Effects of Ammonium Paratungstate Morphology and Particle Size Distribution on the Strength of Tungsten Powder Compacts
- Details
- Category: Tungsten Information
- Published on Wednesday, 16 December 2015 16:57

Tungsten Supplier: Chinatungsten Online www.chinatungsten.com | Tel.: 86 592 5129696; Fax: 86 592 5129797;Email:sales@chinatungsten.com |
Tungsten News & Prices, 3G Version: http://3g.chinatungsten.com | Molybdenum News & Molybdenum Price: http://news.molybdenum.com.cn |
Tungsten Alloy Cylinder Counterweights Applications in AutoⅠ
- Details
- Category: Tungsten Information
- Published on Wednesday, 16 December 2015 16:50
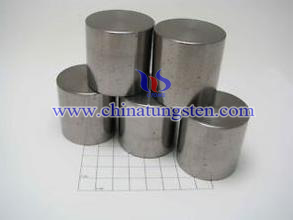
Tungsten Alloy Supplier: Chinatungsten Online www.tungsten-alloy.com | Tel.: 86 592 5129696; Fax: 86 592 5129797;Email:sales@chinatungsten.com |
Tungsten News & Prices, 3G Version: http://3g.chinatungsten.com | Molybdenum News & Molybdenum Price: http://news.molybdenum.com.cn |
Tungsten Alloy Crankshaft Counterweights
- Details
- Category: Tungsten Information
- Published on Wednesday, 16 December 2015 16:39
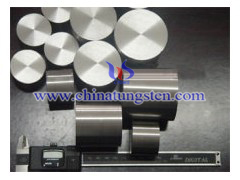
Tungsten Alloy Supplier: Chinatungsten Online www.tungsten-alloy.com | Tel.: 86 592 5129696; Fax: 86 592 5129797;Email:sales@chinatungsten.com |
Tungsten News & Prices, 3G Version: http://3g.chinatungsten.com | Molybdenum News & Molybdenum Price: http://news.molybdenum.com.cn |
Nano Copper powder of Tungsten Copper Electrode Preparation II
- Details
- Category: Tungsten Information
- Published on Wednesday, 16 December 2015 16:23
Compared with traditional powder metallurgy (PM), tungsten copper electrode nano composite material including powder milling, compacting and sintering process, but due to the characteristics of nano particles, there are some differences between traditional powder metallurgy and nano copper powder preparation.
3. Mechanochemistry
It combined both high energy ball milling and chemical reaction. High energy ball milling has many advantages, such as simple operation, high efficiency, especially suitable for the metal with high melting point, mutually insoluble solid solution system, micro intermetallic compound fabricating and micro metal ceramics composite materials. However, the distribution of grain produced in this way is uneven and it will easily bring in other impurities in the process of ball milling. The researchers uses Mechanochemistry, which smash the mixture of CuN and Na powder and produces Cu and NaCl micro nanocrystaline mixture by solid substitution reaction. Washing the mixture to remove the milled sodium chloride, ultrafine copper powder can be obtained. It can not be neglected that adding NaCl will avoid the mixture burning, and the copper powder will be finer (20-50μm of granularity).
4. γ Ray irradiation - hydrothermal crystallization
The method mainly in the experimental stage, some scholars use Co γ ray irradiation source strong metal ultrafine particles prepared using γ-ray radiation - hydrothermal crystallization method jointly received an average particle diameter of about 50μm of copper nano particles.
5. Liquid phase reduction
In liquid or very close to the liquid state, the raw material can be synthesized directly metal nano powders. The use of inorganic metal compounds in the alcohols (ethylene glycol, diethylene glycol, etc.) in the heating reduction can be prepared mono disperse copper nano particles. The researchers used hydrazine hydrate reduced copper pickled copper, while adding polyethylene polymer protective agent pyrrolidone (PVP) help stabilize the grain to prevent agglomeration, use magnesium Mg as the catalyst reaction, copper obtained a considerable part of condensed matter. However, the methods used hydrazine hydrate is highly toxic, is not suitable to promote production use.
6. Self suspended directional flow
Metal material melts in high frequency power supply heating to the metal droplets in countercurrent sensor electromagnetic field generated by spherical droplets of molten metal suspended in studio and continues to be heated. Meanwhile, the inert gas as a cooling medium is always a constant flow rate passing molten metal droplet surface. When the spherical droplet reaches a certain temperature, the surface of the metal vapor produced in the cooling stream of inert gas is too cold nucleation and subsequently grow up (including a collision with the merger between the particles), the final formation of the desired metal nano particles.
Tungsten Copper Supplier: Chinatungsten Online tungsten-copper.com | Tel.: 86 592 5129696; Fax: 86 592 5129797;Email:sales@chinatungsten.com |
Tungsten News & Prices, 3G Version: http://3g.chinatungsten.com | Molybdenum News & Molybdenum Price: http://news.molybdenum.com.cn |
Tungsten Copper Electrode Sintering Mechanism and Densification II
- Details
- Category: Tungsten Information
- Published on Wednesday, 16 December 2015 16:20
According to the mechanism of one solid phase sintering, we can build a compact model as follow (the show map of the change of the powder during the solid phase):
Viewed from the diagram, the particle with deep color, cladded internal is tungsten (W), and the external particles in white is copper (Cu), the particles contacts by point. In the solid-phase state, the shrinkage of powder takes up 1/3 shrinkage of total volume. Generally, tungsten copper W-Cu powder does not shrink in the solid-phase state. However, if the temperature rises up to or exceeds copper recrystallization temperature during the copper powder sintering, it will remarkably sintering in solid-phase.
In addition, tungsten grain of tungsten copper nano composite powder is disperse at the beginning, basically Cu phase contacts with each other. Therefore, some related researchers propose that Cu solid-phase sintering at the temperature lower than copper liquid is the main mechanism of sintering densification, and the internal tungsten grains cladded in Cu blocks out the sintering process to some extent.
Picture a to picture c shows that due to the diffusing and flowing effect of copper liquid, the contact area of particles is expanding, the internal gas is extruded so that the compact densification. Tungsten particles close to each other and in contact gradually under the action of the flow of fluid passing copper will eventually gather and grow up under the influence of interfacial tension.
Picture a is the initial status of compact, which powder is disperse and the contact of particles is point with small contact area, the small tungsten grain inside of Cu phase is separated by the larger Cu grain; Picture b shows that with the increasing sintering temperature gradually, the tension of diffusion of surface atoms and surface tension force it to flow to the contact, the contact area expands, the pores shrinks and the internal tungsten grain cladded by Cu phase get close, gathers and grows up by the flowing copper liquid and interfacial energy; Picture c, with the temperature increasing further, the contact area is becoming larger, the pore is shrinking to ball-shaped, tungsten grain is gathering and composed of the larger grain, which blocks out copper solid-phase sintering further.
Tungsten Copper Supplier: Chinatungsten Online tungsten-copper.com | Tel.: 86 592 5129696; Fax: 86 592 5129797;Email:sales@chinatungsten.com |
Tungsten News & Prices, 3G Version: http://3g.chinatungsten.com | Molybdenum News & Molybdenum Price: http://news.molybdenum.com.cn |
Advantages For Tungsten Alloy Materials Preparing Radiation Shielding
- Details
- Category: Tungsten Information
- Published on Tuesday, 15 December 2015 18:45
Tungsten alloy is a kind of alloy, which based with tungsten and added some other elements. In metals, tungsten has the highest melting point, high temperature strength, good creep resistance, good thermal conductivity, good electrical conductivity and electron emission properties and large specific gravity. In addition to be greatly used in the manufacture of carbide alloy and additives of alloy, tungsten and its alloys are not only widely used in electronics, electric light industry, but also used in aerospace, casting, weaponry and other sectors for producing rocket nozzles, casting molds, penetrator, contacts, heating element, heat shields and so on. In addition, high-density tungsten alloy are often used to make the tungsten radiation shielding,which been used in many fields.
The studies have confirmed that the radiation shielding ability has a close relationship with the density of materials, the greater the density, the better the radiation shielding performance. In another words, higher density means better-ray absorption capacity and radiation shielding capability. Due to the high density of tungsten alloy than other materials, the tungsten alloy radiation shielding of γ-ray has better radiation shielding properties, thereby can reduce the volume of the shield without affecting the radiation shielding performance. The same volume of tungsten alloy radiation shielding will have better radiation shielding performance compared to lead.
Tungsten alloy combines high density (the density is 60% higher than lead), machinability, good corrosion resistance and high radiation absorption capacity(better than lead and steel), high strength, etc., so it can be seen that the tungsten alloy materials are the best raw materials to prepare radiation shielding.
Tungsten Alloy Supplier: Chinatungsten Online www.tungsten-alloy.com | Tel.: 86 592 5129696; Fax: 86 592 5129797;Email:sales@chinatungsten.com |
Tungsten News & Prices, 3G Version: http://3g.chinatungsten.com | Molybdenum News & Molybdenum Price: http://news.molybdenum.com.cn |
Tungsten Radiation Shielding Application in Non-destructive Testing(NDT)
- Details
- Category: Tungsten Information
- Published on Tuesday, 15 December 2015 18:38
Non-destructive testing is a method or relevant means that usually been used without damaging the product structure, without compromising the performance of the product. The detection of products can be divided into two kinds, which included destructive products and non-destructive products, the latter focused on appearance, it means that should be tested one by one, but can be as long as qualified. For the former usually takes some samples, and focuses on the intrinsic quality of the designated products suspected inherent defects were dissected. Since the destructive testing will eventually be used at the cost of a product, so using non-destructive testing method to test products can balance that, i.e., it can certainty not destruct the product and handle the intrinsic quality of the product.
Non-destructive testing(NDT) methods may rely upon use electromagnetic radiation, sound and inherent properties of materials to examine samples, which includes examining the materials external surfaces in details by microscope. Although samples preparation techniques for matallographic, optical microscope and electron microscope are generally destructive as the surfaces must be made smooth through polishing or the samples must be electron transparent in thickness. Therefor the interior of samples can only be examined with penetrating electromagnetic radiation, such as X-rays or 3D X-rays. Therefor,Tungsten radiation shielding could be used effectively for radiation protection from the harm radiation when testing the defects of products by X-ray or 3D X-ray.
PS:TUNGSTEN ALLOY RADIATION SHIELDING
Tungsten Alloy Supplier: Chinatungsten Online www.tungsten-alloy.com | Tel.: 86 592 5129696; Fax: 86 592 5129797;Email:sales@chinatungsten.com |
Tungsten News & Prices, 3G Version: http://3g.chinatungsten.com | Molybdenum News & Molybdenum Price: http://news.molybdenum.com.cn |
Tungsten Alloy Radiation Shielding Advantage
- Details
- Category: Tungsten Information
- Published on Tuesday, 15 December 2015 18:31
Experts find that radiation exposures could be reduced by maxing shielding. The density of tungsten alloy radiation shielding materials is related to its radiation stopping ability. Higher density means better stopping and absorbing radiation ray ability.
Due to a higher density that most other materials,tungsten radiation shielding has a much higher ability of absorbing and stopping almost rays than other metals, such as the traditional radiation shielding-lead. Tungsten radiation shielding has greater linear attenuation of gamma radiation and means that less is required for equal shielding. Altematively equal amounts of tungsten shielding provide diminished exposure risks than equivalent lead. So, tungsten alloy is the right and suitable material for radiation protection, as its combination of high density, good machinability, good corrosion resistance and high radiation absorbing ability. Besides, tungsten alloy is a kind of toxic pollution material, it would be better for environmentally friendly.
Tungsten Alloy Supplier: Chinatungsten Online www.tungsten-alloy.com | Tel.: 86 592 5129696; Fax: 86 592 5129797;Email:sales@chinatungsten.com |
Tungsten News & Prices, 3G Version: http://3g.chinatungsten.com | Molybdenum News & Molybdenum Price: http://news.molybdenum.com.cn |
Nano Copper powder of Tungsten Copper Electrode Preparation
- Details
- Category: Tungsten Information
- Published on Tuesday, 15 December 2015 17:10
Compared with traditional powder metallurgy (PM), tungsten copper electrode nano composite material including powder milling, compacting and sintering process, but due to the characteristics of nano particles, there are some differences between traditional powder metallurgy and nano copper powder preparation.
1. Gas Evaporating
Copper evaporates in inert gas atmosphere, then a conflict with an inert gas and the particles, cooling, condensation forming nano copper particles. The forming powder process including 3 stages: one is metal evaporates and produces vapor, another one is metal vapor diffuses in inert gas and nucleation and crystal nucleus growth. The powder particle size is mainly determined by the growth process from the evaporation surface to this temperature region, and this process is affected by evaporation temperature and the pressure and the type of inert gas, the influence of temperature gradients within the device and convection conditions. Metal ultra micro powder with 10nm-1μm can be fabricated by the process parameters controlling. This method is the most direct and effective in metal ultra micro powder fabricating, a company from France uses induction heating to improve the gas evaporating and succeed in fabricating copper ultra micro powder.
2. Plasma
Plasma has high temperature and high reaction speed, you can get a uniform, nano-powder of small particles, easily to achieve mass production, can be prepared almost any nanomaterials. It can be specifically divided into direct current arc (DC), high frequency (RF) and mixture (HP). DC has many advantages, such as simple equipment and operation, high efficiency and wide application, but it will easily melt and evaporate at high temperature, which will pollute the product; RF has no pollution of electrode, high speed of reaction, but its energy utilization rate is lower and instability. HP is combined with DC and RF, which has large space of plasma, high purity, high efficiency and good stability.
Tungsten Copper Supplier: Chinatungsten Online tungsten-copper.com | Tel.: 86 592 5129696; Fax: 86 592 5129797;Email:sales@chinatungsten.com |
Tungsten News & Prices, 3G Version: http://3g.chinatungsten.com | Molybdenum News & Molybdenum Price: http://news.molybdenum.com.cn |
Tungsten Copper Electrode Sintering Mechanism and Densification
- Details
- Category: Tungsten Information
- Published on Tuesday, 15 December 2015 17:08
Tungsten copper has been widely used in electrode (EDM or ECM), electronic packaging materials and some fields because of its high density, strength and excellent thermal and electrical conductivity. Due to the large differences physicochemical property between two metals (tungsten and copper), which called binary psudoalloy, tungsten copper uses powder metallurgy (PM) to manufacture replace casting process. It uses tungsten and copper powder with fine grain and high purity, the general process is: powder milling → mixed → compacting → sintering → infiltration → cold working.
This paper concentrates on analyzing the relation between sintering mechanism and densification of tungsten copper material. Generally, the traditional sintering theory said that if a system intend to achieve higher densification, it should has good wettability and the solid phase can dissolve in the liquid phase and proper amount of liquid phase. According to the relationship of tungsten and copper in the process of sintering, the copper-tungsten binary phase diagram can be drew as follow:
The diagram shows that tungsten copper system belongs to completely insoluble system. In addition, the wettability of copper solution is not so well to tungsten skeleton in common conditions. Recently, more and more researchers and scholars find that tungsten copper powder with nano composite structure has better sintering properties. It is due to tungsten copper compacts in solid phase state, although tungsten copper powder with nano composite structure does not dissolve the segregation. They though it is related with one solid phase sintering and liquid particle rearrangement effects.
Except the cementation of powder particle, densification and the change of constituent of pure metal, there is no dissolve and appear new phase in the process of one solid phase sintering. Then we will use the model of tungsten copper pressed compact to show the varieties of powder in the process of solid phase, which will intuitively describe the relation between sintering mechanism and densification of tungsten copper electrode.
Tungsten Copper Supplier: Chinatungsten Online tungsten-copper.com | Tel.: 86 592 5129696; Fax: 86 592 5129797;Email:sales@chinatungsten.com |
Tungsten News & Prices, 3G Version: http://3g.chinatungsten.com | Molybdenum News & Molybdenum Price: http://news.molybdenum.com.cn |