Preparing Composite Powder Tio2-Wo3-Sio2 Used as Catalyst Carrier
- Details
- Category: Tungsten Information
- Published on Friday, 19 February 2016 16:45
Anatase nanometer TiO2 is mainly used as activity carrier for denitration catalyst. Because of TiO2 composites with WO3 in TiO2-WO3-SiO2 powder, the structure and surface properties have been changed. Also it causes WO3 distributing more uniform, thus improve the processing performance which is advantageous to mixing, extruding, drying process, thus ensure rate of finished products. We propose a method for preparing composite powder TiO2-WO3-SiO2, and the specific steps as follows:
1. Beating and dispersing the raw material H2TiO3, and then adjust the concentration of titanium dioxide slurry;
2. Add ammonium paratungstate and white carbon black into the slurry;
3. Add ammonia to adjust pH to 5.5~8.5 for improving combination with WO3 and the calcination properties of metatitanic acid;
4. Filtrating and dehydrating the slurry to get massive cake, in which mass fraction of TiO2is controlled in 40%~55%;
5. Crushing massive cake mechanical, then drying it at 200~380℃ for 2.5 hours, and then calcined 380~680℃ for 4.5 hours;
6. Crushing to generate the required composite powder TiO2-WO3-SiO2.
The method descripts above has the following advantages:
1) Low manufacturing cost, simple process;
2) The products obtained are not only with long service life and high surface area, surface chemical activity, good processing performance, but also have the advantages of high mechanical strength and resistance to erosion.
APT Supplier: Chinatungsten Online ammonium-paratungstate.com | Tel.: 86 592 5129696; Fax: 86 592 5129797;Email:sales@chinatungsten.com |
Tungsten News&Tungsten Prices, 3G Version: http://3g.chinatungsten.com | Molybdenum News & Molybdenum Price: http://news.molybdenum.com.cn |
Cleaning SCR Denitration Catalyst on Production Process
- Details
- Category: Tungsten Information
- Published on Friday, 19 February 2016 16:41
The activity of SCR denitration catalyst in-service will decrease by being abraded from flue gas, deposited from solid material, poisoned from alkali metal. And then after 2 or 3 years the catalyst would lose activity and end its life. Cleaning the SCR denitration catalyst is becoming very necessary because it costs high, and belongs to consumables. At the same time, the waste catalyst is difficult to handle because of the toxicity which will cause secondary pollution to the environment easily. We push a method for cleaning SCR denitration catalyst on the production process, steps as following:
1. Configure the cleaning solution
Stirring with a machine to mix oxalic acid solution, dispersing agent MF, ammonium metavanadate and ammonium paratungstate for more than 10 minutes for generating cleaning solution. Among them, the mass concentration that MF is 0.1-1wt%, ammonium metavanadate is l-3wt%, and ammonium paratungstate controlled at 5-15wt%. The pH value of the oxalic acid solution supposed to be 5-7;
2. Blowing and cleaning the surface of SCR denitration catalyst by a sonic soot-blower for 15s, and then cleaning the surface and pore of catalyst for 1min in certain circumstances;
3. Washing the SCR denitration catalyst for 5mins, and collect the waste liquid at the same time;
4. Washing the SCR denitration catalyst with cleaning solution for 10-20mins, also the waste liquid should be collected;
5. Dry the catalyst through a hot air drying device for 2-4 hours, thus finish the progress of cleaning SCR denitration catalysts.
APT Supplier: Chinatungsten Online ammonium-paratungstate.com | Tel.: 86 592 5129696; Fax: 86 592 5129797;Email:sales@chinatungsten.com |
Tungsten News&Tungsten Prices, 3G Version: http://3g.chinatungsten.com | Molybdenum News & Molybdenum Price: http://news.molybdenum.com.cn |
Tungsten Carbide Ball Grinding Methods (2/2)
- Details
- Category: Tungsten Information
- Published on Friday, 19 February 2016 16:27
Tungsten carbide ball double V-slot grinding can ensure that the rotation angle of the ball will change with sphericity, but it requires that the grinding tray V-slot up and down has higher properalignment and shape error and assembly error institutions needed to be effectively controlled, otherwise the blank ball can not roll along the groove smoothly. The relevant domestic scholars have done a lot of this research and developed a conical grinding method in which the abrasive disk is tapered, which makes carbide ball blank has a large corner across from the milling process (usually up to 45 ° left and right), to obtain a full rotation, enhanced rotary slide ball blank, improving overall processing efficiency. The following is a schematic view of the three grinding work mode, you can clearly see different from the design of the grinding tray:
Besides these three kinds of conventional grinding methods, Related researchers and academics abroad in order to achieve high-speed grinding ceramic balls have also proposed a flexible and high material removal rate of magnetic fluid polishing. Its basic principle is to use magnetic fluid mixing abrasive particles as an abrasive, when the magnetic fluid is given a certain magnetic field, the magnetic fluid will produce upward thrust, by the corresponding floating disc ceramic balls implement processing load. It remarkably improve the efficiency of precision ceramic ball and its roundness error less than 0.14μm, surface roughness reaches 0.01μm, material removal rate reaches 12μm / min, which is more than 40 times that of conventional grinding method.
However, this method due to the complex structure, inconvenient operation, and the magnetic fluid itself heightening price, after the magnetic fluid and particles worn when machining, material removal will be affected to some extent, it is also the emergence of a non-magnetic fluid polishing (water and glycerol mixture) instead of magnetic fluid and resin bonded diamond grinding wheel instead of embedding the abrasive grinding tray. Although the processing efficiency and processing efficiency and non-abrasive magnetic fluid magnetic fluid grinding pretty, its precision can not be fully guaranteed, both of structure of them are relatively complex, which is not suitable for large-volume production of high-precision machining of tungsten carbide ball.
Tungsten Carbide Supplier: Chinatungsten Online tungsten-carbide.com.cn | Tel.: 86 592 5129696; Fax: 86 592 5129797;Email:sales@chinatungsten.com |
Tungsten News&Tungsten Prices, 3G Version: http://3g.chinatungsten.com | Molybdenum News & Molybdenum Price: http://news.molybdenum.com.cn |
Tungsten Carbide Ball Grinding Methods (1/2)
- Details
- Category: Tungsten Information
- Published on Friday, 19 February 2016 16:24
With the development of technology, the grinding methods of tungsten carbide ball are developing rapidly. There are conventional grinding methods (includes single V-slot, double V-slot and conical slot), fluid polishing (magnetic fluid, non-magnetic fluid) and high precision grinding (eccentric V-slot, active control of rotation), etc. Single V-slot grinding, the value of rotation angle depends on the angle and ball milled blank disc slot diameter, in a closed loop process almost from the corner does not change, and since the angle is very small, but only for a relatively compact carbide balls orientation change (i.e. ball billet rotation axis and the revolution axis angle of the same size) grinding motion.
The contact point of blank ball and polishing discs trace ball billet was formed on the surface of the center axis of the rotation axis of the ring. The defect of this method is that it can not ensure quickly billet surface grinding ball uniform, thereby reducing the efficiency and accuracy of carbide and sphericity processing. Therefore, the related researchers modified in part designed to travel around the grinding disc moving grooves, making the ball spin axis changes can be made randomly. Compared with single V-slot grinding, both of the upper and lower grinding tray of tungsten carbide ball double V-slot grinding are V-shaped, while single V-slot only the lower grinding tray is V-shaped.
Tungsten Carbide Supplier: Chinatungsten Online tungsten-carbide.com.cn | Tel.: 86 592 5129696; Fax: 86 592 5129797;Email:sales@chinatungsten.com |
Tungsten News&Tungsten Prices, 3G Version: http://3g.chinatungsten.com | Molybdenum News & Molybdenum Price: http://news.molybdenum.com.cn |
Preparing Glassy Tungsten Trioxide
- Details
- Category: Tungsten Information
- Published on Friday, 19 February 2016 15:29
You may have seen a wide variety of glass products in life, such as mobile phones glass, glass vases, glass windows, glass roofs, glass lid, glass cups, and so on. They all have one thing in common, and that is: they are transparent. But did you have seen the glassy tungsten trioxide? How it is prepared? Is it transparent?
Tungsten trioxide are yellow powder, it dissolves in water, dissolves in alkali, slightly dissolves in acid. It is mainly used to restore the production of calcined tungsten powder and tungsten carbide powder, and then for the production of carbide products, such as tool and die manufacturing. It also can be used in the manufacture of pure tungsten products, tungsten electrode; and the use of counterweight and radiation shielding material. In the shipbuilding industry, the tungsten trioxide is used as important anti-corrosion paint and coatings material. Due to extensive use of tungsten trioxide, more and more people increase research efforts on the tungsten trioxide, at present, the study shows that glassy tungsten trioxide is unique performance oxidation, it is able to meet the needs of production and processing areas.
Preparing glassy tungsten trioxide, the first steep is adding tungsten powder (diameter 1μm) 15% to hydrogen peroxide capacity of 25ml (H2O2), stirring for 3-10 minutes, and the tungsten powder is almost completely dissolved. As colorless solution, it is strongly acidic to remove small amount of undissolved impurities. The second steep is meshing Pt, Pt-plated to reduce the excess H2O2. Finally, drying solution at room environment, we can obtain paint yellow glassy tungsten trioxide.
Tungsten Oxide Supplier: Chinatungsten Online www.tungsten-oxide.com | Tel.: 86 592 5129696; Fax: 86 592 5129797;Email:sales@chinatungsten.com |
Tungsten News & Prices, 3G Version: http://3g.chinatungsten.com | Molybdenum News & Molybdenum Price: http://news.molybdenum.com.cn |
Solvent Influencing Tungsten Trioxide Preparing Cyclohexanone
- Details
- Category: Tungsten Information
- Published on Friday, 19 February 2016 15:20
Cyclohexanone is organic compound, it is carbonyl carbon atom including the six-membered ring saturated cyclic ketone; it is colorless and transparent liquid, it containing traces of phenol. Cyclohexanone impurities are yellow. Cyclohexanone has a carcinogenic effect; it is mainly used in industrial organic synthesis of raw materials and solvents. Cyclohexanone is an important chemical raw materials, it is widely used in nylon, caprolactam and adipic acid intermediate principal. It is also an important industrial solvent, such as for paints, in particular for nitrocellulose, vinyl chloride polymers and copolymers or methacrylic acid ester polymer paint.
In the process of preparation, a suitable solvent for the reaction is very important. We can see from the data in Table 1-1, the methanol is the best solvent for reaction.
1-1 Effect of different solvents on the yield of cyclohexanone
Cyclohexanone |
Free Solvents |
Ethanol |
Ethanol |
Acetone |
Yield /% |
73.5 |
88.0 |
65.2 |
61.2 |
1-2 Effect of the amount methanol on the yield cyclohexanone
The amount of Methanol /mL |
Yield % |
Reaction Time /h |
5 |
88.0 |
3 |
10 |
84.1 |
3 |
15 |
65.8 |
3 |
Table 1-1 shows that methanol is the best solvent for the reaction. As we can see from the data in Table 1-2, the yield of cyclohexanone decreases with increasing amount of methanol. Due to the increased amount of methanol, this results the concentration of reactants and the cyclohexanol conversion rate reducing.
Tungsten Oxide Supplier: Chinatungsten Online www.tungsten-oxide.com | Tel.: 86 592 5129696; Fax: 86 592 5129797;Email:sales@chinatungsten.com |
Tungsten News & Prices, 3G Version: http://3g.chinatungsten.com | Molybdenum News & Molybdenum Price: http://news.molybdenum.com.cn |
AMT/SiO2 Catalyst on Orthortho-Hydroxy Anisole Production(2/2)
- Details
- Category: Tungsten Information
- Published on Thursday, 18 February 2016 17:55
AMT Supplier: Chinatungsten Online www.ammonium-metatungstate.com | Tel.: 86 592 5129696; Fax: 86 592 5129797;Email:sales@chinatungsten.com |
Tungsten News&Tungsten Prices, 3G Version: http://3g.chinatungsten.com | Molybdenum News & Molybdenum Price: http://news.molybdenum.com.cn |
AMT/SiO2 Catalyst on Orthortho-Hydroxy Anisole Production (1/2)
- Details
- Category: Tungsten Information
- Published on Thursday, 18 February 2016 17:53
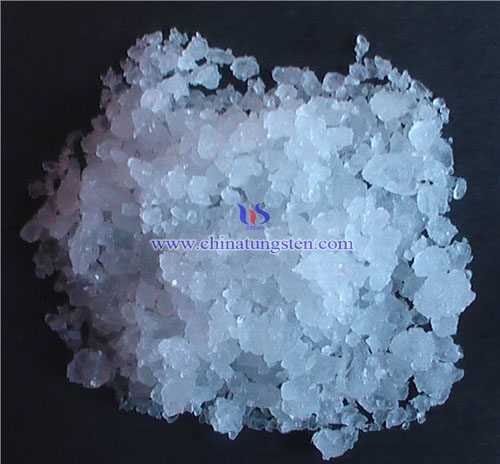
AMT Supplier: Chinatungsten Online www.ammonium-metatungstate.com | Tel.: 86 592 5129696; Fax: 86 592 5129797;Email:sales@chinatungsten.com |
Tungsten News&Tungsten Prices, 3G Version: http://3g.chinatungsten.com | Molybdenum News & Molybdenum Price: http://news.molybdenum.com.cn |
Using Impregnation Method for Barium Tungsten Electrodes Production
- Details
- Category: Tungsten Information
- Published on Thursday, 18 February 2016 17:45
Using impregnation method to produce barium tungsten electrode it has good emission properties, high current density, smooth electrode surface and long service life and other good performance. However, this method has the disadvantage of complex processes and processing difficult.
To produce barium tungsten electrode by impregnation method there are two elements, tungsten cavernous spongisum and emitting material and the production processes are as following:
1. Tungsten cavernous spongisum production:
Raw materials: tungsten powder (250 mesh / cm2): 97g, paraffin: 3g, aviation gasoline: 30~40cc, glycerol;
Production processes: Pour gasoline into paraffin to make paraffin melted, then pour them into tungsten powder (about 180 ℃) with rapid stirring, until the smell of gasoline is gone. And then compress it into blocks. The compacted tungsten powder was processed low-temperature sintering, and before sintering temperature slowly raised to 600 ℃the temperature is 100~150 ℃/ h, but at 600 ~ 1400 ℃ the temperature is 200 ℃/h (heating preservation for 1 hour). When the temperature at 1700℃ the product is molding. Finally, high temperature sintering, high temperature sintering temperature is about 2000 ℃ (about half an hour).
2. Emitting material: barking barium aluminum in oven at about 100 ℃,after grinding and compressing put it into molybdenum boat for sintered with Al2O3 doping when the sintering temperature reaches to 700 ~ 800 ℃, heating preservation for 1 hour, when the sintering temperature is 1400 ℃, heating preservation for 2 hours, after sintering pulverized it into pieces to get finished.
3. Barium tungsten electrode: putting barium aluminum into nitrocellulose stir into a paste, applied to the surface of the tungsten cavernous. And then burn to 1750 ℃, until the product surface shows light green color. Then the sintered electrode in pumping quartz vessel prepared products roast vacuum high frequency. Finally, the electrodes are placed dried in a vacuum environment for storage.
Barium tungsten electrode Use Notes:
1. Can not make it wet or long-term exposure to the atmosphere, deposited in a vacuum state for the best;
2. Can not direct contact with the to prevents sweat marks shows on the surface of the electrode;
3. Electrode texture is light and crispy, using gently;
4. Improper storage electrode surface will oxidation, you can process burn hydrogen treatment to remove surface dark spots, and then continue to use;
5. The transmission side of electrode has cracks or broken, to stop using it.
Tungsten Supplier: Chinatungsten Online www.chinatungsten.com | Tel.: 86 592 5129696; Fax: 86 592 5129797;Email:sales@chinatungsten.com |
Tungsten News & Prices, 3G Version: http://3g.chinatungsten.com | Molybdenum News & Molybdenum Price: http://news.molybdenum.com.cn |
Barium Tungsten Electrode
- Details
- Category: Tungsten Information
- Published on Thursday, 18 February 2016 17:39
Barium tungsten electrode is a high intensity discharge lamp electrode material. It is produced for improve the properties of tungsten electrode which is changing the low electrons emission ability of pure tungsten electrodes, increasing electrons and electron current density, improving gas discharge lamp ignition speed, reducing electrode working temperature so it can apply in different fields. Barium tungsten electrode has high electron emission capability, low work function, high electron emission electron current density, good gas discharge lamp ignition speed, low working temperature and other good performances. In addition, the barium tungsten electrode is a non-radioactive poison electrode and has anti-poisoning ability.
Because barium tungsten electrode having the above excellent performances often used in optoelectronic products, navigation mark identification, target tracking, laser mercury pump, medical positioning light treatment and military weapons field and so on. For example, because it having low work function (φ = 1.6 ev), high current density (10A / cm2), good starting performance, large power output and other characteristics, are widely used in HID lamps. In addition, barium tungsten electrode having low work function, so often used to make electric vacuum and laser device in which the electron emission performance of light products can be achieved from low to high repetition rate (1 ~ 40 times / sec). The start-up performance of stroboscope lamp has been significantly improved which is produced by barium tungsten electrode. On the other hand, because current density of the electrode is high, so the luminance of stroboscope lamp increases by about 15%. At the same time, using barium tungsten electrodes to produce high frequency stroboscope lamp has long service life, up to 500 million times. Besides, during working there are not occur leakage flash, chain lightning and other problems.
Tungsten Supplier: Chinatungsten Online www.chinatungsten.com | Tel.: 86 592 5129696; Fax: 86 592 5129797;Email:sales@chinatungsten.com |
Tungsten News & Prices, 3G Version: http://3g.chinatungsten.com | Molybdenum News & Molybdenum Price: http://news.molybdenum.com.cn |