Effect of Time on Ammonium Paratungstate Production
- Details
- Category: Tungsten Information
- Published on Tuesday, 29 December 2015 17:47
Tungsten Supplier: Chinatungsten Online www.chinatungsten.com | Tel.: 86 592 5129696; Fax: 86 592 5129797;Email:sales@chinatungsten.com |
Tungsten News & Prices, 3G Version: http://3g.chinatungsten.com | Molybdenum News & Molybdenum Price: http://news.molybdenum.com.cn |
Effect of the Original Solution Purity on APT Crystallization
- Details
- Category: Tungsten Information
- Published on Tuesday, 29 December 2015 17:42
When the impurities contained in ammonium tungstate solution is not too high, the influence on crystal grains is not obvious. test taking into account the normal production, the amount of ammonium chloride in ammonium tungstate solution prepared by ion exchange method was quite different from the one prepared by classic method.
Tungsten Supplier: Chinatungsten Online www.chinatungsten.com | Tel.: 86 592 5129696; Fax: 86 592 5129797;Email:sales@chinatungsten.com |
Tungsten News & Prices, 3G Version: http://3g.chinatungsten.com | Molybdenum News & Molybdenum Price: http://news.molybdenum.com.cn |
Tungsten Alloy Shielding Application in PETⅡ
- Details
- Category: Tungsten Information
- Published on Tuesday, 29 December 2015 17:23
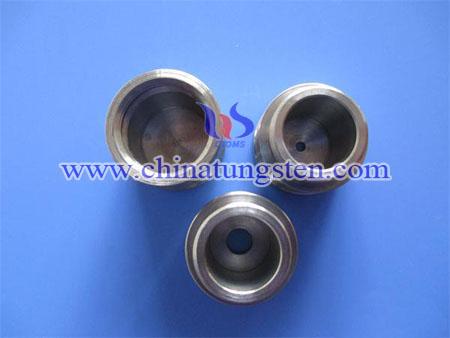
Tungsten Alloy Supplier: Chinatungsten Online www.tungsten-alloy.com | Tel.: 86 592 5129696; Fax: 86 592 5129797;Email:sales@chinatungsten.com |
Tungsten News & Prices, 3G Version: http://3g.chinatungsten.com | Molybdenum News & Molybdenum Price: http://news.molybdenum.com.cn |
Cemented Carbide High-end Products
- Details
- Category: Tungsten Information
- Published on Tuesday, 29 December 2015 17:06
With the development of technology and equipments of tungsten carbide, high-end tungsten carbide products are developing to different requirements of customers. The main application of tungsten carbide products are cutting tools, mining tools and some wear parts.
1. Cutting tool
Cutting tool is one of the most significant applications of tungsten carbide, due to its high hardness, high strength, thermal stability and high precision, which dominates the world market of cutting tool gradually. At present, coated tungsten carbide CNC blade, printed circuit board (PCB) micro drill and precision hole overall tungsten carbide tool are the most high-end products in the field. So far, coated tungsten carbide CNC has diverse coating layer meets different requirements, such as aluminum oxide (Al2O3), titanium nitride (TiN), Hf, Zr and some rare earth elements or ceramics powder; PCB micro drills and mills focus on the coated cutting tools with less than 0.3mm diameter; precision hole overall tungsten carbide tools orient to special use and deep processing products.
2. Mining tool
Tungsten carbide has a broad prospect in energy, minerals and offshore drilling. There are three types of high-end tungsten carbide products: one is mineral mining, such as mating buttons for rock drilling; and ultra fine grain tungsten carbide drill bit for offshore drilling and deep well drilling; another one is suitable for complicate stratum cutting and public facilities construction. In a word, high-end tungsten carbide product for mining tools tends to ultra coarse grain and new structure.
3. Wear part
Some mold manufacturing industries requires high hardness, high toughness and excellent electrochemical corrosion resistance, using tungsten carbide will has better precision, strength and suitable for sealing ring bushing or wire drawing die, etc.
Tungsten Carbide Supplier: Chinatungsten Online tungsten-carbide.com.cn | Tel.: 86 592 5129696; Fax: 86 592 5129797;Email:sales@chinatungsten.com |
Tungsten News&Tungsten Prices, 3G Version: http://3g.chinatungsten.com | Molybdenum News & Molybdenum Price: http://news.molybdenum.com.cn |
Tungsten Alloy Shielding Application in PETⅠ
- Details
- Category: Tungsten Information
- Published on Tuesday, 29 December 2015 16:29
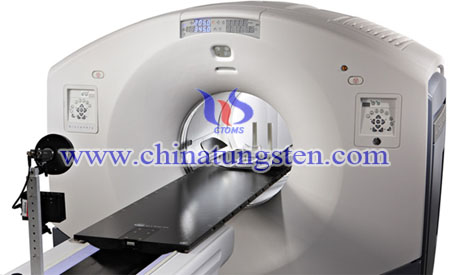
Tungsten Alloy Supplier: Chinatungsten Online www.tungsten-alloy.com | Tel.: 86 592 5129696; Fax: 86 592 5129797;Email:sales@chinatungsten.com |
Tungsten News & Prices, 3G Version: http://3g.chinatungsten.com | Molybdenum News & Molybdenum Price: http://news.molybdenum.com.cn |
Tungsten Alloy Shielding Application in X-ray MachineⅡ
- Details
- Category: Tungsten Information
- Published on Tuesday, 29 December 2015 16:26
Tungsten Alloy Supplier: Chinatungsten Online www.tungsten-alloy.com | Tel.: 86 592 5129696; Fax: 86 592 5129797;Email:sales@chinatungsten.com |
Tungsten News & Prices, 3G Version: http://3g.chinatungsten.com | Molybdenum News & Molybdenum Price: http://news.molybdenum.com.cn |
Tungsten Alloy Shielding Application in X-ray MachineⅠ
- Details
- Category: Tungsten Information
- Published on Tuesday, 29 December 2015 16:24
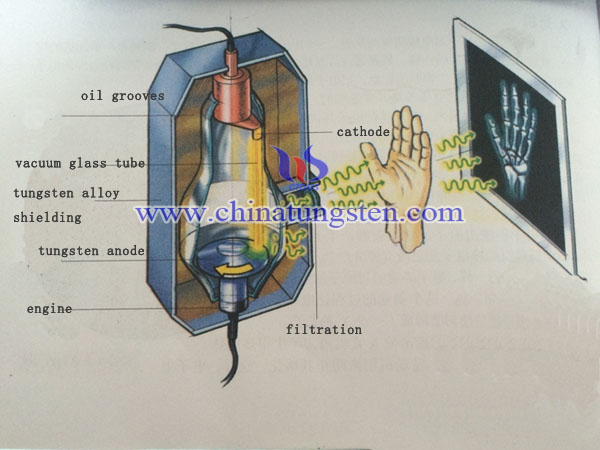
Tungsten Alloy Supplier: Chinatungsten Online www.tungsten-alloy.com | Tel.: 86 592 5129696; Fax: 86 592 5129797;Email:sales@chinatungsten.com |
Tungsten News & Prices, 3G Version: http://3g.chinatungsten.com | Molybdenum News & Molybdenum Price: http://news.molybdenum.com.cn |
Soda Thermal Decomposition Scheelite to Produce Sodium Tungstate
- Details
- Category: Tungsten Information
- Published on Tuesday, 29 December 2015 09:04
More than 20 kinds of tungsten minerals have been discovered in the nature. But wolframite and scheelite have the value of industrial research. Scheelite is the main raw material of tungsten smelting. The traditional industrial production technology of disposing scheelite requires a high alkaline, high temperature and high pressure leaching technology to achieve a better decomposition rate. At the same time the leachate contains a lot of alkali salts and the impurity ions. So a large amount of industrial waste water containing salt was produced. Therefore, it is imperative to improve the existing production process.
This article introduced a novel process to separate tungsten from gangue material to produce sodium tungstate with high purity, in which the sheelite was used as feed and the flowsheet was dry ball milling activation一roasting一high temperature smelting with slag former adding. The main research work included directly high temperature smelting and ball milling activation一roasting一high temperature smelting. The experimental methods can be divided into three steps in total:
2. The research of soda roasting of sheelite. The results showed that under the conditions: roasting temperature was 595℃,reaction time was 2 hour, alkali additive amount was 2.3 times of theory stiochemistry consumption, the sheelite decomposition ratio reached 93.79%. Adding quartz had a negative effect on decomposition.
3. The high temperature smelting. Without adding of slag formers, the smelting results showed that the separation of sodium tungstate and slag was very difficult only by increasing smelting temperature(from 1100℃to1500℃). With adding of slag formers, the results showed that the decrease of Ca0 ratio in slag former and the increase of temperature could improve the property of slag and effectively separate slag and sodium tungstate. The addition of sodium floride can not obviously improve the srnelting property.
Melting temperature of scheelite decomposition Melting time of scheelite decomposition
In conclusion, the process of dry ball milling activation一roasting一high temperature smelting with slag former adding, not only effectively decompose scheelite (the decomposition ratio was above 98%), but also produce sodium tungstate with high purity through effective separation of tungsten from gangue. T'he purity of sodium tungstate (include sodium molybdate) was above 94%. Molybdenum cannot be separated from tungsten in decomposition and smelting. The residue can be reused for roasting and smelting.
Sodium Tungstate Supplier: Chinatungsten sodium-tungstate.com | Tel.: 86 592 5129696; Fax: 86 592 5129797;Email:sales@chinatungsten.com |
Tungsten News & Prices, 3G Version: http://3g.chinatungsten.com | Molybdenum News & Molybdenum Price: http://news.molybdenum.com.cn |
Sodium Tungstate Application
- Details
- Category: Tungsten Information
- Published on Tuesday, 29 December 2015 09:01
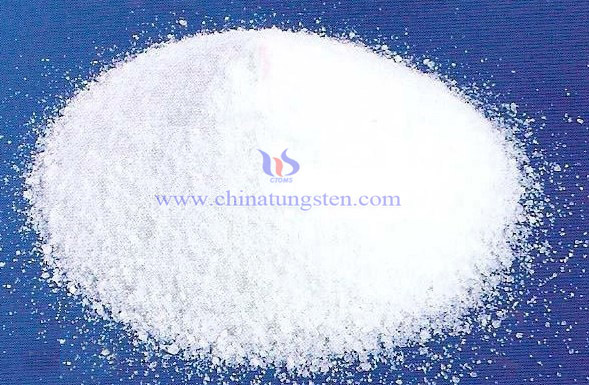
Sodium Tungstate Supplier: Chinatungsten sodium-tungstate.com | Tel.: 86 592 5129696; Fax: 86 592 5129797;Email:sales@chinatungsten.com |
Tungsten News & Prices, 3G Version: http://3g.chinatungsten.com | Molybdenum News & Molybdenum Price: http://news.molybdenum.com.cn |
Sodium Tungstate Solution Eliminating Chromium Method
- Details
- Category: Tungsten Information
- Published on Monday, 28 December 2015 19:56
Sodium Tungstate Supplier: Chinatungsten sodium-tungstate.com | Tel.: 86 592 5129696; Fax: 86 592 5129797;Email:sales@chinatungsten.com |
Tungsten News & Prices, 3G Version: http://3g.chinatungsten.com | Molybdenum News & Molybdenum Price: http://news.molybdenum.com.cn |