Production Processes of Tungsten Crucible
- Details
- Category: Tungsten Information
- Published on Monday, 25 April 2016 16:49
Tungsten crucible is one of the metal tungsten products. It can be divided into sintering, stamping and spinning type. Sintering tungsten crucible is mainly applied to the powder metallurgy technology. Stamping and spinning type of tungsten crucible is made of tungsten rod by turning, the size of this type of tungsten crucible is generally smaller than the ordinary one. Tungsten crucible can be used in vacuum inactive gas under 2600℃. Tungsten has a high boiling point, a high melting point, high temperature strength as well as a excellent anti-wear performance. In addition, its coefficient of thermal expansion is small and quenching degree is good. So, tungsten crucible is widely used in smelting of rare earth, quartz glass, electronic painting, crystal growth and other industries.
Generally, the first step of the production process of tungsten crucible is the preparation of tungsten powder and then sifting them. Because the thickness of the tungsten powder has some differences, and in order to meet the requirement of finished tungsten crucible product, users should separate coarse tungsten powder and thin tungsten powder from the mixed tungsten powder with a mesh. And then blending the different tungsten powder which has the same chemical composition together. And then placed it in a closed container which is filled with liquid. Put the same pressure gradually on each surface by supercharging system, so that it can reduce the distance to increase density of material and improve the physical properties of material without any shape-shift. After that, lathe the rough blanks and then put them into a medium frequency furnace for sintering. The next step is the lathing of competitive products. Finally, inspecting the finished product package.
Besides the usual production process, tungsten crucible can also be formed by the following production processes into various types, including sintering, forging, chemical deposition, plasma spraying, a spinning method, rivet linking and welding in according with the requirement of users. Users select a different preparation process to make different types of tungsten crucible. On the other hand, demand of tungsten crucible is increasing year by year, so that states should research and develop different production processes to meet changing market demands. With the rapid development of tungsten industry, researchers should constantly improve the production process of tungsten crucible. In addition, in the manufacturing process of the tungsten crucible, users should pay attention to its pollution and increase the utilization of raw materials to protect the environment.
Tungsten Metals Supplier: Chinatungsten Online www.tungsten.com.cn | Tel.: 86 592 5129696; Fax: 86 592 5129797;Email:sales@chinatungsten.com |
Tungsten News & Prices, 3G Version: http://3g.chinatungsten.com | Molybdenum News & Molybdenum Price: http://news.molybdenum.com.cn |
Contrast between Yttrium Oxide Tungsten Crucible and Pure Tungsten Crucible
- Details
- Category: Tungsten Information
- Published on Monday, 25 April 2016 16:44
The color of yttrium oxide is white with a little yellow which is incompatible with water and alkali, and mainly dissolve in acid. Yttrium oxide is mainly formed by the decomposing of fergusonite, and after the extraction of mixed rare earth solution, dissolving it in acid, and extract again, and concentrate it directly. Finally burning it. Yttrium oxide tungsten crucible is a new type of tungsten crucible which has a high strength and has a strong corrosion resistance.
Tungsten crucible has many excellent properties. Such as high melting point, high temperature strength, a good thermal conductivity, and a small coefficient of thermal expansion. However, because the boundary of the tungsten granule is easily to be corroded, and therefore, the corrosion resistance of ordinary crucible tungsten should be improved. On the contrary, yttrium oxide tungsten crucible can solve this problem radically.
In the manufacturing process of yttrium oxide tungsten crucible, the 1μm yttrium oxide particles will penetrate into the boundaries of the tungsten crystal, distributing evenly around the tungsten crystal. The uniform penetration of yttrium oxide particles can suppress the molten metal and tungsten particles into chemical compound. And it can improve the corrosion resistance of the tungsten crucible. on the other hand, strength of bending resistance of this type tungsten crucible would reach 800MPa under 1000 ℃. Therefore, the yttrium oxide tungsten crucible has a stronger bending strength which is the five times than the pure tungsten crucible.
Except for the improvement of corrosion resistance, yttrium oxide tungsten crucible has a stronger thermostability by comparison with the general pure tungsten crucible. Under normal circumstances, yttrium oxide tungsten crucible can melt dysprosium, neodymium and other reactive rare earth metals, such as aluminum. When melting rare earth metals, yttrium oxide tungsten crucible cannot be corroded and melted.
In addition to the above features, in the manufacturing process of yttrium oxide tungsten crucible, users should pay attention to the protection of yttrium oxide toxicity. Yttrium oxide does harm for our eyes if it contact with the eyes. And it would cause some damage to the liver and lungs if accidentally taking it. Therefore, during the manufacturing process of yttrium oxide tungsten crucible users should be careful with the respiratory system and eyes. It would be better to choose the appropriate respirator and wear anti-chemical goggles and face mask and use safety appliance such as glove when apply, avoid directly touch.
Tungsten Metals Supplier: Chinatungsten Online www.tungsten.com.cn | Tel.: 86 592 5129696; Fax: 86 592 5129797;Email:sales@chinatungsten.com |
Tungsten News & Prices, 3G Version: http://3g.chinatungsten.com | Molybdenum News & Molybdenum Price: http://news.molybdenum.com.cn |
Tungsten Copper Heat Sink Material Hermeticity (2/2)
- Details
- Category: Tungsten Information
- Published on Monday, 25 April 2016 15:11
Merely rely on raising the temperature of the tungsten blanks shrink to increase the density, which is difficult to control precisely. Such as the deviation of heat matching, it is the major influencing factor of conventional infiltration hermeticity. Some researchers try to ultrafine tungsten powder added to certain activators, such as nickel (Ni), cobalt (Co), iron (Fe), etc., and then mixed with copper powder. After pressing and activated sintering, the relative density of tungsten copper can reach 98 % or more, which can be a good solution to tungsten copper heat sink material hermeticity issue. But it added activator of Ni, Co, Fe and other elements will be Cu and W-phase and phase mutually dissolved, and magnetic Fe, Cu content changes will directly affect the conductivity and the thermal conductivity of the material, so not suitable in the heat sink industry applications.
Therefore, on this basis, the researchers conducted a process optimization, the tungsten powder mixed with a small amount of copper powder, copper powder can effectively preserve this part of the green bodies connected pores, when carried out at high temperature and pressure infiltration of liquid copper can be fully effective filled tungsten skeleton. This section is also known as copper induction of copper, its main role lies in two main aspects, one is to enhance the strength of tungsten blanks, and the other is infiltration process hermeticity guarantee.
Tungsten powder has high hardness, poor plasticity, generally under pressure prone to "arch effect" between the powder. Once the pressure is too large, blank-arch bridge will make a release force is rupture and delaminated, and thus the relative density of tungsten powder can only reach about 60%. But copper powder has good plasticity, which can effectively destroy the "arch effect" between the tungsten powder and plastically deformed. Both of them can fill each other, engage with each other, thereby increasing the density and strength of tungsten copper green. On the other hand, since the initial tungsten skeleton have a uniform distribution of copper, the part of copper changed into liquid and complement with the copper liquid out side the skeleton at 1350℃.
Tungsten Copper Supplier: Chinatungsten Online tungsten-copper.com | Tel.: 86 592 5129696; Fax: 86 592 5129797;Email:sales@chinatungsten.com |
Tungsten News & Prices, 3G Version: http://3g.chinatungsten.com | Molybdenum News & Molybdenum Price: http://news.molybdenum.com.cn |
Tungsten Copper Heat Sink Material Hermeticity (1/2)
- Details
- Category: Tungsten Information
- Published on Monday, 25 April 2016 15:10
Based on high density, high strength, excellent chemical stability and arc ablation resistance, tungsten copper material also has perfect thermal and electrical conductivity, which can be widely used in EDM electrodes, electrical contacts, military industry and heat sink materials. However, tungsten copper electrodes and contacts used for electrical machining has different requirements of properties with tungsten copper used in heat sink. As heat sink materials, tungsten copper not only be supposed to have excellent thermal conductivity, but also should have excellent hermeticity to ensure the equipment working stability. Since any porosity and leakage will lead to the operation failure of the microwave component.
In the early 1980s, tungsten copper has been chosen as heat sink materials, which due to it has the similar coefficient of thermal expansion to some ceramic, and both of them after brazing can not only guarantee the thermal matching, but also form a good thermal channel. Theoretically, W and Cu has big difference in physical and chemical properties, which the difference of melting point of them are as much as 2000℃. And they can not form a solid solution or a compound so that it is only suitable for using powder metallurgy process. And the best process is infiltration, tungsten powder is compacted to a certain density of blank, after sintering and shrinking at high temperature forms tungsten skeleton with a certain density and then at a temperature above the melting point of copper was infiltrated tungsten skeleton.
Since the high hardness and poor plasticity of tungsten powder, using a general manufacturing method infiltrated tungsten copper alloy will be some of the pores, the relative density can only reach about 60%. Densification at high temperatures also have some closing pores in copper infiltration process is not sufficiently filled with tungsten skeleton, reducing the product's tightness. In order to reduce the porosity of the relevant parameters need to be improved so that it can meet the requirement of hermeticity.
Tungsten Copper Supplier: Chinatungsten Online tungsten-copper.com | Tel.: 86 592 5129696; Fax: 86 592 5129797;Email:sales@chinatungsten.com |
Tungsten News & Prices, 3G Version: http://3g.chinatungsten.com | Molybdenum News & Molybdenum Price: http://news.molybdenum.com.cn |
Tungsten Bronze Niobate Crystal II
- Details
- Category: Tungsten Information
- Published on Friday, 22 April 2016 18:14
Tungsten Oxide Supplier: Chinatungsten Online www.tungsten-oxide.com | Tel.: 86 592 5129696; Fax: 86 592 5129797;Email:sales@chinatungsten.com |
Tungsten News & Prices, 3G Version: http://3g.chinatungsten.com | Molybdenum News & Molybdenum Price: http://news.molybdenum.com.cn |
Tungsten Carbide Additives (2/2)
- Details
- Category: Tungsten Information
- Published on Friday, 22 April 2016 17:11
Tungsten carbide additives play an important role in inhibiting the WC grain growth, and there are several major additive inhibitory effects: VC> Cr3C2> NbC> TiC> Mo2C> TiC> ZrC> HfC. Their inhibition principle includes:
1. Growth inhibitor changed the energy and characteristics of the solid / liquid interface, hindering the process of tungsten carbide precipitation and dissolution;
2. According to two-dimensional nucleation theory, the border energy leads to subtle changes in a significant change in the control of grain growth of two-D nucleation. During sintering grain growth inhibitors can be added by increasing the boundary can improve dimensional nucleation energy obstacle, making it the nucleation rate dropped significantly, WC grain coarsening has been suppressed;
3. Grain growth inhibitor can change the interface energy or interfere the surface dissolution- precipitation process; and it has higher solubility and diffusion coefficient in the binder phase Co, mainly through migration or diffusion bonding phase in the WC / Co interface, so it is likely to grow crystal grains in the activation WC lattice deposition occurs, thereby preventing the further growth of grains;
4. Add grain growth inhibitors will reduce the rate of diffusion of the activation energy is increased, and it will migrate along the WC / Co interface segregation occurs thereby restricting grain interface.
As an anti-corrosive component, Cr3C2 can be used as additives to improve the corrosion resistance of cemented carbide. It usually added in an amount to be controlled within the solid solubility of Cr in the γ phase, so it can improve its corrosion resistance without compromising the strength of the alloy. The basic principle is dissolved in Cr and Co binder phase in which surface to form a layer of passive film, can significantly reduce the current density, and the higher the ratio of Cr / Co and blunt alloy is greater. The addition of rare earth elements, such as molybdenum (Mo), niobium (Nb), tantalum (Ta), rhenium (Re), ruthenium (Ru) can significantly improve the high temperature properties of the cemented carbide. Ru can keep Co hexagonal structure stable at high temperature and improve the toughness and wear resistance of tungsten carbide; Re can form solid solution with Co, and Co-Re binder may significantly increase the softening temperature and reduce tackiness during processing.
These metal elements are usually added in the wet milling process, except some added in the form of master alloy. In addition, there are some non-metal can be used as additives, such as P, B and some carbide. It forms low-melting eutectic by reacting with other metals, and WC grain will rapidly dissolute in the liquid at relatively low sintering temperature so the alloy can be densified rapidly; while carbide can be synthesized at high temperature and pressure diamond diffuse carbide, which has a hardness close to diamond as well as close to conventional carbide toughness.
Tungsten Carbide Supplier: Chinatungsten Online tungsten-carbide.com.cn | Tel.: 86 592 5129696; Fax: 86 592 5129797;Email:sales@chinatungsten.com |
Tungsten News&Tungsten Prices, 3G Version: http://3g.chinatungsten.com | Molybdenum News & Molybdenum Price: http://news.molybdenum.com.cn |
Tungsten Carbide Additives (1/2)
- Details
- Category: Tungsten Information
- Published on Friday, 22 April 2016 17:09
Tungsten carbide (WC-Co) consists of the hard phase WC and the binder Co, it has higher hardness, high strength, high melting point and excellent wear resistance, which can be widely used in cutting tools, molding and drilling industries. However, with the expanding application and more and more complex conditions, tungsten carbide with WC-Co system can not entirely meet the requirements of the working performance. Tungsten carbide additives appear to effectively solve this problem, different additives can be suitable for different properties of tungsten carbide required.
For instance, in order to suppress the grain growth, the grain growth inhibitors can be used (TaC, MoC, VC); in order to improve the density, toughness and other properties, we can add the corresponding rare earth elements; in order to improve the corrosion resistance of tungsten carbide, we can add some ingredients of corrosion resistance. A relatively small amount of additives, will not have a greater impact on the original carbide other properties, but can significantly improve a certain desired properties, which is an ideal solution.
Theoretically, the finer tungsten carbide WC grain size (micron scale to submicron scale, even nanometer scale), its product density, hardness, fracture toughness, impact toughness will be remarkably improved. But correspondingly to prepare tungsten carbide with smaller granularity, its specific surface area larger and surface activity greater and it easily grows during the sintering process, so the grain growth inhibitors plays a important role. There are several major additive inhibitory effects: VC> Cr3C2> NbC> TiC> Mo2C> TiC> ZrC> HfC.
Tungsten Carbide Supplier: Chinatungsten Online tungsten-carbide.com.cn | Tel.: 86 592 5129696; Fax: 86 592 5129797;Email:sales@chinatungsten.com |
Tungsten News&Tungsten Prices, 3G Version: http://3g.chinatungsten.com | Molybdenum News & Molybdenum Price: http://news.molybdenum.com.cn |
Titanium Blast Furnace Slag Prepares Tungsten Trioxide Denitration Catalyst 2/2
- Details
- Category: Tungsten Information
- Published on Friday, 22 April 2016 17:08
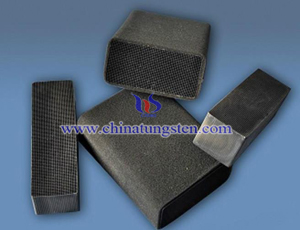
Tungsten Oxide Supplier: Chinatungsten Online www.tungsten-oxide.com | Tel.: 86 592 5129696; Fax: 86 592 5129797;Email:sales@chinatungsten.com |
Tungsten News & Prices, 3G Version: http://3g.chinatungsten.com | Molybdenum News & Molybdenum Price: http://news.molybdenum.com.cn |
Titanium Blast Furnace Slag Prepares Tungsten Trioxide Denitration Catalyst 1/2
- Details
- Category: Tungsten Information
- Published on Friday, 22 April 2016 17:06
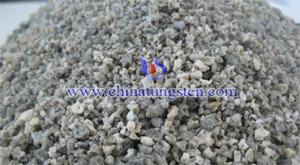
Tungsten Oxide Supplier: Chinatungsten Online www.tungsten-oxide.com | Tel.: 86 592 5129696; Fax: 86 592 5129797;Email:sales@chinatungsten.com |
Tungsten News & Prices, 3G Version: http://3g.chinatungsten.com | Molybdenum News & Molybdenum Price: http://news.molybdenum.com.cn |
Tungsten Boat Atomic Absorption Spectrometer
- Details
- Category: Tungsten Information
- Published on Friday, 22 April 2016 16:50
Atomic absorption spectroscopy (AAS) is a spectroanalytical procedure for the quantitative determination of chemical elements using the absorption of optical radiation (light) by free atoms in the gaseous state. Tungsten boat atomic absorption spectrometer is one of the most important types of AAS.
Since the 1990s, with the rapid development of industry in China, toxic element produced by industry harmful, such as leas which can cause a variety of human diseases. The issue that the over-standard rate of blood lead of adolescent is 30-80% gets a great attention in public. Tungsten boat AAS can solve the problems of blood lead testing in clinical testing.
Tungsten boat AAS uses the standard test method, atomic absorption spectrometry. This type of instrument can detect trace amounts, and has a high sensitivity, the accuracy of result is also very high. In addition, tungsten boat AAS has an advantage of a low power and it doesn’t need for any industrial electricity. It doesn’t require for a good installation condition and cooling water and other assistant equipment, so the operation is much simple than other types of AAS. When exterminating, it is convenient for tungsten boat AAS to collect blood samples. Tungsten boat AAS only requires less blood but can obtain concentration data of lead, cadmium at the same time and it only takes about two minutes to obtain the test data.
Compared to the other types of AAS, the operating cost of tungsten boat AAS is much lower. In the detection of concentration of lead and cadmium, each part only requires one diluent. Then print the test results directly with the intelligent computer without manual calculations. On the other hand, the appearance of tungsten boat AAS is more exquisite, it is easy to move. It is suitable for infants, young children, pregnant women, adolescents, the aged, adult health checks, and other special checks.
Since the tungsten boat AAS occurred, through a large number of clinical experiments and experimental observations and professional certification, its excellent performance and simple operation method obtain the praise of experts. They indicate that the tungsten boat AAS is considered as an international leading technology, it solves the problems which are beset for a long time in clinical examination in detecting trace elements. Tungsten boat AAS is the most desirable instrument to replace the graphite furnace AAS to detect blood lead and cadmium.
Tungsten Metals Supplier: Chinatungsten Online www.tungsten.com.cn | Tel.: 86 592 5129696; Fax: 86 592 5129797;Email:sales@chinatungsten.com |
Tungsten News & Prices, 3G Version: http://3g.chinatungsten.com | Molybdenum News & Molybdenum Price: http://news.molybdenum.com.cn |