Tungsten Carbide Buttons Used for DTH Drill Mechanism (2/2)
- Details
- Category: Tungsten Information
- Published on Monday, 29 February 2016 17:37
To study the process of tungsten carbide DTH drilling buttons that can be summarized as follows several stages:
Stage I: Cracks emerge, at this stage tungsten carbide buttons just contact with the rock surface, rock stress is transmitted to the contact surface has not been fully released, brittle failure in the contact surface, meanwhile accompanied by the generation of micro-cracks;
Stage II: With the increasing stress, the rock contacted with tungsten carbide button has plastic deformation and forms cracking area;
Stage III: On the boundary of the region will have been pulverized tensile stress cracks, and gradually developed into an initial crack, the crack will be increasing stress and further expansion;
Stage IV: With the increase of stress, both side of the initial crack formation and generates corresponding tensile stress crack, was extended obliquely downward;
Stage V: Cracks form a funnel-shaped expanding and consequential damage leap forward.
In addition, except that the study on the mechanism of tungsten carbide DTH drill buttons, we should also notice that although tungsten carbide buttons have higher hardness and impact resistance, it is brittle and has lower wear resistance. The main pattern of invalid is corrosion, which includes grain wear, surface fatigue wear as well as adhesive wear. It is mainly due to in the process of drilling, the high temperature of the high-speed collision with rock buttons occurrence arising will make carbide hardness decreased and crushed quartz particles made of a soft but opposed the hard phase transition occurs. Therefore, It also put forward tungsten carbide buttons higher requirements, which can be added some element or coated with a high-performance materials to improve the wear resistance of the tooth carbide buttons.
Tungsten Carbide Supplier: Chinatungsten Online tungsten-carbide.com.cn | Tel.: 86 592 5129696; Fax: 86 592 5129797;Email:sales@chinatungsten.com |
Tungsten News&Tungsten Prices, 3G Version: http://3g.chinatungsten.com | Molybdenum News & Molybdenum Price: http://news.molybdenum.com.cn |
Tungsten Carbide Buttons Used for DTH Drill Mechanism (1/2)
- Details
- Category: Tungsten Information
- Published on Monday, 29 February 2016 17:36
DTH drill bit is a kind of high-performance tool, which is also the one of the most widely used in excavation, rock drilling work. It is suitable for drilling hard, hard and abrasive rock formations, relying on high impact energy have a great impact energy of rock cracking. And it has so many advantages, such as high efficiency of drilling, high impact energy, has shear crash and longer service life; especially its driving force is based on airflow, which sufficient airflow can take away the rock debris from the bottom to improve the efficiency of drilling and reduce the abrasion of tungsten carbide buttons. As for the choice of tungsten carbide button becomes essential, to be considered in accordance with DTH drill diameter as well as the impact on other aspects of work, number and position of the buttons determines whether a reasonable share DTH drill the impact on power.
Theoretically, tungsten carbide buttons used for DTH drill uses rotary impact for rock drilling, It has short impacting time, the buttons in an instant contact with the rock produces a huge impact and brittle rocks internal stress concentration, under the action of impact force generated volume very easily broken so that the efficiency of DTH drill has been improved. Furthermore, tungsten carbide DTH drill buttons while also impact rock rocks rotary cutting button and drill the ball pure axial pressure is significantly smaller than rotary cutting bit, the button wear is also reduced a lot , thereby improving the wear resistance and grinding of carbide DTH drill buttons, extended service life.
Tungsten Carbide Supplier: Chinatungsten Online tungsten-carbide.com.cn | Tel.: 86 592 5129696; Fax: 86 592 5129797;Email:sales@chinatungsten.com |
Tungsten News&Tungsten Prices, 3G Version: http://3g.chinatungsten.com | Molybdenum News & Molybdenum Price: http://news.molybdenum.com.cn |
An Invention for APT/AMT Production-Examples
- Details
- Category: Tungsten Information
- Published on Monday, 29 February 2016 17:34
EXAMPLE I
AMT Supplier: Chinatungsten Online www.ammonium-metatungstate.com | Tel.: 86 592 5129696; Fax: 86 592 5129797;Email:sales@chinatungsten.com |
Tungsten News&Tungsten Prices, 3G Version: http://3g.chinatungsten.com | Molybdenum News & Molybdenum Price: http://news.molybdenum.com.cn |
An Invention for APT/AMT Production
- Details
- Category: Tungsten Information
- Published on Monday, 29 February 2016 17:30
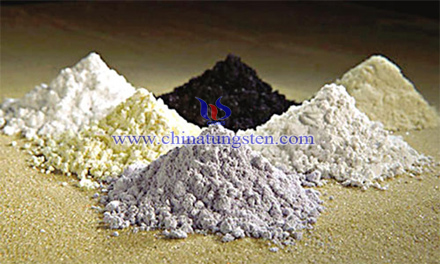
AMT Supplier: Chinatungsten Online www.ammonium-metatungstate.com | Tel.: 86 592 5129696; Fax: 86 592 5129797;Email:sales@chinatungsten.com |
Tungsten News&Tungsten Prices, 3G Version: http://3g.chinatungsten.com | Molybdenum News & Molybdenum Price: http://news.molybdenum.com.cn |
Doping Tungsten Trioxide Thin Film Property
- Details
- Category: Tungsten Information
- Published on Monday, 29 February 2016 16:45
Tungsten trioxide thin film will significantly improve certain properties, such as sensitivity and selectivity. Tungsten trioxide thin film doped with the metal ions can be incorporated or can be sputtered rare metals, such as palladium (Pd), platinum (Pt), gold (Au), silver (Ag), lithium (Li) and the like. Metal ions are in the form of he corresponding metal salt is added, such as LiN03, RbCl, CsCl, Bi (N03) 3, AgN03.
Sensing property will be significantly different with the incorporation of different metal ions additives. After doping palladium or platinum to hydrogen sensitivity, tungsten trioxide thin film electrochromic performance is greatly improved, especially the speed time and fade time are improved. Silver-doped tungsten trioxide thin film gas sensitivity can be increased. Tungsten thin film as hydrogen-sensitive element in the test shows that the addition of palladium or platinum can improve the sensitivity of the thin film with the hydrogen and palladium or platinum, which can shorten the response time.
The 1.0% Ag-doped tungsten trioxide thin film effectively improve the sulfur dioxide (SO2) sensitivity and selectivity at 450 ℃. Research shows that 15% Li-doped tungsten trioxide thin film is similar to the not doped tungsten trioxide thin film, but thin film doped coloration and its fade time is long. The Au-doped tungsten trioxide thin film improves the selectivity of NH3.
Tungsten Oxide Supplier: Chinatungsten Online www.tungsten-oxide.com | Tel.: 86 592 5129696; Fax: 86 592 5129797;Email:sales@chinatungsten.com |
Tungsten News & Prices, 3G Version: http://3g.chinatungsten.com | Molybdenum News & Molybdenum Price: http://news.molybdenum.com.cn |
Propylene Tungsten Trioxide Preparing Tungsten Carbide Powder
- Details
- Category: Tungsten Information
- Published on Monday, 29 February 2016 16:27
Propylene is colorless. It is slightly narcotic, flammable. It dissolves in water; and not dissolves in organic solvents. It is low toxicity substance. Propylene is the base stock material of three syntheses, mainly for the production of polypropylene, acrylonitrile, isopropanol, acetone, and propylene oxide. In addition, propylene is reacted on olefin bond; it can also react in the methyl group. Propylene polymerization in the presence of an acidic catalyst can form dimmers, trimmers, mixtures and tetramer. It can be used as high-octane fuel. Propylene and ethylene propylene rubber are generated. Propylene acid catalyst (sulfuric acid, hydrofluoric acid and the like) can become alkylation with isobutane to produce branched paraffin. Propylene in the presence of a catalyst with ammonia and oxygen in the air from the oxidation of ammonia to produce acrylonitrile, which can become a synthetic plastic, rubber, fiber and other polymer materials.
In the preparation of propylene tungsten trioxide prepare tungsten carbide powder, we make tungsten trioxide and propylene as raw material, the raw material is placed at 450 ℃ ~600 ℃. Then heating it after the mixed gas 90% Ar + 10% H2 at 1100 ℃ -1400 ℃ 2h, the material is crushed to obtain tungsten carbide powder .
Propylene tungsten trioxide prepares tungsten carbide powder, which improves the preparation of Chinese tungsten carbide powder level, and the obtained tungsten carbide powder can be used in production, which making China tungsten carbide powder resource advantages into economic advantages quickly, and makes a great contribution for China's export.
Tungsten Oxide Supplier: Chinatungsten Online www.tungsten-oxide.com | Tel.: 86 592 5129696; Fax: 86 592 5129797;Email:sales@chinatungsten.com |
Tungsten News & Prices, 3G Version: http://3g.chinatungsten.com | Molybdenum News & Molybdenum Price: http://news.molybdenum.com.cn |
Reasons of AMT / SiO2 The Catalyst Deactivation
- Details
- Category: Tungsten Information
- Published on Friday, 26 February 2016 18:18
AMT Supplier: Chinatungsten Online www.ammonium-metatungstate.com | Tel.: 86 592 5129696; Fax: 86 592 5129797;Email:sales@chinatungsten.com |
Tungsten News&Tungsten Prices, 3G Version: http://3g.chinatungsten.com | Molybdenum News & Molybdenum Price: http://news.molybdenum.com.cn |
Tungsten Copper Used in Vacuum Switch (2/2)
- Details
- Category: Tungsten Information
- Published on Friday, 26 February 2016 17:14
Tungsten copper composite materials require extremely low gas containing impurities (such as oxygen O2, N2 gas, etc.), it requires the use of a low gas content of raw materials and special process (high temperature sintering, vacuum infiltration, vacuum degassing, etc.) prepared. n these vacuum tungsten copper contact materials, in addition to conventional grades, the proportion of copper tungsten contact material has also developed a number of high-low tungsten copper tungsten copper, tungsten W is usually its content> 85%, such as W-10Cu, W-15Cu, etc., when asked tungsten copper material used in the case of low value when the closure, which can also add some other low melting point metal (such as antimony Sb, bismuth Bi, tellurium Te).
In contrast, there is a high copper content (60% -90%) of tungsten copper alloy, wherein W-70Cu Tungsten copper alloy products have been tested and Vickers hardness reaches1100MPa and 80% -85% IACS of high conductivity, and at 600 ℃ can still maintain a high hardness and conductivity, stable performance. Therefore, It also gradually replace some of the precious metal contacts (such as silver contacts, etc.), which significantly reducing the cost of the contact material. Overall, with the application of tungsten-copper composite materials more widely, for its new tungsten copper alloy materials research is also developing, such as tungsten copper with gradient structure, nano-crystalline tungsten copper, tungsten copper deformation processing, tungsten copper used in vacuum, tungsten copper with high or low content of tungsten, which replace the conventional materials in EDM, micro electronics, high temperature, military fields gradually. However, there are some problems of tungsten copper products in china, includes less high-end products, low utilization, the research and production are disjoint.
Tungsten Copper Supplier: Chinatungsten Online tungsten-copper.com | Tel.: 86 592 5129696; Fax: 86 592 5129797;Email:sales@chinatungsten.com |
Tungsten News & Prices, 3G Version: http://3g.chinatungsten.com | Molybdenum News & Molybdenum Price: http://news.molybdenum.com.cn |
Tungsten Copper Used in Vacuum Switch (1/2)
- Details
- Category: Tungsten Information
- Published on Friday, 26 February 2016 17:10
Tungsten copper composite material has high hardness, high melting point, high strength and sweating property so that it can be widely used in high temperature, military fields, aeronautics and astronautics, vacuum switch, electronic packaging, EDM electrode and so on. Here we highlight tungsten-copper composite material in vacuum switch electrical aspects. Theoretically, vacuum switch is a kind of pressure in the vacuum system for the protection of the automatic controller, small size, excellent performance, stability, ease of maintenance and long service life. It can be widely used in various industrial automation environments, such as water utilities, petrochemicals, railways, military, pipelines, ships and so on.
When the vacuum pressure is greater than the set point, the controller will automatically cut off the circuit, signals, to ensure the normal operation of the system. When the pressure in the system is higher or lower than the safe pressure, pressure sensor immediate action within the controller, the controller makes contact on or off, the device stops working; When the pressure within the system to a safe pressure range of the device, the pressure sensor inside the controller reset immediately, the contacts within the controller turned on or off, the device is working properly. In order to adapt some high-voltage as well as vacuum switch electrical demand, related researchers developed special vacuum switch of tungsten copper. It can be perfectly adapt to flammable, explosive, high temperature and low temperature, moisture, corrosive environments, and gradually dominate the high-voltage (6-35V) grid and electrification equipment.
Tungsten Copper Supplier: Chinatungsten Online tungsten-copper.com | Tel.: 86 592 5129696; Fax: 86 592 5129797;Email:sales@chinatungsten.com |
Tungsten News & Prices, 3G Version: http://3g.chinatungsten.com | Molybdenum News & Molybdenum Price: http://news.molybdenum.com.cn |
Preparing Ammonium Paratungstate from Worn-Out Tungsten Oxide 2/2
- Details
- Category: Tungsten Information
- Published on Friday, 26 February 2016 16:38
4) Vacuum filtration or pressing leaching, and translate the ammonium tungstate solution in a storage tank for 10~30 hours.
3. Preparation of ammonium paratungstate
1) Outlet the ammonium tungstate solution into a reaction kettle, heating to boiling, and then insulation for evaporating and concentrating till large numbers of APT crystal come into being;
2) Stop heating when the solution proportion dropped down to I.08~I.05, cooling the temperature below to 90℃ with stirring; then filtering the solution together with the APT crystal into the vacuum filtration or centrifugal, and washing with water for 3~4 times;
3) drying at the temperature of 80-130℃;
4) Cooling down and screening with 80 mesh sieve, inspecting, packaging, then we get ammonium paratungstate.
Advantages about this way to prepare ammonium paratungstate from the warn-out tungsten oxide are like bellows:
1. Save a lot of extra caustic soda, sodium carbonate and hydrochloric acid, thus reduce the cost;
2. Simplify the process to shorten the production cycle;
3. Strong acid and alkali do not used in the reaction process; therefore, the environmental costs have been reduced;
4. Save energy and pollutants discharging has been reduced.
APT Supplier: Chinatungsten Online ammonium-paratungstate.com | Tel.: 86 592 5129696; Fax: 86 592 5129797;Email:sales@chinatungsten.com |
Tungsten News&Tungsten Prices, 3G Version: http://3g.chinatungsten.com | Molybdenum News & Molybdenum Price: http://news.molybdenum.com.cn |