When Formaldehyde Meets Tungsten Trioxide Photocatalyst
- Details
- Category: Tungsten Information
- Published on Tuesday, 31 May 2016 18:30
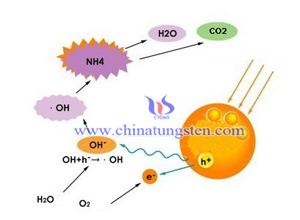
Tungsten Oxide Supplier: Chinatungsten Online www.tungsten-oxide.com | Tel.: 86 592 5129696; Fax: 86 592 5129797;Email:sales@chinatungsten.com |
Tungsten News & Prices, 3G Version: http://3g.chinatungsten.com | Molybdenum News & Molybdenum Price: http://news.molybdenum.com.cn |
Encounter Tungsten Trioxide Photocatalyst
- Details
- Category: Tungsten Information
- Published on Tuesday, 31 May 2016 18:27
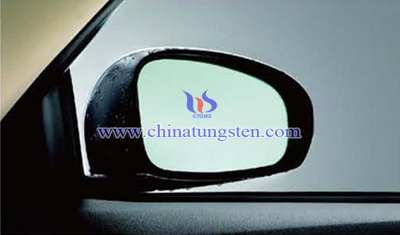
Tungsten Oxide Supplier: Chinatungsten Online www.tungsten-oxide.com | Tel.: 86 592 5129696; Fax: 86 592 5129797;Email:sales@chinatungsten.com |
Tungsten News & Prices, 3G Version: http://3g.chinatungsten.com | Molybdenum News & Molybdenum Price: http://news.molybdenum.com.cn |
Cesium Tungsten Bronze Solid-Phase Synthesis
- Details
- Category: Tungsten Information
- Published on Tuesday, 31 May 2016 17:52
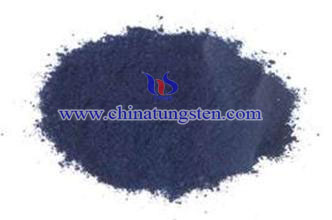
Tungsten Oxide Supplier: Chinatungsten Online www.tungsten-oxide.com | Tel.: 86 592 5129696; Fax: 86 592 5129797;Email:sales@chinatungsten.com |
Tungsten News & Prices, 3G Version: http://3g.chinatungsten.com | Molybdenum News & Molybdenum Price: http://news.molybdenum.com.cn |
Gradient Tungsten Carbide Button Process
- Details
- Category: Tungsten Information
- Published on Tuesday, 31 May 2016 16:58
At present, the main process of tungsten carbide button with gradient structure includes compound hard metal technique, powder layering compression (with different binder content), metal melt impregnation and so on. Compared with these processes, the lack of carbon carbide carburizing treatment method has many advantages, such as better wear resistance and toughness; according to different needs to use different combinations in different parts of the process flexibility and breadth of application have been greatly improved; equipment is simple, easy to operate, relatively low cost.
Carbide composite method uses cemented carbide powder with different particle sizes or particle size distribution is divided into regions having different cemented carbide and use, which can achieve different binder phase content in the cemented carbide sintered body interior. However, such fine-grained portion having higher binder phase content than the coarse-grained portion, there is a small difference in the wear resistance and toughness of different parts; use layered pressed powder (with different content of binder), you need to use a different focus on the binder content of cemented carbide powder was pressed layer by layer. As a result, not only complex process operation, and during sintering compacts easily generated between the different layers of binder content homogenized, so that differences in wear resistance and toughness of the alloy between the different parts are gradually narrowing; The molten metal impregnation method requires special equipment and the need to prepare the metal melt impregnation, and the gradient structure fabricated is limited to the surface area so the range of applications has been greatly limited.
The lack of carbon carbide carburizing treatment, is (the lack of carbon or low carbon) is generated in the carbide structure after sintering carbide mixing at a carbon content below stoichiometric conditions missing carbon phase -η phase. Whether or relative lack of free carbon-carbon phase will have a negative effect on the carbide products. Since η phase is too brittle to form micro-cracks on the surface easily, which causes the fracture of tungsten carbide in the process of using. For the drills with tungsten carbide button, the wear resistance is the primary factor. Tungsten carbide with low content of Co is difficult to be welded owing to welding stress produced may lead to the fracture of alloy. When carbide ball button fixed inserts welded steel body, the contact area between button and steel will appear gap in the drilling process, and gradually expand in the drilling process, the button broken finally, which generally occurs in the bottom surface of button.
Tungsten Carbide Supplier: Chinatungsten Online tungsten-carbide.com.cn | Tel.: 86 592 5129696; Fax: 86 592 5129797;Email:sales@chinatungsten.com |
Tungsten News&Tungsten Prices, 3G Version: http://3g.chinatungsten.com | Molybdenum News & Molybdenum Price: http://news.molybdenum.com.cn |
Gradient Tungsten Carbide Button
- Details
- Category: Tungsten Information
- Published on Tuesday, 31 May 2016 16:56
Gradient tungsten carbide button is also known as tungsten carbide button with gradient structure or multi-phase tungsten carbide buttons. The hardness of tungsten carbide is closely related to the granularity of WC and Co. In general, higher content of WC, the grains finer and the hardness is higher; while higher content of Co, the hardness is correspondly lower. Gradient tungsten carbide button has different hardness distribution due to the uneven structure. And the three layer micro-structure of gradient tungsten carbide buttons has significant differences: Since the WC particles enriched in surface layer, which has a high hardness; the intermediate layer distributes more Co phase, so the hardness is relatively low; internal contains a lot of W phase, the hardness is relatively high.
Throughout the process of carburizing, with the carburizing time goes by, Co alloy surface with constant migration to the alloy of the intermediate layer, the intermediate layer of Co alloy phase content increases with the carburization time. At the same time, the alloy surface WC grains occur grow inside the alloy due to the dissolution when carburizing sintering - precipitation mechanism of action, WC grains have a slight tendency to grow up. Such a sandwich structure can be simultaneously improved surface hardness and internal toughness and can effectively reconcile the contradiction between the wear resistance and the strength of tungsten carbide buttons.
To change the distribution of the alloy binder phase of cemented carbide base cemented carbide substance gradient structure is to take the lack of carbon in the system that is η- phase containing the carburizing process, it was low structure, so that different parts of the materials to achieve different performance. At present, the main process of tungsten carbide button with gradient structure includes compound hard metal technique, powder layering compression (with different binder content), metal melt impregnation and so on.
Tungsten Carbide Supplier: Chinatungsten Online tungsten-carbide.com.cn | Tel.: 86 592 5129696; Fax: 86 592 5129797;Email:sales@chinatungsten.com |
Tungsten News&Tungsten Prices, 3G Version: http://3g.chinatungsten.com | Molybdenum News & Molybdenum Price: http://news.molybdenum.com.cn |
Tephra Contained Tungsten Trioxide Denitration Catalyst
- Details
- Category: Tungsten Information
- Published on Monday, 30 May 2016 18:40
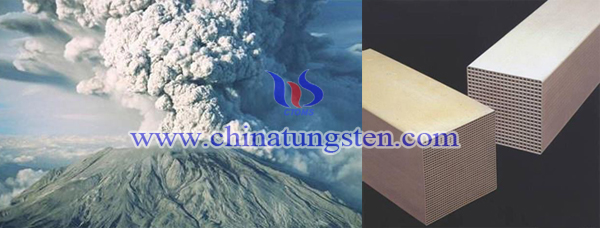
Tungsten Oxide Supplier: Chinatungsten Online www.tungsten-oxide.com | Tel.: 86 592 5129696; Fax: 86 592 5129797;Email:sales@chinatungsten.com |
Tungsten News & Prices, 3G Version: http://3g.chinatungsten.com | Molybdenum News & Molybdenum Price: http://news.molybdenum.com.cn |
Ultrasonic NDT Used in Tungsten Copper Contacts
- Details
- Category: Tungsten Information
- Published on Monday, 30 May 2016 18:38
We introduce how to measure the porosity of powder metallurgy products by ultrasonic NDT based on the principle of pulse reflection, and through metallographic observation of fracture morphology and to further analyze the relationship between the test results and powder metallurgy product defects and related performance. In general, we use ultrasonic detector and supporting direct probe to determine defects burial depth according to the position of the defect wave, and estimate the equivalent defect size according to defect wave amplitude.
For instance, there is an experiment that uses NaCl as a pore-forming agent is mixed with tungsten powder and copper powder, obtained by the method of powder metallurgy tungsten copper contacts with different porosity. By microstructure photograph can be seen that with the increasing amount of pore former, the pore volume occupied by proportionately decrease, lower porosity means relatively dense structure and the loose structure has higher porosity. And then analyze based on the width of the peak intensity of different porosity defects resulting waves and waves of difference.
The sample with pores small and few, due to the pore size is smaller than the wavelength of ultrasound, which can not form scattering. At this time only by the noise signal itself affected by the material of matrix, and the ultrasonic scattering is weak, the waveform is smoother; on the contrary, the coarser pores and higher porosity will form the intensive scattering signal and the waveform will be sharper. Furthermore, with the increase of open porosity, defect wave peak will be significantly reduced. This is due to the absorption will increase with the increasing open porosity rate, sound waves encounter defects reflected sound waves to reduce the intensity of the inevitable, the peak value decreases correspondly. And there is a certain relationship between the speed of sound and the opening rate and hardness of the sample. With the sound velocity decreases, the opening rate increases, the density decreases, the hardness decreases. As a result of increasing amount of pores, the absorption of ultrasonic enhanced, thus the speed of sound decreased. The severe plastic deformation will be affected by increasing porosity. However, materials of different elastic module are different, need to draw the curve separately.
In a word, Ultrasonic nondestructive testing the scattering wave waveform can reflect the tungsten copper contacts, and other powder metallurgy products and the number of pores in the state to some extent. Scattered wave is smoother, no obvious ups and downs, which indicate that the porosity of the material is lower, and may be less than the ultrasonic wavelength; or scattered wave signal messy and there is significant ups and downs, it indicates the porosity defects is more. In addition, nondestructive has certain linear relationship between the detected speed of sound and material porosity. Reducing the speed of sound material represents the increase in porosity, at the same time can objectively reflect the overall performance of other materials.
Tungsten Copper Supplier: Chinatungsten Online tungsten-copper.com | Tel.: 86 592 5129696; Fax: 86 592 5129797;Email:sales@chinatungsten.com |
Tungsten News & Prices, 3G Version: http://3g.chinatungsten.com | Molybdenum News & Molybdenum Price: http://news.molybdenum.com.cn |
Tungsten Copper Contact —Ultrasonic NDT
- Details
- Category: Tungsten Information
- Published on Monday, 30 May 2016 18:37
Tungsten copper contact is also known as tungsten copper electrical contact or tungsten copper contact tip, which is a kind of psudoalloy that consist of W and Cu two kinds metals of immiscible and without the formation of intermetallic compounds. Consequently, it not only has high hardness, high melting point, high strength, low coefficient of thermal expansion and excellent wear resistance and corrosion resistance of W, but also has perfect electrical and thermal conductivity and plasticity of Cu. And it has been played an important role in some high-voltage switch, breaker, and instrument components.
Currently, preparation of tungsten copper contacts is mainly used in PM (powder metallurgy) technology, the corresponding method used for the performance testing, such as the density, the hardness, the compressive strength, the tensile strength and micro-structure, etc., will have some damages on the integrity of tungsten copper products and lead to failure. And these tools to test for products in large quantities can only do a certain proportion of sample, which is difficult to have some representation. If the unqualified tungsten copper contacts undetected used in actual production is likely buried security risk, both for production or personal safety is extremely unfavorable. So the relevant researchers use Non-destructive testing techniques to measure and evaluate the mechanical properties of tungsten copper related products.
Ultrasonic NDT (Non-destructive Testing) is a kind of process that ultrasound can penetrate deep into the use of a metallic material, by entering a cross-sectional another cross-sectional; edge reflection occurs at the interface characteristics of the parts to check for defects. When the ultrasonic beam from the surface of the part by the probe pass to the metal inside encounter defects and Part underside of the reflected wave occurs, respectively, form a pulse waveform on the screen, based on these pulse waveforms to determine the location and size of the defect. Compared with other detecting methods, Ultrasonic NDT has many advantages, such as:
1. Ultrasound has perfect penetration ability, low transmission loss and the probing depth of up to several meters;
2. High sensitivity, it can be found with the diameter of the air-based reflectance 0.1-1mm equivalent reflector;
3. Accurate positioning, to assume the shape and the size are also more accurate;
4. Convenient in operation and it is suitable for the most materials;
5. The entire testing process will not cause environmental pollution, no harm to the human body completely.
Tungsten Copper Supplier: Chinatungsten Online tungsten-copper.com | Tel.: 86 592 5129696; Fax: 86 592 5129797;Email:sales@chinatungsten.com |
Tungsten News & Prices, 3G Version: http://3g.chinatungsten.com | Molybdenum News & Molybdenum Price: http://news.molybdenum.com.cn |
Automobile Exhaust Denitration Catalyst Uses Tungsten Trioxide
- Details
- Category: Tungsten Information
- Published on Monday, 30 May 2016 18:36
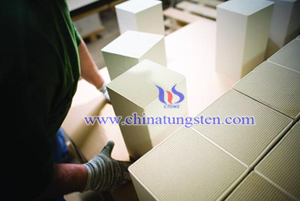
Tungsten Oxide Supplier: Chinatungsten Online www.tungsten-oxide.com | Tel.: 86 592 5129696; Fax: 86 592 5129797;Email:sales@chinatungsten.com |
Tungsten News & Prices, 3G Version: http://3g.chinatungsten.com | Molybdenum News & Molybdenum Price: http://news.molybdenum.com.cn |
Tungsten Bronze Metaniobate Lead High Temperature Ceramics Preparation
- Details
- Category: Tungsten Information
- Published on Monday, 30 May 2016 15:48
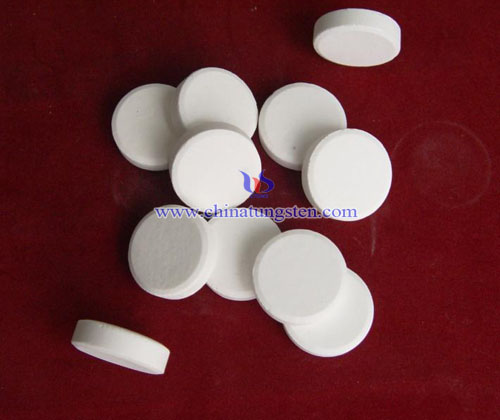
Tungsten Oxide Supplier: Chinatungsten Online www.tungsten-oxide.com | Tel.: 86 592 5129696; Fax: 86 592 5129797;Email:sales@chinatungsten.com |
Tungsten News & Prices, 3G Version: http://3g.chinatungsten.com | Molybdenum News & Molybdenum Price: http://news.molybdenum.com.cn |