Electrolysis method for preparing tungsten trioxide powder
- Details
- Category: Tungsten Information
- Published on Friday, 25 December 2015 16:19
Tungsten has a high melting point, vapor pressure, high hardness, corrosion resistance and good acid excellent physical and chemical properties, for use in various sectors of the national economy and defense industry range and consumption is increasing year by year. However, tungsten is an important national strategic non-renewable resources, although tungsten ore resources to maintain our country ranks first in the world, but to deal with the preparation of tungsten concentrate tungsten metal powder to go through the decomposition of tungsten concentrate, APT system to take three Preparation of tungsten oxide and reducing tungsten powder preparation process, there is a long production process and other shortcomings, the development of short process, improve resource utilization, reduce production costs has become a trend in metallurgical technology development.
Molten salt electrolysis
Molten salt electrolysis method is one method of producing metal from theory, most of the metal is obtained by the molten salt electrolysis process, especially for those who can not generate more negative deposition potential of metal ions in an aqueous solution, must melt salt electrolysis. Currently, aluminum, and some rare earth metals by molten salt electrolysis production. Given the molten salt electrolysis method for the preparation of metals and their alloys aspects of the unique advantages and potential of certain alkali metals, alkaline earth metals (such as Li, Na, Mg), almost all of the transition metal elements and rare earth elements, and some rare high melting point metal such as Ti, Sc, Nab, Ta, has become with molten salt electrolysis producing metal hotspot. In addition, studies using molten salt electrolysis method also involves some non-metallic elements such as B, Si and the like. With the success of the preparation of a number of elemental metals, molten salt electrolysis research in the field of preparation of the alloy is also very wide, including aluminum alloy (such as Al-k, Al-Sr like), magnesium alloys, titanium alloys and rare earth alloy.
The experiment comprises the following steps: (1) mixing molten salt and water removal (2) treatment electrode (3) pre-electrolyzed (4) electrolysis (main parameters: temperature, cell voltage, current density and electrolysis time, etc.) (5) Tungsten powder separation and collection. Preparation of raw material of the present invention is a low cost, short process, simple equipment, there is no solid, liquid and gas waste emissions, no secondary pollution, at low cost direct electrolysis of tungsten powder prepared from tungstate.
Tungsten Oxide Supplier: Chinatungsten Online www.tungsten-oxide.com | Tel.: 86 592 5129696; Fax: 86 592 5129797;Email:sales@chinatungsten.com |
Tungsten News & Prices, 3G Version: http://3g.chinatungsten.com | Molybdenum News & Molybdenum Price: http://news.molybdenum.com.cn |
Tungsten Alloy Counterweights Application in Ski Board
- Details
- Category: Tungsten Information
- Published on Friday, 25 December 2015 14:55
Tungsten Alloy Supplier: Chinatungsten Online www.tungsten-alloy.com | Tel.: 86 592 5129696; Fax: 86 592 5129797;Email:sales@chinatungsten.com |
Tungsten News & Prices, 3G Version: http://3g.chinatungsten.com | Molybdenum News & Molybdenum Price: http://news.molybdenum.com.cn |
Tungsten Alloy Gaming Mouse Counterweights
- Details
- Category: Tungsten Information
- Published on Friday, 25 December 2015 14:53
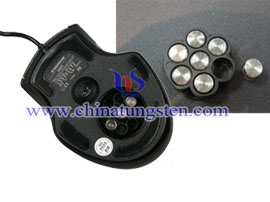
Tungsten Alloy Supplier: Chinatungsten Online www.tungsten-alloy.com | Tel.: 86 592 5129696; Fax: 86 592 5129797;Email:sales@chinatungsten.com |
Tungsten News & Prices, 3G Version: http://3g.chinatungsten.com | Molybdenum News & Molybdenum Price: http://news.molybdenum.com.cn |
Tungsten Alloy Ailerons CounterweightsⅡ
- Details
- Category: Tungsten Information
- Published on Friday, 25 December 2015 14:50
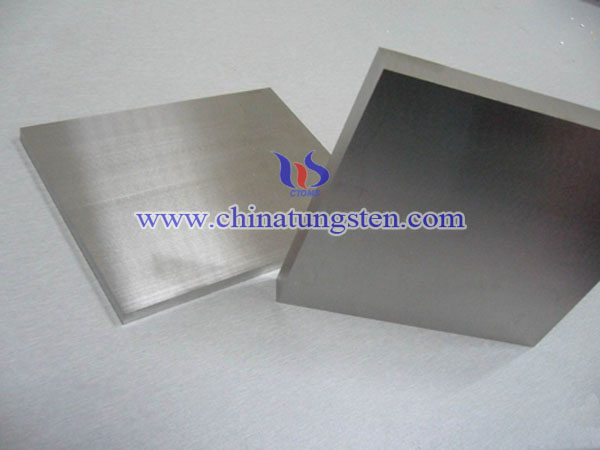
Tungsten Alloy Supplier: Chinatungsten Online www.tungsten-alloy.com | Tel.: 86 592 5129696; Fax: 86 592 5129797;Email:sales@chinatungsten.com |
Tungsten News & Prices, 3G Version: http://3g.chinatungsten.com | Molybdenum News & Molybdenum Price: http://news.molybdenum.com.cn |
Tungsten Alloy Ailerons CounterweightsⅠ
- Details
- Category: Tungsten Information
- Published on Friday, 25 December 2015 14:46
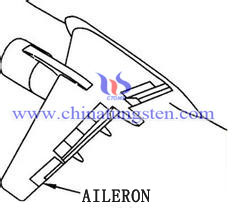
Tungsten Alloy Supplier: Chinatungsten Online www.tungsten-alloy.com | Tel.: 86 592 5129696; Fax: 86 592 5129797;Email:sales@chinatungsten.com |
Tungsten News & Prices, 3G Version: http://3g.chinatungsten.com | Molybdenum News & Molybdenum Price: http://news.molybdenum.com.cn |
Submicron Spherical Tungsten Powder from Ammonium Paratungstate
- Details
- Category: Tungsten Information
- Published on Friday, 25 December 2015 10:25
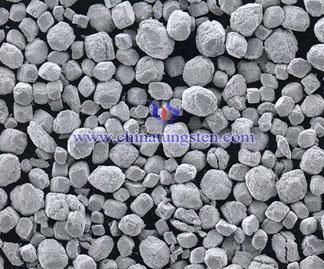
4.Dexoygenizing tungsten trioxide we obtained in step3 in the hydrogen for the second time,tungsten powder comes,
APT Supplier: Chinatungsten Online www.ammonium-metatungstate.com | Tel.: 86 592 5129696; Fax: 86 592 5129797;Email:sales@chinatungsten.com |
Tungsten News&Tungsten Prices, 3G Version: http://3g.chinatungsten.com | Molybdenum News & Molybdenum Price: http://news.molybdenum.com.cn |
Recrystallization to Produce High Purity Ammonium Paratungstate
- Details
- Category: Tungsten Information
- Published on Friday, 25 December 2015 10:20
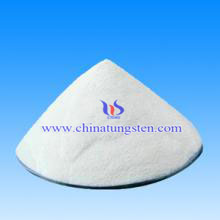
APT Supplier: Chinatungsten Online www.ammonium-metatungstate.com | Tel.: 86 592 5129696; Fax: 86 592 5129797;Email:sales@chinatungsten.com |
Tungsten News&Tungsten Prices, 3G Version: http://3g.chinatungsten.com | Molybdenum News & Molybdenum Price: http://news.molybdenum.com.cn |
Preparation of submicron molybdenum trioxide superfine powder 2/2
- Details
- Category: Tungsten Information
- Published on Thursday, 24 December 2015 17:48
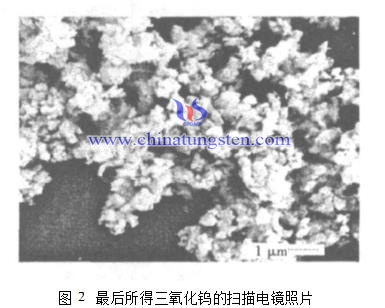
Tungsten Oxide Supplier: Chinatungsten Online www.tungsten-oxide.com | Tel.: 86 592 5129696; Fax: 86 592 5129797;Email:sales@chinatungsten.com |
Tungsten News & Prices, 3G Version: http://3g.chinatungsten.com | Molybdenum News & Molybdenum Price: http://news.molybdenum.com.cn |
Preparation of Submicron Tungsten Trioxide Ultrafine Powder 1/2
- Details
- Category: Tungsten Information
- Published on Thursday, 24 December 2015 17:44
Due to various excellent properties of fine-grain carbide, submicron powder (average particle 1m) demand was a rapid upward trend in recent years. Today, industrial production has been able to ultrafine tungsten powder (average particle size 0.5m). Production of ultra-fine tungsten oxide powder material made increasing demands, especially in the purity and uniformity of raw materials.
The method of preparation of ultrafine tungsten trioxide powder there are many, the following method is used in many redox. Experimental procedure:
(1) APT was calcined in air at a temperature 500 ℃.
(2) Calcining the resulting reduction in hydrogen tungsten trioxide, temperature 850 ℃, insulation 25min.
(3) Oxidation in air after the first reduction resulting tungsten powder, temperature 500 ℃, insulation 20min.
(4)Reduction in hydrogen tungsten trioxide first after oxidation, temperature 850 ℃, insulation 25min.
(5) In the air oxidation of the second reduction resulting tungsten powder, temperature 500 ℃, insulation 20min.
(6) After the second oxidation resulting tungsten trioxide and second reduction resulting tungsten powder dispersed in distilled water, made after laser particle size analysis.
(7) Analytically pure alcohol dispersion of tungsten oxide and tungsten powder made after the electron probe scanning.
The particle size distribution of the resulting product test each step of FIG.
Analysis of results:
ATP obtained after calcined tungsten trioxide, most were pine needles together. When reduced under a hydrogen atmosphere, the surface of the tungsten trioxide aggregate is first restored, so that the surface density becomes smaller, because the tungsten trioxide powder since the tungsten is generated when deoxidation is reduced significantly smaller volume. That is, the reunion surface becomes fluffy. This reunion internal tungsten trioxide reduction will surface tungsten powder stays split, so a lot of surface microcracks reunion. Some also reunite a larger particle size; surface energy is small, cracks deeper, a direct result of reunion split, split into pieces smaller reunion. Thus, when generating the tungsten powder is oxidized, the surface of the tungsten powder agglomeration direct oxidation of tungsten trioxide. However, the reunion internal tungsten powder to be oxidized, oxygen atom necessary to reunite through the cracks into the interior surface combined with tungsten powder, which is sufficient to cause the crack to expand reunion split. Although this is a combination of an oxygen atom of tungsten powder, but the particle size or become smaller reasons. About produced tungsten trioxide have agglomeration of reasons, because of the oxidation reaction can be considered bound oxygen atoms, so that would have to rely on relatively close between tungsten powder filled with oxygen, thereby forming a reunion. After re-oxidation reduction of tungsten oxide, tungsten trioxide significantly smaller particle size, when the reason is still in deoxygenating reduction and tungsten
powder cracks.
Tungsten Oxide Supplier: Chinatungsten Online www.tungsten-oxide.com | Tel.: 86 592 5129696; Fax: 86 592 5129797;Email:sales@chinatungsten.com |
Tungsten News & Prices, 3G Version: http://3g.chinatungsten.com | Molybdenum News & Molybdenum Price: http://news.molybdenum.com.cn |
Ball Milling Time Effect on Tungsten copper Electrode Powder Granularity
- Details
- Category: Tungsten Information
- Published on Thursday, 24 December 2015 17:03
High speed and high frequency of impact by high energy planetary ball milling grinding media, which is beneficial for energy conversion and the transport and diffusion of atoms, molecular and plasma. Some experiments show that the milling strength has an important influence on the formation of mechanically alloyed amorphous. When the strength is low, the powder is formed into an amorphous longer, even unable to form an amorphous; while the strength is high, forming an amorphous time will be greatly shortened, and help broaden the scope of amorphous components, but continued milling when it would make already amorphous powder re-crystallization of the formation of a new phase. High-energy ball milling easily forms a stable compound rather than amorphous. Ball milling time directly affects the composition and purity of powder production.
The amorphous and crystalline transformation of some metals or alloys only within a certain time, the milling time is too short too small to gather energy inside the material damage which binds covalently; the long ball milling time will cause other changes. In the process of grinding, due to the friction and compacts of powder, the self temperature of powder, partial temperature increasing is beneficial for solid-phase reaction. But overall temperature rise will reunite furniture material and adhesion between the ball and the cylinder wall and the milling of certain organic compounds, high temperature will cause it to break down and so on.
Furthermore, under the effect of compaction, rolling and cold heading between grinding ball or inside wall. With the increasing ball milling time, tungsten copper (W-Cu) powder will form schistose composite powder under plastic deformation and cold welding. Since microscopic strain hardening and increased plastic composite powder decreased, resulting in its fracture refinement, the particles have a break after constantly repeated cold welding and re-fracture, mixing tungsten copper alloy electrode particles are more uniform composite powder becomes more small homogeneous particles.
Tungsten Copper Supplier: Chinatungsten Online tungsten-copper.com | Tel.: 86 592 5129696; Fax: 86 592 5129797;Email:sales@chinatungsten.com |
Tungsten News & Prices, 3G Version: http://3g.chinatungsten.com | Molybdenum News & Molybdenum Price: http://news.molybdenum.com.cn |