Method of Taifu Application in Wolframite Dressing
- Details
- Category: Tungsten Information
- Published on Tuesday, 12 January 2016 18:34
Tungsten Supplier: Chinatungsten Online www.chinatungsten.com | Tel.: 86 592 5129696; Fax: 86 592 5129797;Email:sales@chinatungsten.com |
Tungsten News & Prices, 3G Version: http://3g.chinatungsten.com | Molybdenum News & Molybdenum Price: http://news.molybdenum.com.cn |
Gravity Concentration and Selection in Wolframite Dressing
- Details
- Category: Tungsten Information
- Published on Tuesday, 12 January 2016 18:31
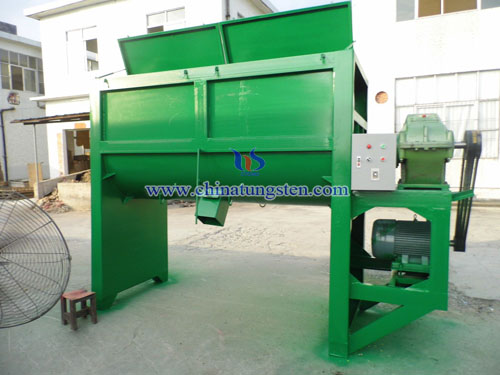
Tungsten Supplier: Chinatungsten Online www.chinatungsten.com | Tel.: 86 592 5129696; Fax: 86 592 5129797;Email:sales@chinatungsten.com |
Tungsten News & Prices, 3G Version: http://3g.chinatungsten.com | Molybdenum News & Molybdenum Price: http://news.molybdenum.com.cn |
Ammonium Paratungstate with High Purity Prepared by Ultrasonic-Microwave-Hydrothermal-Synergism-Enhanced Method
- Details
- Category: Tungsten Information
- Published on Tuesday, 12 January 2016 17:59
Equipment requirements: crystallizer with microwave oven which includes door with button and furnace body. Magnetic stirrer, microwave generator and fault detection module are set in the oven; a tray set in inner cavity of the oven, place the three flasks up on the sensor; A sensor on the side wall of the inner cavity connect to temperature sensor; the ultrasonic generator and two glasses tube are arranged on the top of the oven, and the upper end of ultrasonic generator connects water inlet and outlet pipe, the lower end connect probe made by titanium alloy; both of the probe and temperature sensor are fixed in the inner of three flasks, the lower end of two glasses tube connected with a side port of three flasks, the relay connect with ultrasonic and microwave generator, and temperature and press sensor connected with relay trough transmitter; one side of fault detection module connect to microwave generator, and the other connect to relay.
The specific steps of ammonium paratungstate with high purity prepared by Ultrasonic-Microwave-Hydrothermal-Synergism-Enhanced method are like follows:
1. Place ammonium tungstate with concentration of WO3 not less than 220 g/L in a three flasks and turn on magnetic stirrer, keep the stirring speed in 70-300rpm;
2. Turn on microwave and ultrasonic generator, power of both are controlled at 1-3KW, set microwave frequency among 0.5-1.5Hz and ultrasonic frequency 100-200KHZ, heating the solution;
3. Turn on the camera and temperature sensor;
4. Control temperature above 80℃, because solution began to crystallization when temperature reached 80℃;
5. The crystallization end for rate of 65%, then the pure APT crystal can be made.
APT Supplier: Chinatungsten Online ammonium-paratungstate.com | Tel.: 86 592 5129696; Fax: 86 592 5129797;Email:sales@chinatungsten.com |
Tungsten News&Tungsten Prices, 3G Version: http://3g.chinatungsten.com | Molybdenum News & Molybdenum Price: http://news.molybdenum.com.cn |
Direct Reduction of Ammonium Metatungstate and Ammonium Paratungstate Producing Tungsten Powder 2/2
- Details
- Category: Tungsten Information
- Published on Tuesday, 12 January 2016 17:55
Specific steps are as follows:
The raw materials used in this method are ammonium metatungstate (AMT) and ammonium paratungstate (APT), which are reach or above pure grade in industrial.
Scheme one: A certain proportion of AMT and APT mixed, and then reducing
1. Raw materials APT and AMT in accordance with 20~80% accounted for AMT, and the rest of the proportion of APT mixed;
2. Placed the mixed raw material powder in hydrogen reduction furnace for One-Step reduction, temperature controlled in 750~1000°C, keep the highest temperature for 0.5 ~ 5h;
3. Screening and drying tungsten powder in vacuum, then get the tungsten powder with high strength.
Scheme two: Reducing APT and AMT respectively, and then mixed tungsten powder in a certain proportion
1. Place the two kinds of material powder respectively in different reduction furnace for one-Step reduction, control temperature in 700~1000°C, keep the highest temperature for 0.5 ~ 5h;
2. Screening and drying tungsten powder in vacuum respectively;
3. Mixing the two kinds tungsten powder dried in different proportion, then get tungsten powder with high strength.
The advantages of this method are reflected in the following 3 aspects:
1. There is no need to go through calcination and intermediate process, because we use AMT and APT for direct reduction, low energy consumption and simple process;
2. Purity of tungsten powder prepared is very high (higher than 99.0%), with good property of suppression, strength of compression fracture reached 2.8~4.0Mpa, meeting the requirements of tungsten powder with high strength in industrial;
3. Particle size of tungsten powder prepared is uniform, high sintering activity, which is conducive to the preparation of high properties tungsten products.
Therefore, control the morphology and size of APT can improve the formability and compressive strength of tungsten powder. Control from the source, help to reduce the cost for subsequent links and make up the basic trend of the final products to produce tungsten powder with stable quality.
APT Supplier: Chinatungsten Online ammonium-paratungstate.com | Tel.: 86 592 5129696; Fax: 86 592 5129797;Email:sales@chinatungsten.com |
Tungsten News&Tungsten Prices, 3G Version: http://3g.chinatungsten.com | Molybdenum News & Molybdenum Price: http://news.molybdenum.com.cn |
Direct Reduction of Ammonium Metatungstate and Ammonium Paratungstate Producing Tungsten Powder 1/2
- Details
- Category: Tungsten Information
- Published on Tuesday, 12 January 2016 17:53
In modern tungsten industry, tungsten products are generated from tungsten powder, and tungsten powder with high purity and good quality will help in improving tungsten products’ properties. So, it supposed to be very important that how to make the tungsten powder with excellent properties, such as particle well developed, good uniformity and fluidity, and concentration of the particle size distribution. With the development and application of new products and materials in tungsten industry, the quality of tungsten powder supposed to be higher and higher. Tungsten powder with higher quality is required in preparing tube with large diameter and thin wall and large tungsten crucible ect. Usually strength higher than 2.5MPa will meet the requirement of pressing, transport and machining and improve the survival rate of products. However, at present, strength of tungsten powder is generally 1.0MPa, which is far less than the requirement. Therefore, the preparation of tungsten powder with good formability and high strength is the basis for preparing huge tungsten products with high properties.
In the process of production, the morphology and size distribution between tungsten powder and ammonium paratungstate (APT) are hereditary, that is, they are strong related. During the formation of tungsten powder, both morphology and particle distribution are important factors that affect strength.
A new method that directs reduction of ammonium paratungstate and ammonium metatungstate for production of tungsten powder was proposed. A certain proportion of ammonium tungstate (AMT) and ammonium paratungstate (APT) are mixed, direct reduction in reducing furnace, then get tungsten powder with high purity and strength; or deducted ammonium tungstate and ammonium metatungstate in different reducing furnace to obtain tungsten powder, then mixed according to a certain proportion. Tungsten powder strength reached 2.8~4.0Mpa in two ways above, and they can be widely used for preparing excellent properties of tungsten or tungsten carbide products.
APT Supplier: Chinatungsten Online ammonium-paratungstate.com | Tel.: 86 592 5129696; Fax: 86 592 5129797;Email:sales@chinatungsten.com |
Tungsten News&Tungsten Prices, 3G Version: http://3g.chinatungsten.com | Molybdenum News & Molybdenum Price: http://news.molybdenum.com.cn |
Effect of Lubricant on the Density of Tungsten Copper Electrode
- Details
- Category: Tungsten Information
- Published on Tuesday, 12 January 2016 17:22
In general process of hot pressing, tungsten particles are present between particles and mold the inner wall of the different sizes of friction, the two friction to some extent hindered the densification process material, in order to obtain the desired the green density, is bound to adopt more pressing pressure. Thus, both from the quality of compacts or maintenance of the equipment from the point of view, we must try to avoid such friction. The reduced friction in the pressing process basically includes two methods: one is to adapt tungsten carbide mold with high fineness to replace the steel mold; the other one is use lubricant, which can effectively decrease the friction of particles and the mold, and it has an large influence on the density of tungsten copper electrode sintering.
However, there are some problems about lubricant: 1. It decreases the mobility of powder; 2. Adding lubricant will reduce the volume of the original blank, which makes reducing green density is not conducive to the production of high density products; 3. In the process of pressing, he degree of contact between the metal powder is reduced due to the lubricant barrier, thereby reducing the intensity of some of the powder metallurgy compacts; 4. Lubricant should be removed before the sintering or during the sintering so that it will has an influence on the appearance of sintered body and the exhaust gas may decrease the life of furnace.
After milling, molding and sintering conditions (temperature, heating rate, etc.) under the same conditions, after adding tungsten-copper composite powder sintering and milling lubricant is not added tungsten-copper composite powder lubricant milling and grinding sintered density of time comparing the relationship between added density of the sintered body is 1% of lubricant stearic acid as compared to a lower sintered density was not added lubricant. This is due to the stearic acid was added, equivalent to the introduction of certain impurities, thereby reducing the sintering activity of the powder particles, resulting in a sintered tungsten copper electrode material density decreases. Therefore, comprehensive view of tungsten copper alloy electrode density plays a leading role in the activity of the powder, friction is a minor factor.
Tungsten Copper Supplier: Chinatungsten Online tungsten-copper.com | Tel.: 86 592 5129696; Fax: 86 592 5129797;Email:sales@chinatungsten.com |
Tungsten News & Prices, 3G Version: http://3g.chinatungsten.com | Molybdenum News & Molybdenum Price: http://news.molybdenum.com.cn |
New Types, Structure of Coated Cemented Carbide—Diamond Coating 3/3
- Details
- Category: Tungsten Information
- Published on Tuesday, 12 January 2016 17:20
The test of diamond coating properties is as important as the deposition. The main part of the test includes the grain size of diamond coating, another is the binding force of diamond coating and tungsten carbide matrix.
Theoretically, diamond coating has crystalline structure, the coarseness is mainly determined by the size of grain (smaller granularity, lower coarseness of surface). For tungsten carbide drawing die, the coarseness of surface plays an important role in the comprehensive properties. In the diamond coating applied to the graphite tooling tests show that when the grain size is less than 1μm, the surface roughness of <1μm, and the roughness of the workpiece conventional diamond coating is greater than 2-3μm, and operates in a workpiece using prone to particle shedding. In addition, diamond coating can combine micro particle with ultra nano particle, which can be observed clearly by SEM. This combination can be more suitable for tungsten carbide drawing die with high demand and high performance.
The other is the test of the binding force between diamond coating and tungsten carbide matrix. The binding force between diamond coating and tungsten carbide matrix is the foundation of the drawing work, if the binding strength is lower, diamond coating will drop off in the processing of some wire with high strength drawing, which make the mold become invalid. The binding force is adapted by diamond indentation tester, it uses diamond indenter to press the surface of diamond coating layer, the image as follow:
Viewed from the indentation of diamond coating, we can more clearly see the diamond coating cracked or peeling around the indentation does not occur, the central portion of the diamond indentation remains firmly bonded carbide coating surface of the test, followed by the pressure applied to 1.5KN, diamond coating is damage. Compared with traditional diamond coating has maximum load lower than 600N, the coating by chemical vapor deposition (CVD) can remarkably improved.
Tungsten Carbide Supplier: Chinatungsten Online tungsten-carbide.com.cn | Tel.: 86 592 5129696; Fax: 86 592 5129797;Email:sales@chinatungsten.com |
Tungsten News&Tungsten Prices, 3G Version: http://3g.chinatungsten.com | Molybdenum News & Molybdenum Price: http://news.molybdenum.com.cn |
Microwave Calcination Tungsten Trioxide Preparation
- Details
- Category: Tungsten Information
- Published on Tuesday, 12 January 2016 16:34
Tungsten trioxide is an important intermediate product in the process of tungsten extractive metallurgy. The tungsten powder and tungsten main raw material-related are prepared usually by the calcining. Microwave calcination has an internal fast, selective calcination, the material can be overcome: the "cold center", energy-saving features, it is easy to control automatic implement, can effectively improve the quality rate and pass rate. Compared with the traditional production process of tungsten trioxide, microwave calcination time is short, low cost, high thermal efficiency, low energy consumption, and the powder is not easy to leak.
APT is a white crystalline, sheet-like or needle-like. It slightly dissolves in water, its solubility is less than 2% at 20 ℃I n water. The ammonium APT losing some crystal water and ammonia, or may be converted to ammonium metatungstate AMT in 220-280 ℃. It losing all crystal water and ammonia, completely transformed as a yellow tungsten trioxide heated at above 600 ℃. APT is mainly used to produce tungsten trioxide or tungsten blue oxide metal tungsten powder; tungsten material downstream products series, such as tungsten, tungsten and other electric vacuum material; there are alloy series, such as tungsten carbide, tungsten carbide, alloy blades, alloy drill, alloy molds and the like; other wear, pressure, mechanical equipment and other high-temperature components.
We put accurate weighing of the dried samples into the crucible, recording the weight of material as W1. Using the modified multimode microwave calcined, recording time and power, removing after cooling weighing, recording data W2. The W1 minus W2, we can get APT, calculate the actual weight loss rate (%). After the 4 minutes of microwave by calcination, ammonium APT of decomposition is 96.67%, and orthogonal experiments. The best conditions in the experimental are: microwave power is 650w, the calcination time is 4min, and the material weighs are 10g.
Tungsten Oxide Supplier: Chinatungsten Online www.tungsten-oxide.com | Tel.: 86 592 5129696; Fax: 86 592 5129797;Email:sales@chinatungsten.com |
Tungsten News & Prices, 3G Version: http://3g.chinatungsten.com | Molybdenum News & Molybdenum Price: http://news.molybdenum.com.cn |
Tungsten Gold-plated Blocks For Securities Trading Gifts
- Details
- Category: Tungsten Information
- Published on Tuesday, 12 January 2016 16:28
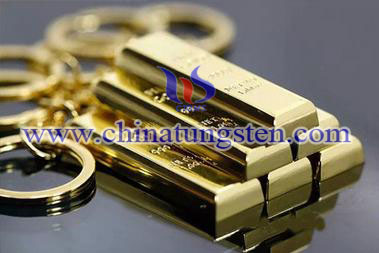
Tungsten Gold Plated Supplier: Chinatungsten Online www.tungsten-alloy.com | Tel.: 86 592 5129696; Fax: 86 592 5129797;Email:sales@chinatungsten.com |
Tungsten News & Prices, 3G Version: http://3g.chinatungsten.com | Molybdenum News & Molybdenum Price: http://news.molybdenum.com.cn |
Carbon Nanotubes Tungsten Trioxide Thin Film Producing Method
- Details
- Category: Tungsten Information
- Published on Tuesday, 12 January 2016 16:20
Carbon nanotubes tungsten trioxide film, the preparation method and application in solar cells are belong to the technical field of nano materials. The composite film is made by interspersed net carbon nanotube film and tungsten trioxide. On the one hand, the carbon nanotubes tungsten trioxide is more stable after weaving, and it can realize directly transfer, which can avoid the introduction in the process of traditional tungsten trioxide transfer. On the other hand, carbon nanotube tungsten trioxide is simpler than tungsten trioxide; it has better conductivity and higher conversion efficiency.
Chemical vapor deposition process (CVD), refers to the reaction mixture containing the desired vapor and gaseous elements, introducing the film liquid reactant or other gases introduced into the reaction chamber. Many films were prepared by using the CVD method in VLSI The deposition temperature is low, it is easy to control the film composition, film thickness and deposition time proportional, uniformity, repeatability, excellent step coverage. We prepare the tungsten coating by physical or chemical vapor deposition method at present, or improve the coating properties of tungsten by vapor deposition method in combination with other preparation techniques.
We prepare carbon nanotube film tungsten trioxide by taking ordered or disordered carbon nanotube film as a template and taking an organic metal compound as tungsten source in the presence or absence of a substrate supporting the presence of a base. The next step in the formation of a low temperature crystal is forming the size, orientation degree and thickness of tungsten oxide nanotubes controlled film. Carbon nanotube film tungsten trioxide has more flexibility and good light transmittance by comparing with the traditional materials.
Tungsten Oxide Supplier: Chinatungsten Online www.tungsten-oxide.com | Tel.: 86 592 5129696; Fax: 86 592 5129797;Email:sales@chinatungsten.com |
Tungsten News & Prices, 3G Version: http://3g.chinatungsten.com | Molybdenum News & Molybdenum Price: http://news.molybdenum.com.cn |