Tungsten Copper Composite Power Injection Molding (2/2)
- Details
- Category: Tungsten Information
- Published on Thursday, 18 February 2016 17:39
The main function of packaging materials includes mechanical support, signal transduction, heat radiating, sealing and protecting products, so they requested that the material has a certain mechanical strength, good electrical and thermal capacity, chemical stability, and product line expansion coefficient matched material, easily for producing Conventional substrates has been difficult to meet the rising temperature of the circuit and to ensure steady long run, this will affect the reliability of electronic components to some certain extent. Therefore, tungsten copper material becomes more and more significant in microelectronics packaging. Electronic components and packaging material due to small size, complex structure and other reasons, it is difficult for mass production by conventional pressing sintering process method, which makes tungsten copper powder injection molding technology has been further developed.
Related researchers uses 10%, 15%, 20% content of copper for powder injection molding, which after infiltration obtained, fine-grained tungsten-copper composite materials, have reached a density more than 99%, transverse rupture strength reaches 1500MPa. Some scholars have also done the injection molding parameters tungsten copper W-30Cu nano-composites T-die, and after forming the binder removal process to obtain a good surface quality, regular shape of the compact, the adhesive extrusion rate reached more than 99%, can be obtained through direct sintering manner relative density higher than 96% of tungsten-copper composite parts. However, the process will caused by tungsten (W) powder loading of different or the intake air in the mixing process and lead to material gathered in the stress state, a certain amount of defects such as large irregularly shaped cracks or holes generated in the process of degreasing, it is easy leading to infiltration of copper pool and closed pores formed.
Tungsten Copper Supplier: Chinatungsten Online tungsten-copper.com | Tel.: 86 592 5129696; Fax: 86 592 5129797;Email:sales@chinatungsten.com |
Tungsten News & Prices, 3G Version: http://3g.chinatungsten.com | Molybdenum News & Molybdenum Price: http://news.molybdenum.com.cn |
Tungsten Copper Composite Power Injection Molding (1/2)
- Details
- Category: Tungsten Information
- Published on Thursday, 18 February 2016 17:37
Inspired from powder injection molding of conventional powder metallurgy (PM), tungsten-copper composite powder injection molding technology is based on the injection of tungsten skeleton is formed, and it breaks the limitations of conventional Infiltration produced tungsten-copper composite. Metal injection molding (MIM) is a kind of process that suitable for fabricating the products with complex or irregular shape, and it was first extended by the plastic injection molding industry. In recent years, a substantial increase in the content of the solid particles and the binder is completely removed during sintering densification of the compact, resulting in metal products with high strength, excellent wear and corrosion resistance.
Its basic steps is that choose the metal powder meet the requirements of MIM (includes shape of powder, the granularity, the content, specific surface and so on) and corresponding binder (MIM is the core technology, with enhanced liquidity and maintain compact shape function), At a certain temperature using appropriate methods uniformly mixing the powder with a binder feed, injection molding after granulating, injection molding and degreasing obtained the products. Tungsten-copper composite material due to its high strength, high density, high melting point, good chemical stability, and is a good electrical and thermal conductivity of the heat sink material, not only from the field of military aviation in a number of electrical contacts and electrodes have a wide range the use of some of the tightness in demanding electronic packaging materials is also a good choice.
Tungsten Copper Supplier: Chinatungsten Online tungsten-copper.com | Tel.: 86 592 5129696; Fax: 86 592 5129797;Email:sales@chinatungsten.com |
Tungsten News & Prices, 3G Version: http://3g.chinatungsten.com | Molybdenum News & Molybdenum Price: http://news.molybdenum.com.cn |
Ammonium Paratungstate Used for Preparing Tungsten Trioxide Nano Film 2/2
- Details
- Category: Tungsten Information
- Published on Thursday, 18 February 2016 16:51
Specific steps are as follows:
1. Preparing precursor solution
Dissolve APT in deionized water, then add a certain amount of dispersing agent and modifier, continually stir in the magnetic stirrer for 3-5 hours, and then stand constantly in the water bath environment at 70-90℃ to generate precursor solution;
2. Coating
Coat at substrate by dip-coating or spin-coating method, and dry under a suitable temperature condition. The substrate should be washed and other pre-dealing;
3. Roasting
Roasting the substrate at high-temperature (350-600) in a temperature controllable procedures muffle furnace for 2-5 hours after it is dried, and finally gets the nano tungsten trioxide film.
Its obvious advantages lay in:
1. Take APT as precursor, by adding dispersant and a modifier, final get nano tungsten trioxide film firmly adhesion to substrate;
2. The precursor solution can be stored for more than 3 months with a stable state and no precipitation phenomenon produced, it also can be reused, easy to operate, greatly reduced the production cost;
3. The dispersant and modifier added into precursor solution are entirely organic matter which can easily be oxidation and removed at high temperature, without introducing metal elements except W, especially metallic element of the alkali metal (Na+, K+), also it does not affect the performance of the photocatalytic activity of W03 and photoelectric conversion;
4. Nano tungsten trioxide film prepared is of excellent photoelectric properties.
APT Supplier: Chinatungsten Online ammonium-paratungstate.com | Tel.: 86 592 5129696; Fax: 86 592 5129797;Email:sales@chinatungsten.com |
Tungsten News&Tungsten Prices, 3G Version: http://3g.chinatungsten.com | Molybdenum News & Molybdenum Price: http://news.molybdenum.com.cn |
Ammonium Paratungstate Used for Preparing Tungsten Trioxide Nano Film 1/2
- Details
- Category: Tungsten Information
- Published on Thursday, 18 February 2016 16:48
Photoelectrochemical Cells Hydrogen Production (PEC) technology is based on solar energy and water, and the two substances are renewable with no byproduct, not pollution to the environment, and also can be applied to small as well as large scale development. Therefore, the technology is the most attractive way to produce hydrogen by solar energy. The property of photoelectric which is consisted of semiconducting materials determines the efficiency of PEC. Compared with the traditional semiconductor materials such as titanium dioxide and zinc oxide, W03 can be well applied with the advantages that narrow band gap (2.5ev), absorbing solar spectrum in a wavelength greater than 500nm in visible light, and low price, good chemical stability, non-toxic, no corrosion.
The method for preparing nano tungsten trioxide film using ammonium paratungstate (APT) as raw material we describes in this paper, has advantages that stable precursor solution, reuseable, production process simplified, cost reduced, high purity of the obtained product and so on.
The reagent used: apt, modifier (can be one of citric acid, polyethylene glycol octyl phenyl ether, oleic acid and acetyl acetone), deionized water, dispersing agent. The dispersing agent plays the role of constituting large numbers of mass weaving structures to make sure the crystals not easy broken in the dry, hot environment; and the modifier will increase stability of the precursor solution, also prevent the nano tungsten trioxide to reunion thus leading the film to peeling in the condition of high temperature.
Coating substrates: aluminum, stainless steel, glass, graphite or silicon wafers.
APT Supplier: Chinatungsten Online ammonium-paratungstate.com | Tel.: 86 592 5129696; Fax: 86 592 5129797;Email:sales@chinatungsten.com |
Tungsten News&Tungsten Prices, 3G Version: http://3g.chinatungsten.com | Molybdenum News & Molybdenum Price: http://news.molybdenum.com.cn |
Gold-Plated Tungsten Coin For Father’s Day
- Details
- Category: Tungsten Information
- Published on Thursday, 18 February 2016 15:50
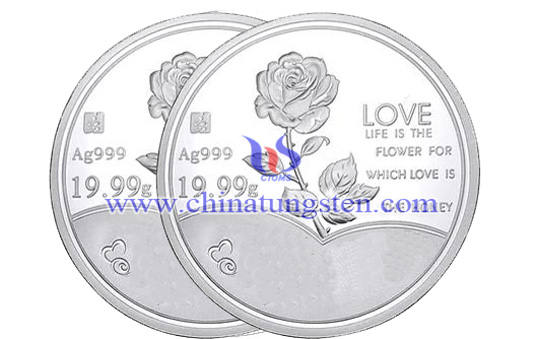
Tungsten Gold Plated Supplier: Chinatungsten Online www.tungsten-alloy.com | Tel.: 86 592 5129696; Fax: 86 592 5129797;Email:sales@chinatungsten.com |
Tungsten News & Prices, 3G Version: http://3g.chinatungsten.com | Molybdenum News & Molybdenum Price: http://news.molybdenum.com.cn |
Gold-plated Tungsten Coin For Mother’s Day
- Details
- Category: Tungsten Information
- Published on Thursday, 18 February 2016 15:45
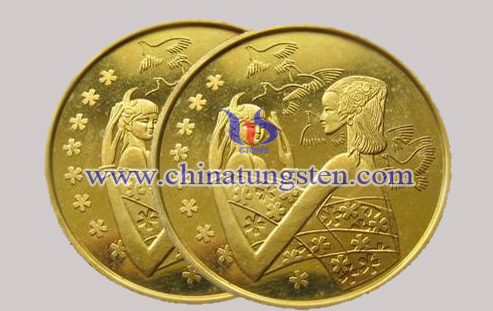
Tungsten Gold Plated Supplier: Chinatungsten Online www.tungsten-alloy.com | Tel.: 86 592 5129696; Fax: 86 592 5129797;Email:sales@chinatungsten.com |
Tungsten News & Prices, 3G Version: http://3g.chinatungsten.com | Molybdenum News & Molybdenum Price: http://news.molybdenum.com.cn |
Pyrochlore Tungsten Trioxide Sensing Application
- Details
- Category: Tungsten Information
- Published on Thursday, 18 February 2016 15:01
Currently, the prepared pyrochlore type tungsten trioxide (Pyrochlore-type H2W2O7) is A-multi-bit deletion as the layered perovskite tissue. Pyrochlore type tungsten trioxide takes tungsten WO6 distorted octahedral structural as motifs, it builds a layered structure having six-membered ring channels by the angle of the top of the tungsten trioxide rigid skeleton, and has a three-dimensional tunnel along the (111) direction. Pyrochlore tungsten trioxide is used in layered composite materials, sensing field, and be calcimined to prepared tungsten oxide.
Pyrochlore types of tungsten trioxide are pyrochlore type structure, it is also known as yellow-stone structure or pyrochlore structure. There will be more prominent pyrochlore out of tungsten trioxide used in the preparation of battery sensing field because it is hydrate, and its unique physical and chemical properties. Currently, it is widely used in the sensing field.
In the application process, we often make pyrochlore type tungsten trioxide in LiClO4 electrolyte 1mol / L as the cathode, and we make lithium foil as anode, and uniformly embedding Li in the pyrochlore tungsten trioxide. Last, we have a process by ion exchange for pyrochlore type tungsten trioxide containing sodium. After testing, the result shows that the finished product has the lowest resistivity, good durability and repeatability, which can exhibits good electrochromic properties.
Tungsten Oxide Supplier: Chinatungsten Online www.tungsten-oxide.com | Tel.: 86 592 5129696; Fax: 86 592 5129797;Email:sales@chinatungsten.com |
Tungsten News & Prices, 3G Version: http://3g.chinatungsten.com | Molybdenum News & Molybdenum Price: http://news.molybdenum.com.cn |
Oxalic Acid Preparing Pyrochlore Tungsten Trioxide
- Details
- Category: Tungsten Information
- Published on Thursday, 18 February 2016 14:51
Oxalic acid is metabolite of the organism, it is widely distributed in plants, animals and fungi in the body, and it plays different functions in different living body. Industrial oxalic acid is colorless monoclinic crystal or prism sheet or white powder; it is usually odorless oxidation oxalic acid. Its sublime is in 150 ~ 160 ℃. Oxalic acid can be used as bleaching agent, reducing agent, mordant, and it has rust function.
Oxalic acid as an additive for preparing pyrochlore type tungsten trioxide, the first steep is configuring concentration of 100g / L of sodium tungstate solution 10mL, adding an appropriate amount of oxalic acid, adjusting the pH value of the solution about 7.0, the second steep , the sodium tungstate solution is transferred to a low pressure reaction vessel, maintaining constant temperature at 140 ℃ , conditions reaction 24h, measuring the reaction rate of the solution according to the concentration of tungsten trioxide. The resulting solution is filtered and treated; water as well as the spent ion alcohol is washed 2-3 times, drying it to obtain finished pyrochlore type tungsten trioxide.
It was found that the highest rate of decomposition of oxalic acid as an additive tungstate sodium in hot water system can reach about 60%, and the reaction is faster, the decomposition rate closes to the maximum. The decomposition rate has been around 60% of small amplitude fluctuations. It exploded a short time in the entire hot water system; it is suitable for industrial production applications.
Tungsten Oxide Supplier: Chinatungsten Online www.tungsten-oxide.com | Tel.: 86 592 5129696; Fax: 86 592 5129797;Email:sales@chinatungsten.com |
Tungsten News & Prices, 3G Version: http://3g.chinatungsten.com | Molybdenum News & Molybdenum Price: http://news.molybdenum.com.cn |
Preparation of Low Cost SCR Method for Denitration Catalyst
- Details
- Category: Tungsten Information
- Published on Wednesday, 17 February 2016 18:40
A low cost method to prepare SCR denitration catalyst which can reduce the preparation and operation cost, improve the abrasion resistant property of catalyst. The weight composes are like bellows: grounded slag powder takes 52~55%, gypsum 2.7~2.9%, partial ammonium metavanadate 1.3~1.5%, ammonium paratungstate 5.5~5.7%, silica sol 2.6~2.8%, clay 1.6~1.8%, glass fiber yarn 2.5~3.0%, methyl cellulose 2.7 to 2.9%, poly ethylene oxide 1.3~1.5%, a glycol ammonium 2.7~3.0%, distilled water of 20~23%.
The preparation steps are as follows:
1. Grinding and activate the carriers
Send grounded slag powder and gypsum by weight ratio of 17.9~20.4:1 into grinding equipment, inlet the high temperature steam (100 to 120℃), grinding and activate to get the carrier;
2. Preparation of slurry
Send carriers and ammonium metavanadate, ammonium paratungstate, silica sol, clay, glass, fiber, methyl cellulose, poly ethylene Huan and ethanol ammonium into the mixer, adding distilled water while stirring, stirring more than 2 hours until the solution uniform, to generate slurry with water below 25%;
3. Molding catalyst
Form the slurry in the required prepared shape, then dry and calcine to get the products we needed. The calcine conditions are like bellows: first calcined in 250~255℃ for 45~50 hours, then 370~390℃ calcined for 23~25 hours, again calcined at 445~455℃for 11~13 hours.
APT Supplier: Chinatungsten Online ammonium-paratungstate.com | Tel.: 86 592 5129696; Fax: 86 592 5129797;Email:sales@chinatungsten.com |
Tungsten News&Tungsten Prices, 3G Version: http://3g.chinatungsten.com | Molybdenum News & Molybdenum Price: http://news.molybdenum.com.cn |
Preparation for Ammonia Selective Catalytic Reduction of Honeycomb Denitration Catalyst
- Details
- Category: Tungsten Information
- Published on Wednesday, 17 February 2016 18:38
We propose a honeycomb ammonia selective catalytic reductive SCR catalyst preparation method with simple process, high strength, and denitrification activity, continued for a long time in this paper. The catalyst uses Ti02 as carrier, V205 as active component, W03 as co-catalyst. In which Ti02 anatase is used to be the raw materials of carrier, 80% content of the catalyst weight; V205 is added in the form of ammonium metavanadate, 0.1%-5% of the catalyst weight percent content; co-catalyst as W03 added in the form of ammonium paratungstate, 1%-20% of the catalyst weight percent content.
Steps are as follows:
1. Preparation of carrier stock
Take Ti02 powder, stirring in the water bath at the temperature of 60~80℃, get support slurry;
2. Join the loaded active component and other additives
Slowly add ammonium metavanadate and ammonium paratungstate into the carrier stock during the mixing process, and then add a variety of additives;
3. Mixing in the pug mill and being stale
Transfer the slurry obtained in step 2 to vacuum refining mud machine mixing, and stale in the constant humidity, continue to kneading. Pug kneaded for half an hour each time, the stale time is 8 hours, repeated several times to generate mud practiced;
4. Molding. Shaped the mud in the honeycomb;
5. Drying and roasting the catalyst
Dry the honeycomb for 3~6 days in drying box which the humidity and drying speed is controllable; and then roasted in the furnace of 300~600℃ for 12~24 hours, then to obtain the final honeycomb catalyst.
APT Supplier: Chinatungsten Online ammonium-paratungstate.com | Tel.: 86 592 5129696; Fax: 86 592 5129797;Email:sales@chinatungsten.com |
Tungsten News&Tungsten Prices, 3G Version: http://3g.chinatungsten.com | Molybdenum News & Molybdenum Price: http://news.molybdenum.com.cn |