Tungsten Carbide Valve Ball Applicability (2/2)
- Details
- Category: Tungsten Information
- Published on Wednesday, 17 February 2016 17:50
Theoretically, tungsten carbide ball rely on the role of the media between ball and seat have a mutual compression to achieve cut-off function. The valve seat ring at predetermined contact pressure localized plastic deformation and elastic region, so that it is possible to compensate for manufacturing precision and surface roughness of the sphere, in order to ensure the sealing performance of the ball valve. Then we introduce some common occasions of tungsten carbide ball valve:
1. In the two-position adjustment, sealing requirements of high performance, open and close rapidly (1/4 turn open and close), the larger the pressure, the operating torque, low flow resistance, cavitation or vaporization of the piping system should use tungsten carbide ball;
2. Pipeline with corrosive media;
3. In cryogenic apparatus or high-temperature and high-pressure piping systems;
4. Full bore welded carbide ball valve can be used in pipelines and gas pipelines need buried in the ground;
5. Specially designed V-shaped openings carbide ball structure may have regulatory function;
6. Petrochemical, power systems, metallurgical industry and other fields have a higher operating temperature;
7. Refined oil and natural gas transportation or storage of piping or equipment.
In addition, due to different connectors, it can be divided into carbide ball full bore or reduced diameter valve, welded ball valves, flanged ball valves, floating ball valve threaded connection. Among flanged ball valve (which is the two pipes, fittings or equipment, each fixed in a first flange, and then between the two flanges plus flange gasket, bolt the last two law Flanges tighten it closely combine a removable connector.) the most common, both in the metallurgical oxygen piping system, or in the city gas and natural gas pipeline systems have been widely used.
Tungsten Carbide Supplier: Chinatungsten Online tungsten-carbide.com.cn | Tel.: 86 592 5129696; Fax: 86 592 5129797;Email:sales@chinatungsten.com |
Tungsten News&Tungsten Prices, 3G Version: http://3g.chinatungsten.com | Molybdenum News & Molybdenum Price: http://news.molybdenum.com.cn |
Tungsten Carbide Valve Ball Applicability (1/2)
- Details
- Category: Tungsten Information
- Published on Wednesday, 17 February 2016 17:48
Application of carbide materials plus computer-aided design (CAD), computer aided manufacturing (CAM) and a flexible manufacturing system (FMS is controlled by a unified information system, material handling system and a set of digital control and processing equipment composition, can adapt to the introduction of automated machinery manufacturing system of the object transformed Flexible manufacturing system) and other related technology allows design and manufacturing efficiency and accuracy of the ball valve have been greatly improved.
Tungsten carbide ball valve without any abrasion and wear in the rapid process of opening and closing, and the flow resistance is small and close to zero infinitely when it fully opened, which can well endure the larger pressure difference fully closed. Therefore, equal diameter ball valve can be widely used in pipeline cleaning of oil and gas work. Most of tungsten carbide ball valve due to its ability to wipe a certain opening and closing process can be used in the medium with suspended solid particles. However, since the valve seat ring material (more common with Teflon, synthetic rubber, nylon, etc.) restricted, making it suitable for a temperature range subject to certain restrictions.
Tungsten Carbide Supplier: Chinatungsten Online tungsten-carbide.com.cn | Tel.: 86 592 5129696; Fax: 86 592 5129797;Email:sales@chinatungsten.com |
Tungsten News&Tungsten Prices, 3G Version: http://3g.chinatungsten.com | Molybdenum News & Molybdenum Price: http://news.molybdenum.com.cn |
Porosity Influencing Tungsten Trioxide Ceramic Density
- Details
- Category: Tungsten Information
- Published on Wednesday, 17 February 2016 16:59
Porosity is a measure of the degree of dense objects, the pore volume of the object to a percentage of the total volume; it is the degree of sintering ceramics and refractories and other products, it is the determination of porous material such as activated carbon adsorption capacity, as well as to measure the technical properties of the foam material and so on. The size, temperature and pressure of porosity are related. Generally speaking, the higher the temperature, the greater the pressure, the greater the general porosity. Porosity ceramic material is dense level of characterization.
The test results in the following table:
Sintering temperature |
sample volume |
dry weight of the sample |
water-saturated sample weigh(g) |
significant pore volume |
porosity |
1100 |
0.639 |
4.294 |
4.2652 |
|
|
1180 |
0.4745 |
3.1826 |
3.1725 |
|
|
1200 |
0.2708 |
1.8284 |
1.8295 |
0.0011 |
0.41 |
1210 |
0.2305 |
1.5228 |
1.531 |
0.0082 |
3.56 |
国外样品 |
0.182 |
1.1454 |
1.1528 |
0.0074 |
4.1 |
The data of porosity in the table above shows that the sintering temperature is 1100 ℃ and 1180 ℃, the sintered samples are in loose state, heating 2h, tungsten trioxide dusting off the lumps in boiling water; and the porosity of the sintered samples sintered samples is lower than abroad when the temperature is 1200 ℃, porosity is smaller, and therefore can prove the porosity value increases at this temperature, the sintered density of the sample increase.
Tungsten Oxide Supplier: Chinatungsten Online www.tungsten-oxide.com | Tel.: 86 592 5129696; Fax: 86 592 5129797;Email:sales@chinatungsten.com |
Tungsten News & Prices, 3G Version: http://3g.chinatungsten.com | Molybdenum News & Molybdenum Price: http://news.molybdenum.com.cn |
Morphology and Size of Ammonium Metatungstate Microsphere Prepared by Spray Drying Method
- Details
- Category: Tungsten Information
- Published on Wednesday, 17 February 2016 16:52
AMT Supplier: Chinatungsten Online www.ammonium-metatungstate.com | Tel.: 86 592 5129696; Fax: 86 592 5129797;Email:sales@chinatungsten.com |
Tungsten News&Tungsten Prices, 3G Version: http://3g.chinatungsten.com | Molybdenum News & Molybdenum Price: http://news.molybdenum.com.cn |
Pressure Influencing Tungsten Trioxide Ceramic Density
- Details
- Category: Tungsten Information
- Published on Wednesday, 17 February 2016 16:48
Pressure refers to the object of force occurs in two contact surfaces, or gas to the vertical forces of solid and liquid surface, liquid or solid surface of the vertical force. Solid surface pressure is usually the result of elastic deformation; it is generally the contact force. The surface of the liquid and the gas pressure is usually the result of gravity and molecular motion. The observed effects of stress are not perpendicular to the direction of the contact surface, which usually is a result of pressure and friction interaction.
Detection molding pressure affects densification of tungsten trioxide, preparing the pressure is 4MPa, the sintering temperature is 1200 ℃, holding time 2h to analyze.
The test results in the following table:
Pressure(MPa) |
Density(g/cm³) |
Shrinkage(%) |
3 |
6.67 |
9.87 |
4 |
6.73 |
11.2 |
5 |
6.75 |
11.2 |
10 |
6.80 |
10.5 |
As it can be seen from the data in the table above, we can see sintering densification increases with pressure increasing. In general, the greater the pressure molding, the particles contact more closely, the diffusion resistance is smaller, but the high pressure molding powder may cause brittle fracture. Visible, in order to obtain high-quality tungsten trioxide ceramics, the pressure should be controlled between 4MPa and 5MPa, so that the grain linked closely together.
Tungsten Oxide Supplier: Chinatungsten Online www.tungsten-oxide.com | Tel.: 86 592 5129696; Fax: 86 592 5129797;Email:sales@chinatungsten.com |
Tungsten News & Prices, 3G Version: http://3g.chinatungsten.com | Molybdenum News & Molybdenum Price: http://news.molybdenum.com.cn |
Structure and Thermal Decomposition of Ammonium Metatungstate
- Details
- Category: Tungsten Information
- Published on Wednesday, 17 February 2016 15:17
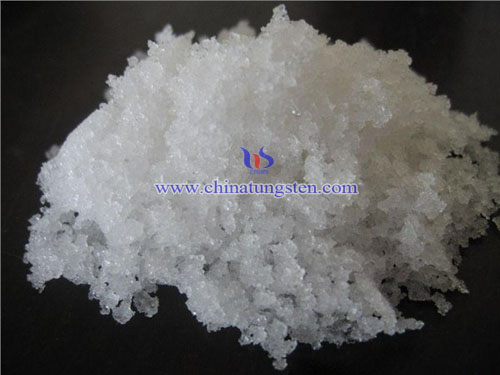
AMT Supplier: Chinatungsten Online www.ammonium-metatungstate.com | Tel.: 86 592 5129696; Fax: 86 592 5129797;Email:sales@chinatungsten.com |
Tungsten News&Tungsten Prices, 3G Version: http://3g.chinatungsten.com | Molybdenum News & Molybdenum Price: http://news.molybdenum.com.cn |
Tungsten Electrode Surface Ablation of Argon Arc Welding
- Details
- Category: Tungsten Information
- Published on Tuesday, 16 February 2016 18:33
Tungsten electrode is an important part of argon arc welding. Besides, tungsten electrode plays an important role in arcing, welding quality and arcing stability. Operation at the high temperature tungsten electrodes will occurs in the mass loss, called electrodes ablation. And ablation can be divided into added oxide ablative and tungsten substrate ablation, and the added oxides include ThO2, CeO2, and La2O3 and so on. Because they melting point is lower than the tungsten substrate’s, so the ablation rate will faster. The ablation of added oxide in the electrode may cause the oxide content in the electrode surface reduction, resulting in hard to arcing or arcing unstable. So as we knew, added oxide in tungsten electrodes ablation in some degree greatly affects the properties of the arcing and the arcing stability of the argon arc welding. On the other hand, the tungsten substrate ablation mainly because of the hot tungsten electrode react with the surrounding environment or oxygen in the shielding gas, and produced oxide will deposit in the head of electrode to cause tungsten substrate ablation. Tungsten substrate ablation not only seriously affect the stability of the arcing, and will cause the deposited tungsten shedding, changing the composition of the welding content, affecting the quality of welding.
The experiment found that reducing tungsten electrode ablation not only can improve the life of the tungsten electrode, and can ensure the welding quality. And reducing the tungsten electrode ablation there are some approaches as following:
1. To improve the purity of the inert gas, which at the same time reducing the oxygen content;
2. In the welding process, to use appropriate protective gas flow;
3.To select appropriate and well-torch welding gun and electrode size;
4. To use tungsten electrode which doped nano-oxide.
Tungsten Supplier: Chinatungsten Online www.chinatungsten.com | Tel.: 86 592 5129696; Fax: 86 592 5129797;Email:sales@chinatungsten.com |
Tungsten News & Prices, 3G Version: http://3g.chinatungsten.com | Molybdenum News & Molybdenum Price: http://news.molybdenum.com.cn |
Synthesis and Interfacial Electron Transfer of a Composite Film of Graphene and AMT
- Details
- Category: Tungsten Information
- Published on Tuesday, 16 February 2016 18:08

APT Supplier: Chinatungsten Online www.ammonium-paratungstate.com | Tel.: 86 592 5129696; Fax: 86 592 5129797;Email:sales@chinatungsten.com |
Tungsten News&Tungsten Prices, 3G Version: http://3g.chinatungsten.com | Molybdenum News & Molybdenum Price: http://news.molybdenum.com.cn |
Tungsten Copper with Gradient Structure (2/2)
- Details
- Category: Tungsten Information
- Published on Tuesday, 16 February 2016 17:15
For the manufacturing process of the gradient structure tungsten-copper composite materials, researchers and scholars in related fields, and also made a variety of attempts to conceive. Here is a brief introduction to several related new technologies, such as conventional dry lamination method, hierarchical load a different size of tungsten powder, cold pressed, sintered, after copper infiltration preparing different graded material consisting of tungsten-copper ( good sintered porous tungsten skeleton electrochemical corrosion formed along the direction of tungsten skeleton having a gradient porosity by infiltration of copper can be obtained having a continuous change in the composition of tungsten copper gradient material); the other one uses hot isostatic pressing diffusion bonding to form tungsten copper with gradient structure by different contents.
In addition, another type is prepared by continuous gradient layer, such as slip casting, sedimentation molding, centrifugal molding, etc. Plasma spraying is a kind of new method that are compacting and sintering tungsten copper powder with different content. There are two methods which have already patented process, one is the use of powder metallurgy - infiltration process. Preparation of powder metallurgy method which utilizes two components completely different copper tungsten compact, then where the thermal conductivity of tungsten copper larger compact embedded in another compact, due to the embedding of relatively high copper content briquette making its thermal conductivity is relatively high, and has a lower peripheral compact copper content, thus ensuring the overall coefficient of thermal expansion gradient material decreases. Another one is that combines tungsten copper (W-Cu) with ceramic based on aluminum nitride-aluminum (AlN-Al), ceramic has a gradient structure with a metal having a thermal expansion coefficient due to the match, so the lower internal stress, and as part of a combination of metal and ceramic high thermal conductivity such that heat will not affect the heat concentrated in the buffer layer and the heat radiating effect of the heat sink materials.
Tungsten Copper Supplier: Chinatungsten Online tungsten-copper.com | Tel.: 86 592 5129696; Fax: 86 592 5129797;Email:sales@chinatungsten.com |
Tungsten News & Prices, 3G Version: http://3g.chinatungsten.com | Molybdenum News & Molybdenum Price: http://news.molybdenum.com.cn |
Tungsten Copper with Gradient Structure (1/2)
- Details
- Category: Tungsten Information
- Published on Tuesday, 16 February 2016 17:13
Tungsten copper (W-Cu) and molybdenum copper (Mo-Cu) are composed of respectively tungsten and molybdenum with copper, which called two-phase composites and has many advantages when it used in some devices with high power, such as high hardness, high strength, high melting point, excellent chemical stability, excellent thermal and electrical conductivity and lower coefficient of thermal expansion. As a kind of electronic packaging heat sink material takes place of conventional materials gradually, the related researchers make an intensive study on tungsten copper, which includes add active agents, change powder properties to improve the sintering density of tungsten copper materials.
However, the conditions of some industries today have become more and more strict (including temperature, pressure, power, etc.), which requires tungsten copper has better properties. Inspired by tungsten carbide with gradient structure, the Japanese researcher propose new concept of functional materials with gradient structure and from the preparation process structure, computer simulation and forecasting has done sufficient research, have also made substantial progress, so that it plays an important role in some high-power devices. Tungsten copper composite material is kind of two-phase psudoalloy, which composed of two metals tungsten and copper with a great difference in physicochemical properties.
Its properties will change with the structure. Viewed from the aspect of gradient structure, it can has one end with a high hardness, high melting point, tungsten or copper content is low high-density tungsten copper, while the other end is a good electrical and thermal conductivity and high plasticity of copper or copper content of tungsten, copper, in this way the formation of gradient structure having a tungsten-copper composite materials have a good specificity and a broader application prospect.
Tungsten Copper Supplier: Chinatungsten Online tungsten-copper.com | Tel.: 86 592 5129696; Fax: 86 592 5129797;Email:sales@chinatungsten.com |
Tungsten News & Prices, 3G Version: http://3g.chinatungsten.com | Molybdenum News & Molybdenum Price: http://news.molybdenum.com.cn |