Coated Cemented Carbide Process III
- Details
- Category: Tungsten Information
- Published on Monday, 04 January 2016 17:20
Based on traditional chemical vapor deposition (CVD) and physical vapor deposition (PVD), some new coating technologies are emerging.
5. Plasma Chemical Vapor Deposition (PCVD)
Plasma Chemical Vapor Deposition (PCVD) uses the kinetic energy of charged particles of plasma to inspire the vapor chemical reaction. The basic principle is that deposited a film with high hardness and high wear resistance on the surface of metal matrix, such as titanium nitride (TiN), TiAlN, TiCN, TiSiN hard film and so on. Different from traditional chemical vapor deposition (CVD), PCVD has lower deposited temperature (about 500-600℃), which reduces the deposition directionality and makes the coating uniform. At present, the coating temperature of latest PACVD decreases to 180-200℃, the welding properties is much better and the welding place is no affected, which is suitable for welding-used tungsten carbide cutting tools and the surface hardening process of mold. The experimental data shows that compared with common high-speed steel drills, tungsten carbide drill by PCVD has higher efficiency, better comprehensive properties (wear resistance and corrosion resistance) and the service life extended about 10 times in the process of steel machining.
6. Vacuum Cathodic Arc Deposition (VCAD)
Vacuum Cathodic Arc Deposition (VCAD) is a kind of process that uses cathodic arc to evaporate and disassociate the target and deposited under negative bias voltages, which has many advantages, such as lower deposition temperature, higher deposition rate, larger covered acreage deposition, high ion energy, high ionization rate, good binding force between the film and the matrix, simple operation and simple equipments, etc. It can be widely used in TiN, TiC and some super-hard film deposited.
Some researcher study that based on the original process of vacuum cathodic arc deposition TiN film, uses titanium aluminum to take place of titanium target for deposited the (Ti, Al)N film with excellent properties, which is beneficial for pushing forward (Ti, Al)N film industrialized producing. Except applied in some metal film with high quality, VCAD is also suitable for Ta-C, optical film, transparent conductive oxide film, nitride multi-layers, nano composite film, MAX phase and some various film deposited.
Tungsten Carbide Supplier: Chinatungsten Online tungsten-carbide.com.cn | Tel.: 86 592 5129696; Fax: 86 592 5129797;Email:sales@chinatungsten.com |
Tungsten News&Tungsten Prices, 3G Version: http://3g.chinatungsten.com | Molybdenum News & Molybdenum Price: http://news.molybdenum.com.cn |
Wolframite Species
- Details
- Category: Tungsten Information
- Published on Monday, 04 January 2016 17:06
Huebnerite:
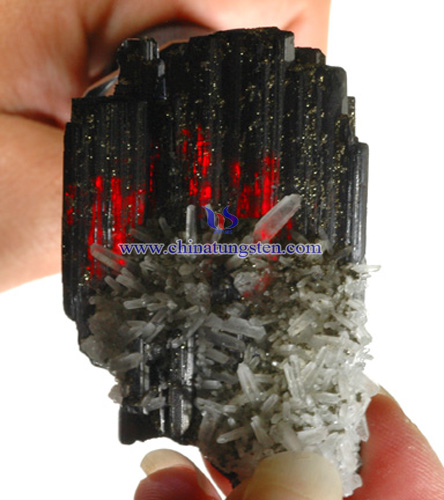
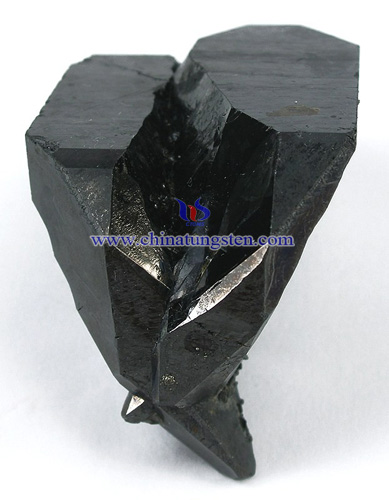
Tungsten Supplier: Chinatungsten Online www.chinatungsten.com | Tel.: 86 592 5129696; Fax: 86 592 5129797;Email:sales@chinatungsten.com |
Tungsten News & Prices, 3G Version: http://3g.chinatungsten.com | Molybdenum News & Molybdenum Price: http://news.molybdenum.com.cn |
Tungsten Mineral Species
- Details
- Category: Tungsten Information
- Published on Monday, 04 January 2016 16:50
Minerals |
Huebnerite |
Wolframite |
Ferberite |
Scheelite |
Formula |
MnWO4 |
(FeMn)WO4 |
FeWO4 |
CaWO4 |
WO3 % |
76.5 |
76.6 |
76.3 |
80.6 |
Crystal System |
monoclinic |
monoclinic |
monoclinic |
square |
Cleavage |
Along the oblique plane |
Along the oblique plane |
Along the oblique plane |
Parallel to the cone |
Mohs Hardness |
5-5.5 |
5-5.5 |
4-4.5 |
4.5-5 |
Density |
7.2-7.5 |
7.1-7.5 |
6.8 |
5.9-6.2 |
Magnetism |
weak |
weak |
weak |
no |
Tungsten Supplier: Chinatungsten Online www.chinatungsten.com | Tel.: 86 592 5129696; Fax: 86 592 5129797;Email:sales@chinatungsten.com |
Tungsten News & Prices, 3G Version: http://3g.chinatungsten.com | Molybdenum News & Molybdenum Price: http://news.molybdenum.com.cn |
The Main Problems of China Tungsten Industry Development (2)
- Details
- Category: Tungsten Information
- Published on Monday, 04 January 2016 15:46
The main problems of China tungsten industry are excess production capacity, striking industrial structural contradictions, scarce R&D ability of high-grade products and input-output ratio of resource is not high. Besides, production cost increase, low international competitiveness, during industry development imbalance, discordant and unsustainable deep-rooted problems and constrictions are more prominence. What’s more, the consciousness of environment protection has enhanced, so China tungsten industry have to change traditional development patterns which depends on consume resources, increase production and sacrifice environment so that China tungsten industry can not only follow international tungsten industry development pace but also can develop better. As below I will more specifically introduce the main problems of China tungsten industry development.
1. Low-level redundant development, acute overloads production contradiction
According to statistic, in the end of 2014, China produced ammonium paratungstate 214,000.00 ton, tungsten powder 762,000.00 ton, tungsten cemented carbide 411,000.00 ton, tungsten wire 35 billion meter, and ferro tungsten 30,000.00 ton on the other hand, the rate of capacity utilization is 41.1%, 49.87%, 63.75%, 63.75%, 45.14% and 19.00% respectively.
2. Low industry contraction, development quality and benefit
China has lot of tungsten companies, but they are scattered, small and weak and this situation is not fundamental change. Besides, industry contraction is low and international competitiveness is not high. According to statistic, in 2013, 193 tungsten companies annual average production was less than 500 ton. Only 21 tungsten company annual production was higher than 1000 ton accounts for 50.28% of production. In 2014, only 3 tungsten companies produce more than 1,000.00 ton cemented carbide accounted for 45.7% of production. And the sales revenue of tungsten cemented carbide was 22 billion RMB and benefit was less than 1 billion RMB.
Tungsten Supplier: Chinatungsten Online www.chinatungsten.com | Tel.: 86 592 5129696; Fax: 86 592 5129797;Email:sales@chinatungsten.com |
Tungsten News & Prices, 3G Version: http://3g.chinatungsten.com | Molybdenum News & Molybdenum Price: http://news.molybdenum.com.cn |
The Main Problems of China Tungsten Industry Development (1)
- Details
- Category: Tungsten Information
- Published on Monday, 04 January 2016 15:43
China has abundant tungsten ore resources. After experienced early period unauthorized mining China government has employed a series of policy to promote tungsten industry development so that China tungsten industry has entered a phase of steady development. At the present, due to deteriorating global economic situation, China and international tungsten industry situation is not optimistic. To understanding the main problem which has occurred during China tungsten industry development process is very important for tungsten industry development.
1. Intensive mining, tungsten ore reserve-production ratio imbalance
Tungsten is an important strategic resource. However, China tungsten total reserve amount ratio accounts for less than 50% of global tungsten total reserve amount, but China has provided 80% global tungsten consumption. What’s more, China reserve-production ratio is less than one fourth with oversea reserve-production. According to the data China tungsten resource has small range increase, but the basic reserve has obviously declined. The tungsten resources superiority of China has been reduce and resource security situation is not optimistic.
2. Lacking independent innovation ability, low technology, content and low added value of products
Comparing with global tungsten industry, China tungsten industry is in the mid-range of global tungsten industry chain. There are great gap between China tungsten industry and advanced international tungsten industry. For example, digital, automation and intelligentize production process, enterprise management informatization, product specialization, scientific and technical innovation integration, market and talents globalization is low-level. Besides, taking company as main part, the scientific and technical innovation mechanism which combines with production, research, study and application is not quite complete. What’s more, research and development spending is less and also lack of high-end technical personnel so R&D ability is weak. What’s more, tungsten industry advanced technology of deep-processing and key areas have little major breakthroughs and originality alloying technique outcome also low. The products of tungsten are mainly mid-low-end which can’t meet China domestic high-end manufacturing’s requirements, so high quality, high precise and high-grade cemented carbide digital cuttings and other high technological content, high added valued tungsten products need to import from oversea.
Tungsten Supplier: Chinatungsten Online www.chinatungsten.com | Tel.: 86 592 5129696; Fax: 86 592 5129797;Email:sales@chinatungsten.com |
Tungsten News & Prices, 3G Version: http://3g.chinatungsten.com | Molybdenum News & Molybdenum Price: http://news.molybdenum.com.cn |
Tungsten Trioxide Hydrogen Reduction Factors
- Details
- Category: Tungsten Information
- Published on Monday, 04 January 2016 15:19
The gas-solid multiphase reaction of Hydrogen (H2) reduction of tungsten trioxide (WO3) is:
WO3+3H2 ===W+3H2O
Reduction Temperature
Volatile tungsten oxide increases with increasing temperature, the higher the reduction temperature, the more water vapor can promote the formation of tungsten oxide and volatile hydrate WOx • nH2O and restored good and cheap tungsten powder particles of tungsten oxide surface that is reduced, which leaving the primary particles grow thick. Since WO3 greater volatility than the WO2, therefore, the production of fine particles of tungsten powder requires the use of a lower reduction temperature. Generally speaking, we use two-stage reduction, the first reduction (WO3 - WO2) should be adopted a lower reduction temperature, while the second reduction (WO2 - W) used a high temperature reduction. Production of coarse particles of tungsten powder is used for some high-temperature reduction (direct reduction) method.
Hydrogen Humidity and Flow
Effect of humidity on hydrogen tungsten powder particle size is very significant. Hydrogen humidity, which is conducive to the formation of tungsten oxide and water vapor volatile hydrates and restored good tungsten powder and tungsten oxide surfaces, resulting in tungsten powder particles grow. In favor of increasing the hydrogen flow rate of water vapor reduction product discharged in time, it increases the reduction reaction speeds, it is easy to obtain fine particles of tungsten powder.
Boat Loading Capacity (Material Thickness)
More than the amount loaded boat or material layer is too thick, hydrogen is difficult to penetrate deep inside the material layer. The inner layer of tungsten oxide reduction is not complete, the steam generated is also difficult to discharge, causing the boat long thick inner layer of tungsten powder, and obtained tungsten powder particle size is uneven.
Push the Boat Speed
Push the boat speed, reducing short time. Tungsten trioxide will not enter the high-temperature region in stepwise reduction of chance to low temperature materials, which resulting in growth and high oxygen content of the tungsten powder. Pushing the boat speed is too slow, tungsten trioxide residence time in the high temperature zone too long; it is easy to grow thick and decreases productivity for tungsten powder.
Temperature Gradient
Large temperature gradient furnace is equivalent to push the boat too fast, which can lead to volatile metal tungsten oxide particles grow.
WO3 Original Size and Impurity
When the reduction process was controlled by hydrogen reduction of fine particulate WO3 generally get fine particles of tungsten powder; but since the surface of the fine particles of WO3 can be high, you may get coarser tungsten powder if reducing improper process control. WO3material containing metal sodium impurities, which will lead to more long thick tungsten powder; molybdenum or chromium and other impurities can inhibit the role of long thick tungsten powder.
Tungsten Oxide Supplier: Chinatungsten Online www.tungsten-oxide.com | Tel.: 86 592 5129696; Fax: 86 592 5129797;Email:sales@chinatungsten.com |
Tungsten News & Prices, 3G Version: http://3g.chinatungsten.com | Molybdenum News & Molybdenum Price: http://news.molybdenum.com.cn |
Tungsten Trioxide Coulomb Titration Sulfur Effect
- Details
- Category: Tungsten Information
- Published on Monday, 04 January 2016 15:01
When tungsten trioxide in Coulomb titration burning sulfur, the organic sulfur can all break down at 800 ℃ ~ 900 ℃,while the sulphate sulfur requires to decompose at 1100 ℃ ~ 1200 ℃, so in order to ensure that coal various forms of sulfur can all decompose, there must be a higher oven temperature, on the other hand, SO2 + O2 = SO3-Q, between sulfur dioxide and sulfur trioxide in the presence of oxygen and heated environment, which is a reversible reaction, while trioxide sulfur does not participate in the reaction in the Coulomb titration process, which cause low determination conclusion .
We can see from the formula of sulfur dioxide and sulfur trioxide, this reaction is an exothermic reaction, the temperature rises will move toward the production of sulfur dioxide, so we should make the direction of the reaction to the reaction of sulfur dioxide and oxygen as far as possible In order to get accurate measurement results. The measurement results can be more accurate by the above two factors that are raising the temperature, but the temperature is too high will shorten the life of the combustion tube, thus, we have to reduce the combustion temperature, but must ensure that the sulfates completely decomposes at a lower temperature, so we cover a layer of catalyst on the coal.
Tungsten Trioxide and Coal Principle During Combustion:
The catalyst is able to significantly change the reaction rate and the material, the chemical reaction itself, the chemical nature and quantity can be changed or not is according to the change of free energy, it can not determine the reaction occurs only according to the change of free energy, because chemical reaction also depends on the reaction energy barrier, that is, if the reaction energy barrier is high, we must provide the energy to fly over the energy barrier, the energy barrier known as the activation energy after completing the reaction, and the role of the catalyst is to reduce the activation of this reaction You can make it happen chemical reaction at relatively harsh environments.
The catalyst changes the reaction rate, which is due to changes in the reaction pathway, as the picture shows, by the reaction path requires a higher energy barrier is needed to change over the reaction pathway of low energy barrier, reducing the activation energy of the reaction. Tungsten trioxide plays a role of enabling sulphate complete decomposition in coal combustion process at a low temperature, which guarantees accurate measurement results.
Tungsten Oxide Supplier: Chinatungsten Online www.tungsten-oxide.com | Tel.: 86 592 5129696; Fax: 86 592 5129797;Email:sales@chinatungsten.com |
Tungsten News & Prices, 3G Version: http://3g.chinatungsten.com | Molybdenum News & Molybdenum Price: http://news.molybdenum.com.cn |
Sodium Tungstate and SDBS Synergistic Inhibition Effect
- Details
- Category: Tungsten Information
- Published on Thursday, 31 December 2015 18:40
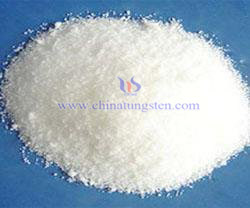
Sodium Tungstate Supplier: Chinatungsten sodium-tungstate.com | Tel.: 86 592 5129696; Fax: 86 592 5129797;Email:sales@chinatungsten.com |
Tungsten News & Prices, 3G Version: http://3g.chinatungsten.com | Molybdenum News & Molybdenum Price: http://news.molybdenum.com.cn |
Sodium Tungstate Catalyzes Cyclohexanone to Synthesize Adipic Acid
- Details
- Category: Tungsten Information
- Published on Thursday, 31 December 2015 18:28
Sodium Tungstate Supplier: Chinatungsten sodium-tungstate.com | Tel.: 86 592 5129696; Fax: 86 592 5129797;Email:sales@chinatungsten.com |
Tungsten News & Prices, 3G Version: http://3g.chinatungsten.com | Molybdenum News & Molybdenum Price: http://news.molybdenum.com.cn |
Sodium Tungstate Preparing Pyrochlore Type Tungsten Oxide
- Details
- Category: Tungsten Information
- Published on Thursday, 31 December 2015 18:26
Sodium Tungstate Supplier: Chinatungsten sodium-tungstate.com | Tel.: 86 592 5129696; Fax: 86 592 5129797;Email:sales@chinatungsten.com |
Tungsten News & Prices, 3G Version: http://3g.chinatungsten.com | Molybdenum News & Molybdenum Price: http://news.molybdenum.com.cn |