Tungsten Gold-Plated Coin For Party
- Details
- Category: Tungsten Information
- Published on Wednesday, 24 February 2016 13:40
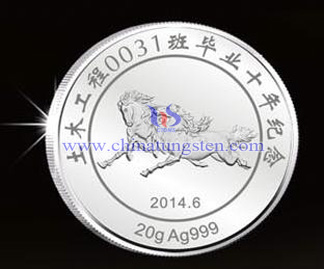
Tungsten Gold Plated Supplier: Chinatungsten Online www.tungsten-alloy.com | Tel.: 86 592 5129696; Fax: 86 592 5129797;Email:sales@chinatungsten.com |
Tungsten News & Prices, 3G Version: http://3g.chinatungsten.com | Molybdenum News & Molybdenum Price: http://news.molybdenum.com.cn |
Tungsten Carbide Ball High Precision Grinding Methods (2/2)
- Details
- Category: Tungsten Information
- Published on Tuesday, 23 February 2016 16:50
In this mechanism, except that the corner of the grinding disc groove diameter, V-channel angle and other geometrical parameters, but also with three abrasive disk rotational speed related. Through three platen speed adjustments can change (within the range of values of -90 ° -90 °) the angle of rotation. In addition, ball blank can be done changing the relative orientation of the spin axis of the grinding motion, its grinding trajectory line is he central axis of the shaft space sphere curve. In this way it is possible to cover the entire surface of the ball blank uniformly conducive to ball billet surface to obtain a uniform and efficient grinding. However, while this method in experiments to ensure good processing accuracy and processing efficiency, but in the actual production practice of commissioning and maintenance there are some difficulties to promote the production and use.
The double rotation grinding by the relevant domestic researchers first proposed, which is based on self-active control angle grinding, under the premise of maintaining the corner from the active control function, the upper lapping plate in the process of fixing the circumferential direction, and applied to ball billet certain elastic load, such that the larger ball blank allowance subject to greater loads, which also meet the size of the ball milled selective conditions. In addition, it uses two separate grinding trays rotating components, simplifying the mechanical structure also reduces the difficulty of assembling and processing (grinding process, the grinding tray during the grinding process does not need to rotate, so that the lower plate coaxial low requirements). But this process also has some problems, due to cobalt tungsten carbide ball in the grinding process prone to greater inertia, which will grind the whole trajectory and process have a certain impact, and high hardness of tungsten carbide cobalt will be on the ball trench uneven wear such precision can not be guaranteed.
Eccentric V-slot grinding, its axis of abrasive tray rotation and V-slot has a certain offset distance, which makes the ball billet revolution center and the center of rotation of the tray is not in the same straight line, and the contact point on the ball billet grinding tray along the upper abrasive tray radial direction. Compared with conventional V-slot grinding, it can achieve better spherical deviation. Chinese scholars also puts forward the optimization program, even if the eccentric disk and V-groove grinding discs rotate simultaneously, by adjusting the rotational speed of the upper and lower grinding disc, grinding track is sufficiently divergent, thus weakening offset the adverse effects of polishing uniformity.
Tungsten Carbide Supplier: Chinatungsten Online tungsten-carbide.com.cn | Tel.: 86 592 5129696; Fax: 86 592 5129797;Email:sales@chinatungsten.com |
Tungsten News&Tungsten Prices, 3G Version: http://3g.chinatungsten.com | Molybdenum News & Molybdenum Price: http://news.molybdenum.com.cn |
Tungsten Carbide Ball High Precision Grinding Methods (1/2)
- Details
- Category: Tungsten Information
- Published on Tuesday, 23 February 2016 16:49
Due to it has high hardness, high density and high strength, tungsten carbide ball plays an significant role in some oilfield or offshore drilling, which takes place of steel ball and ceramic ball gradually. The conventional grinding process itself due to mechanical constraints as well as some human factors can not exclude the influence can not be guaranteed tungsten carbide blank ball consistency and performance stability. Therefore, many related researchers has studied on tungsten carbide ball high precision grinding methods, which mainly includes eccentric V-slot grinding, angle of rotation controlling and double rotation grinding.
Firstly, since grinding angle active control is an idea of some of the relevant scholars from abroad first proposed, which is also known as three sets of coaxial grinding method. It is based on conventional V-slot grinding method, V-slot portion of the lower plate has been separated, so that the entire body is composed of three independently rotatable grinding disc composition, and then to adjust the ball from the corner of the blank by controlling the speed change three of grinding tray, the schematic given as follow:
Tungsten Carbide Supplier: Chinatungsten Online tungsten-carbide.com.cn | Tel.: 86 592 5129696; Fax: 86 592 5129797;Email:sales@chinatungsten.com |
Tungsten News&Tungsten Prices, 3G Version: http://3g.chinatungsten.com | Molybdenum News & Molybdenum Price: http://news.molybdenum.com.cn |
Exploring Tungsten Trioxide Crystal Structure
- Details
- Category: Tungsten Information
- Published on Tuesday, 23 February 2016 16:29
The crystal structure means the crystal of microstructure; it actually refers to the crystal particles (atoms, ions or molecules) arranged in specific circumstances. Solid substances existing in nature can be divided into two categories crystalline and amorphous, solid metals and alloys are large crystals. The most essential difference between the crystalline and the amorphous crystal is composed of atoms, ions, molecules and other particles are regularly arranged (long program), and not a crystal in addition to these particles with its closest outer. Metals and alloys are in a crystalline state to use in most cases. The crystal structure is one of the basic factors that determine the physical, chemical and mechanical properties of solid metal.
In order to explore the crystal structure of tungsten trioxide, we strictly follow the stoichiometric ratio of crystal structure to test the crystal structure of the tungsten trioxide whether meets distorted perovskite structure. It shows that A cation vacancy occurs; and the central atom of oxygen octahedron located in the octahedron.
In addition, we find that all the tungsten trioxide single crystal phase can be seen as octahedral structure, but at a certain structure twisted structure occurred. Since tungsten trioxide varying degrees of oxygen deficiency, and it becomes more complex, so the chemical formula of the tungsten trioxide WO3-X generally written as the type. With the increase in the number of oxygen vacancies, which are distributed in the crystals of WO3-X has become the order to form so-called trimming surface. When X <0.02, these shear surfaces are randomly distributed; when X≥0.02, the shear surface is arranged parallel to each other showing the trend, the degree of ordering trimming surface is also increasing with the increasing degree of reduction of arrangement. These compounds have different crystal structures and vacancies, and the tungsten trioxide has a variety of properties that are not the same.
Tungsten Oxide Supplier: Chinatungsten Online www.tungsten-oxide.com | Tel.: 86 592 5129696; Fax: 86 592 5129797;Email:sales@chinatungsten.com |
Tungsten News & Prices, 3G Version: http://3g.chinatungsten.com | Molybdenum News & Molybdenum Price: http://news.molybdenum.com.cn |
Inquiring Tungsten Trioxide Infrared Reflection Property
- Details
- Category: Tungsten Information
- Published on Tuesday, 23 February 2016 16:20
we use sputtering target of high purity metal tungsten (99.9%), diameter of 100mm, the choice of ITO glass substrate and the monocrystalline silicon wafer as the distance, the target and the substrate is 60mm, AR sputtering gas and O2, the background vacuum is -3000Pa, by a sputtering process parameters (pressure, composition, power, substrate temperature and time) corresponding to a reasonable choice of depositing an amorphous structure and polycrystalline tungsten trioxide thin film. Scattering spectroscopy means analyzing the composition and structure of the deposited thin films, infrared reflective properties of the thin film is measured by a spectrophotometer.
We prepare good cycle stability of polycrystalline tungsten trioxide thin film by using DC reactive sputtering process. It shows that with the co-injection of lithium ions and electrons, polycrystalline thin films of W6+is gradually reduced to W5+, infrared reflectance tests show that electrons become free carriers after electron injection film, such that shows the thin film have some infrared reflectance modulation performance.
We can obtain from the diagram, the deposition thin film shows only diffraction peaks without heating the substrate, the overall performance of the thin film substrate amorphous silicon are single crystal structure; when the substrate temperature reaches 350 ℃, the thin film shows a certain tendency to crystallize. Diffraction peaks of silicon substrate are still evident, the tungsten trioxide thin film can be considered as the alignment deposited under this condition grows extremely obvious, and the structure is not complete.
Tungsten Oxide Supplier: Chinatungsten Online www.tungsten-oxide.com | Tel.: 86 592 5129696; Fax: 86 592 5129797;Email:sales@chinatungsten.com |
Tungsten News & Prices, 3G Version: http://3g.chinatungsten.com | Molybdenum News & Molybdenum Price: http://news.molybdenum.com.cn |
Ammonium Paratungstate to Prepare Waste Gas Purification Catalyst of Porous
- Details
- Category: Tungsten Information
- Published on Tuesday, 23 February 2016 16:18
In traditional denitration of combustion flue gas, ammonia (NH3) is used as reducing agent to decomposition NOx into N and water vapor (H2O). Denitration catalysts are widely applied in the denitrification reaction, to improve the reaction rate and efficiency at the same time. In the past, in order to improve the decomposition rate of NOx, improving the ratio of NH3/NOx is a common method. However, the unreacted ammonia will be mixed into the waste and directly discharged into the atmosphere when excessive increasing the molar ratio of NH3/NOx, thus resulting in secondary pollution.
Waste gas purification catalyst is prepared by using special coating material, and precious metals as activity components, which is widely used for waste gas purification and deodorization treatment in chemical, pharmaceutical and so on, and especially in denitrification. In this paper, we will provide a method for preparing waste gas purification catalyst, which the specific steps are as follows:
1. Add ammonia into amount of metatitanic acid, and slurry is generated after full reaction;
2. Add ammonium paratungstate into the slurry that prepared in step 1;
3. Milling the mixture obtained in step 2;
4. Drying and calcining o obtain the catalyst;
5. Adjust the pore volume to 0.25~0.40g/cc; milling the catalyst powder, forming additives (if necessary) and water in the mixer; molding, drying and calcining for preparing the waste gas purification catalyst of porous we needed.
APT Supplier: Chinatungsten Online ammonium-paratungstate.com | Tel.: 86 592 5129696; Fax: 86 592 5129797;Email:sales@chinatungsten.com |
Tungsten News&Tungsten Prices, 3G Version: http://3g.chinatungsten.com | Molybdenum News & Molybdenum Price: http://news.molybdenum.com.cn |
Prepare High-Surface Area Composite Materials--WC-C
- Details
- Category: Tungsten Information
- Published on Tuesday, 23 February 2016 16:16
The catalyst, being a necessity of improve the efficiency in chemical, energy industry, and the surface area is one of the main factors to determine the catalyst’s property, that means improving the surface area will directly affect the production efficiency. Tungsten carbide (WC) as a new type of catalyst, the performance improvements are hampered due to the lower-surface area. Therefore, how to improve the catalytic activity has become one of the main challenges in preparing WC catalyst. There is an invention which provides a method to generate high dispersion and surface area of WC-C composite material, and the production can be used in the catalysis fields of chemical and electronic. Specific steps are shown as bellows:
1. Use ammonium paratungstate (APT) as precursor, add active metal powder in the mass ratio that APT: metal is 1:0.1~1 into the quartz boat under the protection of nitrogen, then moved in the tube furnace;
2. Inlet carbonization gas –CO to carry out carbonization at the mode of temperature programmed, and the heating rate is 4~15℃/min;
3. Cooling to room temperature under the protection of nitrogen;
4. Remove metal in the acid solution, and then filtering, drying to get black powder that is WC-C composite materials.
Remarks:
1) Ammonium paratungstate can also be replaced by ammonium metatungstate, sodium tungstate or tungstate;
2) Active metal powder can be Mg, Na or Al;
3) The flow rate of carbonization gas-CO through the tube furnace supposed to be 100~200ml/min;
4) Acid solution which is used to remove metal can be hydrochloric, sulfuric acid and other common acid.
APT Supplier: Chinatungsten Online ammonium-paratungstate.com | Tel.: 86 592 5129696; Fax: 86 592 5129797;Email:sales@chinatungsten.com |
Tungsten News&Tungsten Prices, 3G Version: http://3g.chinatungsten.com | Molybdenum News & Molybdenum Price: http://news.molybdenum.com.cn |
Zumwalt-Class Destroyer Tungsten Alloy Counterweights(2/2)
- Details
- Category: Tungsten Information
- Published on Tuesday, 23 February 2016 14:50
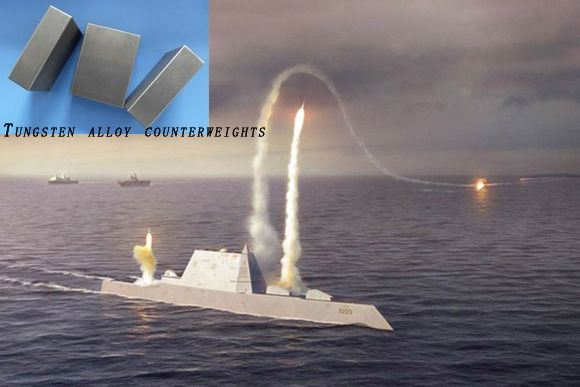
Tungsten Alloy Supplier: Chinatungsten Online www.tungsten-alloy.com | Tel.: 86 592 5129696; Fax: 86 592 5129797;Email:sales@chinatungsten.com |
Tungsten News & Prices, 3G Version: http://3g.chinatungsten.com | Molybdenum News & Molybdenum Price: http://news.molybdenum.com.cn |
Recover Tungsten, Vanadium, Titanium from Waste SCR Catalyst 2/2
- Details
- Category: Tungsten Information
- Published on Monday, 22 February 2016 18:39
3. Add hydrochloric acid into leaching slag
Wash the precipitation obtained in step 2 and adjust pH by adding hydrochloric acid, separated to get s HVO3 filtrate and residue containing H2WO4;
4. Preparation of ammonium Paratungstate
The residue containing H2WO4 that obtained in step 3 is joined ammonia with concentrate of 25~30% at 70~80℃ for dissolving, filtering and evaporating to generate ammonium paratungstate crystal;
5. Preparation of ammonium metavanadate
Add ammonia into the filtrate containing HVO3 which is obtained in step 3, stripping; the stripping liquor goes through filtration, crystallization to obtain ammonium metavanadate, and the raffinate is flowing into reuse process of wastewater.
6. Reuse process of wastewater
The advantages analyzed as follows:
1. The purity and rate of recovery are very high. Ammonium paratungstate and ammonium metavanadate that recycled can be directly used in the production process of SCR catalyst, and the Rutile Titanium Dioxide is high quality raw materials for high-grade ceramic pigment;
2. Zero discharge of industrial waste water;
3. The by-products can be directly soled as product sales to the users downstream;
4. Valuable metals achieve the goal of regeneration and separation and realize harmless clean production;
5. The tall gas generated in the calcination process doesn’t exist by Spray absorption;
6. Use high-pressure water for washing in the pretreatment and the filter reused, which avoid poisonous compounds such as mercury, arsenic, phosphorus and so on in waste SCR catalyst not to be loss with the ash.
APT Supplier: Chinatungsten Online ammonium-paratungstate.com | Tel.: 86 592 5129696; Fax: 86 592 5129797;Email:sales@chinatungsten.com |
Tungsten News&Tungsten Prices, 3G Version: http://3g.chinatungsten.com | Molybdenum News & Molybdenum Price: http://news.molybdenum.com.cn |
Recover Tungsten, Vanadium, Titanium from Waste SCR Catalyst 1/2
- Details
- Category: Tungsten Information
- Published on Monday, 22 February 2016 18:36
Due to denitration agents take 30%~50% the whole investment of denitration equipment in the system, besides the main component V2O5 is of highly toxic which will cause environmental pollution and poison to human body. So, it will create great economic and environmental benefits by comprehensive recycling waste catalyst. A method for recycling tungsten, vanadium and titanium from waste SCR catalyst is put forward in this paper, steps are as follows:
1. SCR waste catalyst pretreatment, high temperature and pressure leaching out
1) Crushing and grinding the waste catalysts, then send them to NaOH solution which the concentration is 200~700g/L, and then leaching out at high temperature (130~220℃), high pressure (0.3~ I.2MPa) for I~6 hours, get filtrate and residue;
Remarks: residue can be used as the material of Rutile Titanium Dioxide;
2) Add hydrochloric acid to adjust the pH value to 0.5~I.5, and heated to 90~100℃ to make Na4TiO4 reacted to H4TiO4, then filter for getting filtrate and residue;
Remarks: ①. Filtrate and washed wastewater are joined into reuse process of wastewater;
②. The residue after washing is calcined at the temperature of 800~900℃ for 2-4 hours to get Rutile Titanium Dioxide.
2. Adjust pH by adding hydrochloric acid to remove impurities
Add hydrochloric acid into leaching solution which is got from step 1 to adjust pH value to 10~11, then add MgCl2 for removing impurity; concentrate and again add hydrochloric acid to adjust pH value to 9~10, and then precipitate WO42- and VO3- ions, separate to obtain filtrate and filter residue, the filter join into reuse process of wastewater.
APT Supplier: Chinatungsten Online ammonium-paratungstate.com | Tel.: 86 592 5129696; Fax: 86 592 5129797;Email:sales@chinatungsten.com |
Tungsten News&Tungsten Prices, 3G Version: http://3g.chinatungsten.com | Molybdenum News & Molybdenum Price: http://news.molybdenum.com.cn |