Tungsten Powder Made from Ammonium Paratungstate—One-step Reduction Method 3/3
- Details
- Category: Tungsten Information
- Published on Tuesday, 05 January 2016 19:40
First one, also the majority one is water removed from APT in the process crystallization;
The second one takes a small part, water comes from the reduction of WO3 to blue tungsten oxide and violet tungsten oxide. Generally believed that the crystal rifted after dehydration and deamination which will help hydrogen enter the crystal, thus help the reduction of tungsten powder.
First, temperature, hydrogen in the high volatility and temperature helps to produce coarse grain tungsten powder of complete crystal forms and uniform and dispersed.
Second, reduction time, effect on the size of tungsten powder, tungsten powder has a trend of growing up with the increasing hydrogen reduction time goes.
Third, shipping amount, the big boat loading cause depth of material becoming thicker, and then do harm to tungsten oxide and water vapor to diffusion and crystal growth in the reduction process. So, reduce the amount of shipping will help producing tungsten powder with uniform size.
APT Supplier: Chinatungsten Online ammonium-paratungstate.com | Tel.: 86 592 5129696; Fax: 86 592 5129797;Email:sales@chinatungsten.com |
Tungsten News&Tungsten Prices, 3G Version: http://3g.chinatungsten.com | Molybdenum News & Molybdenum Price: http://news.molybdenum.com.cn |
High Polymer Tungsten Trioxide Preparation
- Details
- Category: Tungsten Information
- Published on Tuesday, 05 January 2016 18:05
Preparation of High Polymer Tungsten Trioxide
Preparing various samples at different sintering temperatures after the samples were prepared, than measuring different sets of samples according to voltammetry, impedance spectroscopy and dielectric spectroscopy curves. We can obtain micron tungsten trioxide nonlinear coefficient polymer composite samples by calculating the nonlinear coefficients of main sample by measured data. In the composite sample, the tungsten trioxide particles in the sample content has higher nonlinear coefficients, and the nonlinear coefficient of the sintered samples 250 ℃ sintering temperature is higher than the other samples, up to 98. When the organic matter content is higher than 80%, the sample becomes an insulator, the prepared tungsten trioxide polymer material is more stable.
Sample Analysis
The experimental methods commonly based on varistor methods, and calculating barrier trends, comparing barrier with nonlinear coefficient, typical sample made six-phase morphology and structural analysis, and comparing good and bad samples nonlinear function of the body as well as micro particles and nanoparticles composite sample, which shows the trends of barrier are consistent with nonlinear coefficients.
Test results of morphology and electrical properties show that high resistance nonlinear crystal polymer material with an applied electric field tungsten trioxide samples resulting shift toward low-resistance crystalline phase, and it has a close relationship. The result of nonlinear preferred groups of typical sample with impedance spectroscopy show bias under the grain boundary resistance is not changed significantly Resistance is low because of its low resistance phase structure mainly monoclinic.
Tungsten Oxide Supplier: Chinatungsten Online www.tungsten-oxide.com | Tel.: 86 592 5129696; Fax: 86 592 5129797;Email:sales@chinatungsten.com |
Tungsten News & Prices, 3G Version: http://3g.chinatungsten.com | Molybdenum News & Molybdenum Price: http://news.molybdenum.com.cn |
Carbon-Doped Tungsten Trioxide Exploration
- Details
- Category: Tungsten Information
- Published on Tuesday, 05 January 2016 17:54
As we all know, tungsten trioxide (WO3) is an important material and it is indispensable for us in life. It has a wide range of applications in the field of gas detection and photocatalysis. The special structures and morphology of tungsten trioxide determine their excellent performance. The preparation for the quasi one-dimensional structure of the carbon-doped tungsten trioxide nanofibers (C-dopedWO3) is based on template method as template, to explore the performance of carbon-doped tungsten trioxide Absorbent template method as a template prepared to quasi one-dimensional structure of the carbon-doped WO3 nanofibers (C-dopedWO3), which can improve the gas sensing performance and photocatalytic properties of the material.
the systematically study of carbon-doped tungsten trioxide performance based on the use of XRD, TEM, SEM, HRTEM, XPS, Raman spectra and other research samples by means of the analysis, which can find that there are the material selectivity and stability with acetone, and Methylene Blue as model pollutants investigats the photocatalytic activity of the material.
Exploration results are as follows:
(1) The carbon-doped WO3 monoclinic phase under template prepared, the analysis of SEM, TEM, HRTEM and other means of testing shows: WO3-500 fiber diameter with the diameter of the ultrafine nanocrystals composed about 20-40nm 5-10μm, which contains a large number of pores and a hollow structure. The grain size increases by the calcination temperature. The key peaks of C1s XPS spectra of samples of WC 282.2eV appear Raman spectra of carbon into the G-peak, etc. The results show that doped WO3lattice of carbon atoms.
(2) In the test of different condition of different gases (such as acetone, methanol, ethanol, ammonia, etc.) of gas sensing of different operating conditions, we can find carbon-doped WO3 shows high selectivity and sensitivity to acetone gas. The minimum detectable concentration of materials can reach 0.1ppm and material optimum calcination temperature is determined as 500 ℃ at 300 ℃. The WO3-500 sensitivity of 5ppm acetone sample gas reaches 7.9; at 95% relative humidity conditions, the sensitivity of 5ppm acetone resistance remains 5.72. By repeating the gas sensing tests found to have long-term stability, H2S and other toxic gases can not lead to inactivation of sensitive material.
(3) Comparing with pure WO3 contrast, the WO3-500 degradation of methylene blue catalytic activity improves significantly. Under visible light irradiation conditions, WO3-500 and H2O2 Fenton system constructes within 120min of methylene blue degradation rate reaching 97.1%. The synergies of WO3-500 and H2O2 are to enhance the degradation rate of methylene blue and degradation rate. Carbon -doped WO3 catalyst has good stability and it is easily to separate from the degradation of the system, the catalyst reuse still shows high catalytic activity.
Tungsten Oxide Supplier: Chinatungsten Online www.tungsten-oxide.com | Tel.: 86 592 5129696; Fax: 86 592 5129797;Email:sales@chinatungsten.com |
Tungsten News & Prices, 3G Version: http://3g.chinatungsten.com | Molybdenum News & Molybdenum Price: http://news.molybdenum.com.cn |
Gold-plating Process Of Tungsten Gold-plated ProductsⅡ
- Details
- Category: Tungsten Information
- Published on Tuesday, 05 January 2016 17:53
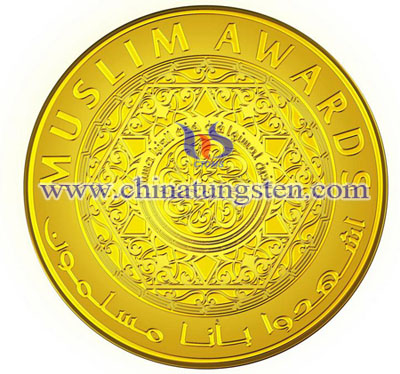
Tungsten Gold Plated Supplier: Chinatungsten Online www.tungsten-alloy.com | Tel.: 86 592 5129696; Fax: 86 592 5129797;Email:sales@chinatungsten.com |
Tungsten News & Prices, 3G Version: http://3g.chinatungsten.com | Molybdenum News & Molybdenum Price: http://news.molybdenum.com.cn |
Gold-plating Process Of Tungsten Gold-plated ProductsⅠ
- Details
- Category: Tungsten Information
- Published on Tuesday, 05 January 2016 17:50
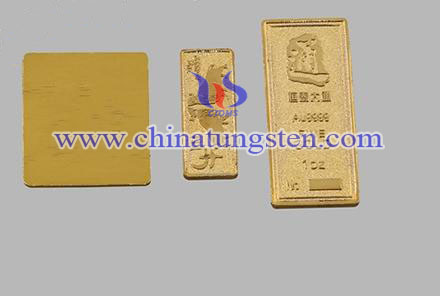
Tungsten Gold Plated Supplier: Chinatungsten Online www.tungsten-alloy.com | Tel.: 86 592 5129696; Fax: 86 592 5129797;Email:sales@chinatungsten.com |
Tungsten News & Prices, 3G Version: http://3g.chinatungsten.com | Molybdenum News & Molybdenum Price: http://news.molybdenum.com.cn |
Tungsten Trioxide Damping Function on OLED
- Details
- Category: Tungsten Information
- Published on Tuesday, 05 January 2016 17:42
The organic light-emitting diode is known as laser electroluminescent display (Organic Light-Emitting Diode, OLED). The feature of OLED display technology is self-luminous, it is made by very thin coating of organic materials and glass substrates composed of organic material which emits light when current passes through. OLED display screen viewing angle is large, with power-saving features.
DC Magnetron Sputtering Method:
When the voltage reaches 20V, the brightness of IWO-OLED (referred IWO) is 8791cd / m2, the brightness of IWO / WO3-OLED (referred IWO / WO3) is 16690cd / m2; when the voltage decreases to 19V, the maximum power efficiency IWO / WO3 devices is 1.581m / W. In contrast, for IWO device, when the current density increases, the luminous efficiency gradually increases, when the current density reaches 181.9mA / cm2, the luminous efficiency reaches a maximum of 4.83cd / A. For IWO / WO3 devices, when the voltage is 19V, luminous efficiency reaches the maximum 9.56cd / A, which is twice than that of the former. In short, in terms of the brightness of IWO / WO3-OLED, luminous efficiency and power efficiency has improved significantly.
Pulsed Plasma Deposition, PPD Method:
When the voltage reaches 20V, the brightness of IWO is 8791cd / m2, the brightness of IWO / WO3 is 17360cd / m2, its brightness is more than twice as light as the non-tungsten trioxide buffer layer devices, which shows adding to the buffer layer of tungsten trioxide indeed improving the OLED device emits light brightness. However, for the purposes of power efficiency IWO / WO3 device, it did not effectively improve because of the insertion of the tungsten trioxide. Luminous efficiency, IWO / WO3-OLED device was not as good IWO-OLED. Analysis shows, the performance of OLED device and the buffer layer are closely linked.
We analyze XRD and AFM characterization of the lattice structure of tungsten trioxide film, which can find prepared amorphous structure having a relatively flat surface. The use of tungsten trioxide films that prepared by two methods as OLED anode electrode, which has cushion work function.
Tungsten Oxide Supplier: Chinatungsten Online www.tungsten-oxide.com | Tel.: 86 592 5129696; Fax: 86 592 5129797;Email:sales@chinatungsten.com |
Tungsten News & Prices, 3G Version: http://3g.chinatungsten.com | Molybdenum News & Molybdenum Price: http://news.molybdenum.com.cn |
Tungsten Minerals: Scheelite, Tungstite, Stolzite
- Details
- Category: Tungsten Information
- Published on Tuesday, 05 January 2016 17:36
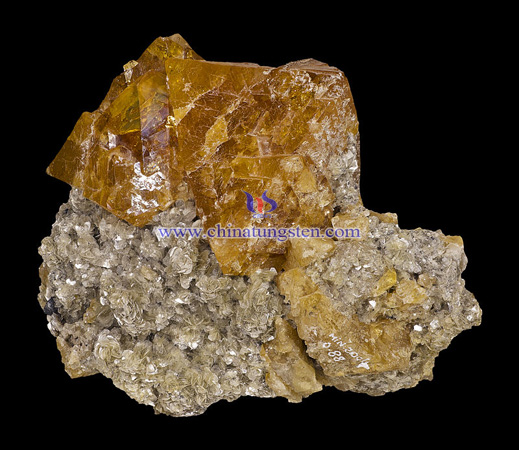
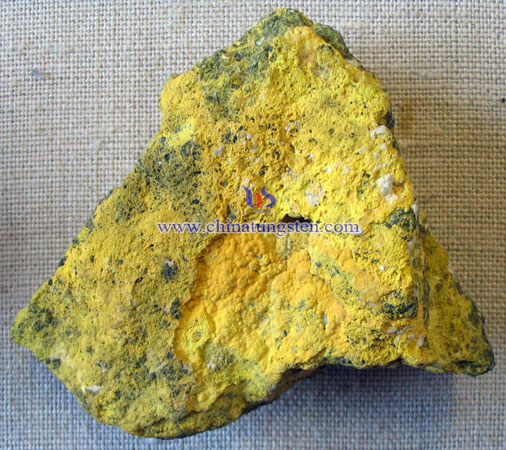
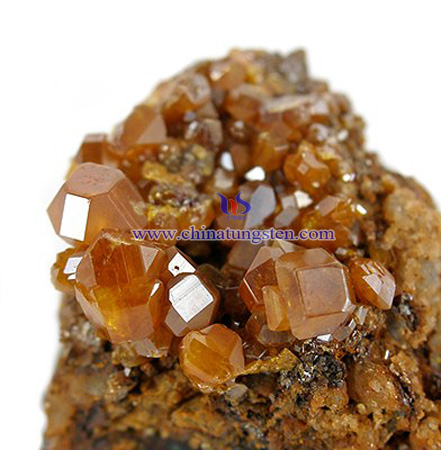
Tungsten Supplier: Chinatungsten Online www.chinatungsten.com | Tel.: 86 592 5129696; Fax: 86 592 5129797;Email:sales@chinatungsten.com |
Tungsten News & Prices, 3G Version: http://3g.chinatungsten.com | Molybdenum News & Molybdenum Price: http://news.molybdenum.com.cn |
Effect of Molding Process on Tungsten Copper Electrode
- Details
- Category: Tungsten Information
- Published on Tuesday, 05 January 2016 17:10
The research shows the ideal structure of tungsten copper composite material has higher density, tungsten particles uniformly dispersed to form a continuous skeleton, and solidified around between copper tungsten particles (including space charge sintered base of the throat gap), a continuous distribution network, and the ideal organizational structure below shows tungsten-copper composite material.
Coefficient of thermal expansion (CTE) is determined by tungsten skeleton. Copper with net structure is stable, which has high density and promote thermal conductivity (TC). Therefore, tungsten-copper composite material densification not only affect the strength of the material, but also directly or indirectly determine the number of other properties of the material, which makes critical study of the sintering process and the molding process of change. In addition, in the process of sintering, many process parameters plays an important role in the density of tungsten copper electrode, such as powder properties, the pressure, the temperature, heating/cooling rate, holding time, lubricant and so on.
Tungsten Copper Supplier: Chinatungsten Online tungsten-copper.com | Tel.: 86 592 5129696; Fax: 86 592 5129797;Email:sales@chinatungsten.com |
Tungsten News & Prices, 3G Version: http://3g.chinatungsten.com | Molybdenum News & Molybdenum Price: http://news.molybdenum.com.cn |
Coated Cemented Carbide Types——Single-layer Coating
- Details
- Category: Tungsten Information
- Published on Tuesday, 05 January 2016 17:08
Since coated cemented carbide developed, coating types were diverse, such as single-layer coating, multi-element composite coating, gradient coating, nano coating, super-hard coating and soft coating.
1. Single-layer and multi-element composite coating
At present, titanium nitride (TiN) and titanium carbide (TiC) are the earliest and the most widely used, which has high hardness, excellent wear resistance. However, it is unavoidable that a big difference of modulus of elasticity and coefficient of thermal expansion between the matrix and the coating layer, which will decrease the binding force and residual stresses between them. In order to improve the comprehensive properties of tungsten carbide, adding some different kinds of elements to form multi-element coating layer. Ti (C,N) and TiAlN are the most common composite coating. In addition, there are some other elements can remarkably improve the properties of coating cemented carbide, such as Si element will increase the hardness and in case of the chemical diffusion, Zr, B, V and Hf elements will improve the wear resistance of material, Cr element will improve antioxidant property.
Take Ti (C,N) as an example, it has both of TiC and TiN coating advantages, which used in tungsten carbide cutting tools will remarkably improve the hardness and toughness, prevent the internal cracks diffusion and the tipping of tools. For coating layer, it decreases the inner stress and improves the binding force between coating layer and matrix. According to the consequence of turning experiment, compared with single-layer coating (TiC, TiN, Al2O3), composite coating layer Ti (C,N) has better tool face wear resistance and crater wear resistance, which is more suitable for common steel, alloy steel, stainless steel and iron casting machining by tungsten carbide cutting tools and the efficiency will be remarkably improved.
TiAlN composite coating layer has heat hardness and excellent antioxidant property and can be widely used in high-speed tungsten carbide cutting tools and cermet cutting tools. It mainly uses cathodic arc ion plating – physical vapor deposition, which has uniform structure, high density, high toughness, high micro hardness (increase 35%-76%) and suitable for high-speed steel, alloy steel and other high-performance materials high-speed milling and the service life is 3-4 times than TiN single-layer coating.
Tungsten Carbide Supplier: Chinatungsten Online tungsten-carbide.com.cn | Tel.: 86 592 5129696; Fax: 86 592 5129797;Email:sales@chinatungsten.com |
Tungsten News&Tungsten Prices, 3G Version: http://3g.chinatungsten.com | Molybdenum News & Molybdenum Price: http://news.molybdenum.com.cn |
Stirring Accelerate Ammonium Paratungstate Crystallization
- Details
- Category: Tungsten Information
- Published on Monday, 04 January 2016 21:25
APT Supplier: Chinatungsten Online ammonium-paratungstate.com | Tel.: 86 592 5129696; Fax: 86 592 5129797;Email:sales@chinatungsten.com |
Tungsten News&Tungsten Prices, 3G Version: http://3g.chinatungsten.com | Molybdenum News & Molybdenum Price: http://news.molybdenum.com.cn |