Nano-cemented Carbide and Traditional Carbide Comparison
- Details
- Category: Tungsten Information
- Published on Thursday, 24 December 2015 17:02
Due to nano-cemented carbide improves the contradictions between the hardness and the toughness which has a remarkable increase in mechanical properties compared with common tungsten carbide. There are two aspects of comparisons between nano-cemented carbide and traditional carbide as follow:
1. Porosity defects
Based on the theory and experience in machining, with the decreasing granularity, the porosity defects decrease and the fracture toughness enhances. Thus, the porosity defects of nano-cemented carbide are lower than traditional tungsten carbide. When the granularity less than 30nm, the granularity of porosity defect will be smaller and the fracture toughness will be remarkably improved.
2. Interface
Compared with traditional carbide, nano-cemented carbide has more interfaces, Crack paths through the hard phase WC interface and Co binder phase interface. In other words, Crack through grain boundaries in nano crystalline increased massively this material, which is indicative of the crack is not a priority but is to advance along the interface by bonding, forming a dense shallow dimple in cemented carbide material. In bond by B / C interface with a lot of broken plastic deformation presence, enhanced by the crack path B / C interface percentage will significantly improve the ability to process fracture, thereby enhancing the overall toughness of nano-carbide materials.
In addition, viewed from the interfacial effect related deformation mechanism, when the grain size to the nanometer level, migration and dislocation motion grains have become relatively difficult, instead of sliding and the proliferation of small-scale grain boundaries, such as changes in grain shape, grain rotation. WC particles covered by nano Co, when the nano crystalline Co called the control phase, corresponding to the mechanical properties of the cemented carbide has occurred. It should be noted that the nano cemented carbide wear than conventional carbide, but it does not follow the traditional mechanism that the wear resistance of tungsten carbide particles increases with the decreasing the granularity.
Tungsten Carbide Supplier: Chinatungsten Online tungsten-carbide.com.cn | Tel.: 86 592 5129696; Fax: 86 592 5129797;Email:sales@chinatungsten.com |
Tungsten News&Tungsten Prices, 3G Version: http://3g.chinatungsten.com | Molybdenum News & Molybdenum Price: http://news.molybdenum.com.cn |
Tungsten Trioxide Reduction Method
- Details
- Category: Tungsten Information
- Published on Thursday, 24 December 2015 16:54

Tungsten Oxide Supplier: Chinatungsten Online www.tungsten-oxide.com | Tel.: 86 592 5129696; Fax: 86 592 5129797;Email:sales@chinatungsten.com |
Tungsten News & Prices, 3G Version: http://3g.chinatungsten.com | Molybdenum News & Molybdenum Price: http://news.molybdenum.com.cn |
Ammonium Paratungstate (APT) Production Conditions
- Details
- Category: Tungsten Information
- Published on Thursday, 24 December 2015 14:31
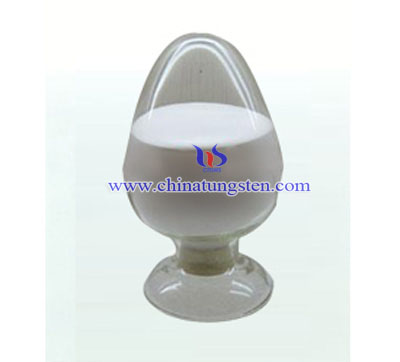
Tungsten Supplier: Chinatungsten Online www.chinatungsten.com | Tel.: 86 592 5129696; Fax: 86 592 5129797;Email:sales@chinatungsten.com |
Tungsten News & Prices, 3G Version: http://3g.chinatungsten.com | Molybdenum News & Molybdenum Price: http://news.molybdenum.com.cn |
Effect of Micro-wave and Ultrasonic on Preparing Process of Ammonium Paratungstate
- Details
- Category: Tungsten Information
- Published on Wednesday, 23 December 2015 18:04
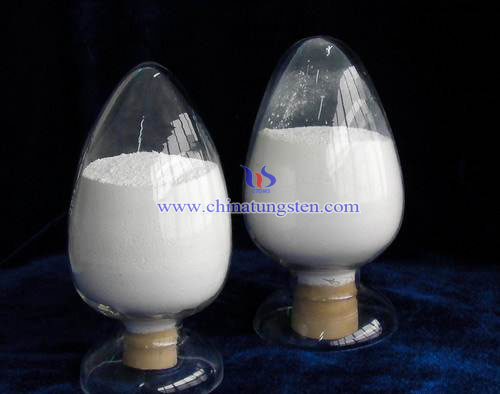
Tungsten Supplier: Chinatungsten Online www.chinatungsten.com | Tel.: 86 592 5129696; Fax: 86 592 5129797;Email:sales@chinatungsten.com |
Tungsten News & Prices, 3G Version: http://3g.chinatungsten.com | Molybdenum News & Molybdenum Price: http://news.molybdenum.com.cn |
Molybdenum Separation from Tungsten during Ammonium Paratungstate Crystallization Process
- Details
- Category: Tungsten Information
- Published on Wednesday, 23 December 2015 18:01

Tungsten Supplier: Chinatungsten Online www.chinatungsten.com | Tel.: 86 592 5129696; Fax: 86 592 5129797;Email:sales@chinatungsten.com |
Tungsten News & Prices, 3G Version: http://3g.chinatungsten.com | Molybdenum News & Molybdenum Price: http://news.molybdenum.com.cn |
Tungsten Alloy Syringe Shielding
- Details
- Category: Tungsten Information
- Published on Wednesday, 23 December 2015 17:25
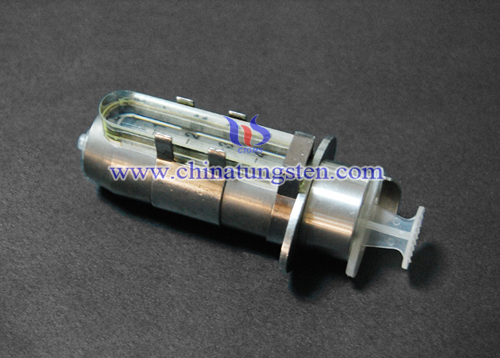
Tungsten Alloy Supplier: Chinatungsten Online www.tungsten-alloy.com | Tel.: 86 592 5129696; Fax: 86 592 5129797;Email:sales@chinatungsten.com |
Tungsten News & Prices, 3G Version: http://3g.chinatungsten.com | Molybdenum News & Molybdenum Price: http://news.molybdenum.com.cn |
Frequent Problems in Tungsten Copper Electrode Machining
- Details
- Category: Tungsten Information
- Published on Wednesday, 23 December 2015 16:58
Tungsten copper electrode machining belongs to powder metallurgy, which has complex process so that there are some frequent problems remain, such as the cracks, the porosity defects and blow hole, etc. Take appropriate measures to solve these issues, which can improve the density of sintered sample.
1. Cracks
This is the most common problem, since the suppression of the pressure too fast, too late to the powder in the gas discharge, the expanded relief elastic aftereffect caused cracks. In addition, the external surface of the sample during sintering of copper will evaporate, leading to the outside of the sample binder phase - copper loss, and prone to cracking. The common solution is to increase the pressure and keep sufficient dwell time to force the gas between grains to discharge favorably. As for the loss of the phenomenon of the copper surface, the current general applications will be used in the method of removing the surface machining section.
2. Blow hole
Besides, tungsten copper composite blow hole from the high temperature copper dissolved in some of the gas can not be effectively excluded during solidification caused, such as vapor and hydrogen. The vapor reacted with the carbon from graphite electrode to form hydrogen (H2) and carbon dioxide (CO2) so that the copper at high temperatures a large amount of dissolved hydrogen can not be completely excluded during solidification, blow holes are formed. A common solution is to avoid all risks of water vapor during sintering, the other is still to gradually increase the pressure in the pressurizing process, and ensure sufficient dwell time, which discharge the gas between grains successfully.
3. Porosity defects
Its production is mainly concentrated in the solidification process and prone to firing in the central part of the sample, which is mainly due to solidification of the central portion of the higher temperature, ambient temperature is relatively low because the site first and then solidified but sucked in part copper formed. In practical application, this kind of defect distributes a little in tungsten copper electrode issues, but it is also difficult to be eliminated.
Tungsten Copper Supplier: Chinatungsten Online tungsten-copper.com | Tel.: 86 592 5129696; Fax: 86 592 5129797;Email:sales@chinatungsten.com |
Tungsten News & Prices, 3G Version: http://3g.chinatungsten.com | Molybdenum News & Molybdenum Price: http://news.molybdenum.com.cn |
Nano-cemented Carbide Description
- Details
- Category: Tungsten Information
- Published on Wednesday, 23 December 2015 16:56
How to balance the wear resistance and the toughness is the important direction of tungsten carbide research. Some new related studies show that when the content of tungsten carbide binder phase remain unchanged, the granularity of tungsten carbide (WC) hard phase decreases to less than 0.8μm, the hardness and toughness have been remarkably improved. And with the decreasing granularity, the effect will be more obvious. Therefore, nano-cemented carbide is becoming a hot spot in the study of tungsten carbide gradually. At present, the general nano-cemented carbide refers to the tungsten carbide less than 250nm, and tungsten carbide with granularity under 30nm is in the stage of research and development, which does not make a further promotion for using.
Nano-cemented carbide gives a new way to deal with the contradictions between the hardness and the strength of tungsten carbide. It has both of high hardness and high strength, which has an advantage in machining some hard and brittle materials compared with tungsten carbide with common structure. For instance, the hardness of nano-cemented carbide WC-Co reaches HRA93, and the transverse breaking strength can be higher than 5000MPa, which greatly satisfies the requirements of modern industries and special material field, especially for tools and mould machining with high loading, high stress, such as PCB (Printed Circuit Board) micro drills or end mills, monolithic cemented carbide drill and some products in high-end fields.
However, there are some problems remain in nano-cemented carbide. Generally, the finer granularity of traditional tungsten carbide, the hardness will increase and the breaking strength will decrease. This is so that when the grain is reduced to a certain extent, such as when the nanometer size, whether the fracture toughness decreased a lot, current research, there are still some uncertainties. Studies have shown that when the carbide grain refinement to the nano scale, its mechanical behavior and performance will have unpredictable change.
Tungsten Carbide Supplier: Chinatungsten Online tungsten-carbide.com.cn | Tel.: 86 592 5129696; Fax: 86 592 5129797;Email:sales@chinatungsten.com |
Tungsten News&Tungsten Prices, 3G Version: http://3g.chinatungsten.com | Molybdenum News & Molybdenum Price: http://news.molybdenum.com.cn |
Radium Radiation And Tungsten Alloy Shielding MaterialsⅡ
- Details
- Category: Tungsten Information
- Published on Wednesday, 23 December 2015 14:30
Tungsten Alloy Supplier: Chinatungsten Online www.tungsten-alloy.com | Tel.: 86 592 5129696; Fax: 86 592 5129797;Email:sales@chinatungsten.com |
Tungsten News & Prices, 3G Version: http://3g.chinatungsten.com | Molybdenum News & Molybdenum Price: http://news.molybdenum.com.cn |
Radium Radiation And Tungsten Alloy Shielding MaterialsⅠ
- Details
- Category: Tungsten Information
- Published on Wednesday, 23 December 2015 14:28
Tungsten Alloy Supplier: Chinatungsten Online www.tungsten-alloy.com | Tel.: 86 592 5129696; Fax: 86 592 5129797;Email:sales@chinatungsten.com |
Tungsten News & Prices, 3G Version: http://3g.chinatungsten.com | Molybdenum News & Molybdenum Price: http://news.molybdenum.com.cn |