Heavy Oil HDM Desulfurization Catalyst Containing WO3
- Details
- Category: Tungsten Information
- Published on Wednesday, 04 May 2016 16:38
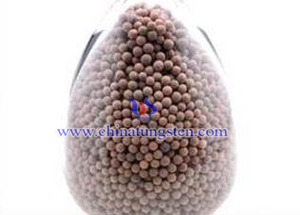
Tungsten Oxide Supplier: Chinatungsten Online www.tungsten-oxide.com | Tel.: 86 592 5129696; Fax: 86 592 5129797;Email:sales@chinatungsten.com |
Tungsten News & Prices, 3G Version: http://3g.chinatungsten.com | Molybdenum News & Molybdenum Price: http://news.molybdenum.com.cn |
Tungsten Copper Liner Warm Flow Compaction (2/2)
- Details
- Category: Tungsten Information
- Published on Wednesday, 04 May 2016 16:23
The liner is the key component of perforation bombs and armor-piercing, whose performance directly affects the penetration depth and piercing armor-piercing shells and after the explosion. In the early days, it uses turning process to fabricate copper rods and iron rods to form the liner shape or press-molding process to copper plate and iron plate. But these process has lower productivity, low dimensional accuracy and less prone to clogging of the perforation. With the development of powder metallurgy, powder sintering gradually replaced the cover plate liner, the production process is simplified, and overall efficiency has been improved.
However, due to the cover wall is thinner, easily deformed during sintering, poor surface fineness, it needs some optimization. Warm flow compaction can form the large component with a complex shape or structure and uniform density distribution, which is beneficial for the further expansion of tungsten copper material applications. It combines the advantages of injection molding and warm compacting process, which improves the flowability of the mixed powder by the viscosity changing of the binder. There are some experiments shows that the density distribution of W-70Cu liner by warm flow compaction is more uniform and the penetration is more stable.
Overall, compared with the injection molding suitable for the smaller components, warm flow compaction is more suitable for the larger components with complex structure and shape. It has higher requirements on the granularity of raw material and is sensitive to the temperature changes and the amounts of binder. Low temperature may cause mixing powder flow properties deteriorated, so that the tungsten copper shaped charge density distribution can not be molded or uneven. High temperature may obviously separate the two phase (the mixed powder and the binder). The excessive amount of adhesive may cause infiltrated tungsten skeleton pore through the large, so that the density decreases and easily deformed. In addition, warm flow compaction combines the advantages of injection molding and warm compacting process, and it can effectively improve the density, the penetration depth and armor capability of tungsten copper liner, which is the ideal choice for tungsten copper liner manufacturing in the future.
Tungsten Copper Supplier: Chinatungsten Online tungsten-copper.com | Tel.: 86 592 5129696; Fax: 86 592 5129797;Email:sales@chinatungsten.com |
Tungsten News & Prices, 3G Version: http://3g.chinatungsten.com | Molybdenum News & Molybdenum Price: http://news.molybdenum.com.cn |
Thoriated Tungsten Electrode Introduction
- Details
- Category: Tungsten Information
- Published on Wednesday, 04 May 2016 16:22
Grinding
Grinding electrode will produce radioactive dust into atmosphere. So it is recommended during grinding should make up a dedicated grindstone and local dust extraction. Besides, a simple filter mask is necessary unless you contact with small number of electrodes (less than about 20 per year). On the other hand, if the grinding wheel is not fitted with a protective viewing screen, eye protection should be worn. What’s more, the air extract from the grindstone should be collection so that the particles are deposited into a substantial disposable bag and will not release to the atmosphere just in case of ingestion or inhalation by welders.
After finish welding process, the area round the grinding wheels should be cleaned daily with a vacuum cleaner to remove dust particles. Besides, welders should be encouraged to wash their hands or whole body.
Welding
Some hazardous substance of thoriated tungsten electrode does occur during welding but it is a very small amount and the corresponding level of radioactivity is extremely low. However, wearing mouth, nose and eye protection during welding would further reduce any risk of contamination, and make welders more safety.
Alternatives to thoriated tungsten electrode
Lanthanum, cerium, yttrium and zirconium oxides can all be used with tungsten to produce lanthanated, ceriated, zirconiated and yttriated tungsten electrodes. Compared with thoriated tungsten electrode, they are all marginally radioactive, so the risk is even lower than with thorium oxide, so no specific precautions are needed. At the present, especially in developed counties they prefer to use these electrodes to place thoriated tungsten electrode. Among these rare earth tungsten electrodes, ceriated or lanthanated tungstens electrode are acceptable alternatives to thoriated tungsten electrode, particularly with a DC current, while zirconiated tungsten is preferred for AC current welding. There are very minor differences in the arc voltages required for equal currents between the various alternatives. Consideration should be given to justifying the use of thoriated tungsten electrodes in preference to other suitable alternatives.
Tungsten Metals Supplier: Chinatungsten Online www.tungsten.com.cn | Tel.: 86 592 5129696; Fax: 86 592 5129797;Email:sales@chinatungsten.com |
Tungsten News & Prices, 3G Version: http://3g.chinatungsten.com | Molybdenum News & Molybdenum Price: http://news.molybdenum.com.cn |
Tungsten Copper Liner Warm Flow Compaction (1/2)
- Details
- Category: Tungsten Information
- Published on Wednesday, 04 May 2016 16:20
Tungsten copper liner is a kind of psudoalloy that composed of W and Cu, which is immiscible and forming compound with each other. So it is difficult to fabricate by common pressing-sintering process, the most widely used in tungsten copper products is powder metallurgy (PM), which includes infiltration and activated liquid-phase sintering. Infiltration presses tungsten powder into a compact, at a certain temperature pre-sinter the porous tungsten skeleton with density and strength. And then the low melting point of the molten liquid copper is infiltrated tungsten skeleton in order to obtain tungsten copper alloy with fully densified. The main mechanism is the liquid metal wetting porous matrix metal, under the effect of capillary forces along the inter-particle pore liquid copper flows and fills pores of the porous tungsten skeleton.
According to the sintering temperature, infiltration process can be specifically divided into sinter tungsten skeleton at high temperature + Cu infiltrated and sinter composite powder at low temperature + Cu infiltrated. Sinter tungsten skeleton at high temperature + Cu infiltrated presses tungsten powder into a compact before sinter and infiltrated Cu at 1800-2200℃. Since the tungsten powder at a high temperature to fully restore the remaining low-melting impurities and sub-oxides can be restored by evaporation gasification and thermal decomposition was removed, thus prepared tungsten copper shaped relative density of 99.2% comprehensive and excellent performance.
However, it also has some disadvantages, such as long production cycle, the control parameters are many and complex and high production cost. While sinter composite powder at low temperature + Cu infiltrated is mixed with a small amount of induced copper before sintering and infiltration. Generally, induced copper content of about 2.5% -3.5% and the granularity is similar to tungsten powder, which can effectively improve the compacting performance and the flowability of liquid Cu. But too much of the added amount of copper will result in enrichment-induced infiltration of copper, so that the overall the density of tungsten copper liner decreases.
Tungsten Copper Supplier: Chinatungsten Online tungsten-copper.com | Tel.: 86 592 5129696; Fax: 86 592 5129797;Email:sales@chinatungsten.com |
Tungsten News & Prices, 3G Version: http://3g.chinatungsten.com | Molybdenum News & Molybdenum Price: http://news.molybdenum.com.cn |
Thoriated Tungsten Electrode Hazards
- Details
- Category: Tungsten Information
- Published on Wednesday, 04 May 2016 16:18
Introduction
Thoriated tungsten electrode has low work function, stable welding performance and long service life, so in the early time it was widely used in welding industry.
Tungsten electrodes are used in tungsten inert gas (TIG) or plasma welding. During the welding process the electrode, arc and weld pool are protected from atmospheric contamination by an inert protective gas. A tungsten electrode is used in welding industry because it can withstand very high temperatures without melting or erosion. It is usually made by powder metallurgy and is formed to various sizes after sintering. Besides, according to different doped rare earth oxides, it can be divided into different types. Oxides used are primarily those of zirconium, thorium, lanthanum, yttrium or cerium, and doped quantity is usually 1%-4%. All these oxides greatly improve arc initiation, especially when direct current (DC) welding is employed.
Hazards
As we know thorium (Th) is slightly radioactive with a long half life and emits mainly alpha (α) particles, but occasionally some beta (β) and gamma (γ) radiation is emitted. Thoriated tungsten electrode was made by 2%thorium oxide, therefore, a low level radioactive material which contains in electrode, and it will cause small external radiation hazard and an internal hazard from ingestion or inhalation to welders. The external hazard estimated for a welder holding an electrode for a long time is a very small fraction of the maximum permissible radiation dose and it is concluded that the external radiation hazard is likely to be negligible. However, to achieve maximum arc stability the electrode tip should grind to a conical point before use and the shape is maintained during use by regular regrinding. During the grinding process, particles of electrodes may be produced with thoria on the surface. These dust particles that create the major hazard, as they may be inhaled. On the other hand, during welding, electrode will release hazardous substance, if welder ingestion or inhalation by accident it will harm to their health.
Storage
It is recommended that thoriated electrodes are stored in steel boxes with clearly labelled. When stored in closed boxes, there should no significant hazard in handling and storage. 10 pieces electrodes for one plastic box can be handled by welders safely without any special precautions.
Tungsten Metals Supplier: Chinatungsten Online www.tungsten.com.cn | Tel.: 86 592 5129696; Fax: 86 592 5129797;Email:sales@chinatungsten.com |
Tungsten News & Prices, 3G Version: http://3g.chinatungsten.com | Molybdenum News & Molybdenum Price: http://news.molybdenum.com.cn |
Tungsten Crucible for Waterproof Membrane
- Details
- Category: Tungsten Information
- Published on Wednesday, 04 May 2016 10:55
With the continuous development of optical applications, the scope of application of optoelectronic products becomes more widely, and product requirements have gradually increased. A waterproofing membrane is a layer of material that prevents the passage of water. These materials are used in a huge range of products, but the term is generally used when referring to construction or clothing. Waterproof is often a matter of degree rather than certainty. In the vacuum coating process, the inorganic material would become the vapor and deposit on the substrate surface which is bombarded by ohmic heating or high energy electron gun. Because the microstructure film is uneven which would cause a large number of capillary voids during deposition, causing the lens surfaces absorb dust, water, oil. Finally, it will easily scratch the surface of the product, on the other hand, the dust would have a great impact on the optical performance of products. Thus, the waterproof film prepared by a wolfram crucible can overcome this deficiency partly.
First of all, put the high purity and amorphous oxides materials as carrier materials, and then form them into the final shape through freezing process or heating process by adhesive in a room temperature. After that, put the semi-finished product into a tungsten crucible which is put into a high temperature furnace and pressure inside the furnace, the heat treatment with the 850-1500 ℃ temperature. In the case of heat treatment, form oxide carrier materials with many hole and evenly shape through the changing of the shape. At the end of it, dropping waterproof material which contains an organic fluorine-silicon in a porous oxide carrier material, eventually forming a waterproof membrane.
As a carrier of semi-finished product, when heating, tungsten crucible would cost much less time to rise the temperature thanks to its high melting point, boiling points, and high thermal conductivity. Operation of wolfram crucible for waterproof membrane is simple and convenient which can also produce a lot of production in a short time. After using silica oxide carrier materials, people do not need to pay special attention to its recycling, manufacturers can generally handle it the same as the general waste, therefore, the cost is relative low. Wolfram crucible for waterproof membrane would make less time-consuming as well as high performance and the in the productions process it would not cause a great impact on the environment.
Tungsten Metals Supplier: Chinatungsten Online www.tungsten.com.cn | Tel.: 86 592 5129696; Fax: 86 592 5129797;Email:sales@chinatungsten.com |
Tungsten News & Prices, 3G Version: http://3g.chinatungsten.com | Molybdenum News & Molybdenum Price: http://news.molybdenum.com.cn |
Characteristic of Stamping Tungsten Boat
- Details
- Category: Tungsten Information
- Published on Wednesday, 04 May 2016 10:52
Manufacturing process of tungsten boat is generally stamping at a high temperature. Depending on the different requirements of the finished wolfram boat, Manufacturing process of it can be divided into stamping, welding, sintering, riveting. The following will talk more details about stamping tungsten boat. Stamping (also known as pressing) is the process of placing flat sheet metal in either blank or coil form into a stamping press where a tool and die surface forms the metal into a net shape. Stamping includes a variety of sheet-metal forming manufacturing processes, such as punching using a machine press or stamping press, blanking, embossing, bending, flanging, and coining.
First of all, tungsten plate should be blended into a certain angle, or bending the blended workpiece again. After that, it should be pressed into any hollow shape by mould, or bending the hollow mould workpiece further deformation. Afterward the hole or the outer edge of tungsten plate should be folded into a straight wall by mould. Forcing an outward radial force on the hollow member by mould, so that the local diameter can be expanded. After expansion, pressing the outside-in radial pressure on the hollow member so to narrow the local diameter. Next, putting the bloom into the die cavity, squeeze it out from the gap of mould to form the hollow or solid workpiece. Roll the panel into a ball peen whose shape approximate to a close one. Finally, press the bended or stretched workpiece into a right W-boat shape.
The main characteristic of the stamping W-boat is the high rate of final products but it would cause noise pollution. Because that this type of W-boat using the stamping equipment and stamping mould, the accuracy of size and shape the stamping wolfram crucible are much higher. What’s more, it has a long life time and it is not easily to be damaged, therefore, shape of the W-boat from the same production batch is almost the same which quality is also stable. On the other hand, pressure of stamping device is accurate, so that it will not damage the surface quality of the finished W-boat. However, there still exist some disadvantages of it. For example, during the stamping process, the device will produce noise and vibration which would have a great influence on operators. Furthermore, the mould is an essential material for stamping process, so the quality of the mould determines the quality of the W-boat.
Users can make reasonable adjustments to the size of the stamping W-boat as needed.
Tungsten Metals Supplier: Chinatungsten Online www.tungsten.com.cn | Tel.: 86 592 5129696; Fax: 86 592 5129797;Email:sales@chinatungsten.com |
Tungsten News & Prices, 3G Version: http://3g.chinatungsten.com | Molybdenum News & Molybdenum Price: http://news.molybdenum.com.cn |
Why Use Tungsten Alloy Shielding
- Details
- Category: Tungsten Information
- Published on Tuesday, 03 May 2016 18:42
Along with widely using of radiation in medical, industrial, scientific communications, food, medicine and other fields, radiation hazards and how to achieve radiation protection also attract people's attentions. In physics, radiation is the emission or transmission of energy in the form of waves or particles(such as alpha particles, beta articles)through space or through a material medium. It is generally divided into ionizing radiation and non-ionizing radiation depending upon the energy of the radiated particles. Ionizing radiation (including α, β and γ radiation) has enough high-energy radiation to ionizing atoms, while the energy of non-ionizing radiation is lower than that of ionizing radiation, which can't ionize substances. In the medical field, radiation may be used to diagnose and treat diseases, such as physicians can use X-rays to find broken bones and locate cancer grow in vivo; in the field of science, radioactive atom is used as tracer; and in modern communication systems the form of radiation is mainly electromagnetic radiation.
With the increasing use of radiation in our lives, its harm cannot be neglected any longer. Most electronic devices have electromagnetic radiation that have a great harm on human health. For example, long-term irradiation during pregnancy will cause fetal malformations. Long-term exposure to radiation also can also make human body discomfort, resulting in human organs and system damage, lead to leukemia, cancer, eye diseases, reproductive system damage, aplastic anemia and other diseases. Therefore, the radiation protection is a must. Radiation protection can be reached by putting a shielding between humans and the radiation source or around the radiation source in order to achieve the effect of weakening the intensity of radiation to avoid human suffering from radiation damage. Common shield material are lead shielding, tungsten alloy shielding, depleted uranium, of which tungsten alloy is the best radiation shielding material.
Tungsten alloy is a tungsten-based alloy that adds other elements. It is found naturally on Earth almost exclusively in chemical compounds. It has the highest melting point of all the elements and also has strength at high temperature, high creep resistance and good thermal conductivity and electron emission performance. Compared with other shielding materials, tungsten has a higher density, while the radiation shielding performance of a metal material is closely related to its density, the higher the density is, the better the shielding performance is, and therefore tungsten alloy shielding has a good radiation shielding effectiveness. In addition, tungsten alloy shielding is a non-toxic, environmental protection and friendly shielding metal alloy shielding, neither pollute the environment, nor endanger human health.
Tungsten Alloy Supplier: Chinatungsten Online www.tungsten-alloy.com | Tel.: 86 592 5129696; Fax: 86 592 5129797;Email:sales@chinatungsten.com |
Tungsten News & Prices, 3G Version: http://3g.chinatungsten.com | Molybdenum News & Molybdenum Price: http://news.molybdenum.com.cn |
Sodium Tungsten Bronzes Single Crystal Growth
- Details
- Category: Tungsten Information
- Published on Tuesday, 03 May 2016 18:28
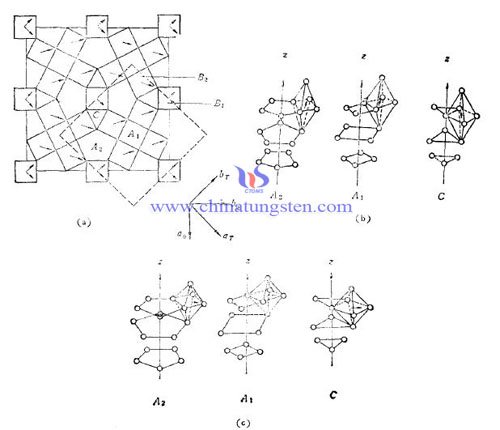
Tungsten Oxide Supplier: Chinatungsten Online www.tungsten-oxide.com | Tel.: 86 592 5129696; Fax: 86 592 5129797;Email:sales@chinatungsten.com |
Tungsten News & Prices, 3G Version: http://3g.chinatungsten.com | Molybdenum News & Molybdenum Price: http://news.molybdenum.com.cn |
WO3 for Gasoline Selectively Hydrodesulfurization Catalyst
- Details
- Category: Tungsten Information
- Published on Tuesday, 03 May 2016 18:11
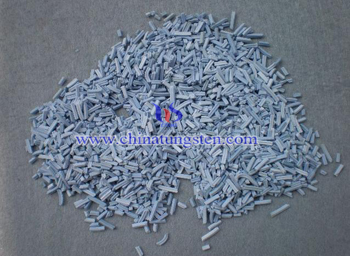
Tungsten Oxide Supplier: Chinatungsten Online www.tungsten-oxide.com | Tel.: 86 592 5129696; Fax: 86 592 5129797;Email:sales@chinatungsten.com |
Tungsten News & Prices, 3G Version: http://3g.chinatungsten.com | Molybdenum News & Molybdenum Price: http://news.molybdenum.com.cn |