Tungsten Carbide Hollow Drill Description
- Details
- Category: Tungsten Information
- Published on Friday, 20 May 2016 17:37
Tungsten carbide hollow drill mainly composed of the refractory metal carbide WC and the binder phase Co, which is also called as coring drill, center drill, punch drill and so on. It is one type of tungsten carbide drills, except the hollow drill, there are cone bit, drill with indexable inserts and tungsten carbide acicular drill, etc. Tungsten carbide drill breaks the rocks through the impact load produced by the drilling pressure and rotation itself. In the process of rock drilling, the drill bit is subjected to high frequency impact load, and by twisting, bending, stretching, compression and other complex stress, and in the high-speed rotation of the environmental impact is subjected to rock, rock dust and wear and corrosion mineral water.
For the highly abrasive formations, autogenous tungsten carbide acicular drill can be used. Usually hard alloy drill drilling rock drillability is Ⅶ grade Ⅱ formation; tungsten carbide drill bits drilling Ⅵ Ⅷ stage rock. Tungsten carbide hollow drill mostly used for cutting, drilling, annular groove processing, which can be widely used in rail, construction, machinery, aerospace, bridges, ships and other processing areas. It has high drilling efficiency, flexible operation and can be used with other types of drills and achieve multifaceted process, and the drilling performance is remarkably better than the conventional twist drill.
Tungsten carbide hollow drill mainly includes the following grades:
1. YG3X HRA ≥91.5 cobalt tungsten titanium in the best wear resistance, but poor impact toughness, suitable for cast iron, nonferrous metals and alloys, broken fire steel, alloy steel small section of high-speed finishing;
2. YG3 HRA ≥90.5 wear resistance second only YG3X, more sensitive to shock and vibration, for cast iron, nonferrous metals and alloys continuous cutting of fine cars, semi-finishing and processing, fine threading and reaming;
3. YG6A HRA ≥91.5 case of fine-grained alloy, good wear resistance, suitable for cooled cast iron, nonferrous metals and other semi-finished alloy is also suitable for broken fire steel alloy steel semi-finishing and finishing;
4. YG6 HRA ≥90 high wear resistance, but less than YG3, shock and vibration is better than YG3X. For cast iron, nonferrous metals and alloys, non-metallic materials medium cutting speed semi-finishing and finishing;
5. YG8 HRA ≥89.5 use of high strength, impact resistance, shock resistance compared YG6 good, but lower wear resistance and allow the cutting speed. For cast iron, nonferrous metals and alloys, non-metallic materials at low cutting speed.
Tungsten Carbide Supplier: Chinatungsten Online tungsten-carbide.com.cn | Tel.: 86 592 5129696; Fax: 86 592 5129797;Email:sales@chinatungsten.com |
Tungsten News&Tungsten Prices, 3G Version: http://3g.chinatungsten.com | Molybdenum News & Molybdenum Price: http://news.molybdenum.com.cn |
Rare Earth Tungsten Electrode Applies to High Intensity Discharge Lamps
- Details
- Category: Tungsten Information
- Published on Friday, 20 May 2016 16:26
Comparing the luminescent properties of rare earth tungsten electrode and thoriated tungsten electrode in different power lighting metal halide lamp and car halide found rare earth tungsten electrodes has similar properties with thoriated tungsten electrode , which can replace radioactive thoriated tungsten electrodes using in high intensity discharge lamps, not only environmental and having good performance.
Tungsten electrode is an important component of high-intensity discharge lamps. According to the functions can be divided into cathode and an anode. The cathode is to emit electrons at a certain temperature, so that the electrodes can move to the anode, and the anode receives electrons. In alternative current, the tungsten electrode is not only as the cathode, but as the anode. In the positive half cycle it is anode and in the negative half cycle it is cathode, so in the exchange discharge lamp the electrode will be referred as cathode. Rare earth tungsten electrode used in high-intensity discharge lamps, its performance is closely related to the discharge lamp life. So rare earth tungsten electrode as cathode material can meet the following requirements:
1. Having low work function,
2. Having good arcing performance and arcing stability;
3. Having low evaporation rate, when meets the requirement of cathode material;
4. Having stable structure, small high-temperature creep strength, electron resistance and ion bombardment resistance;
5. Having stable chemical property, the electrode will not react with filler material of lamp;
6. High intensity discharge lamps operate at temperatures above 2000K, so the electrodes so have good high temperatures property.
Rare earth tungsten electrodes production processes are as following: mixing rare earth nitrate solution with tungsten oxide by solid-liquid doping method, after reduction to obtain mixed powder. After pressed, sintered the mixed powder can obtain the blank. Then to process a series of machining can obtain rare earth tungsten electrodes. There are two ways for rare-earth doping. One is the traditional solid-liquid doping method, which is to mix rare earth nitrate solution with tungsten oxide. The second is liquid-liquid doping method, which is more effective.
Tungsten Metals Supplier: Chinatungsten Online www.tungsten.com.cn | Tel.: 86 592 5129696; Fax: 86 592 5129797;Email:sales@chinatungsten.com |
Tungsten News & Prices, 3G Version: http://3g.chinatungsten.com | Molybdenum News & Molybdenum Price: http://news.molybdenum.com.cn |
Ceriated Tungsten Electrode Manufacturing
- Details
- Category: Tungsten Information
- Published on Friday, 20 May 2016 16:22
Ceriated tungsten electrode has many different manufacturing methods. Manufacturers usually use yellow tungsten oxide to mix with cerium and after second reduction can obtain mixed powder. The mixed powder processes pressing, sintering and subsequent processing to obtain electrode. Some manufacturers will mix pure tungsten powder with cerium compound to obtain cerium tungsten powder.
Using solid-liquid doping method to mix blue tungsten oxide with ceria oxide, after reduction, pickling, isostatic pressing, sintering, and rolling cogging and other subsequent processing obtain electrode. Using this method to produce electrodes not only the cerium content distribution in electrode is evenly, but also the electrode has good arcing effect and small burning rate. The production processes are as follows:
1. Blue tungsten oxide (fee's size is boat 8 ~ 12um) mixes with cerium nitrate hexahydrate solution.
2. Adjust the pH of the suspension, so that the deposits of metal hydroxides will deposit on the porous blue tungsten oxide particles.
3. To dry the mixed powder, and then places in 600 ~ 1000 ℃ continuous hydrogen reduction furnace to restore. Blue tungsten oxide and metal hydrides were restored to tungsten and metal oxides.
4. The cerium tungsten powder after acid-washed and sieved uses isostatic pressing machine to press.
5. The compacted blank is placed at 1200 ℃ ± 50 ℃ hydrogen furnace for30 min pre-sintered, in order to improve the strength of the electrode.
6. After pre-sintered, the blank will process three-steps heating and preservation. The first step of heating and preservation can removal the impurities of billet. In the second step should increase the temperature, but below cerium’s melting point, for minutes preservation, which can make cerium oxide to maintain dispersion state. The third step should increase the temperature to 2600 ℃, complete sintering.
7. After sintering, the blank should process rotary swaging and drawing. In the process of process, the blank should be annealed. And then after straightening, polishing, cutting and other processes obtains ceriated tungsten electrode.
Tungsten Metals Supplier: Chinatungsten Online www.tungsten.com.cn | Tel.: 86 592 5129696; Fax: 86 592 5129797;Email:sales@chinatungsten.com |
Tungsten News & Prices, 3G Version: http://3g.chinatungsten.com | Molybdenum News & Molybdenum Price: http://news.molybdenum.com.cn |
What Is the Difference between Tungsten Bar and Tungsten Metal?
- Details
- Category: Tungsten Information
- Published on Friday, 20 May 2016 10:10
At present, “tungsten metal” is increasingly known for a vast number of consumers, but most of them still cannot have a clear definition of its concepts. China is one of the biggest countries to produce wolfram in the world, reserves of wolfram is 5.2 million tons, which account for 65% of the world's total reserves, pbaruction and export volume ranking first in the world. Under normal circumstances, people will consider metal tungsten as "wolfram metal", thinking that it is a kind of tungsten alloys which contains other alloying elements. Another saying about wolfram metal is that it is taken as a kind of metal which has a large proportion of metal, such as plumbum, however, prices of lead are actually much lower than tungsten.
What’s more, it is referred to a kind of tungsten material which contains gold. Some people think it doesn’t matter for its name. In fact, clear up the name of the above clarification is important, because there exist a large difference in their prices. The first case should be referred to the metal tungsten or tungsten bar. This variety takes "ton" or "kilogram" as the unit of measurement. Accordance to the current market situation, its price is generally at 245 RMB / kg. If someone sells you so-called "the price of wolfram metal bars with purity of 99.97% is several hundred thousand dollars per kilogram", that is a lie, in fact, it is pure tungsten bars. Wolfram metal is nonexistent in the world, that is, pure tungsten, people tamper with the concept to make money. Also, lead is taken "ton" as the unit, the current market price is 12,850-12,950 RMB per ton. Tungsten alloy is gold which belongs to a precious metal, even if it only contains a small amount of tungsten, it also belongs to gold. The charge unit of precious metals is generally taken "g" as a unit, according to the current market, its price is 200-300 RMB per gram.
Therefore, the fuzzy title will easily cause fraud, the large difference of their prices, it is necessary for the broad masses to pay a high attention to the name of products. In fact, both of them are not fundamentally different, the easiest way to judge them is that you can require a quality report of wolfram bars from the businesses who sale the wolfram bars or manufacturers, then, ask business for a quality report of "tungsten gold bars", and then compare their chemical compositions.
Tungsten Metals Supplier: Chinatungsten Online www.tungsten.com.cn | Tel.: 86 592 5129696; Fax: 86 592 5129797;Email:sales@chinatungsten.com |
Tungsten News & Prices, 3G Version: http://3g.chinatungsten.com | Molybdenum News & Molybdenum Price: http://news.molybdenum.com.cn |
Manufacturing Processes of Tungsten Bar
- Details
- Category: Tungsten Information
- Published on Friday, 20 May 2016 10:07
Manufacturing processes of tungsten bar mainly depend on seven steps. The first is to be formulated doped tungsten powder. While formulating, weighing raw wolfram powder in according with the percentage of weight of wolfram powder, put the content of 0.2 ~ 0.6wt% silicon dioxide and burnt potash which contains 0.2 ~ 0.6 wt% of silicic acid and caustic potash mixed solution as well as aluminum nitrate solution containing 0.02 ~ 0.1wt% alumina into the blender. Then at a temperature of 50 ℃ ~ 60 ℃, it is mixed for 3 to 5 hours. Then it was dried for 3 to 6 hours, dried at a temperature to 100 ℃ ~ 200 ℃ finally obtain blue doped wolfram powder.
The next step is reduction treatment. Firstly, load doped wolfram powder in tungsten boat, reduction treatment should be last for 8 to 12 hours in a hydrogen atmosphere under the temperature of 500 ℃ ~ 950 ℃. After cooling, make it go though screen mesh for 100 meshes ~ 200 meshes, and obtain doped wolfram powder. Then scouring doped wolfram powder for 30 to 60 minutes by 3 ~ 6wt% of dilute hydrochloric acid, then removing the supernatant, and then add a concentration of 3 ~ 6wt% hydrofluoric acid, washing powder until the concentration of Si is lower 250ppm, and concentration of Al content is lower 30ppm, and then dried it in vacuum at a temperature of 70 ~ 150 ℃ for more than 10 hours. After drying, make it go though screen mesh for 160 meshes ~ 200 meshes and remove impurities.
Tungsten powder will be compressed into wolfram billet under a 150 ~ 250MPa pressure, and it will be put into the boat, sintering at the atmosphere of hydrogen and a temperature of 1100 ~ 1400 ℃, sintering time is 30 ~ 60 minutes. Self-resistance heating sintering is to a put the pre-sintered billet into the vertical furnace, under hydrogen and 70 to 92% of the fusing current situation to self-resistance heating sintering for 10~25 minutes. After the cooling, obtain a not dense potassium wolfram bar. Finally, put wolfram bars which are obtained above steps into the IF furnace or tungsten bar furnace, sintering for 2 to 6 hours under hydrogen and temperature of 2000 ~ 2300 ℃, and obtain finished product.
Tungsten Metals Supplier: Chinatungsten Online www.tungsten.com.cn | Tel.: 86 592 5129696; Fax: 86 592 5129797;Email:sales@chinatungsten.com |
Tungsten News & Prices, 3G Version: http://3g.chinatungsten.com | Molybdenum News & Molybdenum Price: http://news.molybdenum.com.cn |
Tungsten Alloy Radiation Shielding For X-ray Machine
- Details
- Category: Tungsten Information
- Published on Thursday, 19 May 2016 17:58
An X-ray machine is a device used to generate X-rays. It is made up of a control console which enables the x-ray technician to choose a variety of x-ray techniques suitable for that specific exam, an X-ray generator that creates and produces the desired KV, MA and X-ray tube. The X-ray tube, like any vacuum tube, contains a cathode, which directs a flow of electrons into a vacuum, and an anode, which collects the electrons and is made of tungsten to disperse the heat generated by the collision. When the electrons collide with the target, about 1% of the resulting energy is emitted as X-rays, with the remaining 99% released as heat. Due to the high energy of the electrons that reach relativistic speeds the target is usually made of tungsten even though other materials can be used particularly in XRF applications. The types of X-ray machine include the portable medical X-ray system, the industrial X-ray detection machine and the belt detection X-ray machine. X-ray machines are widely used in hospitals to help doctors diagnose the disease, in industry for non-destructive testing and in railway stations and airports to carry out security checks.
X-ray is a form of electromagnetic radiation. Most X-rays have a wavelength ranging from 0.01 to 10 nanometers, in line with frequencies in the range of 30 petahertz to 30 exahertz and energies in the range of 100 eV to 100 keV. The wavelength of the X-ray is shorter than that of UV ray and typically longer than that of gamma ray. In many languages, X-radiation is referred to with terms meaning Röntgen radiation, who is usually credited as its discoverer, and who had named it X-radiation to signify an unknown type of radiation. X-ray has penetrating effect, ionizing effect and thermal effect. In medicine it is often used for fluoroscopy, in industry for industrial flaw detection. Since the X-ray has a strong penetrating effect, when a living organism is irradiated with X-ray, its living cells can be inhibited, destroyed and even killed, resulting in varying degrees of changes in physiology, pathology and biochemical aspects. In the use of X-ray technology, it also found that X-ray can lead to the patient hair loss, skin burns and can cause vision disorder, leukemia and other ray injury problems on the related personnel.
Tungsten alloy radiation shielding can be used to shield X-ray generated by the X-ray machine. Compared with conventional shielding materials (such as lead), tungsten alloy shielding reflects good value. Since the tungsten alloy has a high density, under the condition of the same thickness, the radiation shielding ability of tungsten alloy is twice than that of lead shielding, and the weight of tungsten alloy shielding is 25 to 50% less than lead. In addition, lead is toxic and tungsten alloy shielding is non-toxic so that it will not harm the human body or pollute the environment.
Tungsten Alloy Supplier: Chinatungsten Online www.tungsten-alloy.com | Tel.: 86 592 5129696; Fax: 86 592 5129797;Email:sales@chinatungsten.com |
Tungsten News & Prices, 3G Version: http://3g.chinatungsten.com | Molybdenum News & Molybdenum Price: http://news.molybdenum.com.cn |
Tungsten Bronze Structure Materials Application in TBC
- Details
- Category: Tungsten Information
- Published on Thursday, 19 May 2016 17:50
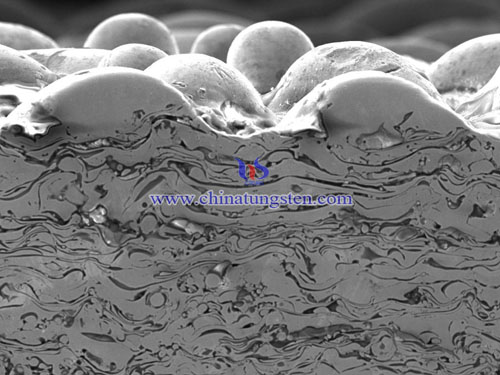
Tungsten Oxide Supplier: Chinatungsten Online www.tungsten-oxide.com | Tel.: 86 592 5129696; Fax: 86 592 5129797;Email:sales@chinatungsten.com |
Tungsten News & Prices, 3G Version: http://3g.chinatungsten.com | Molybdenum News & Molybdenum Price: http://news.molybdenum.com.cn |
Tungsten Copper Wire Process
- Details
- Category: Tungsten Information
- Published on Thursday, 19 May 2016 16:48
The basic process of tungsten copper wires is : Mixing → molding or isostatic pressing → infiltration, sintering tungsten copper rod or tungsten copper block → machining. Except conventional infiltration process, there are some popular processes used more, such as high-temperature liquid phase sintering and activated liquid-phase sintering. The principle of infiltration is that porous tungsten skeleton wetted by copper liquid, under the capillary force the copper liquid flows along the W particle gap, filling the pores of porous tungsten skeleton. So tungsten copper materials have higher density, excellent sintering properties and electrical conductivity; High temperature liquid phase sintering since the sintering temperature is high, a long time, will make a lot of volatile copper phase, so that the sintered tungsten copper material density decrease, the performance will be subject to different degrees of impact, it is difficult to obtain a high density, high conductivity tungsten copper alloy material; activated liquid phase sintering improves the relative density, the hardness and tensile strength of tungsten copper by adding small amounts of trace elements (Ni, Fe, Pd, etc.). But on the contrary, the activated elements will dramatically decrease the electrical and thermal conductivity, which is not suitable for the occasions with high requirements of the conductivity.
The technologies to machine tungsten copper rod or block in wires include drawing processing, rolling processing, roller die drawing techniques and rotary forging technology. Drawing processing take advantage of metal plasticity, when working in the external force so that it is forced through the die, the metal cross-sectional area is compressed to obtain the desired cross-sectional shape and size of the processing method. Preparation of tungsten and copper wire by repeatedly hammering and drawing forming, drawing conducted at room temperature, metal products will produce obvious hardening.
But for tungsten copper with lower Cu content, it has poor plasticity, the drawing rate received extremely limited, which is difficult to draw molding; rolling process is to rely on the friction two rotating rollers and the rolling member rolling pulled into the roll gap, it is compressed to produce plastic deformation process. In addition, the rolling process can also refine the grain, improve the organization, can significantly improve the mechanical properties of the metal alloy, suitable for mass production; Roller die drawing process the billet is drawn in a non-grooved drive, freely rotating rollers consisting of, the sliding friction with the material of the die orifice was changed to rolling friction bearing, the stretching process is more effort not only suitable for drawing round wire, shaped wire may be stretched, but not suitable for low plastic material.
Tungsten Copper Supplier: Chinatungsten Online tungsten-copper.com | Tel.: 86 592 5129696; Fax: 86 592 5129797;Email:sales@chinatungsten.com |
Tungsten News & Prices, 3G Version: http://3g.chinatungsten.com | Molybdenum News & Molybdenum Price: http://news.molybdenum.com.cn |
Tungsten Copper Wire Description
- Details
- Category: Tungsten Information
- Published on Thursday, 19 May 2016 16:46
Tungsten copper alloy is a kind of psudoalloy, which consists of the hard phase W and the binder phase Cu two immiscible metals, so it only can be fabricated by PM (Powder Metallurgy). Tungsten copper material has both advantages of tungsten and copper, the high density, high melting point, excellent wear resistance and corrosion resistance of W; the excellent electrical and thermal conductivity, good plasticity of Cu; and at a temperature above the melting point of copper alloy of copper liquefied evaporated to absorb a lot of heat, reducing the surface temperature. So tungsten copper material is also known as heat sink materials.
According to the shapes and applications, tungsten copper products can be specifically divided into tungsten copper rod, tungsten copper block, tungsten copper plate, tungsten copper contact, tungsten copper tube, tungsten copper electrode, tungsten copper heat sink, tungsten copper wire and so on. In the early 1960s, tungsten copper wire and tungsten copper electrode has been used in EDM (Electrical Discharge Machining) and resistance welding because of its high density, high strength, excellent electrical and thermal conductivity and arc ablation resistance. So far, with the developments of relevant technologies and further study of researchers, tungsten copper begin to use in plasma electrode material processing, precision machining, spraying, LED and other electrode fields. But since the special PM structure of tungsten copper, it has been greatly limited used in wire. In order to improve the uniformity, mechanical properties and production cost, it needs to looking for new technologies and processes.
Used in EDM electrodes of tungsten copper wires are supposed to meet the following requirements:
1. On the basis of excellent electrical and thermal conductivity, it also has good resistance to spark erosion;
2. Good structure uniformity and density, in order to ensure the stability of the electrical processing and improve the utilization of electrode material;
3. It has lower machining consumption and dose not affects the quality and the overall efficiency;
4. Easy for molding, machining molds and products according to design requirements to provide a correspondingly shaped profile tungsten copper electrode bars or complex shapes.
Tungsten Copper Supplier: Chinatungsten Online tungsten-copper.com | Tel.: 86 592 5129696; Fax: 86 592 5129797;Email:sales@chinatungsten.com |
Tungsten News & Prices, 3G Version: http://3g.chinatungsten.com | Molybdenum News & Molybdenum Price: http://news.molybdenum.com.cn |
Tungsten Trioxide Contained Vehicle Denitration Catalyst without Vanadium
- Details
- Category: Tungsten Information
- Published on Thursday, 19 May 2016 16:09
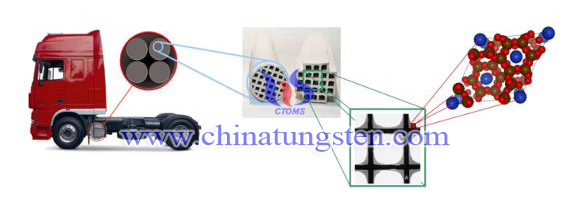
However, when SCR catalyst containing vanadium used for cleaning motor vehicle exhaust, it may lead to toxic vanadium compound going into the air because of the volatility of vanadium under high temperature, thus to cause environmental pollution and personal injury. So, the listed capacity of the car catalyst containing vanadium is low. Therefore, for a long time, researchers and vendors are ongoing committed to provide no vanadium SCR denitration catalyst.
Tungsten Oxide Supplier: Chinatungsten Online www.tungsten-oxide.com | Tel.: 86 592 5129696; Fax: 86 592 5129797;Email:sales@chinatungsten.com |
Tungsten News & Prices, 3G Version: http://3g.chinatungsten.com | Molybdenum News & Molybdenum Price: http://news.molybdenum.com.cn |