Running Time Affects Tungsten Trioxide SCR Denitration Catalyst
- Details
- Category: Tungsten Information
- Published on Wednesday, 20 April 2016 17:46
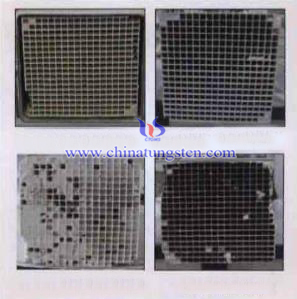
Tungsten Oxide Supplier: Chinatungsten Online www.tungsten-oxide.com | Tel.: 86 592 5129696; Fax: 86 592 5129797;Email:sales@chinatungsten.com |
Tungsten News & Prices, 3G Version: http://3g.chinatungsten.com | Molybdenum News & Molybdenum Price: http://news.molybdenum.com.cn |
Defect of Tungsten Trioxide SCR Denitration Catalyst
- Details
- Category: Tungsten Information
- Published on Wednesday, 20 April 2016 17:44
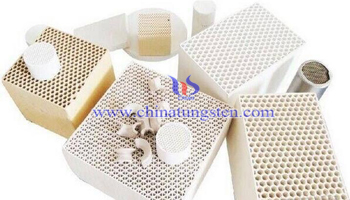
Tungsten Oxide Supplier: Chinatungsten Online www.tungsten-oxide.com | Tel.: 86 592 5129696; Fax: 86 592 5129797;Email:sales@chinatungsten.com |
Tungsten News & Prices, 3G Version: http://3g.chinatungsten.com | Molybdenum News & Molybdenum Price: http://news.molybdenum.com.cn |
Ion Diffusion Mechanism in Potassium Sodium Tungsten Bronze
- Details
- Category: Tungsten Information
- Published on Wednesday, 20 April 2016 17:34
Tungsten Oxide Supplier: Chinatungsten Online www.tungsten-oxide.com | Tel.: 86 592 5129696; Fax: 86 592 5129797;Email:sales@chinatungsten.com |
Tungsten News & Prices, 3G Version: http://3g.chinatungsten.com | Molybdenum News & Molybdenum Price: http://news.molybdenum.com.cn |
CCFL Functionally Graded Cemented Carbide (2/2)
- Details
- Category: Tungsten Information
- Published on Wednesday, 20 April 2016 15:42
Nitride process can form hardened layer with surface-rich cubic phase; while denitrification can form flexible layer of CCFL (cubic carbide free layer). Its mechanism is that the environment of nitrogen partial pressure of nitrogen balance sintered body partial pressure of nitrogen generated escape, which occurred in the formation of nitrogen and CCFL. Compared to the traditional structure of cemented carbide preparation process, the biggest difference between CCFL, the most critical part of functionally graded cemented carbide is that the sintering process.
Since the atomic diffusion rate in the liquid phase faster, CCFL typically select a liquid phase is formed at the stage of sintering becomes gradient and usually uses mixed atmosphere of argon and nitrogen to prevent nitrogen atom escape. Afterwards, we use micro-hardness method, nano-indentation method and XRD (X-ray diffraction) to measure the hardness, fracture toughness and stress of CCFL cemented carbide. The results show that the change in hardness is proportional to the content of binder phase, CCFL decrease in hardness, fracture toughness increased, and the overall stress in a weak state, which inhibits the cracks formation and expansion.
There are many factors of CCFL cemented carbide, such as sintering, carbon and nitrogen content and related compounds. With the extension of sintering time and the sintering temperature, CCFL thickness also increases and the rate of formation has been quickened; with the increase of nitrogen content, nitrogen has a larger range of activity, which CCFL driving force increased, the rate of formation improved; high carbon content can significantly increase the amplitude of the Co-rich, conducive to the formation of CCFL. In addition, the nitride and carbide content increases from zero, CCFL forming ability enhanced, increasing the thickness, but the solubility of nitrogen in the binder phase is limited, and when it is saturated at this time forming ability of CCFL is the best. After the increase nitrides, undissolved nitride takes longer to dissolve and diffusion will hinder the formation of CCFL.
Tungsten Carbide Supplier: Chinatungsten Online tungsten-carbide.com.cn | Tel.: 86 592 5129696; Fax: 86 592 5129797;Email:sales@chinatungsten.com |
Tungsten News&Tungsten Prices, 3G Version: http://3g.chinatungsten.com | Molybdenum News & Molybdenum Price: http://news.molybdenum.com.cn |
CCFL Functionally Graded Cemented Carbide (1/2)
- Details
- Category: Tungsten Information
- Published on Wednesday, 20 April 2016 15:40
Tungsten carbide, also called cemented carbide, is composed of hard phase WC and binder phase Co, which has higher hardness, strength and excellent wear resistance and has been widely used in metal cutting industries. In order to further improve the hardness and wear resistance of tungsten carbide cutting tools, in the actual production is often by adjusting the alloy binder phase content and add cubic carbides (such as TiC, TaC, Cr3C2, etc.) or the like by introducing coating technology (such as CVD chemical vapor deposition, PVD physical vapor deposition) higher in the cemented carbide substrate surface coated surface hardness, chemically more stable phase ceramic layer. However, there are some differences in the coefficient of thermal expansion and binding force between tungsten carbide matrix and coating layer, so the coating will crack and even peel off at work, which remarkably affects the using properties of tungsten carbide coated cutting tools and decreases the overall efficiency.
New functionally graded cemented carbide can effectively inhibit the formation and spreading of cracks to the substrate coating cracks and improve the reliability and service life of tungsten carbide cutting tools. From the component point of view, it can be divided functionally graded cemented carbide non-equilibrium carbon and nitrogen carbide. Unbalanced carbide or carbon, said carbon-poor carbide carburizing process can be prepared for two-phase drilling with carbide; The nitrogen-containing alloy can be divided according to the internal balance of nitrogen partial pressure difference between the pressure of the nitrogen balance in the environment can be achieved nitride, and nitrogen, and forming two distinct surface.
Tungsten Carbide Supplier: Chinatungsten Online tungsten-carbide.com.cn | Tel.: 86 592 5129696; Fax: 86 592 5129797;Email:sales@chinatungsten.com |
Tungsten News&Tungsten Prices, 3G Version: http://3g.chinatungsten.com | Molybdenum News & Molybdenum Price: http://news.molybdenum.com.cn |
Use and Identify Tungsten Electrodes Correctly in Arc Welding
- Details
- Category: Tungsten Information
- Published on Tuesday, 19 April 2016 18:41
Gas tungsten arc welding (GTAW) and plasma arc welding (PAW) usually use nonconsumable tungsten electrode in welding process. These tungsten electrodes have a variety of compositions and shape, and each composition serves a specific purpose:
Pure tungsten electrodes (AWS classification EWP) contain 99.50 percent tungsten. They provide good arc stability for AC welding on aluminum and magnesium. Their color designation is green.
2% thoriated tungsten electrodes (AWS classification EWTh-2) contain 1.70 to 2.20 percent thorium and are the type most commonly used. Compared with pure tungsten, they work exceptionally well for DC electrode negative or straight polarity on carbon and stainless steels. Their color designation is red.
2% ceriated tungsten electrodes (AWS classification EWCe-2) contain 1.80 to 2.20 percent cerium. They has best performance in DC welding at low current settings, but can be used in AC processes as well. Their color designation is orange.
1.5% lanthanated tungsten electrodes (AWS classification EWLa-1.5) contain 1.30 to 1.70 percent lanthanum or lanthana. These have many of the same advantages as ceriated electrodes and closely resemble the conductivity characteristics of 2 percent thoriated tungsten. Their color designation is gold.
Zirconiated tungsten electrodes (AWS classification EWZr-1) contain 0.15 to 0.40 percent zirconium. It is suitable for AC welding, but no recommended zirconiated for DC welding. Their color designation is brown.
Tungsten Metals Supplier: Chinatungsten Online www.tungsten.com.cn | Tel.: 86 592 5129696; Fax: 86 592 5129797;Email:sales@chinatungsten.com |
Tungsten News & Prices, 3G Version: http://3g.chinatungsten.com | Molybdenum News & Molybdenum Price: http://news.molybdenum.com.cn |
Six Tips for Better GTAW Results-Tungsten Electrode Selection
- Details
- Category: Tungsten Information
- Published on Tuesday, 19 April 2016 18:37
There are 6 tips for using GTAW (gas tungsten arc welding). To keep these tips in mind for GTAW applications can help you save time and money in rework and to help ensure a quality finished weld. These 6 tips include knowing the welding material, selection the right tungsten, keeping machine clean, clamping tight to prevent distortion, testing weld and using gas lenses. As follow we will introduce how to select right tungsten electrode.
As we know, at the center of the GTAW process is the tungsten electrode, a nonconsumable metallic element that carries the welding current to the arc. So selecting the right tungsten electrode is key point for GTAW welding performance. The thickness of the material being welded and welding amperage is two important factors to consider when choosing tungsten electrode.
Tungsten electrodes come in a variety of diameters, typically from 0.020 to 5⁄32 inch, and are available in industry-standard lengths of 7 inch. Custom lengths are also available but tend to cost more. The electrodes are composed of either pure tungsten or tungsten doped with rare earth elements and oxides. To eliminate confusion about the various types, each electrode is color-coded at the tip to denote its type.
Depending on the material being welded, you can choose from pure tungsten—typically used for AC welding of aluminum on older transformer-designed machines—or ceriated, lanthanated, rare earth, and thoriated tungsten electrodes is also the best choice. Each option has characteristics suited for certain applications and materials. Ceriated tungsten electrode is good general tungsten electrode that can be used with most everything, while thoriated and lanthanated tungsten are good options for welding stainless steel and exotic materials.
Thoriated tungsten electrode provides many benefits because of its high ability to emit electrons, which allows the arc to come off the tip of the tungsten. However, note that thoriated tungsten contains low levels of radioactivity, so be sure to follow the manufacturer’s warnings, instructions, and the Material Safety Data Sheet (MSDS).
Tungsten Metals Supplier: Chinatungsten Online www.tungsten.com.cn | Tel.: 86 592 5129696; Fax: 86 592 5129797;Email:sales@chinatungsten.com |
Tungsten News & Prices, 3G Version: http://3g.chinatungsten.com | Molybdenum News & Molybdenum Price: http://news.molybdenum.com.cn |
Potassium Sodium Tungsten Bronze Single Crystal
- Details
- Category: Tungsten Information
- Published on Tuesday, 19 April 2016 17:58
Tungsten Oxide Supplier: Chinatungsten Online www.tungsten-oxide.com | Tel.: 86 592 5129696; Fax: 86 592 5129797;Email:sales@chinatungsten.com |
Tungsten News & Prices, 3G Version: http://3g.chinatungsten.com | Molybdenum News & Molybdenum Price: http://news.molybdenum.com.cn |
The Detection of Carbon and Sulfur of EMM Only by Tungsten Granule
- Details
- Category: Tungsten Information
- Published on Tuesday, 19 April 2016 16:47
The full name of EMM is electrolytic manganese metal. EMM has a high purity and it can increase the hardness of the metal materials. Tungsten granule is mainly applied to Carbon sulfur analyzer to analyze the content of carbon and sulfur. To analyze by tungsten particles is a much simpler way. Manganese metal is a kind of metal with a silvery-white color. On the other hand, manganese is hard and easy to be oxidized at an elevated temperature. The metal manganese is widely distributed in nature and the number of manganese is the three-ten thousand of the total number of atoms in the earth’s crust.
For traditional ways to detect the content of carbon and sulfur of manganese metal, the choice of flux include the following types: pure iron and tungsten granule, tin particles and tungsten granule, pure iron plus tungsten granule plus tin particles. The operator cannot control the number of flux well while operation from the three types. If the amount of flux is too much, it would make the samples splash easily or produce dust while burning. If the amount of flux is too less, it would not burn fully, both will have a great impact on the results of the analysis.
Operator selects standard samples of manganese metal and tungsten granule to detect for 3-5 times, and the repeatability of the result will be better. Operator selects a common electrode sample and a high manganese sample, puts about 0.35g of manganese metal specimens in a crucible uniformly, and covers about 1.5g of tungsten granule uniformly to make the analysis. And then, the result of relative standard deviation is less than 5%. It shows that the determination of carbon and sulfur of EMM only by tungsten granule has a very high precision.
Consider tungsten particles as a flux to detect the content of carbon and sulfur of EMM not only can reduce the cost of sample analysis, but also can greatly improving the work efficiency. In addition, the operation of this method is simple.
Tungsten Metals Supplier: Chinatungsten Online www.tungsten.com.cn | Tel.: 86 592 5129696; Fax: 86 592 5129797;Email:sales@chinatungsten.com |
Tungsten News & Prices, 3G Version: http://3g.chinatungsten.com | Molybdenum News & Molybdenum Price: http://news.molybdenum.com.cn |
Operational Principle of Carbon Sulfur Analyzer
- Details
- Category: Tungsten Information
- Published on Tuesday, 19 April 2016 16:26
Carbon and sulfur analyzer is a high-tech product with a world leading level. It has a high accuracy and a wide measurement range when analyze carbon and sulfur. In the determination of carbon and sulfur content in carbon sulfur analyzer, people commonly consider tungsten granule as a flux to further improve the results of measurement. The operator should have knowledge about the principles of carbon sulfur analyzer in order to reduce unnecessary mistakes during operation. If the operator can understand the principles of carbon sulfur analyzer well, it would make the carbon and sulfur analyzer work in a top condition. There are some important principles of the analyzer that operator should pay attention to.
First of all, oxygen should be purified, and then import it into the high-frequency furnace or resistance furnace. What’s more, the sample needs to be oxidized by oxygen through the burner under a high temperature, so that carbon and sulfur of the sample can be oxidized into carbon dioxide, carbon monoxide and sulfur dioxide. After being passed through dust separation plant and water renovation unit, oxides would be loaded into detection cell of sulfur by oxygen to detect the content of sulfur. Thereafter, the mixed gas which consists of carbon dioxide, carbon monoxide, sulfur dioxide and oxygen will get into a furnace with a heating catalyst and sulfur dioxide. In this furnace, carbon monoxide would be catalyzed into carbon dioxide and sulfur dioxide would be catalyzed into sulfur trioxide. When the mixed gas gets into desulfurization reagent tube, and then the operator should import it into detection cell of carbon to detect the carbon content. As a high-quality additive, tungsten granule will facilitate the release of carbon dioxide and sulfur dioxide at the temperature of 650 ℃ inside the analyzer. Tungsten granule can make reaction sufficiently to improve the measurement accuracy of the results.
Tungsten Metals Supplier: Chinatungsten Online www.tungsten.com.cn | Tel.: 86 592 5129696; Fax: 86 592 5129797;Email:sales@chinatungsten.com |
Tungsten News & Prices, 3G Version: http://3g.chinatungsten.com | Molybdenum News & Molybdenum Price: http://news.molybdenum.com.cn |