Effect of Free Ammonia on Ammonium Paratungstate Production
- Details
- Category: Tungsten Information
- Published on Wednesday, 30 December 2015 18:22
Tungsten Supplier: Chinatungsten Online www.chinatungsten.com | Tel.: 86 592 5129696; Fax: 86 592 5129797;Email:sales@chinatungsten.com |
Tungsten News & Prices, 3G Version: http://3g.chinatungsten.com | Molybdenum News & Molybdenum Price: http://news.molybdenum.com.cn |
Effect of Additional Acid on Ammonium Paratungstate Production
- Details
- Category: Tungsten Information
- Published on Wednesday, 30 December 2015 18:09
Tungsten Supplier: Chinatungsten Online www.chinatungsten.com | Tel.: 86 592 5129696; Fax: 86 592 5129797;Email:sales@chinatungsten.com |
Tungsten News & Prices, 3G Version: http://3g.chinatungsten.com | Molybdenum News & Molybdenum Price: http://news.molybdenum.com.cn |
Testing Method of Fe Element in Sodium Tungstate 2/2
- Details
- Category: Tungsten Information
- Published on Wednesday, 30 December 2015 17:24
Another method for testing Fe element in sodium tungstate:
1.Be ready with:
(1)Ferric trichloride solution(FeCl3)
(2)Indicator : sodium diphenylamine sulfonate
(3)Potassium bichromate titrant
(4)250ml dried beaker flask
(5) Funnel inserted with filter paper and small piece of cotton(used for filtration in the later process)
2.Add 1.0g sodium tungstate sample into beaker flask, and then add 50ml FeCl3 solution, jam-pack with rubber plug, shake it fiercely for 15 minutes.
3.Suck-filter the solution from step 2 by suction flask with funnel( inserted with filter paper and small piece of cotton). The filtrate is obtained.
4.Clean the beaker flask for 4-5 times and filter the residue.
5.Adding 15ml mixed acid of sulphoric acid and phosphoric acid, and then adding water to dilute it until 100ml.
6.Adding five drops of 5g/L sodium diphenylamine sulfonate, titrate by potassium bichromate titrant until it turns into bluish violet.
7.Fe content is calculated by : Fe0(%)=VfFe0/m x 100
Among which: fFe0 —— quantity of metal ferric calculated by gram which equals to 1ml potassium bichromate titrant.
V——volume of consumed potassium bichromate titrant during titration.
m——quantity of sodium tungstate sample.
Tungsten Oxide Supplier: Chinatungsten Online www.tungsten-oxide.com | Tel.: 86 592 5129696; Fax: 86 592 5129797;Email:sales@chinatungsten.com |
Tungsten News & Prices, 3G Version: http://3g.chinatungsten.com | Molybdenum News & Molybdenum Price: http://news.molybdenum.com.cn |
Testing Method of Fe Element in Sodium Tungstate 1/2
- Details
- Category: Tungsten Information
- Published on Wednesday, 30 December 2015 17:21
(Note: the water referred following is single-distilled water, the reagent is secondary purity.)
1.Be ready with:
(1)Hydrochloric acid 1:1
(2)Ammonia hydroxide 1:1
(3)50% Citric acid aqueous solution
(4)10% Ethylene Diamine Tetraacetic Acid(EDTA) solution
(5)10% Hydroxylamine hydrochloride solution
(6)Buffer solution(PH:7-8): Mix 25ml 0.2M KH2PO4(13.61g soluble in 500ml water) and 46.1ml 0.1M NaOH, dilute to 100ml, adjust PH value by PH meter.
(7)0.2% Phenanthroline monohydrate solution: Dissolve 1.0g phenanthroline monohydrate in 500ml water(PH:7-8)
(8)Sodium tungstate solution: Adding 14.23g Na2WO4 into beaker with 50ml water, drop in 6N NaoH, after Na2WO4 dissolved completely, move the solution into 100ml volumetric flask, shake it up, WO3 concentration of solution is 100mg/ml.
(9)Fe standard solution: Put 1.0g pure ferric wire into 250ml beaker, add 50ml 1:1 hydrochloric acid, heat it until it dissolve completely, move to 100 ml volumetric flask. Dilute with water to 100ml. The current Fe=1mg/ml. Then dilute the solution into Fe=10ug/ml.
(10)PHs—2 acidimeter; 721 ultraviolet spectrophotometer.
2.Analytical procedure:
(1)Absorb a few ml of sodium tungstate solution(WO3 content is near 100mg) and Fe standard solution(Fe content is 5-20ug) into 100ml beaker, adding 8ml of 50% citric acid aqueous solution, adding water to clean the beaker wall until the volume of solution reaches 25ml, shake it up, heat it for 1-2min on the electric furnace.
(2)Adding 2ml of 10% EDTA solution, 2ml of 10% hydroxylamine hydrochloride solution, adjust PH value to 7 by NH3H2O (firstly coarse tuning by test paper, then adjust by PH meter).
(3)Add 5ml buffer solution. Put beaker in 60℃ water, then adding 2ml of 0.2% phenanthroline monohydrate solution. Keep it warm for 15min. Then pour into 50ml beaker and dilute with water to 50ml.
(4)When the wave length is 510nm, use 2cm cuvette to test its absorbance on 721 ultraviolet spectrophotometer.
3.Working curve:
(1)Absorb 5, 10, 15, 20, 30ug of 10ug/ml Fe standard solution in different 100ml beakers, adding 8ml of 50% citric acid aqueous solution and sodium tungstate solution(WO3 content is 100mg), the following steps is the same as analytical procedure. Then test its absorbance.
(2)Fe content is calculated by :Fe(mg/L)=γ/V x 10-3
Among which:
γ——quantity of Fe(ug) from the tested solution which is obtained from working curve.
V——quantity of sample(L)
4. Note:
(1)When adding citric acid aqueous solution, the obtained solution must reach 25ml or more, the boiling time must be 1-2min, temperature of electric furnace should within a certain limit in case the solution will turn yellow and affect the testing result.
(2)When adding phenanthroline monohydrate solution, shake the beaker at the same time, control the adding speed, if it is too fast, there would be participants. If there is participants, adding ammonium solution to dissolve it and adjust PH value to 8 by 1:1 hydrochloric acid until the participants disappear. If the participants happens again, the sample needs to be modulated again.
Tungsten Oxide Supplier: Chinatungsten Online www.tungsten-oxide.com | Tel.: 86 592 5129696; Fax: 86 592 5129797;Email:sales@chinatungsten.com |
Tungsten News & Prices, 3G Version: http://3g.chinatungsten.com | Molybdenum News & Molybdenum Price: http://news.molybdenum.com.cn |
Tungsten Alloy F1 Racing Car Counterweights Ⅳ
- Details
- Category: Tungsten Information
- Published on Wednesday, 30 December 2015 17:06
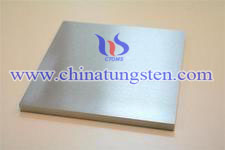
Tungsten Alloy Supplier: Chinatungsten Online www.tungsten-alloy.com | Tel.: 86 592 5129696; Fax: 86 592 5129797;Email:sales@chinatungsten.com |
Tungsten News & Prices, 3G Version: http://3g.chinatungsten.com | Molybdenum News & Molybdenum Price: http://news.molybdenum.com.cn |
Tungsten Alloy F1 Racing Car Counterweights Ⅲ
- Details
- Category: Tungsten Information
- Published on Wednesday, 30 December 2015 17:04
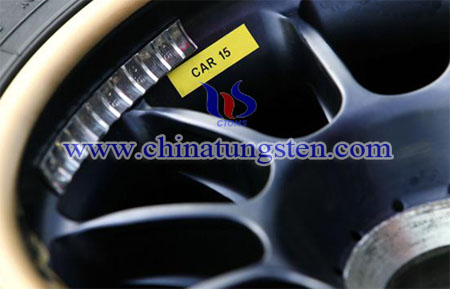
Tungsten Alloy Supplier: Chinatungsten Online www.tungsten-alloy.com | Tel.: 86 592 5129696; Fax: 86 592 5129797;Email:sales@chinatungsten.com |
Tungsten News & Prices, 3G Version: http://3g.chinatungsten.com | Molybdenum News & Molybdenum Price: http://news.molybdenum.com.cn |
Tungsten Alloy F1 Racing Car Counterweights Ⅱ
- Details
- Category: Tungsten Information
- Published on Wednesday, 30 December 2015 17:01
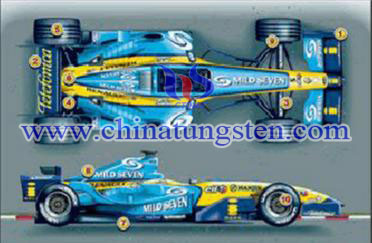
Tungsten Alloy Supplier: Chinatungsten Online www.tungsten-alloy.com | Tel.: 86 592 5129696; Fax: 86 592 5129797;Email:sales@chinatungsten.com |
Tungsten News & Prices, 3G Version: http://3g.chinatungsten.com | Molybdenum News & Molybdenum Price: http://news.molybdenum.com.cn |
Tungsten Alloy F1 Racing Car CounterweightsⅠ
- Details
- Category: Tungsten Information
- Published on Wednesday, 30 December 2015 16:59
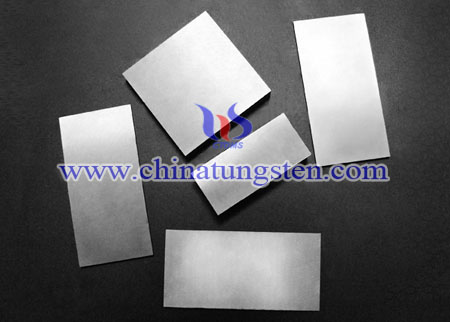
Tungsten Alloy Supplier: Chinatungsten Online www.tungsten-alloy.com | Tel.: 86 592 5129696; Fax: 86 592 5129797;Email:sales@chinatungsten.com |
Tungsten News & Prices, 3G Version: http://3g.chinatungsten.com | Molybdenum News & Molybdenum Price: http://news.molybdenum.com.cn |
Different Ball Milling Time Effect on Tungsten Copper Powder Phase
- Details
- Category: Tungsten Information
- Published on Wednesday, 30 December 2015 16:55
With increasing milling time, milling process leads to undergo refinement Cu diffraction peak intensity decreases, but equal to reduce diffraction peak intensity of W. Under the same conditions as observed, it can still be clearly observed diffraction peaks of Cu, Cu and the second peak has disappeared. This explains the grain refinement is not mechanical alloying process MA W, times the diffraction peaks disappear Cu sample of the main reasons. In the process of ball milling, tungsten copper W-Cu powder solid state reaction occurred, which leads to Cu content with fcc structure so that diffraction peaks disappeared is the main factor.
Viewed from the distance of grains and diffraction angle, with the increasing ball milling time, the distance of grains extend, the angle of diffraction decrease. It suggests that in the process of milling grain refinement occurs and is accompanied by solid solution phenomenon, whereas in solution process, a small amount of copper Cu diffusion into the tungsten W phase, and form solid solution. This is due to the high energy ball milling process, tungsten-copper composite powder produced severe plastic deformation in the ball rolling, cold rolling and cropping intensity, the particles undergone great stress and strain, resulting in grains forming a large number of dislocations, distortions and other microscopic defects, microscopic strain increases and a large number of dislocations tangles, and to promote the formation of sub-cellular structures and lead to reduced grain size. In addition, a large number of grains of crystal defects easily make atomic activity and increased energy storage system, promote the formation of a solid solution.
Tungsten Copper Supplier: Chinatungsten Online tungsten-copper.com | Tel.: 86 592 5129696; Fax: 86 592 5129797;Email:sales@chinatungsten.com |
Tungsten News & Prices, 3G Version: http://3g.chinatungsten.com | Molybdenum News & Molybdenum Price: http://news.molybdenum.com.cn |
Coated Cemented Carbide Process
- Details
- Category: Tungsten Information
- Published on Wednesday, 30 December 2015 16:54
Based on traditional chemical vapor deposition (CVD) and physical vapor deposition (PVD), some new coating technologies are emerging.
1. Chemical Vapor Deposition (CVD)
Since 1970s, chemical vapor deposition (CVD) has been widely used in semiconductor industry, which is suitable for most of metals and alloy materials. Theoretically, it uses two and more materials in gas state to react in chamber and forms new composite material to deposits on the surface of matrix. Viewed from coated cemented carbide, vacuum oven deposits the coating material on the surface of tungsten carbide cutting tool matrix by vacuum coating or arc evaporation at high temperature (about 800-1200℃).
In addition, CVD can be specifically divided into excess temperature controlling technology, medium temperature chemical vapor deposition (MTCVD), vacuum CVD, plasma chemical vapor deposition (PCVD), fluidized CVD, pyrolysis jet and so on. However, this kind of process has some defects, such as traditional CVD process will form brittle metal mesophase by deposited at high temperature, which has a bad effect on the properties in products.
2. Physical Vapor Deposition (PVD)
Physical vapor deposition (PVD) refers to transfer atoms and molecule to the surface of matrix, which uses low voltage, heavy current arc discharging and evaporate the target material. The evaporating material will ionized with the gas, which reaction products deposited on the matrix. Its advantage is that it can spray the grain with high hardness, high strength, good wear resistance and low coefficient of thermal expansion to tungsten carbide matrix, which makes it have better comprehensive properties. PVD also can be specifically divided into ion sputtering, vacuum evaporation, high-energy ion pulse, ion plating (arc ion plating, RF ion plating, hot cathode ion plating, hollow cathode deposition (HCD), DC discharge ion plating, activated reactive evaporation (ARE)) and so on.
Compared with CVD, PVD has lower deposited processing temperature (under 500℃) and it does not need heating process; there is no impact on the flexural strength of cutting tools under 600℃, and the internal stress of film is compression stress, which is more suitable for the coating of tungsten carbide precision or complex cutting tools. However, PVD has more complicate operation, higher demand of conditions and lower using cycles and uniformity than CVD process.
Tungsten Carbide Supplier: Chinatungsten Online tungsten-carbide.com.cn | Tel.: 86 592 5129696; Fax: 86 592 5129797;Email:sales@chinatungsten.com |
Tungsten News&Tungsten Prices, 3G Version: http://3g.chinatungsten.com | Molybdenum News & Molybdenum Price: http://news.molybdenum.com.cn |