear up the residue of tungsten granule which do not react completely.
Tungsten Metals Supplier: Chinatungsten Online www.tungsten.com.cn | Tel.: 86 592 5129696; Fax: 86 592 5129797;Email:sales@chinatungsten.com |
Tungsten News & Prices, 3G Version: http://3g.chinatungsten.com | Molybdenum News & Molybdenum Price: http://news.molybdenum.com.cn |
Effect of Doping on Tungsten Copper Contacts (2/2)
- Details
- Category: Tungsten Information
- Published on Tuesday, 19 April 2016 15:18
Take W80-Cu20 tungsten copper contact as an example, were added 0.3% B, 2.0% Nb, 1.5% Ce, using high-speed photography to capture the arc without tungsten copper contact materials under high voltage and high-current interaction, and arc extinguishing process and calculation of the various stages of the amount of time, while taking advantage of the closure value oscilloscope recording discharging. It can be found that the arcing time of tungsten copper contacts added B and Nb is 1.5 times longer than the original contacts.
n addition, in the stable combustion, undoped tungsten copper contact has smaller arc root and the smallest volume of plasma cloud, which shows that higher density of arc plasma cloud increases the temperature of ionsphere; by comparison, doped tungsten copper contact has wider arc root, larger area of scatter and electron movements, which indicates the doping elements can play a role to split the arc. In summary, doped tungsten copper contact has longer arcing time, smaller chopping value, which can effectively disperse the arc and energy.
Next is anti-arc erosion test, which carried out under an inert gas welding, plasma cutting, select the same operating voltage and current, at regular intervals to contact the ablation mass loss were weighed, and observed by scanning electron microscopy of the surface morphology after ablation. By analyzing the experiment data, undoped tungsten copper contact has the maximum of ablation, the doping amount of contact the ablation of a certain percentage of the different constituent elements are significantly reduced. This is due to electrical breakdown occurs in the Cu-rich region, the arc aggregation and localized melting in the region and causing splashing liquid copper in undoped contacts; And after the addition of Nb and B to improve the distribution of the statue, so that small and uniform distribution of the copper phase in the process of arc arcing does not occur in the Cu-rich region, but evenly distributed over the surface, so as to effectively prevent the arc energy centralized, local ablation lead to failure of the contact material.
Tungsten Copper Supplier: Chinatungsten Online tungsten-copper.com | Tel.: 86 592 5129696; Fax: 86 592 5129797;Email:sales@chinatungsten.com |
Tungsten News & Prices, 3G Version: http://3g.chinatungsten.com | Molybdenum News & Molybdenum Price: http://news.molybdenum.com.cn |
Effect of Doping on Tungsten Copper Contacts (1/2)
- Details
- Category: Tungsten Information
- Published on Tuesday, 19 April 2016 15:17
Tungsten copper contact is key part of some high-pressure, high-load breaker, which plays a significant role in current connecting and diverting. Its stability directly affects electrical service life and reliability of the overall operation. And tungsten copper is a kind of composite material that is composed of uniform distribution, neither form solution nor form composite compound W and Cu phase, which not only has high density, high melting point, high strength and excellent anti-arc erosion, anti-welding of W, but also has excellent thermal and electrical conductivity, plasticity, easy processing advantages of Cu.
But the biggest advantage of tungsten copper materials is a special kind of sweating heat sink material. At a high arc temperature, Cu can absorb a lot of energy of arc evaporation and effectively decrease the arc temperature to improve conditions and reduce the effect of galvanic action. With the rapid development of grid market, gradually toward the high-voltage switchgear high-voltage, large capacity, small direction, while the corresponding circuit breaker capacity will continue to increase, the interrupter space narrowing, which makes contact on a unit area bear the load increases, the performance of tungsten copper contact materials have higher requirements.
Tungsten Copper Supplier: Chinatungsten Online tungsten-copper.com | Tel.: 86 592 5129696; Fax: 86 592 5129797;Email:sales@chinatungsten.com |
Tungsten News & Prices, 3G Version: http://3g.chinatungsten.com | Molybdenum News & Molybdenum Price: http://news.molybdenum.com.cn |
Tungsten Bronze and Avoid Hysteresis Driving Method
- Details
- Category: Tungsten Information
- Published on Monday, 18 April 2016 18:29
Tungsten Oxide Supplier: Chinatungsten Online www.tungsten-oxide.com | Tel.: 86 592 5129696; Fax: 86 592 5129797;Email:sales@chinatungsten.com |
Tungsten News & Prices, 3G Version: http://3g.chinatungsten.com | Molybdenum News & Molybdenum Price: http://news.molybdenum.com.cn |
TiO2-Aluminosilicate Fiber Paper Composite Carrier Tungsten Trioxide Denitration Catalyst
- Details
- Category: Tungsten Information
- Published on Monday, 18 April 2016 17:18
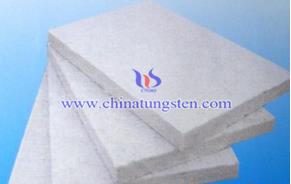
Tungsten Oxide Supplier: Chinatungsten Online www.tungsten-oxide.com | Tel.: 86 592 5129696; Fax: 86 592 5129797;Email:sales@chinatungsten.com |
Tungsten News & Prices, 3G Version: http://3g.chinatungsten.com | Molybdenum News & Molybdenum Price: http://news.molybdenum.com.cn |
Tungsten Trioxide Denitration Catalyst Alkali Metal Poisoning
- Details
- Category: Tungsten Information
- Published on Monday, 18 April 2016 17:15
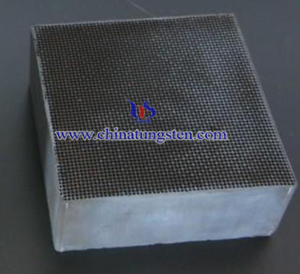
Tungsten Oxide Supplier: Chinatungsten Online www.tungsten-oxide.com | Tel.: 86 592 5129696; Fax: 86 592 5129797;Email:sales@chinatungsten.com |
Tungsten News & Prices, 3G Version: http://3g.chinatungsten.com | Molybdenum News & Molybdenum Price: http://news.molybdenum.com.cn |
Tungsten Electrode Production Technology-Sintering Process and Influence Factors
- Details
- Category: Tungsten Information
- Published on Monday, 18 April 2016 16:37
Tungsten powder and rare earth oxide powder after pressing, tungsten blanks’ density and strength have been greatly improved. After pressing, the blanks should to process sintering. The sintering process will affect tungsten blank’s density, grain size, distribution of rare earth oxides and high temperature evaporation loss quantity and so on, thereby affecting the performance of the tungsten electrode. In the sintering process, time, temperature, heating gradient, heating rate and purity are the main factors affecting the properties of sintered blanks.
When the powder particles is small, if the sintering temperature is too high, the tungsten grain will grow dramatically and will reduce the matrix diffusion coefficient of rare earth oxides in tungsten matrix, increasing electrode’s fare damage rate. Besides, high sintering temperature will lead to low-melting material aggregation, increasing segregation and rare earth oxides loss, so rare earth oxides distributed in the tungsten matrix is unevenly. Meanwhile, the sintering temperature is too high is prone to produce anti-sintering phenomenon, so that tungsten blanks density will decline. Because during the multi-component series sintering, the densification is based on diffusion, with the sintering temperature increase, the diffusion coefficient increases as well, and the shrinkage of sintered blanks become slow. When the sintering temperature is too low, the sintered density of the tungsten electrode can reach requirement also affect the using results.
Tungsten Metals Supplier: Chinatungsten Online www.tungsten.com.cn | Tel.: 86 592 5129696; Fax: 86 592 5129797;Email:sales@chinatungsten.com |
Tungsten News & Prices, 3G Version: http://3g.chinatungsten.com | Molybdenum News & Molybdenum Price: http://news.molybdenum.com.cn |
Tungsten Electrode Production Technology-Pressing and Sintering Process
- Details
- Category: Tungsten Information
- Published on Monday, 18 April 2016 16:33
After using two-steps hydrogen reduction method reduced the tungsten powder and rare earth oxide powder, to process pressing. During pressing process uses steel mold pressing method. Tungsten powder and rare earth oxide affected by the pressing pressure, it will produce a series of displacement. Fine tungsten powder has smaller particles which can fill in the large grain tungsten powder, so tungsten powder particles to be re-arranged, resulting in doped tungsten powder volume greatly reduced. Besides, tungsten blanks density and strength are greatly enhanced. In addition, the tungsten powder particles under pressing pressure, the contact area between the particles is increase and the gap between the particles is reduce, increasing the cohesion between the powder particles, thereby improving the mechanical bite force between the powder particles, so the density and strength of tungsten blanks will be further improved. In the pressing process, the pressure is about 8.5Mpa.
Tungsten electrode is a refractory insoluble metal, so the sintering temperature is very high and usually uses self-resistive heating, namely, direct sintering method. During sintering, the sintering current is generally selected 90% fusing current, so this method is also called sintered sintering method. Sintering process will affect tungsten electrode’s density, grain size, rare earth oxides distribution and high temperature evaporation loss quantity and so on. And there are many factors affect sintering process, such as time, temperature, heating gradient, heating rate, powder purity. To well control these factors can obtain good performance sintered tungsten blanks, to produce good performance tungsten electrode.
Sintered tungsten blanks performance testing, we can observe the blanks surface color and surface defects, and you can also test blanks absorbent. Besides, you can also use drainage method to measure blank’s density.
Tungsten Metals Supplier: Chinatungsten Online www.tungsten.com.cn | Tel.: 86 592 5129696; Fax: 86 592 5129797;Email:sales@chinatungsten.com |
Tungsten News & Prices, 3G Version: http://3g.chinatungsten.com | Molybdenum News & Molybdenum Price: http://news.molybdenum.com.cn |
Tungsten Carbide Slotting Cutter (2/2)
- Details
- Category: Tungsten Information
- Published on Monday, 18 April 2016 16:14
Generally used for machining hardened tungsten carbide slotting cutters were tested negative rake angle form the top edge so that both sides of the cutting edge blade angle to obtain the corresponding negative, slotting process will have beveled cutting characteristics. By increasing the negative rake angle cutting method to improve depth profile shaper cutters nose and the side edge chipping capacity and wear resistance. And this feature is not only suitable for cutting hardened hobbing, but also for slotting process. In order to maintain tungsten carbide slotting cutter based on the accuracy of the tooth to improve the cutting performance, the former top general use -5 ° blade angle is appropriate.
The flank of tungsten carbide slotting cutter is helicoid, which only in its truncated plane will have involute. However, when tungsten carbide slotting cutter made front corner and rear corner, the cutting edge will deviate from the cut surface, the shape with the theoretical involute is there are some errors, and this error is difficult to measure directly. So this will be difficult in the grinding process, the shape of the cutting edge will be further amended, and the need for tungsten carbide slotting cutter pressure angle correction.
In addition, in order to break through the conventional configuration (cone) tungsten carbide slotting cutter easily to be chipped, slotting low accuracy, the researchers also tried a new configuration of tungsten carbide slotting cutter for profiled convex instead of the traditional cone and as a shaper cutter teeth rake. As a cross-section will make a substantial increase in the absolute value of negative rake angle; curved front flank and the lateral flank cross a certain line in both the conical surface of the corner, so that the side edge space curve to flatten in case of the distortion caused by difficult control of the shape of the curve in space of cutting edge and ensure the cutting performance and surface quality. Overall, shaped convex curved tungsten carbide slotting cutter effectively solve the contradiction between the traditional configuration exist in the configuration tool and precision, thereby increasing wear resistance and chipping capability resistance.
Tungsten Carbide Supplier: Chinatungsten Online tungsten-carbide.com.cn | Tel.: 86 592 5129696; Fax: 86 592 5129797;Email:sales@chinatungsten.com |
Tungsten News&Tungsten Prices, 3G Version: http://3g.chinatungsten.com | Molybdenum News & Molybdenum Price: http://news.molybdenum.com.cn |
Tungsten Carbide Slotting Cutter (1/2)
- Details
- Category: Tungsten Information
- Published on Monday, 18 April 2016 16:13
From the appearance, slotting cutter is like a gear or a rack, which is widely used in fabricating spur and helical cylindrical gear meshing inside and outside. Especially for Multi-gear, herringbone gears and gear with a shoulder and shaped workpieces can be made by the slotting cutter with special structure, such as cam, internal spline and so on. According to the appearance, slotting cutter can be specifically divided into disc-shaped, tubular, bowl-shaped and taper shank type, and every shape of slotting cutter will correspond to the workpiece with different shape.
Disk-shaped gear shaper cutters are mainly used inside and outside straight tooth meshing, helical and herringbone gears; Cylindrical gear shaper cutters can be used in the processing module and a relatively small external gear; Bowl-shaped slotting cutter for multi-linking internal and external engagement with shoulder machining spur gears, the clamping nut at work can be accommodated in the body shaper cutters, which does not interfere with the cutting process carried out; Taper shank shaper cutters are mainly used in the processing and spur gear meshing helical gears. At present, in the actual production, high-speed steel is the most used material in slotting cutter, but there here are many studies have shown that compared with carbide shaper cutters with better performance. Especially in the hardness, the strength and wear resistance, tungsten carbide slotting cutter has a great improvement.
Tungsten Carbide Supplier: Chinatungsten Online tungsten-carbide.com.cn | Tel.: 86 592 5129696; Fax: 86 592 5129797;Email:sales@chinatungsten.com |
Tungsten News&Tungsten Prices, 3G Version: http://3g.chinatungsten.com | Molybdenum News & Molybdenum Price: http://news.molybdenum.com.cn |