Tungsten Copper Electrode Sintering Mechanism and Densification III
- Details
- Category: Tungsten Information
- Published on Friday, 18 December 2015 16:55
When the temperature further increased to the liquid phase sintering temperature, liquid copper starts to forming, and the particle rearrangement of the tungsten particles occurs by the capillary force of traction at the same time. As previously shows the figure presented in the interior of the copper phase tungsten particles contact with each other rearrangements and contraction.
Therefore, the strength and toughness of powder has been remarkably improved after sintering, which includes two reasons: one is the connection strength between the particles is increasing by the rearrangements, which is known as inter-atomic forces increases in chemistry; another one is the contact surface of the particles inside the body to achieve atomic gravity range of the number is limited, and to further enhance the amplitude of the temperature increase or make atomic diffusion occurs, so that the contact surface into the scope of increasing the number of atomic forces, to form a larger adhesive surface. With the expanding adhesive surface, the strength of sintered compact increases and come into neckformation, this accomplishes the change from particle interface to crystal boundary.
In addition, the shape of pores and the amount or volume changes are also the performance of the sintering strength enhancing. The model of sintering round grain diagram as follow, it shows the change of pore shape. Due to the neckformation grows up, the pores shrink and obturator rounded. In the process of sintering, not only the shape and properties has been altered, the number and the size of pore are also changed. Overall, owing to the shrinkage and gathering of pores, the amount intends to decrease, the average size of pore rise a little and the small pores shrink and disappear faster than the large.
The main reason of shrinkage is not related to the adhesive surface, which indicates densification is not the signal of the beginning of sintering, only the strength of sinter compact enhancing is the obvious. According to the sintering time, the sintering process of tungsten copper powder can be divided into several stages (there is no a definite demarcation):
1. Adhesive: At the beginning of sintering, Particle contact interface to the boundary changes, sintering neck formed at this stage and grew. Grains within the particles does not change, the particle shape can not change substantially, the whole of the sintered body does not shrink, but also the minimum density increases, but the strength and conductivity of the sintered body increases due to particle bonding surface significantly increased;
2. Neckformation: Atomic particles are bonded to the surface of a large number of migration leading to an expansion of sintering neck, shorten the distance between the particles form a continuous network of pores. Further, since the grain growth, grain boundary movement across the pores, grain boundaries are swept place, a large number of pores disappear, the volume of the sintered body shrinkage, increase the density and strength of this stage is the most essential feature;
3. Spheroidizing and shrinkage: In the late of sintering, sintered body has higher related density, most of the pores are completely divided, closed-cell number increased significantly, pore shape close to spherical and shrinking. At this stage, the entire contraction of the sintered body is still slow, but mainly by reducing the voids disappear and the number of small pores to achieve. The duration of this phase is longer, but still a small amount of residual isolation holes can not be eliminated.
Tungsten Copper Supplier: Chinatungsten Online tungsten-copper.com | Tel.: 86 592 5129696; Fax: 86 592 5129797;Email:sales@chinatungsten.com |
Tungsten News & Prices, 3G Version: http://3g.chinatungsten.com | Molybdenum News & Molybdenum Price: http://news.molybdenum.com.cn |
Tungsten Alloy Golf Weights
- Details
- Category: Tungsten Information
- Published on Friday, 18 December 2015 16:17
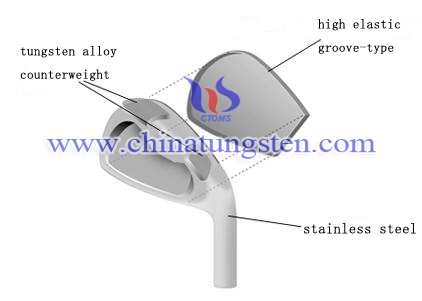
Tungsten Alloy Supplier: Chinatungsten Online www.tungsten-alloy.com | Tel.: 86 592 5129696; Fax: 86 592 5129797;Email:sales@chinatungsten.com |
Tungsten News & Prices, 3G Version: http://3g.chinatungsten.com | Molybdenum News & Molybdenum Price: http://news.molybdenum.com.cn |
Tungsten Alloy Counterweight Brief IntroductionⅡ
- Details
- Category: Tungsten Information
- Published on Friday, 18 December 2015 16:12
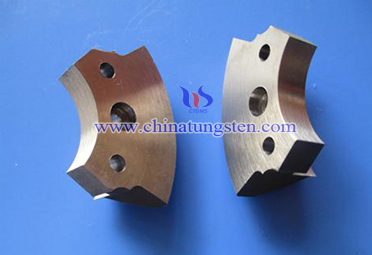
Tungsten Alloy Supplier: Chinatungsten Online www.tungsten-alloy.com | Tel.: 86 592 5129696; Fax: 86 592 5129797;Email:sales@chinatungsten.com |
Tungsten News & Prices, 3G Version: http://3g.chinatungsten.com | Molybdenum News & Molybdenum Price: http://news.molybdenum.com.cn |
Tungsten Alloy Counterweight Brief IntroductionⅠ
- Details
- Category: Tungsten Information
- Published on Friday, 18 December 2015 16:08
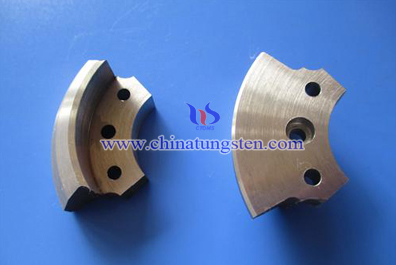
Tungsten Alloy Supplier: Chinatungsten Online www.tungsten-alloy.com | Tel.: 86 592 5129696; Fax: 86 592 5129797;Email:sales@chinatungsten.com |
Tungsten News & Prices, 3G Version: http://3g.chinatungsten.com | Molybdenum News & Molybdenum Price: http://news.molybdenum.com.cn |
Tungsten Alloy Radiation Shielding Materials Application in γ-raysⅡ
- Details
- Category: Tungsten Information
- Published on Thursday, 17 December 2015 18:12
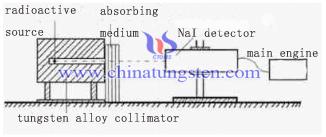
Tungsten Alloy Supplier: Chinatungsten Online www.tungsten-alloy.com | Tel.: 86 592 5129696; Fax: 86 592 5129797;Email:sales@chinatungsten.com |
Tungsten News & Prices, 3G Version: http://3g.chinatungsten.com | Molybdenum News & Molybdenum Price: http://news.molybdenum.com.cn |
Tungsten Alloy Radiation Shielding Materials Application in γ-raysⅠ
- Details
- Category: Tungsten Information
- Published on Thursday, 17 December 2015 18:05
Tungsten Alloy Supplier: Chinatungsten Online www.tungsten-alloy.com | Tel.: 86 592 5129696; Fax: 86 592 5129797;Email:sales@chinatungsten.com |
Tungsten News & Prices, 3G Version: http://3g.chinatungsten.com | Molybdenum News & Molybdenum Price: http://news.molybdenum.com.cn |
Blue Tungsten Oxide Preparation out of Ammonium Paratungstate Self-Reduction
- Details
- Category: Tungsten Information
- Published on Thursday, 17 December 2015 17:50
Tungsten Supplier: Chinatungsten Online www.chinatungsten.com | Tel.: 86 592 5129696; Fax: 86 592 5129797;Email:sales@chinatungsten.com |
Tungsten News & Prices, 3G Version: http://3g.chinatungsten.com | Molybdenum News & Molybdenum Price: http://news.molybdenum.com.cn |
Ammonium Paratungstate Detinning Processes
- Details
- Category: Tungsten Information
- Published on Thursday, 17 December 2015 17:24
Various detinning processes of ammonium paratungstate mainly focus on removing tin acid radical(SnO32-) in sodium tungstate solution. It is depends on the characteristics of tungsten concentrates our country use currently. Tin impurities of tungsten concentrates mainly occurs as SnO2, tin mainly occurs as tin acid radical in the alkali immersion from ore alkali decomposition :
SnO2 + 2OH -= SnO32- + H2O.
Currently, in the occasion that China's tungsten smelting uses high quality tungsten concentrates, since the content of tin impurities in the ore is not high (0.1% to 0.4%) and it’s a monomorphic form mainly as SnO2, the content of tin impurities in leaching solution is not too high. High-quality products APT can be produced if any of detinning processes is taken in tungsten smelting process. Of course, each tin process also has negative impacts, primarily the balance between detinning rate and tungsten loss rate. Although some processes have higher detinning rate, tungsten loss is still serious. In addition, each process has shortcomings such as complex process. Also,there’re great impacts on the production cycle, production cost and process route complexity since the addition of detinning process.
At the same time, it is worth noting that, with the increasing scarcity of high-quality tungsten concentrates available for the exploitation of resources to maintain the tin content and other impurities increasing, more and more complex forms, tungsten concentrate in tin Occurrence Sometimes no longer SnO2-based, but in the state of tin SnO2 and sulfide (Stannite Cu2FeSnS4; SnS2 tin sulfide, etc.) coexist. When alkali leaching by reaction:
3SnS2 + 6OH- = 2SnS32- + Sn (OH) 62-,
It’s found that thiosulfate tin ions (SnS32- ) appear in sodium tungstate solution while the content of tin acid radical increased . In the current production, thiosulfate tin ions are the main reason for excessive tin impurities in product APT. Therefore, the development direction of detinning process should focus on removing thiosulfate tin ion, taking into account not long tungsten smelting process, without reducing the tungsten recovery. This study is little domestic, overseas it has also not been reported. This author has conducted systematic research to study the existing ratio of tin thiosulfate solution acid radical relationship with the pH of the solution, thio tin acid radical removal methods, but only in the exploratory stage, but also we hope to have more metallurgy workers joined the ranks of this study.
Tungsten Supplier: Chinatungsten Online www.chinatungsten.com | Tel.: 86 592 5129696; Fax: 86 592 5129797;Email:sales@chinatungsten.com |
Tungsten News & Prices, 3G Version: http://3g.chinatungsten.com | Molybdenum News & Molybdenum Price: http://news.molybdenum.com.cn |
Radioactive Source Species With Tungsten Alloy Radiation Shielding Materials
- Details
- Category: Tungsten Information
- Published on Thursday, 17 December 2015 17:09
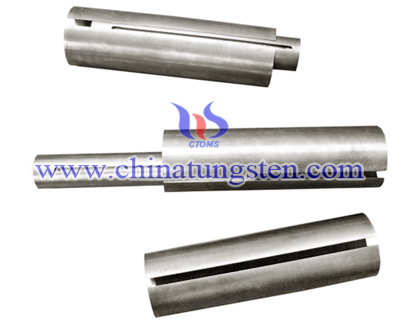
Tungsten Alloy Supplier: Chinatungsten Online www.tungsten-alloy.com | Tel.: 86 592 5129696; Fax: 86 592 5129797;Email:sales@chinatungsten.com |
Tungsten News & Prices, 3G Version: http://3g.chinatungsten.com | Molybdenum News & Molybdenum Price: http://news.molybdenum.com.cn |
Tungsten Alloy Radioactive Source Container
- Details
- Category: Tungsten Information
- Published on Thursday, 17 December 2015 17:05
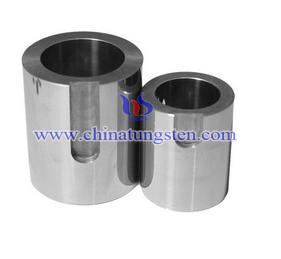
Tungsten Alloy Supplier: Chinatungsten Online www.tungsten-alloy.com | Tel.: 86 592 5129696; Fax: 86 592 5129797;Email:sales@chinatungsten.com |
Tungsten News & Prices, 3G Version: http://3g.chinatungsten.com | Molybdenum News & Molybdenum Price: http://news.molybdenum.com.cn |