Succinic Acid and Sodium Tungstate on Ni-W-P Alloy Coating Influence
- Details
- Category: Tungsten Information
- Published on Thursday, 14 January 2016 17:32
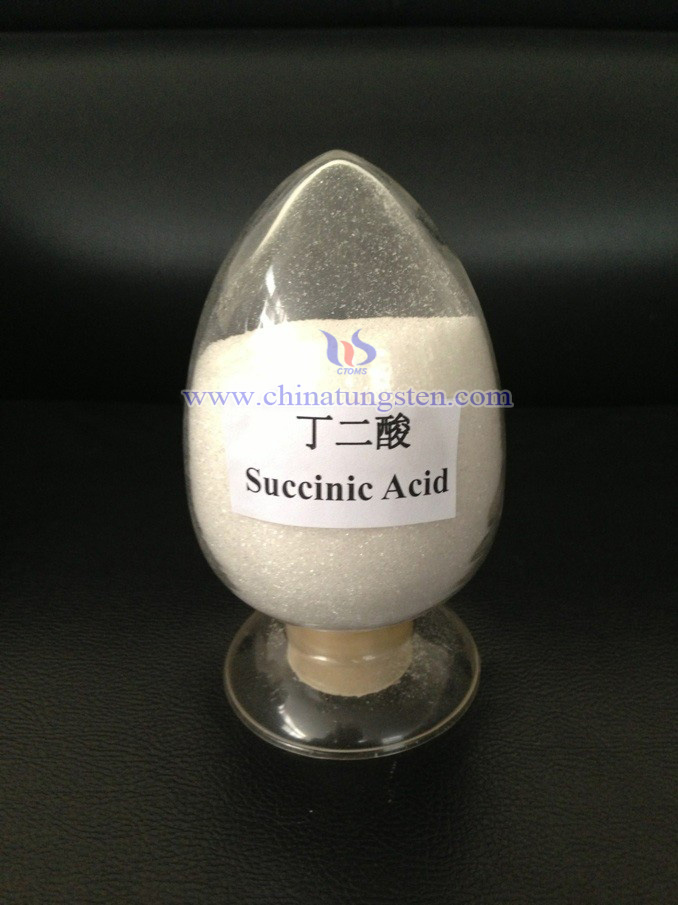
Sodium Tungstate Supplier: Chinatungsten sodium-tungstate.com | Tel.: 86 592 5129696; Fax: 86 592 5129797;Email:sales@chinatungsten.com |
Tungsten News & Prices, 3G Version: http://3g.chinatungsten.com | Molybdenum News & Molybdenum Price: http://news.molybdenum.com.cn |
Tungsten Copper Electrode—Explosive Powder Compaction (2/2)
- Details
- Category: Tungsten Information
- Published on Thursday, 14 January 2016 17:20
Actually, direct explosion pressing method does not require a large investment in equipments and it has simple structure of device. The following picture is one of the common device of direct explosion pressing method in the domestic researches:
The powder was placed there end plugs in low-carbon steel or aluminum (initial density of 50%), processed and evacuated sealed tube covered with a suitable amount of uniform thickness and density of the explosives. After detonator ignition occurs at a constant velocity along the wall down the tube and the detonation powder compaction, its detonation velocity and pressure depends on the role of the type of explosive. However, there are some defects blocks out the industrialization and standardized production of explosive powder compaction process. The biggest factor is the high speed loading generated by explosive compaction molding, it is difficult to obtain effective management and control, on the other hand, the explosion parameter dependencies and to be pressed powder types is still in the study.
After explosive compaction billet annealing for 2 hours at 900 ℃ in a vacuum oven, and the aging process. Then Vickers hardness (HV) hardness detection sample, using the Archimedes method (comparison, ideological integration method) after detecting sintering density of the sample preparation, and then by scanning electron microscopy (SEM) observation of fracture morphology products. We can observe the stress distribution of the fracture surface and breaking patterns. Overall, the explosive powder compaction is the use of explosive shock wave generated by loading technology compacted powder, powder high speed friction and heat insulation under the shock adiabatic shear action, suggesting that local high temperature, so that the surface layer melted particles the purpose of metallurgical bonding, and compacting the powder achieved by powder mainly plastic deformation and fragmentation.
Tungsten Copper Supplier: Chinatungsten Online tungsten-copper.com | Tel.: 86 592 5129696; Fax: 86 592 5129797;Email:sales@chinatungsten.com |
Tungsten News & Prices, 3G Version: http://3g.chinatungsten.com | Molybdenum News & Molybdenum Price: http://news.molybdenum.com.cn |
Scheelite Beneficiation Example
- Details
- Category: Tungsten Information
- Published on Thursday, 14 January 2016 17:18
Tungsten Supplier: Chinatungsten Online www.chinatungsten.com | Tel.: 86 592 5129696; Fax: 86 592 5129797;Email:sales@chinatungsten.com |
Tungsten News & Prices, 3G Version: http://3g.chinatungsten.com | Molybdenum News & Molybdenum Price: http://news.molybdenum.com.cn |
Tungsten Copper Electrode—Explosive Powder Compaction (1/2)
- Details
- Category: Tungsten Information
- Published on Thursday, 14 January 2016 17:16
Generally, tungsten copper consist of tungsten (W) and copper (Cu) is called psudoalloy, which has a big difference of melting point and immiscible. It uses powder metallurgy (PM) to fabricate porous tungsten skeleton and dipped, infiltrated in copper liquid or liquid-phase sintering after mixed powder compacting to achieve tungsten copper composite material. However, for tungsten copper W-Cu system, Tungsten and copper two-phase mutual infiltration is poor, tungsten copper in the liquid is almost insoluble occur, which makes it difficult to achieve the desired uniform organizational structure, and a high degree of densification.
Explosive powder compaction belong to an explosive molding, which is the use of high impact energy generated by the blast, the upcoming explosive chemical energy into mechanical energy, adiabatic compression of the powder, and instantly generate high temperature and pressure to achieve the densification of the powder material. In addition, the explosion process also includes explosive welding, explosive hardening, high-speed forging die and so on. Commonly used explosives are ammonium nitrate explosives, detonating cord, rubber explosives and TNT, etc.
Compared with common processing methods (stamping, hydraulic pressure), explosive powder compaction has many advantages, such as explosion is a very fast process, short duration of action (microsecond), high pressure, high speed of deformation, has fast melting and cooling property, which is beneficial for keeping the excellent properties of the powder. Therefore, it can be widely used in the powder compaction researches of composites with metal matrix, intermetallic compound, nano blocks and quasicrystals, ceramics and other metastable amorphous alloy.
Tungsten Copper Supplier: Chinatungsten Online tungsten-copper.com | Tel.: 86 592 5129696; Fax: 86 592 5129797;Email:sales@chinatungsten.com |
Tungsten News & Prices, 3G Version: http://3g.chinatungsten.com | Molybdenum News & Molybdenum Price: http://news.molybdenum.com.cn |
Scheelite Beneficiation Process
- Details
- Category: Tungsten Information
- Published on Thursday, 14 January 2016 17:09
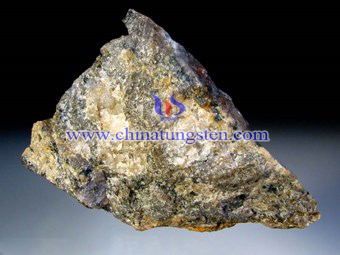
Tungsten Supplier: Chinatungsten Online www.chinatungsten.com | Tel.: 86 592 5129696; Fax: 86 592 5129797;Email:sales@chinatungsten.com |
Tungsten News & Prices, 3G Version: http://3g.chinatungsten.com | Molybdenum News & Molybdenum Price: http://news.molybdenum.com.cn |
Ion-Exchange Method Determines Tungsten Trioxide Content
- Details
- Category: Tungsten Information
- Published on Thursday, 14 January 2016 14:59
It is often difficult to achieve mutual separation because tungsten and molybdenum ionic radius close to the atomic structure of tungsten and molybdenum, and they are similar to chemical properties in minerals. There area many methods of separation: precipitation, extraction, ion exchange method and so on. These methods of separation are to smelt molybdenum tungsten and molybdenum. Among them, the precipitation method is the use of the separation of tungsten and molybdenum tungsten acid, its solubility in water and hydrochloric acid is far less thanthat in molybdic acid. Molybdic acid increases as the temperature rises, the solubility of this nature can not be completely removed.
Ion-exchange method is a method of separation in the use of ion exchanging in the exchangeable groups in the solution of different ion-exchange capacity of ions. Two common methods are water softening and deionization method. Water softening is a lowering water hardness pre-treatment program, which is mainly used before reversing osmosis (RO) process.Tenderizer is way that a sodium ion exchanges two calcium ions or magnesium ions to soften water in spherical resin. The key of ion-exchange method is to choose the suitable ion exchangers, adsorption and elution conditions.
Experimental Procedure
1. Weighing 60g of citric acid dissolved in water and diluting to 100ml;
2. Weighing 0.3g of copper sulfate dissolved in water and diluting to 100ml;
3. Weighing 200g of citric acid, placing in 1000ml beaker, adding 400ml water until completely dissolving and adding 330ml of sulfuric acid 0.20g copper sulfate, diluting with water to 1000ml, mixing;
4. Weighing 0.1500g after 550 ℃ calcination of molybdenum trioxide, placing in 250ml beaker, adding an appropriate amount of sodium hydroxide solution, heating and dissolving completely, after cooling, and transferring to 1000ml volumetric flask with sodium hydroxide solution and mixing.
Tungsten Oxide Supplier: Chinatungsten Online www.tungsten-oxide.com | Tel.: 86 592 5129696; Fax: 86 592 5129797;Email:sales@chinatungsten.com |
Tungsten News & Prices, 3G Version: http://3g.chinatungsten.com | Molybdenum News & Molybdenum Price: http://news.molybdenum.com.cn |
Colorimetry Determines Tungsten Trioxide in Tungsten Concentrate
- Details
- Category: Tungsten Information
- Published on Thursday, 14 January 2016 13:22
Colorimetry method is based on the color reaction to form colored compound, it is measured by comparing the colored substance solution or color depth to determine the content of the component. Colorimetry is an analysis of the color reaction of the basic requirements: the reaction should have a high sensitivity and selectivity, consisting of colored compound produced by the reaction that is constant and stable, it is the larger color difference and color agents. Selecting the appropriate color reaction and controlling the appropriate reaction conditions, which is the key to colorimetry analysis.
There are two commonly colorimetry: visual colorimetry and photoelectric colorimetry, visual colorimetry method is a commonly standard method, which uses different amounts of analyte standard solution in the exact same set of colorimetry tube. The sample solution is also the color under identical conditions, and the standard color gamut is visually identified, the amount of the standard solution can be contained, calculating and determining the content of the sample analytes.
The high levels of tungsten trioxide is determined generally by the use of photoelectric colorimetry, according to the situation of tungsten concentrate, which is based on selecting the visual colorimetry, and acidity, potassium thiocyanate, etc. The test of amount of titanium trichloride conditions is that weighing accurately 0.500 g sample of 2 g of sodium hydroxide flux of iron crucible, placing in a muffle furnace, the temperature is gradually raised to 85 ℃, heating it 25 to 30 minutes, removing to a pre-melted into a 300 ml beaker , heating the water to about 100 ml, which is immediately placed on a hot plate 2 a boil for 5 minutes, removing ,cooling, and washing out the iron orange vortex. The solution can be transferred into a 250-mL volumetric flask diluting the mark.
Tungsten Oxide Supplier: Chinatungsten Online www.tungsten-oxide.com | Tel.: 86 592 5129696; Fax: 86 592 5129797;Email:sales@chinatungsten.com |
Tungsten News & Prices, 3G Version: http://3g.chinatungsten.com | Molybdenum News & Molybdenum Price: http://news.molybdenum.com.cn |
Hydrothermal Method Prepares Tungsten Trioxide Photoanode
- Details
- Category: Tungsten Information
- Published on Thursday, 14 January 2016 13:07
Hydrothermal method is the scope of liquid chemical method. It means in chemical reaction, a sealed pressure vessel with water as a solvent, carried out at high temperature and pressure conditions. Hydrothermal reaction depends on the type of reaction that can be divided into hydrothermal oxidation, water and heat reduction, hydrothermal precipitation, hydrothermal synthesis, water hot solution, hydrothermal crystallization. So the hydrothermal method is the most popular method in crystallization.
Experimental Procedure
The polished clean tungsten sheet was placed in distilled water and ultrasonic cleaning in ethanol were 10min, after drying and controlling the temperature in a muffle furnace at 450 ℃, the tungsten trioxide layer is formed in the calcinations of 30min. Hydrothermal reaction solution of polyethylene glycol (300) 10% is prepared by volume of 0.02mol / L sodium tungstate solution, the solution was adjusted pH2.0 with 3mol / L hydrochloric acid. 25ml of the solution is placed in the Teflon reactor and the tungsten sheet vertically was placed in a pre-oxidized, the reaction temperature is controlled at 180 ℃ 6h. The reaction product was removed with distilled water soak about 10min, and repeating it three times to remove the product surface residue, and then the preparation of tungsten trioxide photoanode is completed after drying calcining at 550 ℃ 180min.
Conclusions
1. Hydrothermal preparation method can generate highly ordered nano-strip structure of tungsten surface, it can reach 1.5V 1.8mA / cm2in the photoanode of current;
2. a curve is made from oxidation of the tungsten film, corresponding to WO3 cubic phase in the oxidation process of 450 ℃ , the oxide layer will be formed on the surface of the tungsten sheet;
3. b curve is hydrothermal reaction product that is not calcined WO3, corresponding to the orthorhombic WO3;
4. c curve is the calcined WO3, corresponding to the monoclinic WO3, which shows three distinct peaks, the highest peak meter bar is vertically grown on the substrate, the height can reach 6.91 microns, which in shows excellent orientation role of tungsten oxide layer of the substrate with polyethylene glycol in the hydrothermal reaction of crystal growth.
Tungsten Oxide Supplier: Chinatungsten Online www.tungsten-oxide.com | Tel.: 86 592 5129696; Fax: 86 592 5129797;Email:sales@chinatungsten.com |
Tungsten News & Prices, 3G Version: http://3g.chinatungsten.com | Molybdenum News & Molybdenum Price: http://news.molybdenum.com.cn |
Tungsten Alloy Recreational Diving Counterweights(2/2)
- Details
- Category: Tungsten Information
- Published on Thursday, 14 January 2016 11:12
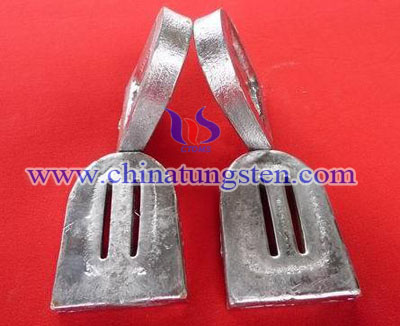
Tungsten Alloy Supplier: Chinatungsten Online www.tungsten-alloy.com | Tel.: 86 592 5129696; Fax: 86 592 5129797;Email:sales@chinatungsten.com |
Tungsten News & Prices, 3G Version: http://3g.chinatungsten.com | Molybdenum News & Molybdenum Price: http://news.molybdenum.com.cn |
Tungsten Alloy Recreational Diving Counterweights(1/2)
- Details
- Category: Tungsten Information
- Published on Thursday, 14 January 2016 11:10
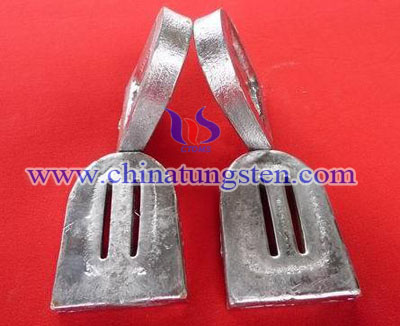
Tungsten Alloy Supplier: Chinatungsten Online www.tungsten-alloy.com | Tel.: 86 592 5129696; Fax: 86 592 5129797;Email:sales@chinatungsten.com |
Tungsten News & Prices, 3G Version: http://3g.chinatungsten.com | Molybdenum News & Molybdenum Price: http://news.molybdenum.com.cn |