Ammonium Paratungstate Catalyze Preparation of Nanosize Titanium Dioxide with Tungsten
- Details
- Category: Tungsten Information
- Published on Monday, 18 January 2016 22:30
Nanosize titanium dioxide (TiO2) refers to titanium dioxide with particles under 100 nm, mainly used in cosmetics, antimicrobial agents, etc.. Burning coal will generate nitric oxide and nitrogen dioxide and other nitrogen oxides which are poison to human body and plant. So denitrification has practical significance in the process of environmental protection. Denitrification catalyst is a substance that promotes the reducing agent reacting with titanium dioxide selectively at a certain temperature. Nanosize titanium dioxide with tungsten is a kind of catalyst for denitrification with a good performance. Preparation principle: Using metatitanic acid prepared by method of sulfuric acid as raw material, adding precursor of ammonium paratungstate and sulfate, delivery to rotary kiln for drying and roasting after stirring, and nanosize titanium dioxide with tungsten with high specific surface and surface acidic obtained.
Preparation process:
1. Remove impurities from partial acid by washing, and control ion concentrations of iron, alkali metal and all kinds of heavy metal below 100ppm;
2. Adding distilled water, configure partial acid slurry with content of TiO2 less than 30%;
3. Adding precursor of sulfate into partial acid slurry after mixing;
4. Adding ammonium paratungstate at the proportion of WO3 accounted 3~10% in the total quality of final titanium dioxide, stirring to mixing uniform;
5. Pressing leaching partial acid slurry by the diaphragm filter, and then send it to rotary kiln, raising the temperature up to 500-640℃ at rate of 20-60℃/h, nanosize titanium dioxide with tungsten which is special used as denitrification catalyst system.
Adding ammonium paratungstate into partial acid slurry, to get nanosize titanium dioxide with tungsten with higher activity, fluidity, honeycomb catalyst squeezed with smaller shrinkage rate for molding.
APT Supplier: Chinatungsten Online ammonium-paratungstate.com | Tel.: 86 592 5129696; Fax: 86 592 5129797;Email:sales@chinatungsten.com |
Tungsten News&Tungsten Prices, 3G Version: http://3g.chinatungsten.com | Molybdenum News & Molybdenum Price: http://news.molybdenum.com.cn |
Tungsten Copper Composites Powder Prepared from Ammonium Paratungstate
- Details
- Category: Tungsten Information
- Published on Monday, 18 January 2016 22:27
Tungsten copper alloy is prepared by tungsten and copper, which belongs to a metal sweating material. Tungsten copper alloy has the properties of both tungsten and copper, with uniform microstructure and high temperature resistance, strength, density and resistance to arc erosion and so on. Tungsten/ copper alloy is used in fields of military and nuclear fusion because of the moderate electric and heat conduction it has.
The preparation process of the tungsten copper alloy is generally prepared in the following five steps: preparing tungsten copper powder→mixed ingredients→pressing process→sintering and dissolution→cold working.
Using ammonium paratungstate and copper nitrate as raw material, improved traditional way to prepare tungsten copper composites powder -- Spray Drying Hydrogen Reduction Method, and reduce process of spray drying. And prepared the final product with only phase of tungsten and copper, also particles of tungsten will keep in the initial size.
The preparation processes are as follows:
1. Mixing water, copper nitrate, tartaric acid, ammonium paratungstate and citric acid according to a certain proportion, stirring under the temperature of 50 ~ 60℃for at least 5 hours, then get mixed liquor;
2. Adding polyethylene glycol to the liquor prepared step 1 and stirring under the temperature of 60~70℃ until it turns to gel;
3. placing the gel in 100 ~ 120℃ to dry for at least 12 hours, then get gel dried;
4. Arrange the dry gel orderly on 290 ~ 310℃ for 3.5 ~ 4.5 hours, then 540 ~ 560 ℃ for 4.5 ~ 5.5 hours, to obtain an intermediate product;
5. Reducing the intermediate product in reduction gas at 760~800℃for more than 3 hours, and tungsten copper composites powder prepared.
APT Supplier: Chinatungsten Online ammonium-paratungstate.com | Tel.: 86 592 5129696; Fax: 86 592 5129797;Email:sales@chinatungsten.com |
Tungsten News&Tungsten Prices, 3G Version: http://3g.chinatungsten.com | Molybdenum News & Molybdenum Price: http://news.molybdenum.com.cn |
Online Testing Molybdenum Ion Concentration in Sodium Tungstate Solution
- Details
- Category: Tungsten Information
- Published on Monday, 18 January 2016 18:31
Sodium Tungstate Supplier: Chinatungsten sodium-tungstate.com | Tel.: 86 592 5129696; Fax: 86 592 5129797;Email:sales@chinatungsten.com |
Tungsten News & Prices, 3G Version: http://3g.chinatungsten.com | Molybdenum News & Molybdenum Price: http://news.molybdenum.com.cn |
Sodium Tungstate Ionic Membrane Electrolytic Tanks
- Details
- Category: Tungsten Information
- Published on Monday, 18 January 2016 18:26
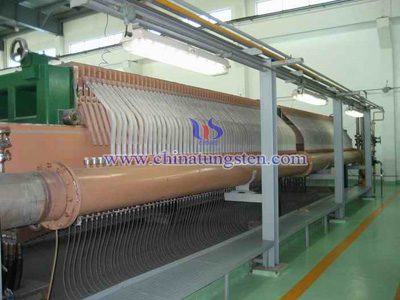
Sodium Tungstate Supplier: Chinatungsten sodium-tungstate.com | Tel.: 86 592 5129696; Fax: 86 592 5129797;Email:sales@chinatungsten.com |
Tungsten News & Prices, 3G Version: http://3g.chinatungsten.com | Molybdenum News & Molybdenum Price: http://news.molybdenum.com.cn |
Exploration on Mesoporous Tungsten Trioxide Electrocatalytic Property
- Details
- Category: Tungsten Information
- Published on Monday, 18 January 2016 17:38
Spray drying method is a systematic method of drying technology that is used in material. After the thinner is atomized in the drying chamber, contacted with hot air, the moisture rapidly vaporized by mechanical action, dispersing them into very fine mist as the same particles (increasing the water evaporation area accelerate the drying process) .and making them contacted with hot air, we can find most of the water is removed in an instant, the material of the solid material dried to a powder. The method can directly make a solution, emulsion dried into powdery or granular products, which can be omitted and evaporated. Spray drying has a fast drying process that can be directly dried into a powder, it is easy to change dry conditions, and it avoids flying dust in the workshop; it can improve product purity, it has high production efficiency.
The preparation of hollow mesoporous tungsten trioxide microspheres (HMTTS) is based on spray drying and calcination, a further load on the surface of the active ingredient of palladium (Pd), which can obtain nano Pd / HMTTS composite catalyst. The morphology and crystal structure of the catalysts are characterized by X-ray powder diffraction (XRD), scanning electron microscopy (SEM) and transmission electron microscopy (TEM), etc. The result shows that, Pd nanoparticles are face-centered cubic crystal structure, evenly distributed in HMTTS surface. We Study Pd, HMTTS electrical properties of catalytic oxidation catalyst in formic acid solution using cyclic voltammetry and chronoamperometry, the results show Pd / HMTTS catalyst is higher than conventional tungsten trioxide palladium catalyst (Pd / WO3) of formic acid exhibits in electro-catalytic activity. It is beneficial for formic acid oxidation process occurs in the surface of the palladium because of HMTTS unique structure and surface properties and hydrogen spillover effect hollow mesoporous.
Tungsten Oxide Supplier: Chinatungsten Online www.tungsten-oxide.com | Tel.: 86 592 5129696; Fax: 86 592 5129797;Email:sales@chinatungsten.com |
Tungsten News & Prices, 3G Version: http://3g.chinatungsten.com | Molybdenum News & Molybdenum Price: http://news.molybdenum.com.cn |
Nitrogen-Doped Impact on Tungsten Trioxide Structure
- Details
- Category: Tungsten Information
- Published on Monday, 18 January 2016 17:27
Doping is an important method to improve the efficiency of light energy conversion of photocatalytic material. Numerous of studies show that the rare earth and metal ions by doping can significantly enhance the catalytic activity of the photocatalyst, however, it may lead the stability of metal-doped catalysts thermal to decrease and the introduction of photo-generated electron and hole recombination centers to reduce its optical conversion efficiency. Some non-metal-doped semiconductor material may improve their stability, electrical conductivity, and pass through between the conductive and leave with the formation of "middle level" and to improve the material efficiency of absorption of visible light.
Numerous of studies show that, the N-doped can significantly improve the absorption efficiency of TiO2, ZrO2, Ta2O5 and other semiconductor materials belong to visible light, the n-type semiconductor, the same can be improved by N-doped WO3-x of visible light absorption efficiency.
The nitrogen (N) doped tungsten trioxide photocatalyst (WO_ (3-x): N) is prepared by Sol-gel - ammonia oxygen atmosphere firing method. The structural properties of the samples were characterization and analysis by using SEM, XRD, XPS and DRS, comparing the experimental study of nitrogen doping on the tungsten trioxide photolysis aquatic oxygen catalytic activity. The results show that NH_3 / O_2 was mixed atmosphere at 500 ℃ , sintering it 3h , doping N, when N enters tungsten trioxide lattice, it does not change WO_ (3-x) polymorphs and morphology. WO_ (3-x ): N remains monoclinic crystal structure, and are a small amount of an unknown sample new phase that causes thinning size and lattice distortion increases while doping surface W ~ (4+) powder and increase the oxygen vacancy. Certain lattice defects and oxygen vacancies are in favor of catalyst response wavelength red shift. The rate of N average oxygen evolution reaches 66.8μmol / (L • g • h) under UV irradiation 12h, while the rate of photolysis under visible radiation water increase to 24.5% than non-doped sample.
Tungsten Oxide Supplier: Chinatungsten Online www.tungsten-oxide.com | Tel.: 86 592 5129696; Fax: 86 592 5129797;Email:sales@chinatungsten.com |
Tungsten News & Prices, 3G Version: http://3g.chinatungsten.com | Molybdenum News & Molybdenum Price: http://news.molybdenum.com.cn |
Scheelite and Wolframite Mixture Ore and Shizhuyuan Method
- Details
- Category: Tungsten Information
- Published on Monday, 18 January 2016 17:05
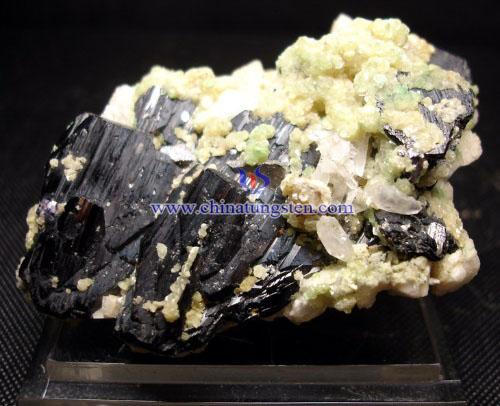
Tungsten Supplier: Chinatungsten Online www.chinatungsten.com | Tel.: 86 592 5129696; Fax: 86 592 5129797;Email:sales@chinatungsten.com |
Tungsten News & Prices, 3G Version: http://3g.chinatungsten.com | Molybdenum News & Molybdenum Price: http://news.molybdenum.com.cn |
Detinning Process of APT Production- Controlling the Alkali Decomposition Conditions
- Details
- Category: Tungsten Information
- Published on Monday, 18 January 2016 16:59
Tungsten Supplier: Chinatungsten Online www.chinatungsten.com | Tel.: 86 592 5129696; Fax: 86 592 5129797;Email:sales@chinatungsten.com |
Tungsten News & Prices, 3G Version: http://3g.chinatungsten.com | Molybdenum News & Molybdenum Price: http://news.molybdenum.com.cn |
Tungsten Copper Electrode and Other Materials Comparison
- Details
- Category: Tungsten Information
- Published on Monday, 18 January 2016 16:44
Tungsten copper powder sintered material having high hardness, high density, high strength, wear resistance, adhesion, excellent electrical and thermal conductivity as well as sweating characteristics, making it ideally suited to withstand high stress resistance welding electrode matching, or as automatic submerged arc welding, carbon dioxide CO2 gas shielded arc welding tip conductive or conductive plate. Tungsten copper flash welding electrode and chromium-copper comparison as follow:
From the table we can see that tungsten copper chromium copper compared to flash welding electrode welding electrode flash at the same working hours, higher welding efficiency, the amount of wear smaller, better weld quality, lower cracking rate life more long, the application is more convenient, and therefore wide range of applications. Vertical automatic welding, soldering conditions when the thickness of 22-28mm, wire directly Φ2.4mm, conductive nozzle aperture when 2.8mm, tungsten, copper and chromium copper conductor conductive nozzle tip wear after welding is very different.
Tungsten copper conductive tip after welding 20m, the aperture remains the prototype, you can still continue to work, in contrast, chromium copper conductive soldering tip less than 2m, its conductivity unilateral eccentric bore wear, maximum diameter enlargement ratio of tungsten copper conductor increases 0.6mm, has been unable to proceed with the welding work. Therefore, resistance welding electrodes and welding conductor tungsten copper powder sintered material having a high hardness, high density, high strength, wear resistance, adhesion, excellent electrical and thermal conductivity and a series of advantages, which has a broad prospect.
Tungsten Copper Supplier: Chinatungsten Online tungsten-copper.com | Tel.: 86 592 5129696; Fax: 86 592 5129797;Email:sales@chinatungsten.com |
Tungsten News & Prices, 3G Version: http://3g.chinatungsten.com | Molybdenum News & Molybdenum Price: http://news.molybdenum.com.cn |
New Technology of Tungsten Copper Electrode—Microwave Infiltration
- Details
- Category: Tungsten Information
- Published on Monday, 18 January 2016 16:42
Actually, microwave infiltration is one of new methods, which combines microwave sintering with traditional infiltration. It has many advantages, such as selective heating (the coupling ability of material and microwave, the ability of microwave absorption is related to the properties of itself, such as electrical conductivity, magnetic conductivity and dielectric constant, which will get diverse heating properties when the material is different in a given microwave field. ), volume heating (Each portion of the object in the portion of the material is heated after the heat acquired, so that the part of the material temperature rises.), non-thermal effect (It general refers to compared with traditional sintering under the same thermal dynamic conditions has remarkable superiority in physical, such as the active sintering of powder material and atomic diffusion rate.) , and uniform structure of infiltration processing. Therefore, microwave infiltration has higher speed of increasing temperature, shorter sintering time, higher energy utilization ratio and uniform structure or excellent properties of the products. Microwave infiltration of microwave sintering equipment is produced by DC magnetron microwave waveguide by introducing the heating chamber, the sample is placed in the cavity is heated sintering. The sketch of structure of the equipment as follow:
The major technical parameters of microwave sintering furnace includes work area, the highest working temperature, thermometric, methods, the range of infrared detection, the precision of temperature control, the out power of microwave, vacuum limit of furnace, the leaking of microwave. At present, the use of microwave sintering heating chamber includes a resonant and non-resonant two, while the cavity can be subdivided into single-mode and multi-mode resonant cavity resonator. Under the same electromagnetic power, single-mode resonant cavity having a stronger magnetic field strength is more suitable for low heating medium. The multimode resonator having multiple resonant modes, the electromagnetic field distribution is more uniform, the structure is relatively simple, suitable for a variety of heating load, the more it is difficult to accurately analyze the data.
Tungsten Copper Supplier: Chinatungsten Online tungsten-copper.com | Tel.: 86 592 5129696; Fax: 86 592 5129797;Email:sales@chinatungsten.com |
Tungsten News & Prices, 3G Version: http://3g.chinatungsten.com | Molybdenum News & Molybdenum Price: http://news.molybdenum.com.cn |