Monoclinic Tungsten Trioxide Effect on Gas Sensing
- Details
- Category: Tungsten Information
- Published on Wednesday, 06 January 2016 17:22
Monoclinic tungsten trioxide prepared by nanometer tungsten trioxide through hydrothermal method and calcination treatment, which is characterized by higher non-symmetry axis and the second symmetry axis, the symmetry plane is more than one. Monoclinic tungsten trioxide has a strong heterogeneity, which has three principal refractive index.
Taking Na2WO4• 2H2O as raw materials, DL- malic acid as supplement aid, in this context, which can be synthesized in a three-dimensional spherical shape containing precursor (WO3 • xH2O). It shows that the addition of malic acid dose of WO3 • xH2O morphology and crystalline phase having a significant impact. Thus gas test shows that the optimum operating temperature of three samples reaches to 250 ℃, and square-shaped monoclinic tungsten trioxide shows the highest sensitivity, which mainly due to its unique and innovative three-dimensional porous structure. At 300 ℃ optimum operating temperature is the lowest detectable concentration of material, which can reach 0.1ppm, material optimum calcination temperature is determined as 500 ℃,the sensitivity of 5ppm acetone sample gas reaches to 7.9; at 95% relative humidity conditions , the sensitivity of 5ppm acetone resistance remains 5.72.
In tests of different gases (such as acetone, methanol, ethanol, ammonia, etc.) in the gas sensing of different working conditions, monoclinic tungsten trioxide gas shows high selectivity and sensitivity. Taking Na2WO4 • 2H2O as raw materials, which are used by Na2C2O4, Na2SO4 and H2C2O4 supplement. The hydrothermal conditions is 24 hours, at 180 ℃. Experimental results show that the solution plays the role in Na +, SO42-, C2O42-, HC2O4- ions and H2C2O4 nano WO3 crystal nucleation and growth process. The results show that three different adjuvants does not effect on crystal of product system. Subsequent tests show Na2C2O3 assisting synthesis of WO3nanorods at 320 ℃ for certain concentrations to gas sensing, which mainly due to its high degree of dispersion and crystallinity.
Tungsten Oxide Supplier: Chinatungsten Online www.tungsten-oxide.com | Tel.: 86 592 5129696; Fax: 86 592 5129797;Email:sales@chinatungsten.com |
Tungsten News & Prices, 3G Version: http://3g.chinatungsten.com | Molybdenum News & Molybdenum Price: http://news.molybdenum.com.cn |
Effect of Powder Property on Tungsten Copper Electrode Density
- Details
- Category: Tungsten Information
- Published on Wednesday, 06 January 2016 17:17
The smaller the particle size, the greater its surface area can be sintered density, the greater the driving force, and therefore tungsten, copper particles smaller particle size will make tungsten copper alloy electrode denser, and particle size on the material the microstructure also has a certain influence. Tungsten copper contact SEM image as follow:
Figure (a) above is the microstructure of our self-developed W-Cu electrode copper tungsten contact material, and (b) of the microstructure of foreign tungsten copper W-Cu electrode contact material. There is an obvious difference between them. W particles of tungsten copper electrode contacts abroad dispersed evenly, distributed copper Cu substrate gap in the tungsten W skeleton and both of two metals has good wettability; the W particles of tungsten copper electrode contact domestic are more coarse and distributed unevenly. Therefore, the difference of contact material is related to the granularity of tungsten powder and the granularity of tungsten powder has a remarkable influence on the properties of tungsten copper alloy. The related experiment shows that with the decreasing granularity of tungsten powder, the corrosion rate decreases. If the granularity of tungsten powder is too fine, the particles will aggregate to block out the path of tungsten skeleton, which leads to insufficient infiltration, macro-segregation, porosity, Cu-concentration and other defects.
Tungsten Copper Supplier: Chinatungsten Online tungsten-copper.com | Tel.: 86 592 5129696; Fax: 86 592 5129797;Email:sales@chinatungsten.com |
Tungsten News & Prices, 3G Version: http://3g.chinatungsten.com | Molybdenum News & Molybdenum Price: http://news.molybdenum.com.cn |
Coated Cemented Carbide Types——Multi-layer Coating
- Details
- Category: Tungsten Information
- Published on Wednesday, 06 January 2016 17:15
Since coated cemented carbide developed, coating types were diverse, such as single-layer coating, multi-element composite coating, gradient coating, nano coating, super-hard coating and soft coating.
2. Multi-layer Coating
With the development of coated cemented carbide technology, single-layer coating has a transition to multi-layer coating with excellent properties. Multi-layer coating combines with excellent properties and applicability of different materials, which improves the comprehensive properties of the matrix further. At present, the major double-layer coating has titanium carbide/titanium nitride (TiC/TiN), titanium carbide/aluminum oxide (TiC/Al2O3), titanium carbide nitride/aluminum oxide (Ti(C,N)/Al2O3), titanium nitride/cubic boron nitride (TiN/CBN) and so on. TiC/Al2O3 coating is the earliest and the most widely used, which compared with single-layer TiC has higher hardness and better wear resistance, and the TiN has excellent chemical stability (in case of the diffusion) and crater wear resistance. In addition, TiC has closer coefficient of thermal expansion to the matrix than TiN, which usually used in the basic coat and has better binding force with the matrix. Its internal residual stress is small so that it can effectively resist the cracks expanding. Generally, TiC/TiN coated cemented carbide cutting tools is more suitable for machining, semi-finishing and precise cutting; TiC/Al2O3 coated cemented carbide has higher heat hardness and toughness, which is suitable for high-speed cutting or high-load cutting.
The common coating with three layers is TiC / Ti (C, N) / TiN, by austenitic stainless steel turning experiments some researchers find that due to TiN coating has small friction factor and has small cutting force, which is suitable for semi-finishing and precise cutting. Besides, TiN/TiC/TiN composite coating has better wear resistance, binding force with the matrix, thermal shock resistance than single-layer coating, which can be widely used in alloy steel, structural steel and high-speed milling. In a word, the more coating layer, the more advantages in high-speed cutting and milling, and with the development of technology, the coating layer become thinner. Multi-layer coating on the physical structure, mechanical properties and chemical properties of the material aspects of carbide cutting tools gives more excellent transition, is the prototype of functionally gradient materials.
Tungsten Carbide Supplier: Chinatungsten Online tungsten-carbide.com.cn | Tel.: 86 592 5129696; Fax: 86 592 5129797;Email:sales@chinatungsten.com |
Tungsten News&Tungsten Prices, 3G Version: http://3g.chinatungsten.com | Molybdenum News & Molybdenum Price: http://news.molybdenum.com.cn |
Tungsten Alloy Balance Wheel Screw CounterweightsⅡ
- Details
- Category: Tungsten Information
- Published on Wednesday, 06 January 2016 15:48
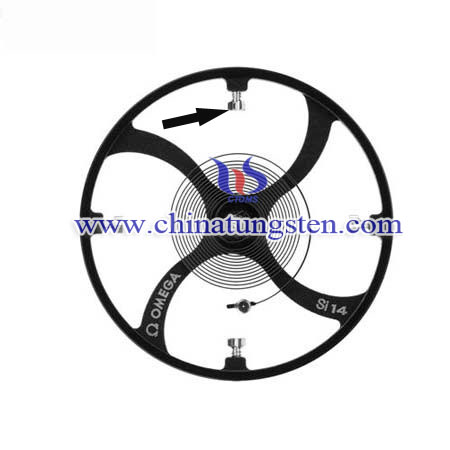
Tungsten Alloy Supplier: Chinatungsten Online www.tungsten-alloy.com | Tel.: 86 592 5129696; Fax: 86 592 5129797;Email:sales@chinatungsten.com |
Tungsten News & Prices, 3G Version: http://3g.chinatungsten.com | Molybdenum News & Molybdenum Price: http://news.molybdenum.com.cn |
Tungsten Alloy Plasma Accelerator Shielding
- Details
- Category: Tungsten Information
- Published on Wednesday, 06 January 2016 15:45
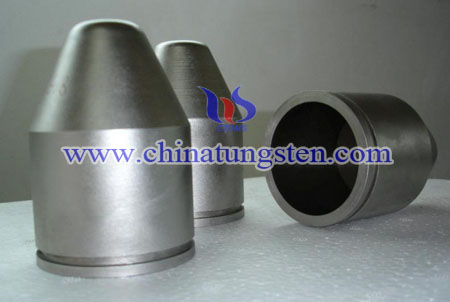
Tungsten Alloy Supplier: Chinatungsten Online www.tungsten-alloy.com | Tel.: 86 592 5129696; Fax: 86 592 5129797;Email:sales@chinatungsten.com |
Tungsten News & Prices, 3G Version: http://3g.chinatungsten.com | Molybdenum News & Molybdenum Price: http://news.molybdenum.com.cn |
APT Quote is Rising and Imports Declines
- Details
- Category: Tungsten Information
- Published on Wednesday, 06 January 2016 15:27
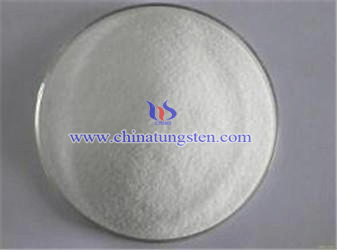
APT Supplier: Chinatungsten Online www.ammonium-paratungstate.com | Tel.: 86 592 5129696; Fax: 86 592 5129797;Email:sales@chinatungsten.com |
Tungsten News&Tungsten Prices, 3G Version: http://3g.chinatungsten.com | Molybdenum News & Molybdenum Price: http://news.molybdenum.com.cn |
Sodium Metatungstate Application in Geology Field
- Details
- Category: Tungsten Information
- Published on Wednesday, 06 January 2016 08:54
Sodium Tungstate Supplier: Chinatungsten sodium-tungstate.com | Tel.: 86 592 5129696; Fax: 86 592 5129797;Email:sales@chinatungsten.com |
Tungsten News & Prices, 3G Version: http://3g.chinatungsten.com | Molybdenum News & Molybdenum Price: http://news.molybdenum.com.cn |
Sodium Polytungstate Separating-Purifying Zeolite
- Details
- Category: Tungsten Information
- Published on Wednesday, 06 January 2016 08:48
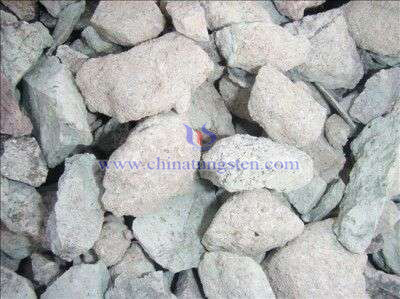
Sodium Tungstate Supplier: Chinatungsten sodium-tungstate.com | Tel.: 86 592 5129696; Fax: 86 592 5129797;Email:sales@chinatungsten.com |
Tungsten News & Prices, 3G Version: http://3g.chinatungsten.com | Molybdenum News & Molybdenum Price: http://news.molybdenum.com.cn |
Sodium Polytungstate Solution Preparation
- Details
- Category: Tungsten Information
- Published on Wednesday, 06 January 2016 08:45
Sodium Tungstate Supplier: Chinatungsten sodium-tungstate.com | Tel.: 86 592 5129696; Fax: 86 592 5129797;Email:sales@chinatungsten.com |
Tungsten News & Prices, 3G Version: http://3g.chinatungsten.com | Molybdenum News & Molybdenum Price: http://news.molybdenum.com.cn |
Behavior of Tin in Producing Ammonium Paratungstate 1/3
- Details
- Category: Tungsten Information
- Published on Tuesday, 05 January 2016 19:48
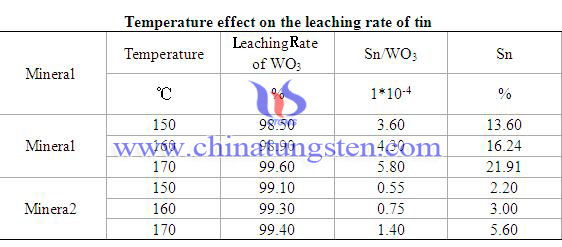
APT Supplier: Chinatungsten Online ammonium-paratungstate.com | Tel.: 86 592 5129696; Fax: 86 592 5129797;Email:sales@chinatungsten.com |
Tungsten News&Tungsten Prices, 3G Version: http://3g.chinatungsten.com | Molybdenum News & Molybdenum Price: http://news.molybdenum.com.cn |