Tungsten Alloy Tennis Rackets CounterweightsⅠ
- Details
- Category: Tungsten Information
- Published on Monday, 28 December 2015 16:57
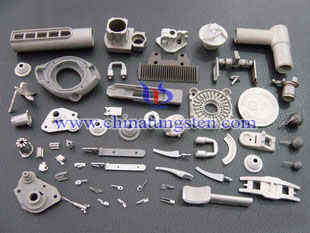
Tungsten Alloy Supplier: Chinatungsten Online www.tungsten-alloy.com | Tel.: 86 592 5129696; Fax: 86 592 5129797;Email:sales@chinatungsten.com |
Tungsten News & Prices, 3G Version: http://3g.chinatungsten.com | Molybdenum News & Molybdenum Price: http://news.molybdenum.com.cn |
Temperature’s Effects on Ammonium Paratungstate Production
- Details
- Category: Tungsten Information
- Published on Monday, 28 December 2015 16:24
Tungsten Supplier: Chinatungsten Online www.chinatungsten.com | Tel.: 86 592 5129696; Fax: 86 592 5129797;Email:sales@chinatungsten.com |
Tungsten News & Prices, 3G Version: http://3g.chinatungsten.com | Molybdenum News & Molybdenum Price: http://news.molybdenum.com.cn |
Effect of Stirring Speed on Ammonium Paratungstate Production
- Details
- Category: Tungsten Information
- Published on Monday, 28 December 2015 16:21
The test results are shown in Figure 2. It’s complicated that stirring speed affects nucleation. On one hand, the stirring speed is accelerated, so that the newly formed crystals were minced and the form much crystal nucleus, particle size becomes fine, on the other hand, in a certain stirring speed range, increasing the stirring speed can increase the relative velocity between solid and liquid, thereby increasing the speed of nuclei grow.
Tungsten Supplier: Chinatungsten Online www.chinatungsten.com | Tel.: 86 592 5129696; Fax: 86 592 5129797;Email:sales@chinatungsten.com |
Tungsten News & Prices, 3G Version: http://3g.chinatungsten.com | Molybdenum News & Molybdenum Price: http://news.molybdenum.com.cn |
Tungsten Trioxide Introduction 3/3
- Details
- Category: Tungsten Information
- Published on Monday, 28 December 2015 16:19
Tungsten Trioxide - Preparation
Tungsten concentrate with sodium hydroxide or soda from the melt temperature, or high pressure sodium tungstate solution prepared boiled, and then purified by ion exchange or extraction, evaporation process to obtain ammonium paratungstate crystals, and then calcined at 700 ℃ to obtain tungsten trioxide. If you are scheelite concentrate as raw material, can also be decomposed into hydrochloric acid ,, then by ammonia dissolution, evaporation process to obtain ammonium paratungstate crystals were then calcined at 700 ℃ was prepared by the tungsten trioxide. It can also be directly obtained by calcining tungstate tungsten trioxide. The main reaction is as follows:
FeWO4 + 4NaOH → 2Na2WO4 + Fe (OH) 2
MnWO4 + 4NaOH → 2Na2WO4 + Mn (OH) 2
CaWO4 + 2HCI = H2WO4 + CaCI2
H2WO4 + 2NH4 (OH) = (NH4) 2WO4 + 2H2O
12Na2WO4 + 14HCl → 5Na2O • 12WO3 + 14NaCl + 7H2O
5Na2O • 12WO3 + 10NH4Cl → 5 (NH4) 2O • 12WO3 + 10NaCl
5 (NH4) 2 • 12WO3 + 10HCl + 7H2O → 12H2WO4 + 10NH4Cl
H2WO4 → WO3 + H2O
5 (NH4) 2O-12WO3-6H2O → 12WO3 + 10NH3 ↑ + 11H2O
Tungsten Trioxide - Inspection
Weigh 0.5g sample, accurate to 0.000 2g, placed in 250mL beaker high type ammonia solution 40mL, cover the surface of the dish and heated in the furnace temperature, the solution was kept close to boiling point, stirring while heating the sample to complete dissolved, remove the hydrochloric acid was added 10mL After cooling to room temperature, carefully placed on a boiling water bath boiling concentrated by evaporation to a volume of about 10mL. The solution was diluted with 70 ℃ warm water to 70mL ~ 80mL, stirring constantly adding hydrochloric acid cinchonine solution 10mL, placed in a water bath (70 ℃ ± 5 ℃) on the insulation 1h, stirring once every 20min, the solution was filtered by pouring method (using Slow 11cm quantitative filter paper), glass and precipitated with beaker wall attached to a quantitative filter paper slowly wipe precipitate was washed with hydrochloric acid cinchonine lotion several times, volume control and the filtrate and washings about 180mL. The precipitate and filter paper moved to a constant weight of platinum crucible in an electric furnace carefully placed after ashing temperature furnace (750 ℃) in burning 10min, removed, cooled to room temperature was added 3mL ~ 5mL hydrofluoric acid and a few drops sulfuric acid, in a boiling water bath after nearly dry steam to move to the electric heating, the risk to make white smoke, then placed in a high temperature furnace (750 ℃) in burning 30min, removed, placed in a desiccator to cool to room temperature, weighed, repeated several times until a constant weight.
NOTE: The sample was dissolved with ammonia, the solution should be avoided so violent boiling, reduce volatilization of ammonia. If long after dissolving solution always appears cloudy or residue, quantitative filter paper, then with warm ammonia [1.5% (m / m)] repeatedly washed thoroughly beaker and filter paper, collect the filtrate and washings continue remaining experiment.
Expression of Results
Tungsten trioxide content expressed as a percentage by mass, according to equation (1):
X(%)=(m1-m2)÷m0
Wherein: X- mass percentage of tungsten trioxide, %;
m0- crucible, g;
m1- crucible and precipitation, g;
m2 Quality sample, g;
The average of the two measurements, the results reservations two decimal places;
The precision r = 0.25%; R = 0.42%.
Tungsten Oxide Supplier: Chinatungsten Online www.tungsten-oxide.com | Tel.: 86 592 5129696; Fax: 86 592 5129797;Email:sales@chinatungsten.com |
Tungsten News & Prices, 3G Version: http://3g.chinatungsten.com | Molybdenum News & Molybdenum Price: http://news.molybdenum.com.cn |
Tungsten Trioxide Introduction 2/3
- Details
- Category: Tungsten Information
- Published on Monday, 28 December 2015 16:07
Tungsten Trioxide - Precautions
Health hazards: low toxicity. The eyes, skin irritation. Tungsten steel smelting workers had systemic weakness, fever, measles-like rash, proteinuria, may be inhaled and smelting of tungsten trioxide related.
Explosion Hazard: This product is flammable, irritating.
Aid Measures
Skin contact: Remove contaminated clothing, rinse with plenty of water.
Eye contact: Did eyelid, mobile water or saline rinse.
Inhalation: rapidly from the scene to fresh air. Keep the airway open. If breathing is difficult, give oxygen. If breathing stops, artificial respiration immediately.
Ingestion: drink enough water, induce vomiting.
Fire-fighting Measures
Hazardous characteristics: with halogen compounds such as bromine pentafluoride, chlorine trifluoride react violently.
Hazardous combustion products: harmful toxic fumes.
Fire fighting methods: firefighters must wear fire protective body suits, the wind on fire. As far as possible to move containers from the scene empty Department for fire fighting. Then select the appropriate fire extinguishing agent fire reasons.
Accident
Emergency treatment: Isolation leak contaminated areas, restricting access. Recommended emergency personnel wearing dust masks, wearing overalls general operations. Do not direct contact with leakage.
A small leak: to avoid dust, carefully scan, collected in dry, clean, covered containers.
Large Leak: recycling or collection shipped to the waste disposal sites.
Handling and Storage
Handling Precautions: closed operation, local exhaust. Prevent dust released into the air workshop. The operator must go through specialized training, strict adherence to rules. Proposed operators wear self-absorption filter respirators, wearing chemical protective safety glasses, wear rubber acid suit, wearing rubber gloves acid. Avoid generating dust. Avoid bromine pentafluoride, chlorine trifluoride touch. Equipped with spill response equipment. Empty containers may be harmful residues.
Storage: Store in a cool, ventilated warehouse. Away from fire, heat source. Prevent direct sunlight. Packing seal. It should bromine pentafluoride, chlorine trifluoride stored separately and avoid mixing reservoir. Storage areas should be equipped with suitable material spill.
Tungsten Oxide Supplier: Chinatungsten Online www.tungsten-oxide.com | Tel.: 86 592 5129696; Fax: 86 592 5129797;Email:sales@chinatungsten.com |
Tungsten News & Prices, 3G Version: http://3g.chinatungsten.com | Molybdenum News & Molybdenum Price: http://news.molybdenum.com.cn |
Tungsten Trioxide Introduction 1/3
- Details
- Category: Tungsten Information
- Published on Monday, 28 December 2015 15:57
Tungsten trioxide is yellow powder. It dissolves in water, soluble in alkali; slightly dissolves acid .It is used to make refractory alloys and tungsten carbide, tungsten and fire system materials. Tungsten ore and soda ash by eutectic after adding acid derived. It depends on the structure of the tungsten trioxide temperature: 740 ° C above it is tetragonal; 330-740 ° C is orthorhombic; 17-330 ° C is monoclinic; -50-17 ° C for the three triclinic. Tungsten trioxide is mainly used in the production of tungsten reduction calcined powder and tungsten carbide powder, and then used to produce carbide products, such as tool and die manufacturing. Tungsten concentrate with sodium hydroxide or soda from the melt temperature, or high pressure sodium tungstate solution prepared boiled, and then purified by ion exchange or extraction, evaporation process to obtain ammonium paratungstate crystals, and then calcined at 700 ℃ to obtain tungsten trioxide.
Chinese name: tungsten trioxide
Chinese alias: tungsten anhydride; tungsten oxide (VI)
English name: Tungsten trioxide
Tungsten Trioxide - Physical and Chemical Properties
Physical Properties
Tungsten Trioxide Structure
Tungsten Trioxide Structural Formula
Melting point (℃): 1472
Relative density (water = 1): 7.16
Boiling point (℃): 1837
Formula: WO3
Molecular Weight: 231.85
Solubility: insoluble in water, soluble in alkali, slightly soluble in acid
Chemical Properties
Significant sublimation at 850 ℃; hardly inorganic acid except hydrofluoric acid and can slowly dissolve in ammonia or concentrated alkali solution. Heating the reaction of chlorine and chlorine oxides, but not reacted with bromine, iodine. Structure depends on the temperature of tungsten trioxide: it is more than 740 ° C for the tetragonal, 330-740 ° C orthorhombic, 17-330 ° C for the monoclinic system, -50-17 ° C for the three triclinic. The most common structures monoclinic, space group P21 / n.
Tungsten Trioxide - Specifications
Tungsten Trioxide Specifications
Tungsten Trioxide - the Role and Purpose
Tungsten trioxide is mainly used in the production of tungsten reduction calcined powder and tungsten carbide powder, and then used to produce carbide products, such as tool and die manufacturing. But also it can be used in the manufacture of pure tungsten products, tungsten, tungsten, tungsten electrode; and uses a counterweight and radiation shielding materials. Industrial production is also a small amount of yellow ceramics used as a coloring agent. Shipbuilding industry, tungsten oxide, tungsten is used as an important anti-corrosion paint and coatings materials.
Tungsten Oxide Supplier: Chinatungsten Online www.tungsten-oxide.com | Tel.: 86 592 5129696; Fax: 86 592 5129797;Email:sales@chinatungsten.com |
Tungsten News & Prices, 3G Version: http://3g.chinatungsten.com | Molybdenum News & Molybdenum Price: http://news.molybdenum.com.cn |
Cupric Sulphate Precipitation Eliminating Molybdenum of Sodium Tungstate
- Details
- Category: Tungsten Information
- Published on Monday, 28 December 2015 11:37
Sodium Tungstate Supplier: Chinatungsten sodium-tungstate.com | Tel.: 86 592 5129696; Fax: 86 592 5129797;Email:sales@chinatungsten.com |
Tungsten News & Prices, 3G Version: http://3g.chinatungsten.com | Molybdenum News & Molybdenum Price: http://news.molybdenum.com.cn |
Anion Exchange Resin Eliminating Molybdenum of Sodium Tungstate
- Details
- Category: Tungsten Information
- Published on Monday, 28 December 2015 11:33
Sodium Tungstate Supplier: Chinatungsten sodium-tungstate.com | Tel.: 86 592 5129696; Fax: 86 592 5129797;Email:sales@chinatungsten.com |
Tungsten News & Prices, 3G Version: http://3g.chinatungsten.com | Molybdenum News & Molybdenum Price: http://news.molybdenum.com.cn |
Recycling and Reusing Ammonium Paratungstate Crystal Liquor 3/3
- Details
- Category: Tungsten Information
- Published on Monday, 28 December 2015 08:31
For Recycling and Reusing Ammonium Paratungstate Crystal Liquor 1/3,please see in
http://news.chinatungsten.com/en/tungsten-information/81761-ti-10572
APT Supplier: Chinatungsten Online www.ammonium-metatungstate.com | Tel.: 86 592 5129696; Fax: 86 592 5129797;Email:sales@chinatungsten.com |
Tungsten News&Tungsten Prices, 3G Version: http://3g.chinatungsten.com | Molybdenum News & Molybdenum Price: http://news.molybdenum.com.cn |
Recycling and Reusing Ammonium Paratungstate Crystal Liquor 2/3
- Details
- Category: Tungsten Information
- Published on Monday, 28 December 2015 08:27
For Recycling and Reusing Ammonium Paratungstate Crystal Liquor 1/3,please see in
http://news.chinatungsten.com/en/tungsten-information/81754-ti-10570
APT Supplier: Chinatungsten Online www.ammonium-metatungstate.com | Tel.: 86 592 5129696; Fax: 86 592 5129797;Email:sales@chinatungsten.com |
Tungsten News&Tungsten Prices, 3G Version: http://3g.chinatungsten.com | Molybdenum News & Molybdenum Price: http://news.molybdenum.com.cn |