Tungsten Alloy Beta Radiation Source Shielding
- Details
- Category: Tungsten Information
- Published on Wednesday, 27 April 2016 18:33
Tungsten alloy beta radiation source shielding can be used for shielding beta radiation released from the use or preparation of beta radiation source with its great radiation shielding ability. Beta radiation source , also referred to as beta source, is a radiation source with the main characteristics as emitting beta particle of it, that can be used to test the thickness and density of a item(such as a paper), and conduct the clinical surface treatment. It can be prepared by radionuclide, such as T, 14C, 22Na, 58Co, 63Ni, 85Kr, 32p, 90Sr, 90y and 147pm, etc. when radionuclide decays, the nucleus would be transformed into another nucleus by emitting electrons and neutrinos, and releasing large amounts of beta particles. Beta particles can be used for treating health conditions such as eye and bone cancer and are also used as tracers.
Beta particles are a type of ionizing radiation which can produce radiation. Being composed of charged particles, beta radiation is more strongly ionizing than gamma radiation, and more strongly penetrating than alpha radiation. Beta radiation is able to penetrate skin to cause radioactive damage. Once it into the human body, it can change the structure of struck molecules and chemical equilibrium of the cells. In most cases, such change can be considered to be damage, with results possibly as severe as cancer or death. If the struck molecule is DNA, it can cause spontaneous mutation, fetal malformation, congenital leukemia. Therefore, it is need to use a tungsten alloy beta radiation source shielding to shield and absorb the beta radiation, in order to effectively prevent people using or preparing the beta radiation source from radiation damage.
Tungsten alloy beta radiation source shielding is made of tungsten alloy. It has a great radiation shielding effectiveness, so that can shield and absorb radiation in a high degree. Tungsten alloy is a tungsten-based alloy joining other elements, for its high density, high melting point, high temperature strength, good creep resistance and good electrical conductivity, it is widely used in a lot of fields. Compared to traditional radiation shielding materials such as lead and boron carbide, tungsten alloy radiation shielding provide excellent density with small capacity. At the same weights high density alloy can provide the same energy absorption as lead using 1/3 less material. Thus, tungsten alloy shielding is the best choice.
Tungsten Alloy Supplier: Chinatungsten Online www.tungsten-alloy.com | Tel.: 86 592 5129696; Fax: 86 592 5129797;Email:sales@chinatungsten.com |
Tungsten News & Prices, 3G Version: http://3g.chinatungsten.com | Molybdenum News & Molybdenum Price: http://news.molybdenum.com.cn |
Industry Standards of Tungsten Crucible for Semiconductor Devices: Inspection Rules, Marking, Packaging, Transportation and Storage
- Details
- Category: Tungsten Information
- Published on Wednesday, 27 April 2016 17:47
Related industries also put forward some standards for tungsten boat for semiconductor device, such as test methods, inspection rules, marking, packing, transportation and storage and other aspects.
After the preparation of the tungsten boat, it should be transported through strict inspection standards. Firstly, the test batches of the product must be the same types which have the same ingredients and produced in the same production process. When test products, people should test them seriously in accordance with the standards to ensure that products meet in all aspects of the standards requirements. Within two months of receipt of the product, the demand side should check products in accordance with the standards. If there exist some problems which do not meet the standards, customers can communicate with suppler.
The inspection for chemical composition of tungsten boat must be analyzed in the chemical composition of a sample in each batch of material. In the case of non-compliant, then the docimaster should analyze chemical composition of the sample, and then averaging it. If it still cannot meet the standards, it is determined that this batch of tungsten boat unqualified. Tungsten boat density test can be taken the same way to the test of the chemical composition. Tungsten boat specifications and surface quality should be one hundred percent inspection.
When packing the qualified tungsten boat. Every 10 wrapped in brown paper, in order to prevent the tungsten boat surfaces from being scratched or breaking. Then ut it into a plastic bag, 20 bags for a box, 4 boxes for a wooden case. Shock-proof scraps of paper should be filled with wooden case, and finally pack it up with iron sheet which can reinforce the wooden case. Inside the packaging boxes of products, material name, batch number, size, quantity, imprint of inspection department, inspectors stamp, date of production and name of the manufacturer should be indicated. Outside the packaging boxes of products, the name of the manufacturer, product names and specifications, quantity, and date of manufacture should be indicated.
In transit, pay attention to handle it. Although there are shock-proof scraps of paper in wooden case, but it still needs to prevent the product from being squeezed, crashed. Before shipping, it is better to have knowledge about the weather conditions, in case rain and snow which would cause product get cold. Therefore, the wooden cases should be place in a dry and ventilated shelves, the relative humidity must less than 65% without any alkalis, acids and other harmful gases.
Tungsten Metals Supplier: Chinatungsten Online www.tungsten.com.cn | Tel.: 86 592 5129696; Fax: 86 592 5129797;Email:sales@chinatungsten.com |
Tungsten News & Prices, 3G Version: http://3g.chinatungsten.com | Molybdenum News & Molybdenum Price: http://news.molybdenum.com.cn |
Industry Standards of Tungsten Crucible for Semiconductor Devices: Brands, Types, Specifications, Technical Requirements
- Details
- Category: Tungsten Information
- Published on Wednesday, 27 April 2016 17:44
Tungsten boat is formed by tungsten sheet through high-pressure tungsten which has a good electrical conductivity, so it is widely used in kinescope, mirror making, toys, household appliances, mobile phones, electrical enclosure and other electronics industries. In recent years, tungsten boat for semiconductor devices has also been given considerable attention by the public. Semiconductors are crystalline or amorphous solids with distinct electrical characteristics, using special electrical characteristics to complete the specific functions of electronic device. Therefore, related industries develop the relevant standards for tungsten boat for semiconductor devices. The followings include brands, models, specifications, technical requirements, test methods, inspection rules, mark, packing, transportation and storage.
Grades of tungsten boat can be named as WZO in according with the chinese phonetic alphabet "wolfram" and "boat". Tungsten boat models can be express as "V" and "U", different types of each model use the Roman numerals Ⅰ, Ⅱ, Ⅲ to represent. Tungsten boat specifications should be express in number in the format "- the wall thickness of the boat - the boat width." Applications should correspond to the marks and models. For example, WZO-V-Ⅰ-02-17, its brand is represented by WZO, V-type non-pressure side with 0.3mm tungsten boat wall thickness, 15mm tungsten boat width. Except that, the surface quality of tungsten boat should always keep in a clean condition, the color is silver-white metallic luster without any cracks, stratification, lack of edge and other defects. All parts of the tungsten boat cannot have glitches. Performance of tungsten plate used by tungsten boat should accord with the national GB3875 requirement. Using the accuracy of 0.02mm caliper and 0.01mm micrometer to measure tungsten boat size, according to national standard GB4196 tungsten boat standards. The weight of tungsten boat should be weight in a balance with a 0.2g sensibility of balance. If the chemical composition of tungsten boat is qualified, it is no need for measuring the melting point.
With the rapid development of tungsten boat for semiconductor devices, the threat of environmental pollution of tungsten boat is also rising. Tungsten compounds such as tungsten carbide dust, tungsten oxide, tungsten carbide, and tungsten boat have a great impact on health which would cause inflammation of eyes or skin and some respiratory diseases such as asthma, if people deal with it for a long time.
Tungsten Metals Supplier: Chinatungsten Online www.tungsten.com.cn | Tel.: 86 592 5129696; Fax: 86 592 5129797;Email:sales@chinatungsten.com |
Tungsten News & Prices, 3G Version: http://3g.chinatungsten.com | Molybdenum News & Molybdenum Price: http://news.molybdenum.com.cn |
Supported WO3-Based Oxidative Desulfurization Catalyst
- Details
- Category: Tungsten Information
- Published on Wednesday, 27 April 2016 17:39
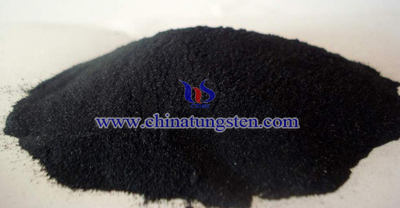
Tungsten Oxide Supplier: Chinatungsten Online www.tungsten-oxide.com | Tel.: 86 592 5129696; Fax: 86 592 5129797;Email:sales@chinatungsten.com |
Tungsten News & Prices, 3G Version: http://3g.chinatungsten.com | Molybdenum News & Molybdenum Price: http://news.molybdenum.com.cn |
WO3 Used for Ultra-Deep Oxidative Desulfurization Catalyst
- Details
- Category: Tungsten Information
- Published on Wednesday, 27 April 2016 17:35
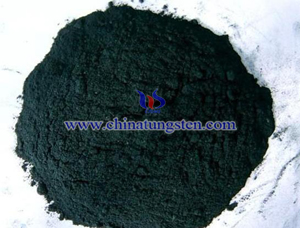
Tungsten Oxide Supplier: Chinatungsten Online www.tungsten-oxide.com | Tel.: 86 592 5129696; Fax: 86 592 5129797;Email:sales@chinatungsten.com |
Tungsten News & Prices, 3G Version: http://3g.chinatungsten.com | Molybdenum News & Molybdenum Price: http://news.molybdenum.com.cn |
Tungsten Trioxide Used in Hydrodesulfurization Catalyst
- Details
- Category: Tungsten Information
- Published on Wednesday, 27 April 2016 17:32
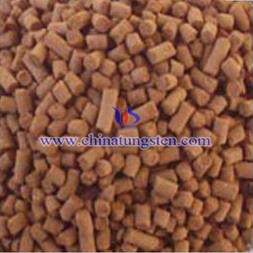
Tungsten Oxide Supplier: Chinatungsten Online www.tungsten-oxide.com | Tel.: 86 592 5129696; Fax: 86 592 5129797;Email:sales@chinatungsten.com |
Tungsten News & Prices, 3G Version: http://3g.chinatungsten.com | Molybdenum News & Molybdenum Price: http://news.molybdenum.com.cn |
Tungsten Copper Heat Sink Plasma Spraying (2/2)
- Details
- Category: Tungsten Information
- Published on Wednesday, 27 April 2016 15:27
The researchers use two kinds of spray gun (internal and external powder feed) to observe the structure and properties of tungsten copper heat sink. It can be found that in the internal powder feeding conditions, W content of tungsten copper composite material is higher than the content of external powder feed. This is due to internal feed powder is powder being ejected before the gun are all located in the plasma flame, part of the W particle is melted, melted and un-melted W particles, and the molten copper solution together is sprayed into the substrate, so that easy obtain raw material powder composition approximating tungsten copper composite material; while in the process of external powder feed, he trajectory of the powder particles are not entirely consistent with the plasma flame, which can only make a fraction of smaller particle size of the W particles melt, and a lot without melting of W particles are difficult to be deposited, so the W collected rate decrease.
Besides, at internal powder feeding conditions, only a small amount of cuprous oxide can be detected, which indicates the impact of power in copper oxidation is not obvious. This is due to the internal powder feeding only a very small amount of oxygen is brought into a powder particle flow, thereby largely avoiding the oxidation of copper; by contrast, in the same power, a large number of external powders feed oxygen into the powder particles flow and exacerbates the copper oxide. With the power increase, the plasma flame temperature also increases, the oxidation of copper increased significantly. Overall, plasma spraying uses plasma arc, which compared with free arc has fine arc, high current density, and high degree of gas ionization. So it has many advantages, such as high temperature, high energy concentration, excellent arc stability, which is the ideal material for tungsten copper heat sink.
Tungsten Copper Supplier: Chinatungsten Online tungsten-copper.com | Tel.: 86 592 5129696; Fax: 86 592 5129797;Email:sales@chinatungsten.com |
Tungsten News & Prices, 3G Version: http://3g.chinatungsten.com | Molybdenum News & Molybdenum Price: http://news.molybdenum.com.cn |
Tungsten Copper Heat Sink Plasma Spraying (1/2)
- Details
- Category: Tungsten Information
- Published on Wednesday, 27 April 2016 15:25
With the rapid development of science and technology, integrated in the microelectronics industry sectors related electronic products have become more sophisticated, the corresponding energy consumption also increased. So it places higher demands on heat sink properties, which not only required high density and strength, but also has excellent electrical conductivity, thermal conductivity and low coefficient of thermal expansion. Tungsten copper is composed of W with high hardness, high density, high strength, high melting point and low coefficient of thermal expansion and Cu with perfect electrical and thermal conductivity so that it can be an ideal material for heat sink. Furthermore, the properties of tungsten copper heat sink can be improved by the adjustment of W and Cu content.
Since there is a great difference in physical and chemical properties between W and Cu, which has 2000℃ difference in melting point. Both of them do not form a compound or solution, so it is a kind of typical pseudo alloy. Therefore, it is difficult to achieve by common pressed and sintered, the infiltration is the best way. But infiltration is easy to form pores certain deficiencies and to bring some difficulties to the subsequent processing. Plasma spraying is a strengthening of the material surface and surface-modified new multi-purpose precision spraying techniques. It uses plasma arc drove by DC as the heat source and has the following characteristics:
1. Ultra-high temperature characteristics, suitable for spraying refractory material;
2. High particle injection rate, the coating is dense and has higher bonding strength;
3. In the process of spraying, inert gas used as the shielding gas so that the coating material difficult to be oxidized.
Plasma spraying technique can make the surface of the substrate with a high temperature oxidation, thermal insulation, anti-friction, wear and corrosion, insulation, radiation protection and sealing properties, which can heat metal, alloy and ceramics to molten or semi-molten state and spray to the surface after pretreatment at high speed to form a firmly attached layer. In addition, plasma spraying also can be used in medical field, the coating layer of a few microns in artificial bone surface coating can achieve enhanced affinity for artificial bone and the strengthening effect.
Tungsten Copper Supplier: Chinatungsten Online tungsten-copper.com | Tel.: 86 592 5129696; Fax: 86 592 5129797;Email:sales@chinatungsten.com |
Tungsten News & Prices, 3G Version: http://3g.chinatungsten.com | Molybdenum News & Molybdenum Price: http://news.molybdenum.com.cn |
Tungsten Alloy Radiation Shielding For IDC Room
- Details
- Category: Tungsten Information
- Published on Tuesday, 26 April 2016 18:44
Tungsten alloy radiation shielding for IDC room is a radiation shielding used to shield electromagnetic radiation generated by IDC room. IDC room, also known as Internet data center, is the standardized telecom room established by the telecom department through utilizing the existing bandwidth resources and Internet communications lines. With the evolving needs of Internet, IDC room rapidly develops into a vital part of China's Internet industry in the new century, to provide professional server rental managed services and related value-added services for the media, enterprises, Internet content providers, government, business or web server group. Therefore, the enterprises or government agencies no longer need to establish their own IDC room,lay the expensive communication lines, and hire network engineers with the use of IDC server hosting business.
Due to IDC room equipments will release large amounts of electromagnetic radiation which is harmful for human body, staffs can use tungsten alloy radiation shielding for IDC room to shield radiation. Electromagnetic radiation has thermal effects, non-thermal effects and cumulative effects on the human body. According to experts, electromagnetic radiation more than 2 gigahertz will cause people to suffer from diseases, such as skin disease, cardiovascular disease, vitiligo, psoriasis, allergic purpura and diabetes, and lead to eyelid edema, bloodshot eyes, stuffy nose, runny nose, sore throat discomfort, or systemic skin urticaria, eczema, itching. Long-term and excessive electromagnetic radiation will also damage human reproductive, nervous and immune system, changing blood, lymph and cell protoplasm, causing fetal malformation or spontaneous abortion.
Tungsten alloy radiation shielding for IDC room mainly uses tungsten heavy alloy. According to the research, the radiation shielding performance of a metal material is closely related to its density, the radiation shielding ability increase with the increasing of density. Due to the high density of tungsten alloy, tungsten alloy radiation shielding for IDC room thus has high radiation shielding properties, which can effectively shield the electromagnetic radiation generated by the IDC room equipment, to reduce the radiation damage on staffs. Moreover, tungsten alloy is a harmless and non-toxic material that will not produce harmful substances or pollute the environment.
Tungsten Alloy Supplier: Chinatungsten Online www.tungsten-alloy.com | Tel.: 86 592 5129696; Fax: 86 592 5129797;Email:sales@chinatungsten.com |
Tungsten News & Prices, 3G Version: http://3g.chinatungsten.com | Molybdenum News & Molybdenum Price: http://news.molybdenum.com.cn |
Five Tips for Successful Aluminum GTAW-Tungsten Electrode Choosing
- Details
- Category: Tungsten Information
- Published on Tuesday, 26 April 2016 18:20
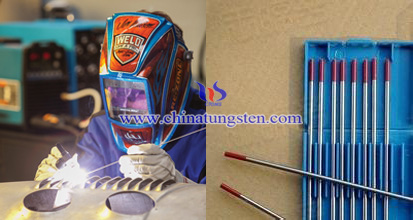
Tungsten Metals Supplier: Chinatungsten Online www.tungsten.com.cn | Tel.: 86 592 5129696; Fax: 86 592 5129797;Email:sales@chinatungsten.com |
Tungsten News & Prices, 3G Version: http://3g.chinatungsten.com | Molybdenum News & Molybdenum Price: http://news.molybdenum.com.cn |