Tungsten Alloy shielding Material Can Shield Radioisotope ElementsⅡ
- Details
- Category: Tungsten Information
- Published on Wednesday, 23 December 2015 14:25
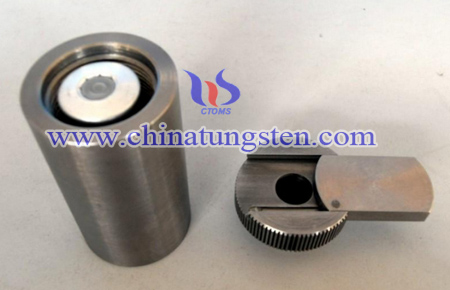
Tungsten Alloy Supplier: Chinatungsten Online www.tungsten-alloy.com | Tel.: 86 592 5129696; Fax: 86 592 5129797;Email:sales@chinatungsten.com |
Tungsten News & Prices, 3G Version: http://3g.chinatungsten.com | Molybdenum News & Molybdenum Price: http://news.molybdenum.com.cn |
Tungsten Alloy shielding Material Can Shield Radioisotope ElementsⅠ
- Details
- Category: Tungsten Information
- Published on Wednesday, 23 December 2015 14:22
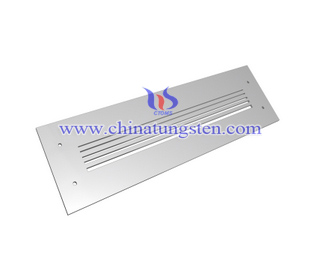
Tungsten Alloy Supplier: Chinatungsten Online www.tungsten-alloy.com | Tel.: 86 592 5129696; Fax: 86 592 5129797;Email:sales@chinatungsten.com |
Tungsten News & Prices, 3G Version: http://3g.chinatungsten.com | Molybdenum News & Molybdenum Price: http://news.molybdenum.com.cn |
Tungsten Alloy shielding Materials Application in C-14 Medical Field
- Details
- Category: Tungsten Information
- Published on Wednesday, 23 December 2015 14:18
Tungsten Alloy Supplier: Chinatungsten Online www.tungsten-alloy.com | Tel.: 86 592 5129696; Fax: 86 592 5129797;Email:sales@chinatungsten.com |
Tungsten News & Prices, 3G Version: http://3g.chinatungsten.com | Molybdenum News & Molybdenum Price: http://news.molybdenum.com.cn |
Tungsten Alloy Flywheel Counterweights
- Details
- Category: Tungsten Information
- Published on Tuesday, 22 December 2015 17:52
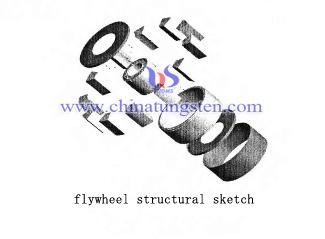
Tungsten Alloy Supplier: Chinatungsten Online www.tungsten-alloy.com | Tel.: 86 592 5129696; Fax: 86 592 5129797;Email:sales@chinatungsten.com |
Tungsten News & Prices, 3G Version: http://3g.chinatungsten.com | Molybdenum News & Molybdenum Price: http://news.molybdenum.com.cn |
Tungsten Copper Electrode Densification Problems II
- Details
- Category: Tungsten Information
- Published on Tuesday, 22 December 2015 16:57
Under normal infiltration, sintering conditions between tungsten and copper are two metals are immiscible and invasive low, which also makes the two powder densification process by certain obstacles, making it difficult to achieve high densification and the desired structure. But only by increasing the pressure and sintering temperature, although to some extent, can increase the density of the final product, but brought a lot of problems in the process conditions and comprehensive performance assurance, the following aspects in general:
2. Composition description
In the process of sintering, the composition controlling precision of tungsten copper is lower, although it calculated by accurate copper infiltration. In addition, the falling and overflow of copper liquid will have an effect on the composition offset and bring some difficulties to the surface machining of parts with complex shape during the liquid-phase sintering. Generally, due to the shrinkage ratio of liquid sintering reaches 15%-20%, the distortion and dimensional accuracy controlling is more difficult than solid-phase sintering. It is not conductive to parts with complex shape machining directly, especially to powder injection molding (PIM).
Thus, in order to achieve densification, we should ensure that the composition and size will be effective controlled, which is beneficial for machining parts with complex shape by PM and PIM. According to the present research, improving the activity of powder, such as choosing ultrafine powder and high energy-storing powder, can achieve densification rapidly, decrease the amount of copper overflowing and the size precision will remarkably improved. It is the most beneficial for composition controlling that sintering can be in solid phase state. This is due to liquid-phase sintering has some difficulties in distortion and size controlling, especially for the high volume fraction.
3. Size distribution
The study on the size controlling of liquid-phase sintering shows that the macroscopic deformation and micro structure has some internal connection, such as solubility, contact angle, grain size, coordination number and the volume fraction of solid. Tungsten copper (W-Cu) system has low solubility and high dihedral angle. Relevant scholars through calculations show that the three-dimensional grain contiguity of more than 3:00 to avoid collapse and deformation resistance critical solid volume fraction is 0.2. It is clear that the structure of complex parts, the only requirement without deformation is not enough, which also needs to have a certain size range of accuracy requirements. It is similar to component controlling, sintering in solid phase state is beneficial for size precision sintering and high densification.
Tungsten Copper Supplier: Chinatungsten Online tungsten-copper.com | Tel.: 86 592 5129696; Fax: 86 592 5129797;Email:sales@chinatungsten.com |
Tungsten News & Prices, 3G Version: http://3g.chinatungsten.com | Molybdenum News & Molybdenum Price: http://news.molybdenum.com.cn |
Tungsten Alloy Counterweights Liquid-phase Sintering Preparation MethodⅡ
- Details
- Category: Tungsten Information
- Published on Tuesday, 22 December 2015 16:55
Tungsten Alloy Supplier: Chinatungsten Online www.tungsten-alloy.com | Tel.: 86 592 5129696; Fax: 86 592 5129797;Email:sales@chinatungsten.com |
Tungsten News & Prices, 3G Version: http://3g.chinatungsten.com | Molybdenum News & Molybdenum Price: http://news.molybdenum.com.cn |
Tungsten Copper Electrode Metallographic Phase and Properties Analysis
- Details
- Category: Tungsten Information
- Published on Tuesday, 22 December 2015 16:53
Tungsten copper powder sintered material morphology distribution of tungsten skeleton evenly distributed on the copper matrix. Due to the nature of tungsten (W) high melting point and high hardness, tungsten at 1000 ℃, its ultimate tensile strength is still 50kgf/mm2, low carbon intensity is even higher than room temperature, which makes tungsten copper material copper melting point below the temperature (about 1000 ℃), still has a very high wear resistance and heat hardness. The tungsten skeleton with copper as matrix stick as a whole, and constitutes the sintered material good heat conductor and pathways, so that the tungsten skeleton used in the process does not has partial overheating.
The strength at room temperature of common metal is determined by two essentials, which are Metal atomic binding force and resistance to dislocation motion. When tungsten copper used as electrode in welding resistance, it improves the strength by enhancing the resistance to dislocation motion, which includes cold hardening and the demolition. However, with the increasing temperature, the effect will remarkably decrease, even disappear. For instance, after cold hardening, the hardness at room temperature of red copper is HB100-110, when the temperature reaches 200-250℃, the hardening effect will disappear almost. In addition, most of strengthening copper alloy by precipitate phase will weaken owing to the phase integrates into the matrix again.
In contrast, the recrystallization and phase change of copper-tungsten powder sintered material does not occur at a high temperature. Some studies show that the data on tungsten copper materials, tungsten, copper W-30Cu hardness and conductivity higher than beryllium copper, the softening temperature was more than twice as beryllium copper. Therefore, tungsten copper material used as flash butt welding or arc welding electrodes, especially in continuous operation at high temperatures, which has high requirements of conductivity and high wear resistance requirements, it will better highlight the tungsten copper electrode material superiority.
Tungsten Copper Supplier: Chinatungsten Online tungsten-copper.com | Tel.: 86 592 5129696; Fax: 86 592 5129797;Email:sales@chinatungsten.com |
Tungsten News & Prices, 3G Version: http://3g.chinatungsten.com | Molybdenum News & Molybdenum Price: http://news.molybdenum.com.cn |
Tungsten Alloy Counterweights Liquid-phase Sintering Preparation MethodⅠ
- Details
- Category: Tungsten Information
- Published on Tuesday, 22 December 2015 16:51
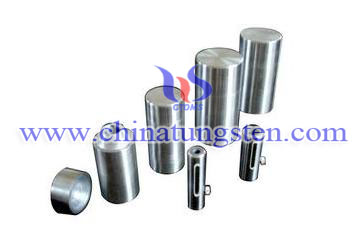
Tungsten Alloy Supplier: Chinatungsten Online www.tungsten-alloy.com | Tel.: 86 592 5129696; Fax: 86 592 5129797;Email:sales@chinatungsten.com |
Tungsten News & Prices, 3G Version: http://3g.chinatungsten.com | Molybdenum News & Molybdenum Price: http://news.molybdenum.com.cn |
Tungsten Alloy Sword Hilt Counterweights
- Details
- Category: Tungsten Information
- Published on Tuesday, 22 December 2015 16:46
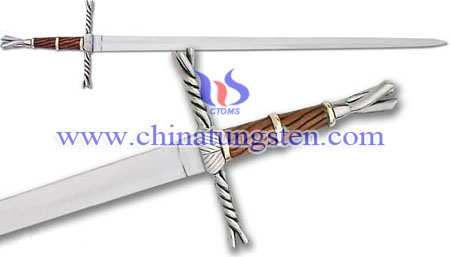
Tungsten Alloy Supplier: Chinatungsten Online www.tungsten-alloy.com | Tel.: 86 592 5129696; Fax: 86 592 5129797;Email:sales@chinatungsten.com |
Tungsten News & Prices, 3G Version: http://3g.chinatungsten.com | Molybdenum News & Molybdenum Price: http://news.molybdenum.com.cn |
Effects of Ammonium Paratungstate Calcination Temperature on Properties of Tungsten Powder
- Details
- Category: Tungsten Information
- Published on Tuesday, 22 December 2015 14:32
Tungsten Supplier: Chinatungsten Online www.chinatungsten.com | Tel.: 86 592 5129696; Fax: 86 592 5129797;Email:sales@chinatungsten.com |
Tungsten News & Prices, 3G Version: http://3g.chinatungsten.com | Molybdenum News & Molybdenum Price: http://news.molybdenum.com.cn |