WO3 Desulfurization Catalyst Environmental Effects
- Details
- Category: Tungsten Information
- Published on Thursday, 31 March 2016 16:22
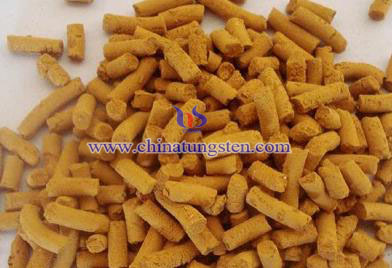
Tungsten Oxide Supplier: Chinatungsten Online www.tungsten-oxide.com | Tel.: 86 592 5129696; Fax: 86 592 5129797;Email:sales@chinatungsten.com |
Tungsten News & Prices, 3G Version: http://3g.chinatungsten.com | Molybdenum News & Molybdenum Price: http://news.molybdenum.com.cn |
Reaction Time Effect on CsxWO3 Powder Absorbance
- Details
- Category: Tungsten Information
- Published on Thursday, 31 March 2016 10:13
Tungsten Oxide Supplier: Chinatungsten Online www.tungsten-oxide.com | Tel.: 86 592 5129696; Fax: 86 592 5129797;Email:sales@chinatungsten.com |
Tungsten News & Prices, 3G Version: http://3g.chinatungsten.com | Molybdenum News & Molybdenum Price: http://news.molybdenum.com.cn |
Lanthanum Tungsten Electrode Analysis
- Details
- Category: Tungsten Information
- Published on Wednesday, 30 March 2016 16:16
Lanthanum tungsten electrode is mainly produced by powder metallurgy method. It is added 1%, 1.5% or 2% lanthanum oxide to tungsten powder, after doping, reduction, vertical melt, swaging and stretching to obtain lanthanum tungsten electrode. Lanthanum tungsten electrodes have good welding performance, long service life, and no radioactive contamination, so it is considered the best substitute for thorium tungsten electrode and it is widely used in tungsten inert gas welding (TIG welding), plasma welding and cutting field. By comparison electrical property found, lanthanum tungsten electrode’s electrical property is superior to cerium tungsten electrode and thoriated tungsten electrode. Lanthanum oxide, having low mobility and evaporation rate, can form a good lap dovetail organization, so lanthanum tungsten electrode has good high temperature creep performance.
After swaging process, La2O3 particle is evenly distributed over the tungsten grain and boundaries. If not properly control billet processing, it is prone to delamination or peeling. On the other hand, if feeding too fast in swaging process can also cause delamination or peeling.
After electrical property analysis understand the La and Ce distribution in lanthanum tungsten electrode and cerium tungsten electrode. At DC 200A, for 20min, the electrode tip working at high temperature 2600 ~ 3000 ℃, La2O3 and Ce2O3 from the center migrate to the surface and to the tip. Their average content decreased gradually from the edge to the center portion and there has almost no La2O3 andCe2O3. Ce2O3 has faster migration and evaporation rate.
After electrical property test observed electrode’s microstructure found that the electrode grains grow along axial direction. The grains aspect ratio of cerium tungsten electrodes and lanthanum tungsten electrode is respectively (3: 1 to 15: 1), (3: 1 to 7: 1). In lanthanum tungsten electrode there are a large number of bubbles and a small amount of La2O3 particle. Besides, grain boundaries are dovetail lap organizations which can impede grain boundary sliding laterally, so it has better thermal shock, creep performance. Lanthanum tungsten electrode electrical property is better than other electrodes.
Tungsten Metals Supplier: Chinatungsten Online www.tungsten.com.cn | Tel.: 86 592 5129696; Fax: 86 592 5129797;Email:sales@chinatungsten.com |
Tungsten News & Prices, 3G Version: http://3g.chinatungsten.com | Molybdenum News & Molybdenum Price: http://news.molybdenum.com.cn |
Composite Rare Earth Tungsten Electrode Production Technology
- Details
- Category: Tungsten Information
- Published on Wednesday, 30 March 2016 16:13
Adding rare earth into tungsten electrodes can refine tungsten grain and can change the tungsten electrode plastic-brittle transition temperature, to improve the performance of the electrode. But composite rare earth electrode production technology is more complex and production costs are high, and therefore could not be widely used. Improving production technology of composite electrode has important significance for the composite electrode industrial production. Production technology includes the doping process, reduction process and sintering process.
Thorium tungsten electrode generally uses tungsten oxide and thorium oxide as raw material doped directly. Cerium tungsten electrode generally uses tungsten oxide and rare earth nitrate as raw material to doping. For multiple composite rare earth tungsten electrode usually uses APT and rare earth nitrates as raw material doped directly. This doping method not only efficient, and eliminates APT calcining process, shorten the production process. Uniformly doped with these two materials can improve the mechanical property of the composite electrode so that the electrode has a high finished product rate and high electron emission property.
Composite rare earth tungsten electrodes are usually produced by powder metallurgy method. In this production method, the quality of metal powder plays a decisive role on electrode quality. During the reduction process usually uses secondary reduction method. In the first reduction appropriate increase particles size and increase reduction temperature gradients which are conducive to improving the particle size of the metal powder.
Sintering process mainly affects electrode’s density, grain size, rare earth oxides distribution and high temperature evaporation loss amount and so on. During sintering process for composite rare earth tungsten electrode production should control the sintering temperature. Because if the sintering temperature too high the tungsten grain will grow dramatically to reduce the diffusion coefficient of rare earth oxide, to increase electrode’s burning rate. And the sintering temperature too high will make the rare earth oxide forming low-melting substance grew up together, to increased segregation, resulting in rare earth oxide evaporation loss, unevenly distributed.
Tungsten Metals Supplier: Chinatungsten Online www.tungsten.com.cn | Tel.: 86 592 5129696; Fax: 86 592 5129797;Email:sales@chinatungsten.com |
Tungsten News & Prices, 3G Version: http://3g.chinatungsten.com | Molybdenum News & Molybdenum Price: http://news.molybdenum.com.cn |
Tungsten Gold Jewelry Box
- Details
- Category: Tungsten Information
- Published on Wednesday, 30 March 2016 15:18
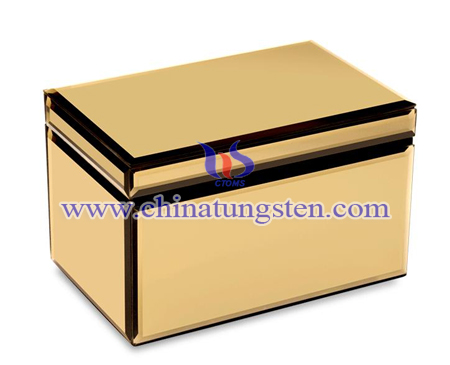
Tungsten Gold Plated Supplier: Chinatungsten Online tungsten-alloy.com | Tel.: 86 592 5129696; Fax: 86 592 5129797;Email:sales@chinatungsten.com |
Tungsten News & Prices, 3G Version: http://3g.chinatungsten.com | Molybdenum News & Molybdenum Price: http://news.molybdenum.com.cn |
Tungsten Gold-Plated Bar For National Day
- Details
- Category: Tungsten Information
- Published on Wednesday, 30 March 2016 15:15
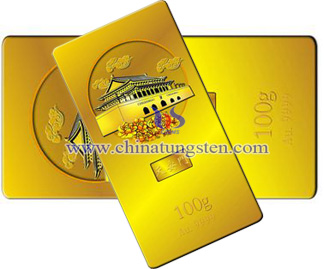
Tungsten Gold Plated Supplier: Chinatungsten Online tungsten-alloy.com | Tel.: 86 592 5129696; Fax: 86 592 5129797;Email:sales@chinatungsten.com |
Tungsten News & Prices, 3G Version: http://3g.chinatungsten.com | Molybdenum News & Molybdenum Price: http://news.molybdenum.com.cn |
Tungsten Carbide Mixture Wet Milling-spray Drying (2/2)
- Details
- Category: Tungsten Information
- Published on Wednesday, 30 March 2016 15:11
In the process of preparation, it is significant that choosing the granularity and controlling the balance of carbon and oxygen. It requires uniform WC powder and the original granularity is equal to tungsten carbide granularity after sintering. The balance of carbon and oxygen is not only the most critical but also the most difficult to control. Due to the fluctuation range of the content of W-C-Co ternary alloy allowed in C is extremely limited, the decarbonized phase (η phase) and carburizing phase (graphite phase) will have a great impact on tungsten carbide performance.
Next, wet milling adds WC powder, Co powder and additives or carbides prepared into the grinder for milling until the ground to the desired particle size and thoroughly mixed with the Co. In the wet milling process, only the destruction of the dispersed particles and aggregates, crushing and dispersing the material fully, in order to ensure effective mixing between each component powder. And wet milling will be specifically divided into rolling milling and stirring milling. Roll milling uses the grinding ball and grinding media (the mixture) rotated to a certain height in the friction and centrifugal force to fall freely on the tube material will have an impact and grinding effect of grinding material and stir well. While stir milling depends on the power drive shaft rotatable stirring and stirring ball material, cut its rotation and centrifugal force generated by the component material and the ball moves in radial. Due to the end of the tube and the tube wall resistance and resistance in the material sphere generate vertical component and tangential component and material spiraling ball, colliding with each other, forming a complex friction movement.
Spray-drying tower is a kind of advanced process in tungsten carbide mixture drying and granulation. After the mixture after the wet grinding with pumped into the feed tank, stir heating, pressure slurry is fed to the atomizer atomized into the tower from the bottom of the tower. After oil and gas heat exchanger heated nitrogen N2 gas from the blower to the top of the tower distributor and uniformly into the tower of the atomized slurry was dry granulated. Pellets after drying off the bottom of the tower back for recycling. Finally, after separated with fine grain preliminarily, washed and heated, the gas can be reused.
Tungsten Carbide Supplier: Chinatungsten Online tungsten-carbide.com.cn | Tel.: 86 592 5129696; Fax: 86 592 5129797;Email:sales@chinatungsten.com |
Tungsten News&Tungsten Prices, 3G Version: http://3g.chinatungsten.com | Molybdenum News & Molybdenum Price: http://news.molybdenum.com.cn |
Tungsten Carbide Mixture Wet Milling-spray Drying (1/2)
- Details
- Category: Tungsten Information
- Published on Wednesday, 30 March 2016 15:10
Tungsten carbide is basically composed of WC and Co, which has high hardness, high strength, high wear resistance and excellent chemical stability and can be widely used in various cutting tools, drilling tools and so on. Now tungsten carbide has been a new development in the field of electronics as well as some in the medical field, such as PCB micro drills and drills for dental, which place a greater demand on tungsten carbide properties. Therefore, viewed from the raw material, high quality of tungsten carbide products is determined by tungsten carbide mixture. If the mixture has poor quality, even though the process and equipments are advanced, the final products can not be well. Currently, there are two preparation of domestic carbide mixture, one is wet milling-machinery granulation process, the other is wet milling - spray drying process.
Wet milling-machinery granulation process has simple equipment and operations, but the drying and granulation should be divided into two parts so that it needs a long time and the mixture will be oxidized by contacted with the air or other impurities. Although tungsten carbide mixture wet milling-spray drying equipment is more complex, pre-investment is relatively high, its high level of automation of production, produce a better blend of mobility, uniform particle size distribution, bulk density stable and be able to meet the production needs of high-volume, high-performance tungsten carbide products. Compared with conventional wet milling-machinery granulation, the basic process of wet milling-spray drying is preparation → wet milling → spray drying → the mixture, which takes place of vacuum drying, rubbing sieve, granulation and many steps and remarkably improves the overall efficiency.
Tungsten Carbide Supplier: Chinatungsten Online tungsten-carbide.com.cn | Tel.: 86 592 5129696; Fax: 86 592 5129797;Email:sales@chinatungsten.com |
Tungsten News&Tungsten Prices, 3G Version: http://3g.chinatungsten.com | Molybdenum News & Molybdenum Price: http://news.molybdenum.com.cn |
Cordierite Tungsten Trioxide Denitration Catalyst
- Details
- Category: Tungsten Information
- Published on Wednesday, 30 March 2016 14:51
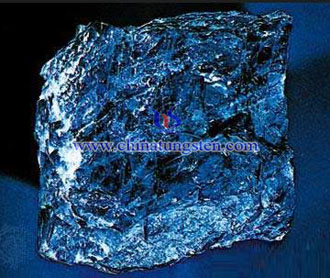
Tungsten Oxide Supplier: Chinatungsten Online www.tungsten-oxide.com | Tel.: 86 592 5129696; Fax: 86 592 5129797;Email:sales@chinatungsten.com |
Tungsten News & Prices, 3G Version: http://3g.chinatungsten.com | Molybdenum News & Molybdenum Price: http://news.molybdenum.com.cn |
Tungsten Trioxide SCR Flue Gas Denitration Catalyst Affecting Factors
- Details
- Category: Tungsten Information
- Published on Wednesday, 30 March 2016 14:48
Tungsten Oxide Supplier: Chinatungsten Online www.tungsten-oxide.com | Tel.: 86 592 5129696; Fax: 86 592 5129797;Email:sales@chinatungsten.com |
Tungsten News & Prices, 3G Version: http://3g.chinatungsten.com | Molybdenum News & Molybdenum Price: http://news.molybdenum.com.cn |