Other Effects on Ammonium Paratungstate Production
- Details
- Category: Tungsten Information
- Published on Thursday, 31 December 2015 15:41
APT Supplier: Chinatungsten Online www.ammonium-paratungstate.com | Tel.: 86 592 5129696; Fax: 86 592 5129797;Email:sales@chinatungsten.com |
Tungsten News&Tungsten Prices, 3G Version: http://3g.chinatungsten.com | Molybdenum News & Molybdenum Price: http://news.molybdenum.com.cn |
Effect of Gas Stirring on Ammonium Paratungstate Production
- Details
- Category: Tungsten Information
- Published on Thursday, 31 December 2015 15:32
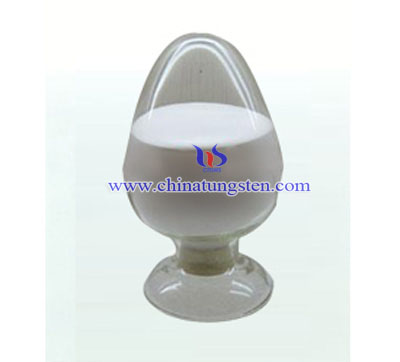
APT Supplier: Chinatungsten Online www.ammonium-paratungstate.com | Tel.: 86 592 5129696; Fax: 86 592 5129797;Email:sales@chinatungsten.com |
Tungsten News&Tungsten Prices, 3G Version: http://3g.chinatungsten.com | Molybdenum News & Molybdenum Price: http://news.molybdenum.com.cn |
China Tungsten Industry Development and Changes
- Details
- Category: Tungsten Information
- Published on Thursday, 31 December 2015 11:36
China tungsten industry started mining with unauthorized till gradually orderly management the whole tungsten industry not only annual production increase, but resource protection consciousness also enhance.
On the other hand, after employed a series of reform policy of tungsten industry there are some development and changes in China tungsten industry:
1.Tungsten price go up, economic strength growing
In 1985, China the whole tungsten industry annual sales revenue was less than 2 billion RMB. In 2003, the annual sales revenue was broken through 100 billion RMB. In 2014, annual sale revenue was 740 billion which was 44.3 times than 1985’s.
2.tungsten import and export volume decline, tungsten carbide export volume increase
During Eleventh Five-Year Plan period, tungsten annual gross production was 140,620.00 ton and export volume was 29,000.00 ton. Expected during the 12th five-year plan, the annual gross production will be 130,440.00 ton and export volume will be 26,900.00 ton comparing with 11th five-year plan the export volume of tungsten decline 8.1%
On the other hand, During Eleventh Five-Year Plan period, tungsten carbide annual gross production was 15,800.00 ton and export volume was 3,159.00 ton. Expected during the 12th five-year plan, the annual gross production will reach 24,100.00 ton and export volume will be 24,100.00 ton comparing with 11th five-year plan the export volume of tungsten carbide increase more than 50%.
3. Technology and equipped level increase rapidly
These year China tungsten industry through import, absorb and innovate technology so tungsten carbide production technology and equipped level has significant increase. For example, low-grade tungsten ore, scheelite and wolframite mixture ore extraction technology got new breakthrough. Besides, tungsten melting process and technology and products quality advanced in the world. What’s more, ultra-fine grain, ultra-rough grain, functionally graded material tungsten carbide material, super-large tungsten carbide product and other high-end tungsten carbide product has kept up with the pace of foreign countries and the tungsten series product will develop with high performance, high precision and high added value
4. Accelerating product’s structure adjustment, industrial concentration increased.
Molybdenum Supplier: Chinatungsten Online www.molybdenum.com.cn | Tel.: 86 592 5129696; Fax: 86 592 5129797;Email:sales@chinatungsten.com |
Tungsten News & Prices, 3G Version: http://3g.chinatungsten.com | Molybdenum News & Molybdenum Price: http://news.molybdenum.com.cn |
Super Saturation Affects Ammonium Paratungstate Physical Properties 1/3
- Details
- Category: Tungsten Information
- Published on Wednesday, 30 December 2015 20:18
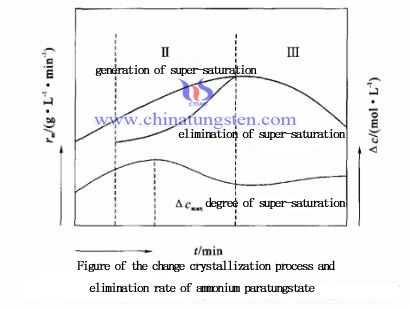
APT Supplier: Chinatungsten Online www.ammonium-metatungstate.com | Tel.: 86 592 5129696; Fax: 86 592 5129797;Email:sales@chinatungsten.com |
Tungsten News&Tungsten Prices, 3G Version: http://3g.chinatungsten.com | Molybdenum News & Molybdenum Price: http://news.molybdenum.com.cn |
Sodium Tungstate Catalyzing Diols and Nitriles Oxidation
- Details
- Category: Tungsten Information
- Published on Wednesday, 30 December 2015 20:16
Sodium Tungstate Supplier: Chinatungsten sodium-tungstate.com | Tel.: 86 592 5129696; Fax: 86 592 5129797;Email:sales@chinatungsten.com |
Tungsten News & Prices, 3G Version: http://3g.chinatungsten.com | Molybdenum News & Molybdenum Price: http://news.molybdenum.com.cn |
Ion-Exchange Kinetics in Sodium Tungstate Solution
- Details
- Category: Tungsten Information
- Published on Wednesday, 30 December 2015 20:12
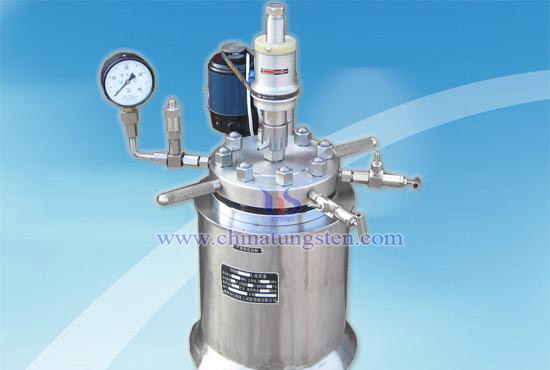
Sodium Tungstate Supplier: Chinatungsten sodium-tungstate.com | Tel.: 86 592 5129696; Fax: 86 592 5129797;Email:sales@chinatungsten.com |
Tungsten News & Prices, 3G Version: http://3g.chinatungsten.com | Molybdenum News & Molybdenum Price: http://news.molybdenum.com.cn |
Tungsten Trioxide Content Mensuration in Sodium Tungstate
- Details
- Category: Tungsten Information
- Published on Wednesday, 30 December 2015 20:10
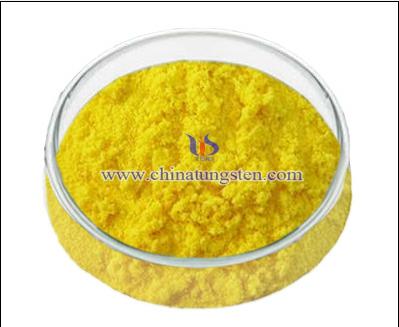
Sodium Tungstate Supplier: Chinatungsten sodium-tungstate.com | Tel.: 86 592 5129696; Fax: 86 592 5129797;Email:sales@chinatungsten.com |
Tungsten News & Prices, 3G Version: http://3g.chinatungsten.com | Molybdenum News & Molybdenum Price: http://news.molybdenum.com.cn |
Super Saturation Affects Ammonium Paratungstate Physical Properties 3/3
- Details
- Category: Tungsten Information
- Published on Wednesday, 30 December 2015 20:06
http://news.chinatungsten.com/big5/tungsten-information/81978-ti-10660
APT Supplier: Chinatungsten Online www.ammonium-metatungstate.com | Tel.: 86 592 5129696; Fax: 86 592 5129797;Email:sales@chinatungsten.com |
Tungsten News&Tungsten Prices, 3G Version: http://3g.chinatungsten.com | Molybdenum News & Molybdenum Price: http://news.molybdenum.com.cn |
Super Saturation Affects Ammonium Paratungstate Physical Properties 2/3
- Details
- Category: Tungsten Information
- Published on Wednesday, 30 December 2015 20:03
APT Supplier: Chinatungsten Online www.ammonium-metatungstate.com | Tel.: 86 592 5129696; Fax: 86 592 5129797;Email:sales@chinatungsten.com |
Tungsten News&Tungsten Prices, 3G Version: http://3g.chinatungsten.com | Molybdenum News & Molybdenum Price: http://news.molybdenum.com.cn |
China Tungsten Industry Development Situation
- Details
- Category: Tungsten Information
- Published on Wednesday, 30 December 2015 18:28
Tungsten Supplier: Chinatungsten Online www.chinatungsten.com | Tel.: 86 592 5129696; Fax: 86 592 5129797;Email:sales@chinatungsten.com |
Tungsten News & Prices, 3G Version: http://3g.chinatungsten.com | Molybdenum News & Molybdenum Price: http://news.molybdenum.com.cn |