The Influencing Factors of Tungsten Copper Electrode Conductivity
- Details
- Category: Tungsten Information
- Published on Thursday, 10 December 2015 16:06
Tungsten copper electrode is one of the most widely used in Electrical Discharge Machining (EDM). Due to EDM uses pulsed spark between tool and workpiece, which ablate the metal by partial high temperature of discharging. Therefore, it is necessary that the electrode of EDM requires ablation resistance and excellent conductivity. What’s more, its distribution should be uniform.
Some researchers find that the measured conductivity is generally lower than the theoretical value by theoretical model of thermal conductivity value (also applied in analyzing conductivity). The influencing factors of conductivity of tungsten copper electrode are impurities, porosity and micro structure. Among them, impurity is the main factor, which trace will remarkably decrease the thermal conductivity and electrical conductivity of tungsten copper.
The source of impurities in the following areas: 1. activator, for improving the densification of tungsten copper, will form the solid solution with Cu and has an effect on the electrical conductivity. 2. The purity of raw material is lower, probably lead in impurities from outside during the preparation.
Tungsten Copper Supplier: Chinatungsten Online tungsten-copper.com | Tel.: 86 592 5129696; Fax: 86 592 5129797;Email:sales@chinatungsten.com |
Tungsten News & Prices, 3G Version: http://3g.chinatungsten.com | Molybdenum News & Molybdenum Price: http://news.molybdenum.com.cn |
Ni-doped Effects on Tungsten Copper Electrode III
- Details
- Category: Tungsten Information
- Published on Thursday, 10 December 2015 16:04
Except that the density and hardness of tungsten copper electrode, the effect of adding nickel (Ni) on the electrical conductivity of tungsten copper electrode is also can not be neglected. The effect of content of Ni on the electrical conductivity of tungsten copper electrode diagram as follow:
The diagram visually shows that the electrical conductivity of tungsten copper electrode dramatically decreases after adding nickel (Ni). (When the content of Ni is 0%, the electrical conductivity is 34.5%IACS, and the electrical conductivity decreases to 17.5%IACS after the content of Ni reaching 0.2 %.) Afterwards, with the increasing content of Ni, the electrical conductivity decreases constantly. The principle is similar to the adding cobalt (Co) that tungsten dissolved in nickel (Ni), which promoted the sintering densification. A large number of solid tungsten particles bonded contact with each other to form a continuous skeleton, limiting the role of liquid Cu infiltration, resulting in tissue tungsten copper alloy electrode uneven. In addition, external Ni atom enlarges the resistance through electrons of tungsten and copper scattering after adding active element Ni.
Tungsten Copper Supplier: Chinatungsten Online tungsten-copper.com | Tel.: 86 592 5129696; Fax: 86 592 5129797;Email:sales@chinatungsten.com |
Tungsten News & Prices, 3G Version: http://3g.chinatungsten.com | Molybdenum News & Molybdenum Price: http://news.molybdenum.com.cn |
Ammonium Paratungstate Tetrahydrate X-Ray Powder Diffraction Data and Unit Cells
- Details
- Category: Tungsten Information
- Published on Thursday, 10 December 2015 11:34
Tungsten Supplier: Chinatungsten Online www.chinatungsten.com | Tel.: 86 592 5129696; Fax: 86 592 5129797;Email:sales@chinatungsten.com |
Tungsten News & Prices, 3G Version: http://3g.chinatungsten.com | Molybdenum News & Molybdenum Price: http://news.molybdenum.com.cn |
Pure Ammonium Paratungstate from Tungsten Scraps
- Details
- Category: Tungsten Information
- Published on Thursday, 10 December 2015 11:05
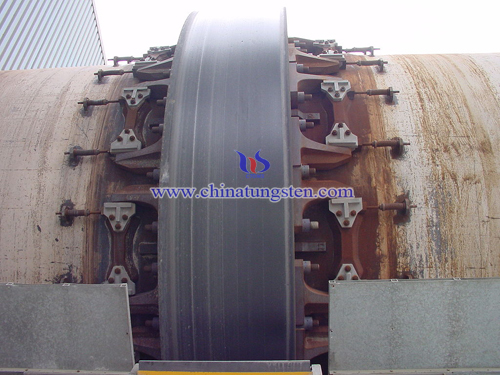
Tungsten Supplier: Chinatungsten Online www.chinatungsten.com | Tel.: 86 592 5129696; Fax: 86 592 5129797;Email:sales@chinatungsten.com |
Tungsten News & Prices, 3G Version: http://3g.chinatungsten.com | Molybdenum News & Molybdenum Price: http://news.molybdenum.com.cn |
Ni-doped Effects on Tungsten Copper Electrode II
- Details
- Category: Tungsten Information
- Published on Wednesday, 09 December 2015 16:03
Except cobalt (Co) element, Nickel (Ni) is also a kind of common additives, and the density, the hardness, the electrical conductivity and other comprehensive properties of tungsten copper electrode will be influenced by the content of Ni. According to the phase diagram of Cu-Ni and Ni-W as follow:
From the Cu-Ni and Ni-W phase diagram can visually see the nickel (Ni) and copper (Cu) is infinitely miscible, and tungsten W can be dissolved in Ni. Therefore, when tungsten copper composite powder mixed with Ni element, the porosity will decrease and the density and the hardness of tungsten copper electrode is improved. In addition, in the process of sintering, tungsten particles rearranged by the liquid Cu, which shortens the distance among the particles and further enhances the densification. Through SEM (Scanning Electron Microscope), we can find that the particle of skeleton is uniform and the granularity is finer. However, with the increasing content of Ni, the connectivity of tungsten skeleton will be better.
More infomations about Ni-doped effects on tungsten copper electrode, click here:
http://news.chinatungsten.com/en/tungsten-information/81132-ti-10471
Tungsten Copper Supplier: Chinatungsten Online tungsten-copper.com | Tel.: 86 592 5129696; Fax: 86 592 5129797;Email:sales@chinatungsten.com |
Tungsten News & Prices, 3G Version: http://3g.chinatungsten.com | Molybdenum News & Molybdenum Price: http://news.molybdenum.com.cn |
Ni-doped Effects on Tungsten Copper Electrode
- Details
- Category: Tungsten Information
- Published on Wednesday, 09 December 2015 16:00
Except cobalt (Co) element, Nickel (Ni) is also a kind of common additives, and the density, the hardness, the electrical conductivity and other comprehensive properties of tungsten copper electrode will be influenced by the content of Ni. The effect of content of Ni on the density and hardness of tungsten copper W-25Cu electrode as follow:
The diagram shows that the density and the hardness of tungsten copper electrode is sensitive to the adding Ni element. When the content of Ni is 0.3%, the density rapidly increases 14.9g/cm3 to 17.0g/cm3. Therefore, adding Ni element will improve the density and the hardness of tungsten copper products.
Tungsten Copper Supplier: Chinatungsten Online tungsten-copper.com | Tel.: 86 592 5129696; Fax: 86 592 5129797;Email:sales@chinatungsten.com |
Tungsten News & Prices, 3G Version: http://3g.chinatungsten.com | Molybdenum News & Molybdenum Price: http://news.molybdenum.com.cn |
Mechannism and Operational Conditions of Silicon, Phosphrous, Arsenic Ammonium Paratungstate (APT)
- Details
- Category: Tungsten Information
- Published on Wednesday, 09 December 2015 11:57
Tungsten Supplier: Chinatungsten Online www.chinatungsten.com | Tel.: 86 592 5129696; Fax: 86 592 5129797;Email:sales@chinatungsten.com |
Tungsten News & Prices, 3G Version: http://3g.chinatungsten.com | Molybdenum News & Molybdenum Price: http://news.molybdenum.com.cn |
The Average Particle Size of Ammonium Paratungstate Reducing Process
- Details
- Category: Tungsten Information
- Published on Wednesday, 09 December 2015 11:43
Tungsten Supplier: Chinatungsten Online www.chinatungsten.com | Tel.: 86 592 5129696; Fax: 86 592 5129797;Email:sales@chinatungsten.com |
Tungsten News & Prices, 3G Version: http://3g.chinatungsten.com | Molybdenum News & Molybdenum Price: http://news.molybdenum.com.cn |
Co-doped Effects on Tungsten Copper Electrode V
- Details
- Category: Tungsten Information
- Published on Tuesday, 08 December 2015 16:29
Since the large part of tungsten copper electrode is used for EDM (Electrical Discharge Machining), the measure of its electrical conductivity is crucial. However, the electrical conductivity is sensitive to the impurities and porosity so that the adding cobalt (Co) has an large effect on the electrical conductivity of tungsten copper electrode. The effect of different content of Co on the electrical conductivity of tungsten copper electrode diagram as follow:
The diagram shows that the adding Co element dramatically decreases the electrical conductivity of tungsten copper electrode. Before adding Co element, the electrical conductivity is about 34.5%IACS, while adds 0.2% Co element, the electrical conductivity greatly decreases 34.5%IACS to 16.4%IACS. With the constant increase of Co content, the electrical conductivity decrease constantly. However, tungsten dissolving in Co improves the sintering densification, a large number of solid phases connected with each other to form the continuous tungsten skeleton, the infiltration of liquid phase copper has been restricted, which leads to the maldistribution.
Tungsten Copper Supplier: Chinatungsten Online tungsten-copper.com | Tel.: 86 592 5129696; Fax: 86 592 5129797;Email:sales@chinatungsten.com |
Tungsten News & Prices, 3G Version: http://3g.chinatungsten.com | Molybdenum News & Molybdenum Price: http://news.molybdenum.com.cn |
Co-doped Effects on Tungsten Copper Electrode IV
- Details
- Category: Tungsten Information
- Published on Tuesday, 08 December 2015 16:24
Use cobalt (Co) powder as activator can greatly promote the solid phase sintering of tungsten skeleton. Some studies have shown that due to the existence of W6CO7 phase or Co atom on the surface of tungsten particle, it has better wettability and improve the rearrangements of particles in sintering. Although the effect of Co additives can not be removed, the high phase boundary diffusion and the transformation of material are enhancing. In the process of tungsten skeleton sintering, W dissolved in Co, firstly formed "carrier phase" on the surface of tungsten particle and then the tungsten atom by spreading the opposing Co phase, when liquid phase sintering is preferentially formed in connecting skeleton. Co-W and Co-Cu binary phase diagram as follow:
During the infiltration, viscous Cu liquid flows and fills the pores in, which further improve the densification. When the Co content exceeds 0.2%, the pores in the material substantially eliminated, and a large number of solid phase tungsten particles is connected with each other to form continuous skeleton, which limit the flow of liquid Cu, block the increase of densification, and decrease the density because of the growth of tungsten particle.
Tungsten Copper Supplier: Chinatungsten Online tungsten-copper.com | Tel.: 86 592 5129696; Fax: 86 592 5129797;Email:sales@chinatungsten.com |
Tungsten News & Prices, 3G Version: http://3g.chinatungsten.com | Molybdenum News & Molybdenum Price: http://news.molybdenum.com.cn |