Waste SCR Denitration Catalyst Recycles Tungsten Trioxide - Secondary Alkaline Leaching Method
- Details
- Category: Tungsten Information
- Published on Thursday, 24 March 2016 17:24
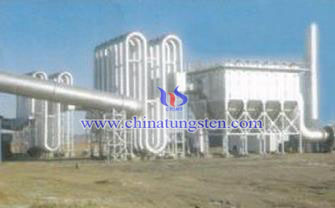
Tungsten Oxide Supplier: Chinatungsten Online www.tungsten-oxide.com | Tel.: 86 592 5129696; Fax: 86 592 5129797;Email:sales@chinatungsten.com |
Tungsten News & Prices, 3G Version: http://3g.chinatungsten.com | Molybdenum News & Molybdenum Price: http://news.molybdenum.com.cn |
Tungsten Carbide Wear Plate — Wear Form(2/2)
- Details
- Category: Tungsten Information
- Published on Thursday, 24 March 2016 17:13
Another failure form of tungsten carbide wear plate is solder peeling bore wear. Under the impact of concrete, the surface of the ring alloy plate glasses has cracks, which is due to poor wear resistance of its internal bore, can not fully resist the impact of concrete and wear. Flowing concrete will has relative movement with internal bore of tungsten carbide wear plate, which makes the solid surface and the material properties of the surrounding surface has changed, easily deformed due to uneven force. Therefore, enhanced tungsten carbide wear plate bore is critical and it has enhanced the protection of surface alloy ring and reduces the deformation effect. In order to improve the service life of tungsten carbide wear plate, we can improve the wear resistance of internal bore of wear plate from material and structure.
We have two choices from the material that welding electrode wear and use tungsten carbide directly. By experimental comparison can be drawn with the following electrode wear carbide abrasive wear table:
From the graph above we can clearly see that the wear resistance of tungsten carbide is 5 times better than the welding electrode so that tungsten carbide as the material for the internal bore is a best choice. For the bore structure of wear plate, in order to avoid high temperatures generated inlaid alloy caused defects, the researchers used a related set of inlaid alloy structure, effectively extends the life of tungsten carbide wear plate.
Tungsten Carbide Supplier: Chinatungsten Online tungsten-carbide.com.cn | Tel.: 86 592 5129696; Fax: 86 592 5129797;Email:sales@chinatungsten.com |
Tungsten News&Tungsten Prices, 3G Version: http://3g.chinatungsten.com | Molybdenum News & Molybdenum Price: http://news.molybdenum.com.cn |
Tungsten Carbide Wear Plate — Wear Form(1/2)
- Details
- Category: Tungsten Information
- Published on Thursday, 24 March 2016 17:10
Generally, the medium of tungsten carbide wear plate is concrete, which is composed of cement, water, fine coarse aggregate and other additives and the hardness index converted to a Rockwell hardness of between about HRC40-50. In the process, the main wear forms can be divided into two types, one is in the process of cutting ring reversal, wear plate and floating cutting ring contacts and has grain wear and erosion; the other is in the process of inhaling or pumping, the internal hole of wear plate has low stress wear and erosion.
After concrete pump working for some time, there is a gap between tungsten carbide wear plate and cutting ring. Theoretically, grinding compounds friction and grinding compounds wear of the sliding contact surfaces are generally the form of typical wear. Both wear plate and cutting ring are tungsten carbide and form a pair of friction, the floating cutting ring swings back and forth on tungsten carbide wear plate quickly. Both of them form grain wear by surface contact constantly.
In addition, there are still ore, quartz sand and some other hard particles, and the concrete also belongs to corrosive medium, which will further exacerbate the grinding compounds wear of tungsten carbide wear plate. At present, with the increasing height of the building, pumping height and pressure is also rising, which for carbide glasses plate and cutting ring put forward higher requirements. As time goes by, it will gradually appear larger gaps or partial abrasion between the cutting ring and the wear plate, and leading to failure of the wear plate finally.
Tungsten Carbide Supplier: Chinatungsten Online tungsten-carbide.com.cn | Tel.: 86 592 5129696; Fax: 86 592 5129797;Email:sales@chinatungsten.com |
Tungsten News&Tungsten Prices, 3G Version: http://3g.chinatungsten.com | Molybdenum News & Molybdenum Price: http://news.molybdenum.com.cn |
Tungsten Sailing Counterweight
- Details
- Category: Tungsten Information
- Published on Thursday, 24 March 2016 15:46
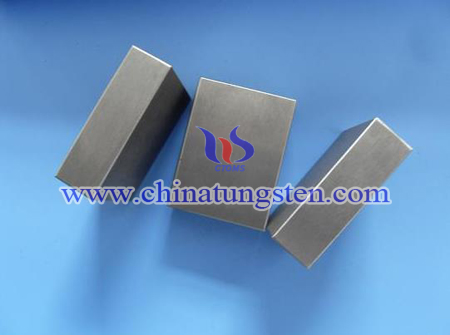
Tungsten Alloy Supplier: Chinatungsten Online www.tungsten-alloy.com | Tel.: 86 592 5129696; Fax: 86 592 5129797;Email:sales@chinatungsten.com |
Tungsten News & Prices, 3G Version: http://3g.chinatungsten.com | Molybdenum News & Molybdenum Price: http://news.molybdenum.com.cn |
Rare Earth Doped Tungsten Electrode History
- Details
- Category: Tungsten Information
- Published on Thursday, 24 March 2016 15:27
Pure tungsten electrode is the earliest used electrode material. Mainly because tungsten has high melting point, low vapor pressure and other properties. However, pure tungsten work function is too high and at high temperature recrystallization will occur to form equiaxed crystal structure, so that the material becomes brittle and fracture. In order to improving the recrystallization and reducing the work function temperature of the tungsten electrode, after research people developed a series of rare earth doped tungsten electrodes.
Rare earth doped tungsten electrode is based on tungsten doped with some refractory oxide as the active material, lowering the work function of tungsten. Common rare earth doped tungsten electrodes are thorium tungsten electrode, cerium tungsten electrode, lanthanum tungsten electrode and zirconium tungsten electrode. Thorium tungsten electrode was invented in 1913. It has good performance, but radioactive, so long-term use would endanger human health and cause environmental pollution. Comparing with thorium tungsten electrode, cerium tungsten electrode and lanthanum tungsten electrode has a relatively better performance, and no radioactive, having broad application prospects.
Rare earth doped tungsten electrode began at former Soviet Union. The Soviet Union had reports of rare earth doped tungsten electrode before the 1960s. China, in 1973, had successful developed and used cerium tungsten electrode.
The late 1980s, Japanese researchers achieved some progress in new electrode material, developed a series of rare earth tungsten electrodes, including tungsten electrodes doped with single oxide, tungsten electrodes doped with two oxide and tungsten electrodes doped with three oxide. In tungsten electrodes doped with single oxide, lanthanum tungsten electrode overall performance is better, followed by yttrium tungsten electrode and cerium tungsten electrode. In tungsten electrodes doped with two oxides, producing it with following proportioning will have better property, La2O3: CeO2 = 1: 1, La2O3: Y2O3 = 1: 3, CeO2: Y2O3 = 1: 3. Tungsten electrodes doped with there oxides (La2O3: CeO2: Y2O3 = 1: 1: 3) have low work function, and low operating temperatures.
Tungsten Metals Supplier: Chinatungsten Online www.tungsten.com.cn | Tel.: 86 592 5129696; Fax: 86 592 5129797;Email:sales@chinatungsten.com |
Tungsten News & Prices, 3G Version: http://3g.chinatungsten.com | Molybdenum News & Molybdenum Price: http://news.molybdenum.com.cn |
Tungsten Electrode and Shielding Gas in TIG Welding
- Details
- Category: Tungsten Information
- Published on Thursday, 24 March 2016 15:24
Tungsten electrode has high melting point, high boiling point, high strength, low thermal conductivity and low high temperature volatile and other good property, so it is often as a non-consumable electrode applied in welding field. Pure tungsten electrode has poor electron emission performance doped with rare earth rare earth to improve electrode property. Rare earth doped tungsten electrode has good electron emission performance and long service life. Besides, it is easy to arcing.
During welding, shielding gas is a protective medium of weld region but it is a gaseous medium of arcing. Therefore, physical and chemical property of protection gas will not only affect the protective effect, will also have some impact on the arcing ignition, welding process stability and quality of arcing.
For TIG welding (tungsten inert gas welding), there are three kind of shielding gas, including argon, helium and mixture gas. Among these shielding gas, the most widely used is argon. Argon is an inert gas. It does not react with welding metal and not soluble in the metal as well. Besides, the density of argon is heavier than air, and specific heat capacity and thermal conductivity smaller than air, so it can effective protect the molten metal from air, oxygen, nitrogen, hydrogen and other harmful elements effect. These features make argon showed good performance in welding process. It not only can play a good protective effect, but it can to stabilize the arc.
Helium is also an inert gas. It has good cooling effect, so the arc energy density is large and arc column is small and focused, while the weld joint has good penetration rate. But helium has high ionization potential, big thermal conductivity, so during the welding arc is more difficult and the energy loss is large. In generally, it is used for nuclear reactor cooling rods and large thickness aluminum alloy welding.
Mixture gas includes a certain proportion of two kind of inert gas, including argon-hydrogen mixed gas and argon-helium mixed gas. During the welding process, mixture gas in favor of increasing thermal power of arc, increasing the weld joint penetration rate, improving production efficiency.
Tungsten Metals Supplier: Chinatungsten Online www.tungsten.com.cn | Tel.: 86 592 5129696; Fax: 86 592 5129797;Email:sales@chinatungsten.com |
Tungsten News & Prices, 3G Version: http://3g.chinatungsten.com | Molybdenum News & Molybdenum Price: http://news.molybdenum.com.cn |
Tungsten Gold-Plated Coin for Labor Day
- Details
- Category: Tungsten Information
- Published on Thursday, 24 March 2016 11:10
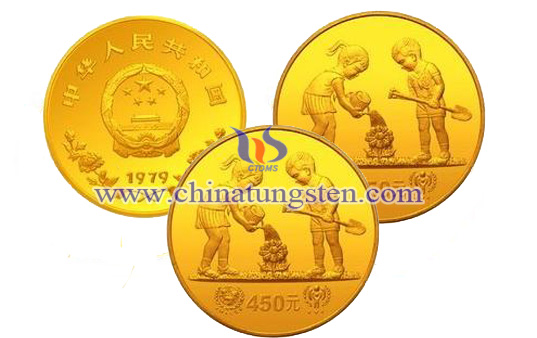
Tungsten Gold Plated Supplier: Chinatungsten Online tungsten-alloy.com | Tel.: 86 592 5129696; Fax: 86 592 5129797;Email:sales@chinatungsten.com |
Tungsten News & Prices, 3G Version: http://3g.chinatungsten.com | Molybdenum News & Molybdenum Price: http://news.molybdenum.com.cn |
Tungsten Gold-Plated Coin for Moon Festival
- Details
- Category: Tungsten Information
- Published on Thursday, 24 March 2016 11:07
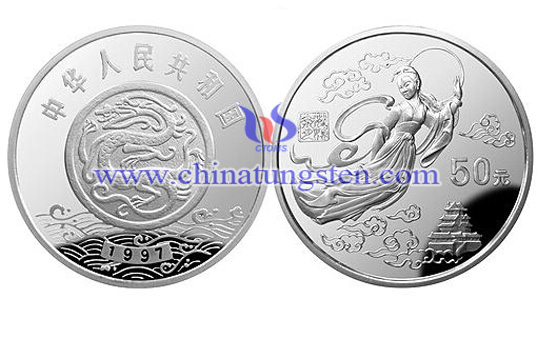
Tungsten Gold Plated Supplier: Chinatungsten Online tungsten-alloy.com | Tel.: 86 592 5129696; Fax: 86 592 5129797;Email:sales@chinatungsten.com |
Tungsten News & Prices, 3G Version: http://3g.chinatungsten.com | Molybdenum News & Molybdenum Price: http://news.molybdenum.com.cn |
WO3 Enhances SCR Denitration Catalyst Activity and Thermal Stability
- Details
- Category: Tungsten Information
- Published on Wednesday, 23 March 2016 19:53
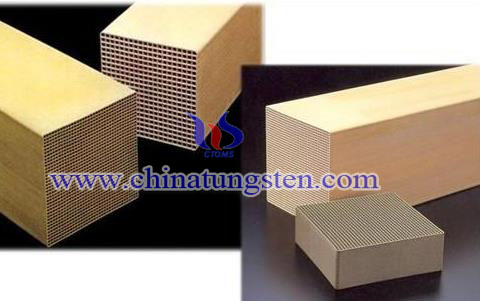
Tungsten Oxide Supplier: Chinatungsten Online www.tungsten-oxide.com | Tel.: 86 592 5129696; Fax: 86 592 5129797;Email:sales@chinatungsten.com |
Tungsten News & Prices, 3G Version: http://3g.chinatungsten.com | Molybdenum News & Molybdenum Price: http://news.molybdenum.com.cn |
Waste Cellular SCR Denitration Catalyst Recovers WO3
- Details
- Category: Tungsten Information
- Published on Wednesday, 23 March 2016 19:51
Tungsten Oxide Supplier: Chinatungsten Online www.tungsten-oxide.com | Tel.: 86 592 5129696; Fax: 86 592 5129797;Email:sales@chinatungsten.com |
Tungsten News & Prices, 3G Version: http://3g.chinatungsten.com | Molybdenum News & Molybdenum Price: http://news.molybdenum.com.cn |