Zr Affects Tungsten Trioxide Denitration Catalyst
- Details
- Category: Tungsten Information
- Published on Monday, 23 May 2016 17:09
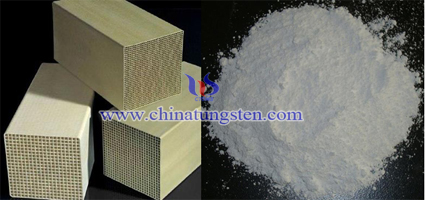
Tungsten Oxide Supplier: Chinatungsten Online www.tungsten-oxide.com | Tel.: 86 592 5129696; Fax: 86 592 5129797;Email:sales@chinatungsten.com |
Tungsten News & Prices, 3G Version: http://3g.chinatungsten.com | Molybdenum News & Molybdenum Price: http://news.molybdenum.com.cn |
Ammonium Tungsten Bronze Nanoparticles Preparation
- Details
- Category: Tungsten Information
- Published on Monday, 23 May 2016 16:04
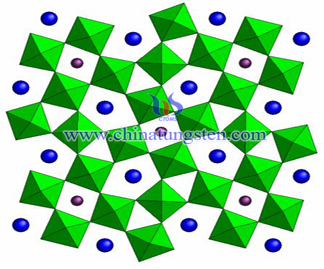
Tungsten Oxide Supplier: Chinatungsten Online www.tungsten-oxide.com | Tel.: 86 592 5129696; Fax: 86 592 5129797;Email:sales@chinatungsten.com |
Tungsten News & Prices, 3G Version: http://3g.chinatungsten.com | Molybdenum News & Molybdenum Price: http://news.molybdenum.com.cn |
Tungsten Copper Electrode — Chemical Co-precipitation (2/2)
- Details
- Category: Tungsten Information
- Published on Monday, 23 May 2016 15:56
The definition of chemical co-precipitation is that in solution mixing materials with different chemical compositions were prepared precursor precipitate mixture added a suitable precipitating agent, then the precipitate is dried or calcined, to thereby obtain the corresponding powder particles. It has two advantages, one is a nano-powder materials can be obtained directly by chemical composition homogeneous solution in a variety of chemical reactions, and the other is easy to prepare small particle size and distribution of nano-powder materials.
The experiment use ammonium tungstate, copper sulfate pentahydrate and concentrated nitric acid as raw materials. The specific operation of concentrated nitric acid in a copper nitrate solution was added with stirring, and then the mixed solution was added a solution of ammonium tungstate, a magnetic stirrer in the chemical co-precipitation reaction; After 1h the reaction solution was removed and the precipitate was placed in a muffle furnace firing 2h, to obtain tungsten copper composite oxide powder; after reduction by hydrogen obtained tungsten copper composite powder; then the tungsten-copper composite powder is extruded to form a green with a certain density and strength, ultra-fine grain was finally sintered tungsten copper alloy products.
Tungsten copper powder is polygon and the granularity is between 30nm – 50nm. Cu into a network-like structure of the W particles are bonded together in an approximation polygon and evenly distributed. This is because the raw material for preparing tungsten-copper composite powders of tungsten and copper salt solution, the distribution of the particles in the solution itself more evenly in the strong magnetic stirring effect, will make the precursor powder to retain the basic solution mixed state molecular level. And calcination and hydrogen reduction process in low temperature effectively inhibited the growth W grains. In addition, the initial structure of the powder is the oxides of tungsten and copper, their mutual isolation is not conductive to the growth of tungsten oxide particles, but is beneficial for evenly dispersed tungsten copper composite powder. From the fracture morphology, W grain evenly distributed in the Cu phase, forming larger dimples around, Cu phase has continuous web-like distribution along with the W grains. From the structure, with the increase in the sintering temperature, tissue distribution is more uniform, the porosity is also decreased. From the properties of alloy, Tungsten-copper composite compacts during sintering two-phase distribution, effective at power-conduction electron-average running speed increases, the conductivity also increases; complete copper network-like structure decrease the contact area of coarse W grains, which is difficult to form necking and beneficial for thermal conduction.
Tungsten Copper Supplier: Chinatungsten Online tungsten-copper.com | Tel.: 86 592 5129696; Fax: 86 592 5129797;Email:sales@chinatungsten.com |
Tungsten News & Prices, 3G Version: http://3g.chinatungsten.com | Molybdenum News & Molybdenum Price: http://news.molybdenum.com.cn |
Tungsten Copper Electrode — Chemical Co-precipitation (1/2)
- Details
- Category: Tungsten Information
- Published on Monday, 23 May 2016 15:54
Tungsten copper is a kind of psudoalloy, which is composed of W with body-centered cubic structure (bcc) and Cu with face-centered cubic (fcc) structure and they are immiscible or not forming intermetallic compound. It not only has high hardness, high strength, low coefficient of thermal expansion and excellent wear resistance and corrosion resistance of W, but also has excellent electrical conductivity, thermal conductivity and plasticity, which can be widely used in some electrical contact materials or electrode materials. Generally, the basic process is: mixing → forming → infiltration, sintering → post-processing.
But tungsten copper electrode fabricated by conventional process, regardless of liquid-phase sintering or solid-phase sintering, the relative density of tungsten copper products produced will lower than 98% because of the wetting angle and the insoluble W in liquid Cu. Although the heating process and re-pressing or re-sintering can remarkably improve this situation, the cost is increasing and the overall efficiency is decreasing. Furthermore, in the sintering process will happen inevitably growth of tungsten grains, which would make it difficult to meet the performance of the market demands tungsten copper electrode material now.
In order to improve the sintering density of tungsten copper electrode and other tungsten copper composite materials, relevant researchers use activated sintering by adding additives. However, the activator can significantly improve the density of tungsten-copper alloy, it will also have some effects on the electrical and thermal conductivity, which is not suitable for the occasions has high demands on electrical and thermal conductivity. So chemical co-precipitation of copper tungsten nano composite powder prepared by reduction combined with hydrogen, by pressing and sintering process to obtain a high-performance compact tungsten copper alloy electrodes become a new hotspot.
Tungsten Copper Supplier: Chinatungsten Online tungsten-copper.com | Tel.: 86 592 5129696; Fax: 86 592 5129797;Email:sales@chinatungsten.com |
Tungsten News & Prices, 3G Version: http://3g.chinatungsten.com | Molybdenum News & Molybdenum Price: http://news.molybdenum.com.cn |
What Is Tungsten Bar?
- Details
- Category: Tungsten Information
- Published on Monday, 23 May 2016 12:08
Tungsten is a rare metal, after mining, rubbing, water re-election, refining and other processes, wolfram ore would be make into a purity of 60% or 90% of the tungsten powder, and then to refining it into the shape of the finished product with high-temperature electric resistance furnace, that is tungsten bar. Its melting point is about 3500 ℃. Pure tungsten is a natural metal mined from the earth. At present, China and Russia are the biggest countries of tungsten ore reserves of tungsten resources in many countries. Generally speaking, it should be a purity of 99.95% or more, and manufactures must issue an inspection report analysis and testing authorities, such as: analysis test report of national nonferrous metals electronic material analysis and testing center, or worldwide recognized Societe Generale de Surveillance (SGS). Wolfram bar may also be referred to tungsten, which has a high hardness after quenching and tempering, and has wear-resisting property. In high temperature conditions, it is also able to maintain the good performance. Therefore, wolfram bar is mainly used in the tool head processing, tungsten wire for lighting equipment and various thermal conductors. What’s more, it can used for making crank axle of advanced automobile, ingredients of cylinder, and a variety ingredients of special steel casting. In addition, tungsten bar is also widely applied in manufacturing guns, artillery, rockets, satellites, aircraft, ship, jewelry and other fashionable accessories.
According to the GB / T 3459-2006 "tungsten" requirement in November 1, 2006 of state. The dimensions of tungsten square bars include: TW-2: (10-16) mm * (10-16) mm * (> = 300) mm; TW-1, TW-4: (10-16) mm * (10-16 ) mm * (> = 30) mm. The dimensions tungsten round bars include: TW-2: (16-30) mm * (> = 300) mm, curvature cannot be greater than 4mm; TW-1, TW-4: (16-30) mm * (> = 30) mm. On the other hand, the ways for packaging of these types of products also have the relevant provisions. Under normal circumstances, each of them is about 1000g. Generally, the package of them can be divided into small packages and large packages. Small package usually uses cartons or plastic boxes, packing in kg is about seven to a box. Large package uses wooden cases, counting for 300, 000 kilograms, generally 5 boxes in a carton. The weight of each carton of international shipping limit 50KG and the domestic transport is 25KG.
Tungsten Metals Supplier: Chinatungsten Online www.tungsten.com.cn | Tel.: 86 592 5129696; Fax: 86 592 5129797;Email:sales@chinatungsten.com |
Tungsten News & Prices, 3G Version: http://3g.chinatungsten.com | Molybdenum News & Molybdenum Price: http://news.molybdenum.com.cn |
What Is Highly Pure Tungsten Bar?
- Details
- Category: Tungsten Information
- Published on Monday, 23 May 2016 12:05
Highly pure tungsten is a kind of wolfram bar which only contains a high concentration of tungsten, and the content of tungsten cannot less than 99.98%. Due to high tungsten content, its price will be a corresponding increase. Tungsten bar is a material with silver-gray metallic luster, generally it can be divided into round bar and square bar, the difference of them is that different sizes and shapes. According to the State on November 1, 2006 implementation of the GB / T 3459-2006 "tungsten" requirement, code of pure wolfram bar is TW-2, which is mainly applied to make bar fight contact, code of tungsten steel is usually TW-1 or TW-4, it is mainly used in steel-making. It also used for the preparation of high quality tungsten, or other fields in high purity tungsten products. There are some differences of manufacturing process between the general tungsten and highly pure wolfram bars. The followings are the main steps to make the highly pure tungsten bar.
The first step is to manufacture tungsten powder. At the beginning of this process, pay attention to ensure that the high-purity of wolfram powder and its granularity. At present, many major manufacturers use the full atmosphere hydrogen reduction furnace to deacidize tungsten oxide and produce high-purity wolfram powder. The second step is press wolfram bar. The point of this technology is to ensure that the size of wolfram bar has the high accuracy. Generally speaking, it is better to make a good mold of the final product in advance, and then press it with a precision pressing.
The third step is the pre-burn stage, heating the compact at a temperature that below the final sintering heating temperature. Then put the pressed tungsten blanks into the sintering furnace to sintering, which could make the internal microstructure of tungsten bar keep a uniform state. The purpose of sintering is to obtain products with the theoretical density and pore-free at the high temperature. The final step is to vertical sinter wolfram bar into the final product. That is to put the semi-finished tungsten bars into vertical sintered machine and sinter it into finished products.
Highly pure tungsten bar and all the related products are all the same industrial products, produced by the plant. Whether it is 99.95%, or 99.96%, 99.97%, 99.98% or even 99.99% of tungsten, it is made by powder metallurgy production.
Tungsten Metals Supplier: Chinatungsten Online www.tungsten.com.cn | Tel.: 86 592 5129696; Fax: 86 592 5129797;Email:sales@chinatungsten.com |
Tungsten News & Prices, 3G Version: http://3g.chinatungsten.com | Molybdenum News & Molybdenum Price: http://news.molybdenum.com.cn |
Low-Cost Tungsten Trioxide Cellular Denitration Catalyst
- Details
- Category: Tungsten Information
- Published on Friday, 20 May 2016 18:16
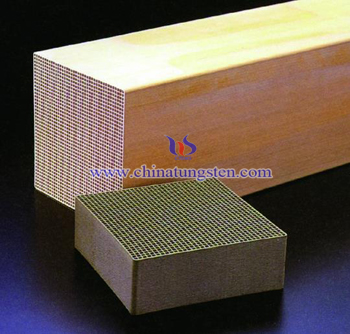
Tungsten Oxide Supplier: Chinatungsten Online www.tungsten-oxide.com | Tel.: 86 592 5129696; Fax: 86 592 5129797;Email:sales@chinatungsten.com |
Tungsten News & Prices, 3G Version: http://3g.chinatungsten.com | Molybdenum News & Molybdenum Price: http://news.molybdenum.com.cn |
Palygorskite Based Tungsten Trioxide Denitration Catalyst
- Details
- Category: Tungsten Information
- Published on Friday, 20 May 2016 18:13
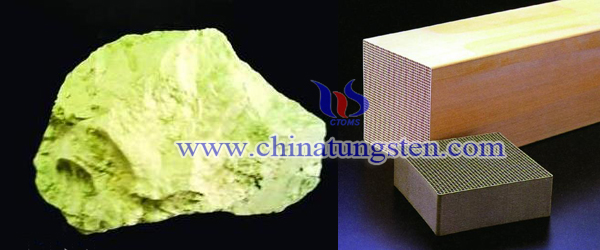
Tungsten Oxide Supplier: Chinatungsten Online www.tungsten-oxide.com | Tel.: 86 592 5129696; Fax: 86 592 5129797;Email:sales@chinatungsten.com |
Tungsten News & Prices, 3G Version: http://3g.chinatungsten.com | Molybdenum News & Molybdenum Price: http://news.molybdenum.com.cn |
Tungsten Alloy Ionizing Radiation Shielding
- Details
- Category: Tungsten Information
- Published on Friday, 20 May 2016 17:58
In fact, there are many kinds of radiation in our life. But experts point out that the radiation which causes damage to the human body to the greatest extent is ionizing radiation. Ionizing radiation refers to a high-energy radiation with short wave length and high frequency, which can directly or indirectly ionize the atoms and molecules of matter by interacting with the matter. The ionizing ability of ionizing radiation depends on the energy carried by the rays, if the rays did not bring enough ionization energy, the ionization can not occur. With the development of radiation technology, the application of ionizing radiation in our life is increasingly widespread. In the nuclear industry, it is used in the mining, smelting and finishing of raw materials, as well as the production, use and research of nuclear reactors and fuel; in agriculture, it is used for cultivation of new varieties, the preservation of fruits and vegetables and food storage; in medicine, it is used in disease diagnosis, cancer therapy and radiography; in industry, it is used for ray generator, electronic speed welder and various accelerators.
When the body is exposed to ionizing radiation whose doses exceed a certain limit, ionizing radiation can cause harm to humans. Ionizing radiation can cause radiation sickness, and lead to the pathological changes in almost all the organs and systems, the most obvious is the blood-forming organs, nervous system and digestive system. Ionizing radiation damage can be divided into acute radiation injury, which caused by receiving a certain dose of radiation in a short time and commonly found in the nuclear accident and the patients treated by radiation therapy, and chronic radiation injury, which caused by receiving scattered dose of radiation in a long time (such as skin damage, hematopoietic disorders, leukopenia, impaired fertility, etc.). In addition, ionizing radiation can also cause cancer and fetal death and malformations. Therefore, the use of protective measures is necessary.
Protective measures include placing a shielding between human body and sources of ionizing radiation to weaken the strength of the ionizing radiation. Since tungsten alloy has the advantages of high density, good machinability, good corrosion resistance and high radiation absorption capacity, tungsten alloy is the best choice for radiation shielding. Reducing the volume and the thickness of tungsten alloy shielding, its shielding ability is still equivalent to lead shielding. In addition, tungsten alloy shielding is non-toxic non-polluting, so that it is easier for people to accept.
Tungsten Alloy Supplier: Chinatungsten Online www.tungsten-alloy.com | Tel.: 86 592 5129696; Fax: 86 592 5129797;Email:sales@chinatungsten.com |
Tungsten News & Prices, 3G Version: http://3g.chinatungsten.com | Molybdenum News & Molybdenum Price: http://news.molybdenum.com.cn |
Tungsten Carbide Hollow Drill Comparison
- Details
- Category: Tungsten Information
- Published on Friday, 20 May 2016 17:39
Besides, hollow drills also use high-speed steel and tool steel. Although high-speed steel and tool steel is more sharp and high drilling efficiency, but it is easy to brittle fracture when drilling high hardness materials. And at this point carbide has better strength and wear and corrosion resistance, not prone to chipping in some of the harder material when drilling in environmental corrosive liquid can be ensured under the drilling work stably performed. Tungsten carbide hollow drill blade portion generally use a combination of three blade structure, ranging from pitch division, there are some special combination of edge structures using a plurality of outer edges of the blades and the inner edge components. Each blade in the cutting process, the work load is only about 1/3, and with the inside of each blade are also cutting, making very smooth chip evacuations.
In addition, since each edge can endure parts of cutting work, its drill holes extremely difficult to be broken. Tungsten carbide hollow drill can drill 50mm in thickness of steel plate at high-speed with high-precision and drilling can be overlapped. With a dedicated core drill machine is also capable of multi-directional drilling, cutting light, high efficiency, bit life long, relatively low cost, suitable for all types of drilling, milling machines, lathes and so on.
Here are some notes on tungsten carbide hollow drills:
1. Before the start of the drilling must ensure that the tool is fully seated, no loose or clamping;
2. It must be ensure that when using the magnetic base drilling rig drilling rig at no iron magnet, suction surface smooth, no machine or swing adsorption phenomena completely;
3. The whole process start drilling until the completion of the drilling should be kept cooled sufficiently, the best use of the cooling conditions, inadequate cooling can lead to damage of the tool.
4. Drilling should start slow and steady feed, cut into the 1-2mm can speed up the feed rate. When appropriate to slow down the knife cutting speed, the cutting process intermediate feed should be kept stable;
5. Tungsten carbide is a kind of materials with high hardness, and it is supposed to prevent the shock.
Tungsten Carbide Supplier: Chinatungsten Online tungsten-carbide.com.cn | Tel.: 86 592 5129696; Fax: 86 592 5129797;Email:sales@chinatungsten.com |
Tungsten News&Tungsten Prices, 3G Version: http://3g.chinatungsten.com | Molybdenum News & Molybdenum Price: http://news.molybdenum.com.cn |