Tungsten Trioxide Photocatalyst Coating
- Details
- Category: Tungsten Information
- Published on Thursday, 02 June 2016 18:32
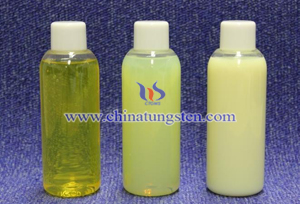
Tungsten Oxide Supplier: Chinatungsten Online www.tungsten-oxide.com | Tel.: 86 592 5129696; Fax: 86 592 5129797;Email:sales@chinatungsten.com |
Tungsten News & Prices, 3G Version: http://3g.chinatungsten.com | Molybdenum News & Molybdenum Price: http://news.molybdenum.com.cn |
Design of Tungsten Heater for Vacuum Coating
- Details
- Category: Tungsten Information
- Published on Thursday, 02 June 2016 11:03
The main raw material of tungsten heater is tungsten filament. Due to its high melting point and strong corrosion resistance, it is widely used in vacuum gilding, aluminum and other decorative items. Vacuum coating is a kind of technology for making film by physical methods. The technology was developed in the 1930s, once it has been introduced, it enjoyed a great popular. This technology was first used in the production of optical lenses, such as telescope disk for sailing. Later it extended to other functional film, music aluminum, decorative coating and surface modification, such as machine tool coating, change processing hardness. Tungsten heater can be twisted into a single strand or multi-strand shape in according with different applications.
Firstly, before designing the appearance of tungsten heater, hank knotting and the heater surface should keep clean, bright without any cracks and visible contamination of impurities, such as oxides and filament drawing lubricants. If there exist impurities on its surface, it will affect the quality of vacuum and influence on the free evaporation rate of the metal, which will reduce the effect of vacuum coating. For the superficial area of tungsten, under the premise of constant power, it should be as large as possible. Size of superficial area is in direct proportion to rate of evaporation, the larger the area, the faster the evaporation. What’s more, it has a direct impact on the quality of vapor deposition and the infiltration flow performance of aluminum.
If it is a single strand tungsten filament, people should choose a relatively thin one whose appearance diameter should be between 0.5 ~ 0.8mm. In the design of the inner diameter of the spiral time, people need to consider whether aluminum can be put in it for many times. On the other hand, it should be ensure that the heat can be effectively concentrated. The pitch of screw thread should be designed for concentrating the heat and the appearance tension of molten aluminum in order to avoid droplet phenomenon.
Tungsten Metals Supplier: Chinatungsten Online www.tungsten.com.cn | Tel.: 86 592 5129696; Fax: 86 592 5129797;Email:sales@chinatungsten.com |
Tungsten News & Prices, 3G Version: http://3g.chinatungsten.com | Molybdenum News & Molybdenum Price: http://news.molybdenum.com.cn |
TIG Rods and Tungsten
- Details
- Category: Tungsten Information
- Published on Wednesday, 01 June 2016 18:16
In TIG welding, shielding gas is necessary, usually using argon, which is running through the torch. Besides, you have an electrode that's made of tungsten, which is extremely hard steel that can stand up to high heat. And depending on the weld metal, the tungsten electrode will require a special alloy ingredient added to provide a stable arc, which helps produce an uncontaminated weld.
If that tungsten electrode weren't enough to wrap products’ head around, you'll also be welding with filler rod in your other hand. That makes three consumables that get used up and replaced periodically.
Tungsten Electrodes
In generally, the tungsten electrode used in TIG welding is not a consumable, since it's not meant to serve as filler rod. An experienced welder can make a tungsten electrode last a long time. On the contrary, a fresh may go through one seven-inch electrode every week. The electrodes are packaged in various quantities ten packs are the most popular. These come in seven or three-inch lengths, which correspond to the two standard tips available with TIG torches. The electrodes are also sold in a range of diameters, just like stick welding.
Tungsten electrode has many types. In order to distinguish one from another, a color code has been developed.
For example, pure tungsten electrode (EWP) is used primarily for AC welding of aluminum and magnesium at low currents. The tip of it must be balled before using. (ISO = W)
1.5% Lanthanated tungsten electrode (EWla-1.5) is a general purpose electrode used for steel and stainless steel at a wide range of currents. It often replaces thoriated tungsten electrode. (ISO = WL15)
2% ceriated tungsten electrode (EWTh-2) can achieve high currents with good arc stability, which is another substitute for thoriated tungsten electrode. (ISO = WC20)
2% thoriated electrode (EWTh-2) is an expensive and radioactive electrode. Use care in grinding (i.e. wear a dust mask), keep your skin covered and avoid contact with the metal when it's heated. (ISO = WT20)
2% zirconiated tungsten electrode (EWZr-2) is usually used in AC welding. It is preferred in situations where resistance to contamination is paramount. The tip of the tungsten is balled before using. (ISO = WZ3)
TIG Filler Rods
Filler rods for TIG welding are taken by a second hand as the first holds the tungsten torch. These rods typically come in 3-foot lengths and are packed in 10 or 50-pound boxes (or tubes). A welder's choice of diameter ranges from 1/16" to 1/4". Since the composition of the filler rod is the same as MIG, the same products are sold for TIG welding, under the category "TIG cut lengths.
Tungsten Metals Supplier: Chinatungsten Online www.tungsten.com.cn | Tel.: 86 592 5129696; Fax: 86 592 5129797;Email:sales@chinatungsten.com |
Tungsten News & Prices, 3G Version: http://3g.chinatungsten.com | Molybdenum News & Molybdenum Price: http://news.molybdenum.com.cn |
The Best Tungsten Electrode for TIG Welding Aluminum
- Details
- Category: Tungsten Information
- Published on Wednesday, 01 June 2016 18:13
As we know, there are many different type TIG machines around. The TIG machines some offers inverter technology and all offers varying degrees of power, so it can be tough to figure out the best tungsten electrode for TIG welding aluminum. With that in mind, what is the best tungsten electrode for TIG welding aluminum?
The tungsten electrodes you choose mainly depend on your particular TIG machine, and the thickness of the metal you’re welding. Besides, the settings you have available. Here are a few tips and general rules that will help you to choose the right tungsten electrode for TIG welding aluminum. Keep in mind that some of these tips may change based on your particular machine.
Some welders have a particular favorite kind of tungsten. They prefer to use thoriated or pure tungsten electrode, but each kind of tungsten electrodes listed above can work if welders have the right settings and the right application.
The following electrodes can be used for TIG welding aluminum, including 2% ceriated tungsten electrode (on AC), 2% lanthanated tungsten electrode (AC and DC), 1.5 lanthanated tungsten electrode(AC and DC), 2% thoriated tungsten electrode (DC only)and pure tungsten electrode (DC only), but there are a few rules and caveats that should follow.
Firstly, don’t use pure tungsten on the AC side since it will ball up, especially if you’re using an inverter.
Secondly, choose the right electrode size for TIG welding aluminum. One of the most common mistakes for welders working with aluminum is they choose an electrode that is too small. You often need to consider a 1/8” electrode for welding aluminum in order to get enough heat and to create a stable arc. As we know, the size of electrode is too small will create a sloppy weld, which is bad for products quality.
If you’re working on AC with a lanthanated electrode, you may be able to use a 3/16” or 3/32” electrode. The key is to match your electrode choice and size with the settings and the project.
While each tungsten electrode has its advantages and disadvantages, one of the safest bets is 2% lanthanated tungsten electrode, which is ground to a point with a flattened tip. Many welders prefer this electrode for both AC and DC because it holds up well and provides a stable arc for a clean weld.
Tungsten Metals Supplier: Chinatungsten Online www.tungsten.com.cn | Tel.: 86 592 5129696; Fax: 86 592 5129797;Email:sales@chinatungsten.com |
Tungsten News & Prices, 3G Version: http://3g.chinatungsten.com | Molybdenum News & Molybdenum Price: http://news.molybdenum.com.cn |
Hydrogen Tungsten Bronze and Fuel Cell Cathode Catalyst
- Details
- Category: Tungsten Information
- Published on Wednesday, 01 June 2016 18:11
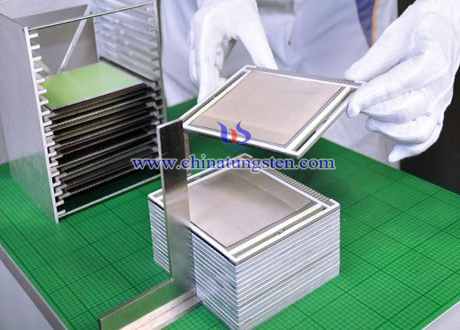
Tungsten Oxide Supplier: Chinatungsten Online www.tungsten-oxide.com | Tel.: 86 592 5129696; Fax: 86 592 5129797;Email:sales@chinatungsten.com |
Tungsten News & Prices, 3G Version: http://3g.chinatungsten.com | Molybdenum News & Molybdenum Price: http://news.molybdenum.com.cn |
Tungsten Oxide Preparing Tungsten Disulfide Lubricant
- Details
- Category: Tungsten Information
- Published on Wednesday, 01 June 2016 17:55
Tungsten disulfide is a kind of solid inorganic lubricant material. The appearance and physical property is similar to calcium disulfide. The physical and chemical property of tungsten disulfide shows that it can not only be used in the regular lubricant, but also can be applied under certain high temperature, low temperature, high load, high vacuum and corrosion circumstances. It can be used with powder appearance, or can be mixed with lubricant, graphite, metal powder or plastic as compound materials.
With the development of scientific technology, the requirement for lubricant material has also been promoted. To solve the lubricant problems, tungsten disulfide has draw people’s attention like other innovative materials. Although there are many methods to prepare tungsten disulfide, the thorough material about its preparing method is rare. The method using tungsten oxide to prepare high purity tungsten disulfide is easy to operate and can assure the quality of the product.
Preparing method:
Raw material: Tungsten oxide (WO3); Sulfuric acid: 20% aqueous solution; Sodium sulfate: 20% aqueous solution.
(1) Adding a certain amount of tungsten oxide into tray, then press it properly. Put the tray into the middle of tubular reactor, connect the conduit, seal the gaps between all interfaces with wax or stop-leak compound. Open the outlet valve of container of sulfuric acid and sodium sulfide, the hydrogen sulfide gas is obtained.
(2) Lead hydrogen sulfide from the bottom of container. After the outlet gas of the container is non-explosive gas (use tube to gather gas to test), clean the bottle by connecting sodium hydroxide container.
(3) Adjust flow rate of sulfuric acid and sodium sulfide solution to keep the pressure of system under 3.92~4.90kPa. Charge with electricity, upper the temperature to a certain value, and keep it stable, lower the temperature to 400℃ when input hydrogen sulfide. Then stop inputting and keep it to room temperature.
Under high temperature, tungsten oxide reacts with hydrogen sulfide, tungsten disulfide with chemical formula WS1.98一WS2.12 is obtained. This method is easy to operate and stable.
Tungsten Oxide Supplier: Chinatungsten Online www.tungsten-oxide.com | Tel.: 86 592 5129696; Fax: 86 592 5129797;Email:sales@chinatungsten.com |
Tungsten News & Prices, 3G Version: http://3g.chinatungsten.com | Molybdenum News & Molybdenum Price: http://news.molybdenum.com.cn |
Tungsten Disulfide MSDS
- Details
- Category: Tungsten Information
- Published on Wednesday, 01 June 2016 15:58
Material safety data sheet(MSDS) of tungsten disulfide(WS2):
Chemical Name: Tungsten Disulfide
Trade Name/Synonyms: Tungsten disulfide; Tungsten disulphide
Chemical Family: Refractory metal sulfide
CAS Number: 12138-09-9
Formula: WS2
Molecular Weight: 248.02
PHYSICAL DATA
Appearance & Odor: Grayish-black powder, no odor
Boiling Point: N/A
Vapor Pressure: (mm HG) N/A
Vapor Density: (air=1) N/A
Solubility in Water: Insoluble
Specific Gravity: (H2O=1) 7.4
Percent Volatile by Volume: 0
Evaporation Rate: N/A
How Best Monitored: Air sample
NON-HAZARDOUS INGREDIENTS
Material: Tungsten disulfide
Percent by Weight: 100
ACGIH TLV: 5MG/M3
HEALTH HAZARD DATA
ROUTES OF EXPOSURE: material can be inhaled, swallowed, or come in contact with the skin or eyes.
EFFECTS OF OVEREXPOSURE: dust and inhalation may cause mild irritation of the nose and throat. With the exception of TOW Russian studies that found early signs of pulmonary fibrosis in some workers exposed to tungsten trioxide, tungsten metal, and tungsten carbide, most studies have shown that insoluble tungsten compounds to be toxicologically inert. Skin and eye contact may cause irritation due to the abrasiveness of the dust. Recent scientific evidence indicates no adverse effects are likely from accidental ingestion of small amounts of the material.
EMERGENCY AND FIRST AID PROCEDURES: inhalation- if symptoms of pulmonary involvement develop, remove from exposure and seek medical attention; skin contact- if irritation occurs, thoroughly wash affected area with mild soap and water and prevent further contact, contact medical help if irritation persists; eye contact- if irritation occurs, flush with copious amounts of a water, contact medical help if irritation persists; ingestion- if substantial quantities are swallowed, give person (if conscious) a large quantity of water to drink, induce vomiting, and seek medical attention; carcinogenic assessment- NTP Annual Report, IARC monographs, et. al.) this material has not been identified as a known or suspected carcinogen by NTP, IARC, or OSHA.
FIRE & EXPLOSION HAZARD DATA
Flash Point: N/A
Flammability Limits: N/A
No fire hazard, use extinguishing agents suitable for surrounding fire. Special procedures: use a self-contained breathing apparatus to prevent inhalation of dust, mist or fumes that may be generated during fire fighting activities. No unusual fire or explosion hazards.
REACTIVITY DATA
Stability: Stable
Conditions to avoid: N/A
Incompatible Materials to Avoid: Contact with strong acids may generate hydrogen sulfide.
Hazardous Decomposition Products: Oxides of sulfur and tungsten may be evolved at extreme temperatures.
SPILL & LEAK PROCEDURES
If spilled or released- ventilate area of spill, clean-up using methods which avoid dust generation, such as vacuuming with appropriate filter, wet dust mop, or wet clean-up. If dust is generated, use approved niosh respirator. Disposal-dispose of in accordance with appropriate federal, state, and local regulations respiratory protection- use an appropriate niosh approved
respirator if airborne dust levels exceed the tlv, appropriate requirements set forth in 29 cfr 1910.134 should be met ventilation- use local exhaust which is adequate to limit exposure levels below tlv gloves-gloves are recommended eye protection recommended special precautions.
HANDLING AND STORAGE: Maintain good house keeping procedures to prevent acumulation of dust; use clean-up methods which minimize dust generation.
OTHER PRECAUTIONS:
wash throroughly after handling and before eating, smoking, and end of work shift; do not shake clothing to remove dust; avoid inhalation, ingestion, and direct skin contact.
Tungsten Oxide Supplier: Chinatungsten Online www.tungsten-oxide.com | Tel.: 86 592 5129696; Fax: 86 592 5129797;Email:sales@chinatungsten.com |
Tungsten News & Prices, 3G Version: http://3g.chinatungsten.com | Molybdenum News & Molybdenum Price: http://news.molybdenum.com.cn |
Tungsten Copper Sheet Sintering Process
- Details
- Category: Tungsten Information
- Published on Wednesday, 01 June 2016 14:55
Tungsten copper materials perfectly combine high hardness, high melting point, high strength, low coefficient of thermal expansion and excellent wear and corrosion resistance of W with high plasticity and excellent thermal and electrical conductivity of Cu. Furthermore, it has another advantage that other material difficult to achieve: there is a great difference in the melting point between W and Cu (W-3380℃, Cu-1083℃), at a temperature exceeding the melting point of Cu, copper evaporation can take away the most of heat and keep the matrix working normal. So it is also called sweating heat sink material.
With the development of electronic devices now tend to be miniaturized and high-power, heating and cooling is an inevitable process of the devices. Tungsten copper alloy with superior performance to meet the cooling requirements of high-power devices, and it may also adjust the coefficient of thermal expansion, and microelectronics devices of different semiconductor materials are well matched connection, so as to effectively prevent heat stress thermal fatigue damage caused. Therefore, in some LSI (large-scale integrated circuit) and high-power microwave devices, tungsten copper sheet has a broad prospect in electronic packaging substrates, heat sinks, connectors and other microelectronic housing material.
Theoretically, as heat sink material, tungsten copper sheet has a strict requirement of theoretical density, usually higher than 98% and the thickness less than 1mm, which conventional PM (powder metallurgy) is difficult to meet the increasing requirements. Recent years, the relevant researchers and scholars have studied in ultra-fine powder fabrication, densified process and alloy molding technology. For tungsten copper sheet sintering process, Surface wettability of densification, microstructure and properties of the alloy a great impact, and tungsten copper two-phase sintering temperature depends on the wettability of tungsten and copper two phases. Through the experiment can be found that sintered at 1200 ℃, tungsten particles agglomerate, with copper and tungsten particles did not enter the group, there are many small voids between the particles of tungsten and copper group phase, which indicates Cu has poor wettability at this time; when sintering temperature up to 1300℃, the wettability of Cu has improved, so it can immersed in the tungsten particles, which is beneficial for flowability and rearrangement of W grains. With the increase of sintering temperature, then Cu phase occurs gathering, that is copper pool of depression phenomenon, inter tungsten particles re-agglomerate and grow interconnected to provide the conditions so that the density of tungsten copper alloy in high temperature sintering stage quickly increase.
Tungsten Copper Supplier: Chinatungsten Online tungsten-copper.com | Tel.: 86 592 5129696; Fax: 86 592 5129797;Email:sales@chinatungsten.com |
Tungsten News & Prices, 3G Version: http://3g.chinatungsten.com | Molybdenum News & Molybdenum Price: http://news.molybdenum.com.cn |
Tungsten Bar and Doping Bubble
- Details
- Category: Tungsten Information
- Published on Wednesday, 01 June 2016 10:16
In the early 1900s, the United States developed a high temperature anti-drooping tungsten wire. Doping (semiconductor), intentionally introducing impurities into an extremely pure semiconductor to change its electrical properties. After many tests, it is found that its sagging resistance is due to a small amount of silicon, aluminum, potassium oxide in the tungsten oxide before reduction. Among them, the researchers proposed a "bubble statement." "Bubble statement" holds the view that the dopant is prone to have the doping effect in the first reduction process, and then form the doping bubble during the vertical melting. These bubbles will be stretched, annealed in follow-up processes. Then it will become small holes arranged in clusters, but these holes may have an impact on the cross motion of tungsten filament grain boundaries during the second recrystallization, or even hinder its movement, eventually leading to the tungsten wire forming a especial recrystallized grain structure, which would make wolfram filament have a high temperature sagging resistance. Anti-sagging tungsten filament is mainly used for incandescent, fluorescent and other light bulb and the heat wire of tube. Anti-sagging tungsten wire of automobile and motorcycle lights is one of the most important applications. There are many methods to detect its anti-sagging performance, the most common ways include high-temperature creep test, high temperature bending drop method (V-shaped test), etc.
Through the preliminary calculation of the test, it can be concluded that the effective conductive cross section area of tungsten bar would significantly reduced if content of potassium increasingly. Because residual potassium will evaporate into gas in a sintering process, and then produce large amounts of adulterate bubble, resulting in a reduction of its effective conducting cross-sectional area. When potassium content is lower than 70ppm, change of density of adulterate bubbles is more pronounced, it would reduced rapidly as decreasing of potassium content, which will reduce the high temperature sagging resistance of tungsten filament.
Tungsten Metals Supplier: Chinatungsten Online www.tungsten.com.cn | Tel.: 86 592 5129696; Fax: 86 592 5129797;Email:sales@chinatungsten.com |
Tungsten News & Prices, 3G Version: http://3g.chinatungsten.com | Molybdenum News & Molybdenum Price: http://news.molybdenum.com.cn |
Tungsten Bar - Indirect Heating Sintering
- Details
- Category: Tungsten Information
- Published on Wednesday, 01 June 2016 10:10
Tungsten bar can be used for the manufacturing process of tungsten filament. So far, most factories adopt vertical sintering method. Such method is working in a water cooling bell, but there is no equipment to keep warm in this bell. Then a large amount of thermal energy generated by electric power are used for heating water, but hot water need cooling device for cooling, this process will consume a lot of power. The temperature field gradient of this method is relatively large, resulting in the density, grain size and degree of porosity of the same batch of tungsten are different. What’s more, density of both ends of the billet is very low, so they must be removed, so that it would waste a part of resources.
To a certain degree indirect heating sintering method can solves these drawbacks, it also improve their quality of billet, which has an excellent energy saving effect. In 1976, an intermediate frequency (IF) induction sintering furnace had been already developed, this device will be able to meet the conditions of uniform temperature field for sintering the tungsten bar. It adopts a tungsten tube as a heating element, and jargonia is a heat insulating material. A sealing member consists of them, the heat energy generated by electrical energy will be surrounded by the sealing member, and concentrated in the middle of the furnace for sintering the wolfram bar.
Horizontal can keep consistent with vertical properties of the bars prepared by this method. In addition, this kind of bars would have a uniform and thin microstructure. The density of both sides of billet does not have a great difference with other parts, so they are not need to be removed. IF induction furnace indirectly heating tungsten products would ensure the stability of its quality, and the more important point is that it can save resources, which plays an important role in environmental protection.
Tungsten Metals Supplier: Chinatungsten Online www.tungsten.com.cn | Tel.: 86 592 5129696; Fax: 86 592 5129797;Email:sales@chinatungsten.com |
Tungsten News & Prices, 3G Version: http://3g.chinatungsten.com | Molybdenum News & Molybdenum Price: http://news.molybdenum.com.cn |