WO3 Used in Hydrodesulfurization Catalyst
- Details
- Category: Tungsten Information
- Published on Tuesday, 26 April 2016 18:13
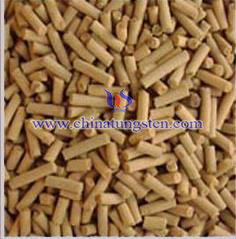
Tungsten Oxide Supplier: Chinatungsten Online www.tungsten-oxide.com | Tel.: 86 592 5129696; Fax: 86 592 5129797;Email:sales@chinatungsten.com |
Tungsten News & Prices, 3G Version: http://3g.chinatungsten.com | Molybdenum News & Molybdenum Price: http://news.molybdenum.com.cn |
Doped Tungsten Bronze Niobate Crystal Structure
- Details
- Category: Tungsten Information
- Published on Tuesday, 26 April 2016 18:09
Tungsten Oxide Supplier: Chinatungsten Online www.tungsten-oxide.com | Tel.: 86 592 5129696; Fax: 86 592 5129797;Email:sales@chinatungsten.com |
Tungsten News & Prices, 3G Version: http://3g.chinatungsten.com | Molybdenum News & Molybdenum Price: http://news.molybdenum.com.cn |
Steel Bonded Carbide Description (2/2)
- Details
- Category: Tungsten Information
- Published on Tuesday, 26 April 2016 15:35
Steel bonded carbide has many advantages, compared with conventional steel, it has higher hardness, wear resistance, hardenability (the ability to obtain the hardened layer depth of quenching); compared with tungsten carbide, it has excellent machinability (such as turning, milling, planing, etc.,), heat treatable and weldable. It also by forging changes its dimensions and internal organizational structure to improve performance, which is generally not available in tungsten carbide. By electrical welding, insert welding, surfacing, vacuum welding, steel bonded carbide can meet a variety of application needs.
Steel bonded carbide also has a smaller proportion of high specific strength, good self-lubricating, high natural frequency and damping characteristics, a significant damping effect. Wherein the circular SiC grains is working with the workpiece surface forms rolling friction, so as to effectively avoid the adhesion of wear and abrasion wear. Combined with the advantages of steel and tungsten carbide, steel bonded carbide has a wide scope of application, which can be used in military materials, marine, aerospace materials, high temperature and corrosion-resistant parts, wear parts of damping, mold material, crushing mining tools, measuring instruments and some fields has special requirements of materials proportion and overall performance.
The machining principle of steel bonded carbide is low cutting rate, accurate control of cutting depth and length, do not add any coolant (except grinding process). If we violet these principles, the surface of steel bonded carbide will be hardened, which hiders the machining process. Material of the tool in the milling process usually uses the high-speed steel and carbide; drilling process should not add coolant to ensure that no oil and drill using medium voltage feed and promptly chip to prevent debris from wear and tear on the drill bit; grinding with high hardness, good self-sharpening diamond grinding wheel 120 #, but should pay attention to the amount of coolant; after quenching, steel bonded carbide will easily crack in the process of electrical machining. In order to prevent the cracks from appearing or extending, it should be extending the annealing time until the stress relief and using quenching or isothermal quenching process.
Tungsten Carbide Supplier: Chinatungsten Online tungsten-carbide.com.cn | Tel.: 86 592 5129696; Fax: 86 592 5129797;Email:sales@chinatungsten.com |
Tungsten News&Tungsten Prices, 3G Version: http://3g.chinatungsten.com | Molybdenum News & Molybdenum Price: http://news.molybdenum.com.cn |
Steel Bonded Carbide Description (1/2)
- Details
- Category: Tungsten Information
- Published on Tuesday, 26 April 2016 15:33
From the narrow sense, the carbide we usually refer to is composed of the hard phase tungsten carbide (WC) and the binder phase cobalt (Co); in a broad sense, cemented carbide refers to the materials that refractory metal compound and a binder metal composed by ingredients, pressing alloy molding, sintering and a series of manufactured. Refractory metal carbides generally refers to the periodic table carbide article IV, V, VI family of W, Ti, Ta, V, Hf and other elements, of which the WC, TiC, TaC of the most widely used.
Cemented carbide has higher hardness, strength, red hardness, excellent chemical stability, perfect wear and ablation resistance and many advantages so that it has a broad application prospect, such as cutting tools, geological mining tools, molding, structural parts, wear parts, high temperature high pressure cavity and so on. Steel bonded carbide is one kind of cemented carbide. In addition, cemented carbide can be divided into common tungsten carbide based (WC - Co, WC- TaC - Co, WC – TiC - Co, WC – TiC – TaC - Co, WC- Ti – TaC – NbC - Co), titanium carbide or titanium carbonitride-based (commonly based on TiC or Ti(C,N) and uses Ni – Mo as the binder), chromium carbide based (commonly based on Cr3C2, uses Ni or Ni – W as the binder) and coated carbide (commonly based on tungsten carbide and deposits hard compound of few microns in thickness by CVD or PVD).
Steel bonded carbide a kind of cemented carbide that based on TiC or WC and uses steel as the binder. It is generally prepared using powder metallurgy method, after machining and heat treatment properties between conventional cemented carbide and steel, which is a new engineering material. Furthermore, according to the final structure of the binder phase, steel bonded carbide can be specifically divided into martensite-based, austenite-based and ferrite-based.
Tungsten Carbide Supplier: Chinatungsten Online tungsten-carbide.com.cn | Tel.: 86 592 5129696; Fax: 86 592 5129797;Email:sales@chinatungsten.com |
Tungsten News&Tungsten Prices, 3G Version: http://3g.chinatungsten.com | Molybdenum News & Molybdenum Price: http://news.molybdenum.com.cn |
Tungsten Alloy All-In-One Laser Printer Shielding
- Details
- Category: Tungsten Information
- Published on Monday, 25 April 2016 19:25
Tungsten alloy all-in-one laser printer shielding can be used for shielding the radiation released during using an all-in-one laser printer. All-in-one laser printer, also known as laser plain paper fax machine, is a fax machine that forms an image by the means of utilizing carbon powder to attach on the paper. All fax machines work by scanning the files to be sent and convert them into a series of black and white point information. These point information would be transformed into audio signals and then be transmitted through a traditional phone line. After the recipient's fax machine receiving the signals, it will print them out, so that the recipient will receive a copy of the original document sent. The difference in different categories of fax machines is the printing method. All-in-one laser printer mainly uses a se drum in the machine body to control the opening and closing of laser beam, thereby producing an image with a charge on the drum, then the carbon powder inside the fax machine will be attracted and attached to the paper to form text or image graphics.
With the development and the maturity of all-in-one laser printer technology, its powerful functionality is widely used in modern office applications. Due to its form of file output of laser printing, it will produce certain laser radiation during the printing process. Today, it is accepted that even low-power lasers with only a few milliwatts of output power can be hazardous to human eyesight when the beam hits the eye directly or after reflection from a shiny surface. At wavelengths which the cornea and the lens can focus well, the coherence and low divergence of laser light means that it can be focused by the eye into an extremely small spot on the retina, resulting in localized burning and permanent damage in seconds or even less time. The same with most electrical appliances, fax machine can also generate electromagnetic radiation which has a certain impact on the human body, by causing cardiovascular disease, diabetes, cancer mutation, miscarriage, infertility, birth defects, immune system and nervous system damage and the like. Therefore, the use of tungsten alloy all-in-one laser printer shielding is necessary.
Because tungsten alloy has a high density, such that its radiation shielding capability can reach very high. Therefore, tungsten alloy all-in-one laser printer shielding has a good radiation shielding performance. Placing a tungsten alloy all-in-one laser printer shielding at the periphery of laser machine can effectively shield the radiation generated during the use of fax machine, thereby reducing the radiation damage of office workers. In addition, compared with traditional materials (such as lead), tungsten alloy is non-toxic and will not pollute the environment, so it is an ideal radiation shielding material.
Tungsten Alloy Supplier: Chinatungsten Online www.tungsten-alloy.com | Tel.: 86 592 5129696; Fax: 86 592 5129797;Email:sales@chinatungsten.com |
Tungsten News & Prices, 3G Version: http://3g.chinatungsten.com | Molybdenum News & Molybdenum Price: http://news.molybdenum.com.cn |
Choosing Right Current for Tungsten Electrode for DCEN Welding and AC welding
- Details
- Category: Tungsten Information
- Published on Monday, 25 April 2016 19:20
People usually use tungsten electrode for aluminum GTAW. As we know, tungsten electrode has many types, and each type is given an AWS classification and includes a painted stripe around one end so you can easily identify the type, including pure tungsten (EWP), 2% thoriated (EWTh-2), zirconiated (EWZr-1), ceriated (EWCe-2), lanthanated (EWLa-1), and rare earth(EW-G)tungsten electrode.
Pure tungsten electrode has a lot of shortages, so manufacturers usually add various additions to the tungsten electrode for improving electrode’s performance. First, doped with rare earth makes the tungsten less likely to sag or droop at high temperatures. Second, it makes electrode easier for the tungsten to emit electrons, which gives it a higher current-carrying capacity compared to pure tungsten.
In the past, people usually use 2 percent thoriated electrodes direct current electrode negative (DCEN) welding, but although more recently lanthanated and ceriated electrodes have become more popular for this type of welding. Because 2% thoriated tungsten electrode has radioaction and it will harm people’s health. On the other hand, When people started to weld aluminum by GTAW using alternating current (AC), they found out 2% thoriated electrodes really weren’t well perform for that type of welding. In AC GTAW much more energy of it is taken up by the tungsten than is taken up in DCEN welding. So in the past the electrode choices for AC using were limited to pure tungsten or zirconiated tungsten, which could carry more current than a pure tungsten electrode of the same size. Neither of these electrodes was used with a sharpened tip. Instead, they were allowed to form a round ball on the end. So during AC, people prefer to choose lanthanated and ceriated electrodes.
On the other hand, thoriated tungsten can produce to a very irregular in geometry, which produced a fluttery, irregular arc. So pure and zirconiated electrodes were preferred.
When inverter GTAW machines came on the scene, the balance control can be set much further toward electrode negative (EN), but it still getting good arc cleaning action. Since only a little electrode positive (EP) is used, the tungsten electrode stays much cooler. In fact, the best electrodes for AC inverter GTAW machines are generally ceriated, lanthanated, and rare-earth electrodes, which are all sharpened to a point and it can retain the point very well during use. Thoriated, zirconiated, and pure tungsten electrodes are not often used with AC inverter machines.
Tungsten Metals Supplier: Chinatungsten Online www.tungsten.com.cn | Tel.: 86 592 5129696; Fax: 86 592 5129797;Email:sales@chinatungsten.com |
Tungsten News & Prices, 3G Version: http://3g.chinatungsten.com | Molybdenum News & Molybdenum Price: http://news.molybdenum.com.cn |
Tungsten Electrode Production and Grinding Process
- Details
- Category: Tungsten Information
- Published on Monday, 25 April 2016 19:17
Tungsten electrode is an important part in welding field. So produce high quality tungsten electrode can not only improve electrode’s life, but also can improve welding performance. In the production process, manufacturers should well control production parameters, properly grinding and cutting electrode also will influence electrode’s performance. As we knew, improperly produced electrode will leads to arc wander, splitting, shedding, inconsistencies, or expensive mistakes and other problems happening in the welding process. Properly produced, ground and cutting and processing electrodes can improve arc starting and stability.
To produce tungsten electrode manufacturers usually uses powder metallurgic method. The detailed production processes are as follow: doping-mixing-pressing-pre-sintered-sintered- multistage swaging process -recrystallization annealing-drawing straightening and polishing. In the production process, every parameter will influence electrode’s performance, so we should continue to improve production technology for improving its welding performance.
On the other hand, tungsten electrode grinding and cutting is another factor influence electrode’s welding performance. And during grinding and cutting diamond wheels are recommended for all tungsten electrodes. While tungsten is a very hard material, the surface of a diamond wheel is harder, which makes for a smooth grind. Grinding with other types of wheels can create jagged edges, imperfections, or invisible poor surface finishes that contribute to weld inconsistency and defects.
There is electrons flow at a greater density on the surface of the electrode. So during grinding, there are some tips should follow. Firstly, electrodes can not grind or polish by crosswise, because the electrons on the surface will jump across the grinding marks. During the welding, the arc begins before the tip, spreads out, and usually wanders, and then tungsten electrode becomes overheated and wears out more quickly. Secondly, if electrodes longitudinal grinding with the grain, the electrons are led steadily to the extreme tip of the tungsten electrode. The arc starts straight and remains narrow, concentrated, and stable.
Tungsten Metals Supplier: Chinatungsten Online www.tungsten.com.cn | Tel.: 86 592 5129696; Fax: 86 592 5129797;Email:sales@chinatungsten.com |
Tungsten News & Prices, 3G Version: http://3g.chinatungsten.com | Molybdenum News & Molybdenum Price: http://news.molybdenum.com.cn |
Tungsten Bronze and SBN Crystal
- Details
- Category: Tungsten Information
- Published on Monday, 25 April 2016 18:53
Tungsten Oxide Supplier: Chinatungsten Online www.tungsten-oxide.com | Tel.: 86 592 5129696; Fax: 86 592 5129797;Email:sales@chinatungsten.com |
Tungsten News & Prices, 3G Version: http://3g.chinatungsten.com | Molybdenum News & Molybdenum Price: http://news.molybdenum.com.cn |
Waste WO3 Denitration Catalyst Regeneration in China
- Details
- Category: Tungsten Information
- Published on Monday, 25 April 2016 17:39
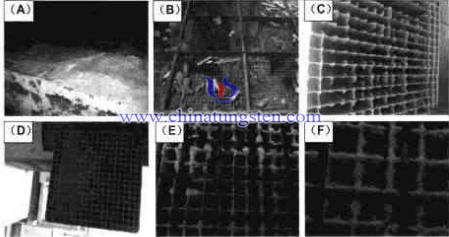
Tungsten Oxide Supplier: Chinatungsten Online www.tungsten-oxide.com | Tel.: 86 592 5129696; Fax: 86 592 5129797;Email:sales@chinatungsten.com |
Tungsten News & Prices, 3G Version: http://3g.chinatungsten.com | Molybdenum News & Molybdenum Price: http://news.molybdenum.com.cn |
Tungsten Crucible for Rare Earth Smelting
- Details
- Category: Tungsten Information
- Published on Monday, 25 April 2016 16:52
Tungsten Crucible is one of the important deep-processing tungsten products which is now widely used in smelting of rare earth for its excellent corrosion resistance and good anti-wear properties as well as a high temperature strength. The choice of tungsten crucible has an important influence on rare earth metal smelting. Thus, in the preparation of tungsten crucible for rare earth smelting, users should pay more attention to the followings.
The first is for the selection of tungsten powder. Tungsten powder is the main raw material for tungsten crucible, the grain size of tungsten powder plays a crucial role on the quality of the finished tungsten crucible. Inappropriate choice of the grain size of tungsten powder will make tungsten crucible have crack during the pressing. Therefore, the grain size of tungsten powder cannot too coarse. If too coarse, the space in the pressing process will be great which will reduce the density of pressed compact and easily lead to cracking. If the users choose too small grain size, movement of position and the amount of deformation between the tungsten powders will increase at the time of pressing. Due to the flabby of elastic stress, the finished tungsten crucible would have crack finally. Accordingly, the grain size of tungsten powder of tungsten crucible for rare earth would better between 2.5μm and 3.0μm. In addition, the oxygen content of the tungsten powder should be less than 0.1%.
Next is the control of pressure in processing. While pressing tungsten crucible with a strong pressure, tungsten powder will have a serious distortion. On the other hand, the strong pressure would increase the elastic stress, and finally, resulting in tungsten crucible cracking. If the pressure is too weak, tungsten crucible cannot enough reach, and it easy to have crack. In addition, the speed of pressure pool should be slow, if too fast, release of elastic stress of tungsten powder will accelerate which would lead to cracking of the tungsten crucible.
Finally is the notice of sintering process. When sintering pressure compact in the medium frequency induction furnace, the sintering temperature should be controlled between 2200 ℃ and 2250 ℃. And the holding time of 3-5 hours is the best. What’s more, the rising rate of sintering temperature cannot too fast or it would cause deformation of tungsten crucible, it is better to rise 80 ℃ or 100 ℃ for one hour.
Tungsten crucible formed by the above ways for rare earth smelting would have better properties and the best effect which can also greatly reduce industry costs.
Tungsten Metals Supplier: Chinatungsten Online www.tungsten.com.cn | Tel.: 86 592 5129696; Fax: 86 592 5129797;Email:sales@chinatungsten.com |
Tungsten News & Prices, 3G Version: http://3g.chinatungsten.com | Molybdenum News & Molybdenum Price: http://news.molybdenum.com.cn |