Tungsten Copper Power Injection Molding — Key Technologies(2/2)
- Details
- Category: Tungsten Information
- Published on Thursday, 03 March 2016 17:24
Water atomization can refine the powder, has higher efficiency, be suitable for mass production, which can be widely used in many fields. However, a powder of irregular shape and size, so that it is easy to form an oxide film on the powder surface, thus affecting the performance of the MIM parts; the powder by aerosol method is spherical, the degree of oxidation of the surface of the powder compared to the formation of low-water atomizing method, but also a lower collection efficiency; From the point of view of the characteristics of the powder, the powder purity carbonyl prepared higher, fine-grained, but the process method subject to certain constraints, and now has only used in pure nickel and pure iron.
2. Adhesive: Except sintering process, the adhesive involved in all steps, and any injection molding process defect can not be obtained from the process to remedy or eliminate, so it played a key role in the tungsten-copper powder injection molding. Overall, the main function of the binder is to increase liquidity and to maintain the shape of the powder product, a powder can be well filled with a complicated shape under the effect of the injection pressure of the cavity. From the base of the sub-species, the adhesive can be divided into oil-based, polymer-based, paraffin-based, thermosetting adhesive gel adhesive, etc. PIM ideal binder should have a viscosity and moderate fluctuations, has a certain rigidity and strength, small weight After cooling, the metal powder has good adhesion and capillary force, the contact angle is small, high chemical stability, non-toxic safety, low thermal expansion coefficient, can be used repeatedly, and so on.
3. Degreasing and sintering process: Degreasing process is in fact warming or incubation stage of gradual removal of the adhesive, so the selection of the binder also determines the process for degreasing. The degreasing time should be shortened as far as possible and ensure that the chemical composites of blank within the permitted range. Degreasing methods can be broadly divided into hot degreasing and solvent degreasing, degreasing hot atmosphere can be divided into hot fat, vacuum thermal degreasing, degreasing and oxidation siphon degreasing, solvent degreasing can be divided into the condensed vapor degreasing and supercritical degreasing. The last process is sintering, which rely on heat treatment and promotes the grains flow and improve the bonding strength of the product sintering temperature, atmosphere, heating and cooling speed and other parameters have a certain influence on the accuracy and performance of the final product.
Tungsten Copper Supplier: Chinatungsten Online tungsten-copper.com | Tel.: 86 592 5129696; Fax: 86 592 5129797;Email:sales@chinatungsten.com |
Tungsten News & Prices, 3G Version: http://3g.chinatungsten.com | Molybdenum News & Molybdenum Price: http://news.molybdenum.com.cn |
Tungsten Copper Power Injection Molding — Key Technologies(1/2)
- Details
- Category: Tungsten Information
- Published on Thursday, 03 March 2016 17:23
Tungsten copper powder injection molding (PIM) is based on conventional powder metallurgy (PM) and combines with plastic molding process to develop a new near net shape molding process. Its appearance makes the conventional metal powder molding process limits on the shape of the product has been a breakthrough, applicable to the preparation of relatively complex geometry, uniform organizational structure, small size, high-performance parts. MIM has many advantages, such as one-step forming, with little or without subsequent processing, minimal dimensional tolerances, high consistency of the batch, injecting material can be used repeatedly, high material utilization, lower cost of production, products surface finish without subsequent processing conditions can still be achieved Ra3.2, nearly fully dense, uniform micro-structure, high flexibility and so on.
Theoretically, injection molding of tungsten copper is used in a proportion of polymer (binder) and tungsten and copper powders under certain conditions, to form a uniform blend having good flowability, molded parts after formation of the desired complex shape by injection then give a final product degreasing, sintering process, and which contains the molding powder, selection and control parameters of the binder are sintered tungsten affect copper powder injection molding process key technologies.
1. Injection Molding Powder: Due to MIM process usually used for preparing parts with small size and complex shape or structure, it has higher requirements compared with conventional powder metallurgy, the finer granularity of powder, which is also the major factor to block it out in developing. Currently the metal powder injection molding process for the production includes water atomization method, aerosol method and carbonyl.
Tungsten Copper Supplier: Chinatungsten Online tungsten-copper.com | Tel.: 86 592 5129696; Fax: 86 592 5129797;Email:sales@chinatungsten.com |
Tungsten News & Prices, 3G Version: http://3g.chinatungsten.com | Molybdenum News & Molybdenum Price: http://news.molybdenum.com.cn |
Tungsten Trioxide Degradating Sewage
- Details
- Category: Tungsten Information
- Published on Thursday, 03 March 2016 17:12
Methylene blue is phenothiazine salt, and it is unstable positive charge. It can be dissolved in water or ethanol, insolubling in ether. Methylene blue is more stable in the air; the solution is alkaline and toxic. Methylene blue is widely used in terms of chemical indicators, dyes, coloring agents and biological drugs. It can be used in the manufacture of ink and color lakes and organisms, bacteria and other aspects of the organization of chromatin. It is used to treat methaemoglobinaemia because of the reduction of methylene blue and its injection. Nitrobenzene is also used for rescue, nitrite and cyanide poisoning. Because of its role of disinfection, methylene blue can be treated with its cystitis and urethritis. In addition, methylene blue will be discharged into the body 30 minutes (injection) several hours (oral) within the urine, which resulting in urine temporarily blue, and it is also used for determination of renal function. In the breeding of ornamental fish, the methylene blue solution is 0.1-0.2ppm that can be used as a disinfection treatment of white spot disease or other diseases.
Tungsten trioxide is a semiconductor photocatalyst that can be used to degrade contaminants in water. In the reaction of photocatalytic treatment of methylene blue with tungsten trioxide, the optimum processing conditions for the tungsten trioxide are dosage 50mg, reaction time 40min, H2O2 dosage 4mL. We can determine the degradation reaction in different tungsten trioxide photocatalytic reaction system in the series by a kinetic study. The use of tungsten trioxide photocatalytic degradation of contaminants in water is one of the more popular research topics; the photocatalyst can generate holes and have a strong oxidizing power of hydroxyl radicals in the reaction, which helps it to get so much attention.
Tungsten Oxide Supplier: Chinatungsten Online www.tungsten-oxide.com | Tel.: 86 592 5129696; Fax: 86 592 5129797;Email:sales@chinatungsten.com |
Tungsten News & Prices, 3G Version: http://3g.chinatungsten.com | Molybdenum News & Molybdenum Price: http://news.molybdenum.com.cn |
Tungsten Trioxide Reverting Ultrafine Tungsten Powder
- Details
- Category: Tungsten Information
- Published on Thursday, 03 March 2016 08:42
The reduction method of tungsten trioxide (WO3) is also known as tungsten trioxide carbonization, the method can be used to restore high-quality ultrafine tungsten powder, the process is needed by the mixer, pellet mill dryer and two rotary kiln components.
Firstly, we take the tungsten trioxide (mass fraction, 84%) and carbon black powder (mass fraction, 16%) to mix the grains in order to have a diameter of 3mm ball, and then to have two successive reduction in a rotary kiln. Continuously during the reaction through a series of intermediate products:
WO3 → WO2.9 → WO2.72 → WO2.0 → W → W2C → WC.
Heating WO3 in the first furnace at 1247 ℃ in N2, the heating reaction products are WO2.72, mixture of WO2 and W, and the ultra-fine grain nucleation occurs in the intermediate product of the transformation. The process WO2.72 and WO2 are due to a sharp contraction in the volume of fine grain, and the transition time of WO2.72 transferring to WO2, which has a significant increase in density. Two compounds promote grain growth WO2 (OH) is not formed in the case of materials containing carbon black. Fine WO2 particles do not thicken into ultrafine grain. Secondly, putting kiln at 1500 ℃ in the rotary, and hydrogen atmosphere ultrafine W are directly restored. Finally, we usually add a small amount of grain growth inhibitor to prevent the ultra-fine carbide grain growth.
Experiments show that in the direct reduction process, original tungsten trioxide and carbon black play an important role in the performance characteristics of tungsten reduction. the size of carbon is reduced in the order of C → B → A. When the original tungsten trioxide particle size is 2.60 micron to 1.80 micron, the tungsten grain size reduction is hardly affected by the particle size of carbon black, in this case of the tungsten powder particle size are reduced about 0.50 microns. When using a particle size of 1.00 micron, tungsten trioxide fine particles and carbon are reduced, the reduction of tungsten particle size is 0.36 micrometers, this depends on the original particle size reduction of tungsten trioxide, and the size and reduction of tungsten powder are prepared by WC- CO alloy.
Tungsten Oxide Supplier: Chinatungsten Online www.tungsten-oxide.com | Tel.: 86 592 5129696; Fax: 86 592 5129797;Email:sales@chinatungsten.com |
Tungsten News & Prices, 3G Version: http://3g.chinatungsten.com | Molybdenum News & Molybdenum Price: http://news.molybdenum.com.cn |
Tungsten Carbide Buttons Used for DTH Drill – Failure Mode (2/2)
- Details
- Category: Tungsten Information
- Published on Wednesday, 02 March 2016 17:13
In addition, edge button lost after the failure of the original gage role DTH drill, drill itself will begin to wear occurs, which also shows the life of buttons directly affects DTH drill service life. Related researchers through a lot of experiments summarized two mechanisms carbide abrasive wear of buttons, one is tungsten carbide (WC) and cobalt (Co) subjected to a uniform wear, similar to polishing action phase, another is cobalt (Co) is first removed, and tungsten carbide (WC) particles are pulled and caused scratch; surface fatigue wear caused by tungsten carbide buttons and rock slide occurred relatively arising and produced alternating load; Adhesive wear occurs at the hardness of tungsten carbide ball and rock hardness are approximately equal state, and tungsten carbide buttons have plastic deformation and rock relative motion between the two separated and then bonded to each other, in this process carbide particles are stripped and blemishes.
2. Button Break: In the form of failure to wear mentions the concept of middle button and the edge button so that button break can be divided into the middle button break and the edge button break. Furthermore, the edge button plays a protective effect on the life of the drill DTH greatest impact. Generally, DTH drill bit end faces and buttons oblique angle of 35 °, due to the action of force is mutual, at the time of impact rock drill, eccentric impact occurs, while when the rotary drill bit cutting edge button by friction of rock, two forces together to produce the side teeth of the roots of a certain moment, the force long-term effect of such cycle prone to cracking source internal button, leading edge button fracture. However, the middle button does not produce eccentric impact, which the impact mainly caused by the friction of rock and button produced the bending tensile stress.
3. Button Drop: Button drop and smash is also occurred. The main reasons of tungsten carbide DTH drill buttons drop includes button drill bit not in the same horizontal plane at a fixed time, causing all the balls can not contact with the teeth of rock, the individual button floating ball practice involved, tensile stress wave, and the buttons has been pulled out; DTH drill cuttings by air blowing to wear during operation, resulting in part of the button exposed, thereby reducing the button bit rigid binding force; The last reason is DTH drill button arrangement when the interference does not fit properly, resulting in insufficient fastening force some button loss occurs.
Tungsten Carbide Supplier: Chinatungsten Online tungsten-carbide.com.cn | Tel.: 86 592 5129696; Fax: 86 592 5129797;Email:sales@chinatungsten.com |
Tungsten News&Tungsten Prices, 3G Version: http://3g.chinatungsten.com | Molybdenum News & Molybdenum Price: http://news.molybdenum.com.cn |
Tungsten Carbide Buttons Used for DTH Drill – Failure Mode (1/2)
- Details
- Category: Tungsten Information
- Published on Wednesday, 02 March 2016 17:11
Although tungsten carbide buttons have higher hardness and impacting resistance, it is brittle and has poor wear resistance. In the process of drilling, the high temperature of the high-speed collision with rock buttons occurrence arising will make carbide hardness decreased and crushed quartz particles made of a soft but opposed the hard phase transition occurs. Therefore, tungsten carbide buttons used for DTH drill failure will directly affect the drilling efficiency. The failure mode of tungsten carbide buttons used for DTH drill includes wear (grain wear, surface fatigue wear and adhesive wear), buttons break, buttons drop and so on. Next, we will discuss these failure modes one by one.
1. Wear: This is the commonest failure mode of tungsten carbide buttons used for DTH drill, which can be specifically divided into grain wear, surface fatigue wear and adhesive wear. Due to the conditions of DTH drill is usually strict, such as underground, down hole operation. The DTH drill buttons except impact and rotary crushing rock and rock cutting wear occurs, the air flow generated by the drill cuttings will be written to the buttons wear, especially in some high pressure DTH drill bit. DTH drill carbide buttons can be divided from the inside edge of middle and edge button, the middle button is mainly used for crushing rock, while the edge button not only involved in rock crushing, but also plays an important role is to protect the drill bit to prevent the surrounding rock drill bit itself wear. Since DTH bits during the rotary cutting rock edge against the outer edge of the button so large line speed, it will be wore earlier so that the size of the edge is larger than the middle ones, but the speed of wearing is higher than the middle.
Tungsten Carbide Supplier: Chinatungsten Online tungsten-carbide.com.cn | Tel.: 86 592 5129696; Fax: 86 592 5129797;Email:sales@chinatungsten.com |
Tungsten News&Tungsten Prices, 3G Version: http://3g.chinatungsten.com | Molybdenum News & Molybdenum Price: http://news.molybdenum.com.cn |
Single-Dimensional Network Structure Tungsten Trioxide Preparation
- Details
- Category: Tungsten Information
- Published on Wednesday, 02 March 2016 14:55
At present, people have been able to prepare different pore sizes of porous tungsten trioxide and using a variety of methods by materials that containing a large hole, mesoporous and microporous, or only two of the pore size. These materials have important applications in catalysis, selective separation and sensors; however, the porous material with a foam shape is generally more fragile and friable. Tungsten trioxide is a transition metal oxide that is widely studied because of its unique properties. In addition, the doping tungsten trioxide complex also has a catalytic effect. It means that tungsten trioxide morphology and structure of the desired application function has a direct relationship.
Steps:
Preparing dimensional network structure WO3 containing mesopores by concentrating hydrogen peroxide (H2O2), methanol, over-acid and polyvinylpyrrolidone (PVP) solution. Preparing WO3 mesh structure by using optical microscopy, scanning electron microscopy (SEM), powder X- ray diffraction (XRD), thermal gravimetric analysis (TG), high-resolution transmission electron microscope (HRTEM) and N2 adsorption isotherms (BET) technology after firing.
Conclusions:
1. Optical microscopy and SEM photograph show this shape of the foam cube mesh structure regardless of WO3, which are relatively stable calcinations that are supported by the nature of the performance.
2. Magnified SEM image shows that the wall mesh structure is assembled from nanoparticles made of WO3 after calcination.
3. XRD diffraction analysis shows that WO3 is amorphous foam before calcination, and is orthorhombic crystals after calcination. As PVP structure, it has the advantage of inducing inexpensive agents and stable solution.
Tungsten Oxide Supplier: Chinatungsten Online www.tungsten-oxide.com | Tel.: 86 592 5129696; Fax: 86 592 5129797;Email:sales@chinatungsten.com |
Tungsten News & Prices, 3G Version: http://3g.chinatungsten.com | Molybdenum News & Molybdenum Price: http://news.molybdenum.com.cn |
Tungsten Oxide Ceramic Varistor Property
- Details
- Category: Tungsten Information
- Published on Wednesday, 02 March 2016 14:40
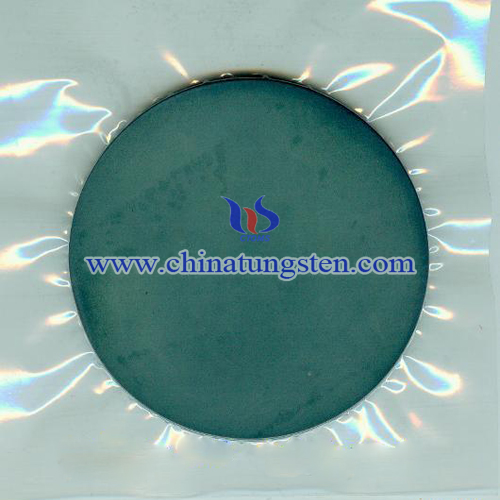
Tungsten Oxide Supplier: Chinatungsten Online www.tungsten-oxide.com | Tel.: 86 592 5129696; Fax: 86 592 5129797;Email:sales@chinatungsten.com |
Tungsten News & Prices, 3G Version: http://3g.chinatungsten.com | Molybdenum News & Molybdenum Price: http://news.molybdenum.com.cn |
Virgo Tungsten Gold-Plated Coin
- Details
- Category: Tungsten Information
- Published on Wednesday, 02 March 2016 10:54
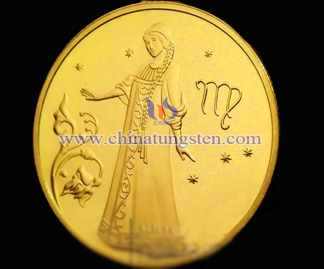
Tungsten Gold Plated Supplier: Chinatungsten Online www.tungsten-alloy.com | Tel.: 86 592 5129696; Fax: 86 592 5129797;Email:sales@chinatungsten.com |
Tungsten News & Prices, 3G Version: http://3g.chinatungsten.com | Molybdenum News & Molybdenum Price: http://news.molybdenum.com.cn |
Leo Tungsten Gold-Plated Coin
- Details
- Category: Tungsten Information
- Published on Wednesday, 02 March 2016 10:53
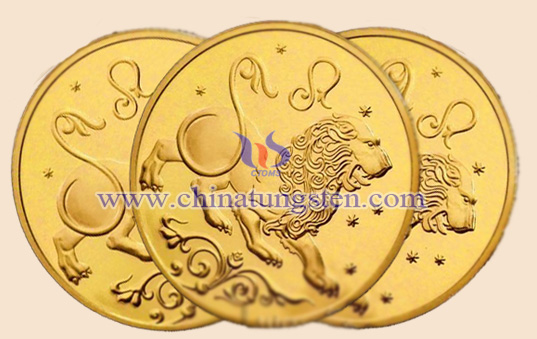
Tungsten Gold Plated Supplier: Chinatungsten Online www.tungsten-alloy.com | Tel.: 86 592 5129696; Fax: 86 592 5129797;Email:sales@chinatungsten.com |
Tungsten News & Prices, 3G Version: http://3g.chinatungsten.com | Molybdenum News & Molybdenum Price: http://news.molybdenum.com.cn |