Gold-plated Tungsten Lettering Process
- Details
- Category: Tungsten Information
- Published on Thursday, 21 January 2016 16:59
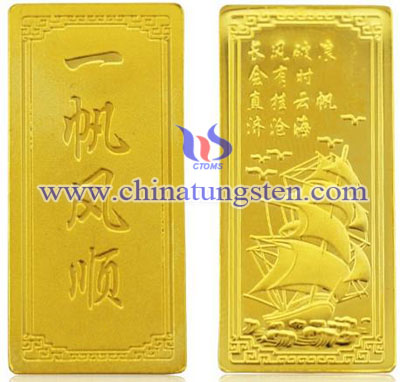
Tungsten Gold Plated Supplier: Chinatungsten Online www.tungsten-alloy.com | Tel.: 86 592 5129696; Fax: 86 592 5129797;Email:sales@chinatungsten.com |
Tungsten News & Prices, 3G Version: http://3g.chinatungsten.com | Molybdenum News & Molybdenum Price: http://news.molybdenum.com.cn |
CVD Diamond Coated Carbide Pretreatment—Transition Applied (1/2)
- Details
- Category: Tungsten Information
- Published on Thursday, 21 January 2016 16:58
Except acid etching and plasma etching to remove cobalt (Co), deposited a transition layer between diamond film and tungsten carbide cutting tool in advance is also a common kind of pretreatment. At present, common types of transition layer can be specifically divided into single-layer transition and composite transition. Single-layer transition includes silicon (Si), chromium (Cr), boron (B), copper (Cu), titanium (Ti), silicon carbide (SiC), silicon nitride (Si3N4), silicon carbide, nitrogen (SiCxNy), titanium nitride (TiN), titanium carbide (TiC), titanium carbonitride (TiCN), (Ti, Si) Nx, diamond-like carbon coating (DLC) and so on; composite transition layer includes tungsten carbide / tungsten (WC / W), titanium carbide / titanium nitride (TiC / TiN), titanium nitride / titanium carbonitride / titanium nitride (TiN / TiCN / TiN), titanium carbonitride / titanium (TiCN / Ti ), chromium / chromium nitride / chromium (Cr / CrN / Cr), and copper / titanium (Cu / T), etc.
There are many effects of the transition layer, such as it blocks out the diffusion of Co, which promotes the growth of graphite in carbon and the matrix; secondly, it decreases the possibility of heat stress appearing caused by the mismatching of crystal lattice parameters and coefficient of thermal expansion between diamond coating and tungsten carbide matrix, thirdly, the transition layer not only can improve the binding force between traditional diamond film and tungsten carbide matrix, but also form a bond of conjunction with two different kinds of materials; and it can increase the density of nucleation of diamond (nucleation, the process of under cooling metal liquid, which is the initial stage of crystallization.) and the binding force of diamond film; last but not least, the transition layer has stable chemical properties and excellent mechanical strength.
Tungsten Carbide Supplier: Chinatungsten Online tungsten-carbide.com.cn | Tel.: 86 592 5129696; Fax: 86 592 5129797;Email:sales@chinatungsten.com |
Tungsten News&Tungsten Prices, 3G Version: http://3g.chinatungsten.com | Molybdenum News & Molybdenum Price: http://news.molybdenum.com.cn |
Rose Gold-plated Tungsten Rings
- Details
- Category: Tungsten Information
- Published on Thursday, 21 January 2016 16:57
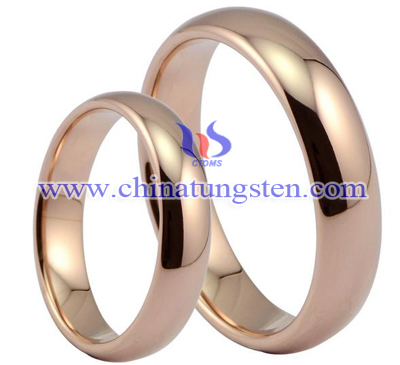
Tungsten Gold Plated Supplier: Chinatungsten Online www.tungsten-alloy.com | Tel.: 86 592 5129696; Fax: 86 592 5129797;Email:sales@chinatungsten.com |
Tungsten News & Prices, 3G Version: http://3g.chinatungsten.com | Molybdenum News & Molybdenum Price: http://news.molybdenum.com.cn |
Gold-plated Tungsten Solvent Method Hot-dipped Process
- Details
- Category: Tungsten Information
- Published on Thursday, 21 January 2016 16:54
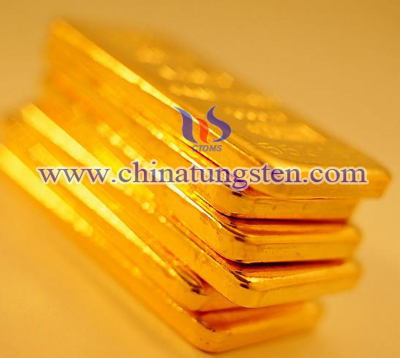
Tungsten Gold Plated Supplier: Chinatungsten Online www.tungsten-alloy.com | Tel.: 86 592 5129696; Fax: 86 592 5129797;Email:sales@chinatungsten.com |
Tungsten News & Prices, 3G Version: http://3g.chinatungsten.com | Molybdenum News & Molybdenum Price: http://news.molybdenum.com.cn |
Electrospinning Prepares Tungsten Trioxide Nanofiber
- Details
- Category: Tungsten Information
- Published on Thursday, 21 January 2016 15:17
Electrospinning is a special form of polymer electrostatically atomizing fluid, in which case the substance is not split atomizing minute droplets, but is the polymer micro-jets that can run for a long distance, eventually solidified into a fiber. Electrospinning is a special fiber manufacturing process, polymer solution or melt spinning have injection in a strong electric field. In the electric field, the droplets will be made at the needle into conical spherical, and extend from the tip of the cone to obtain a fiber filaments. This way can produce nanoscale diameter polymer filaments. Electrospinning and its manufacturing apparatus is simple, low cost spinning, spinning is used in wide range of materials, and it has become one of the main ways the effective nano fiber material. Electrospinning technique has prepared a wide variety of nano-fibers, including organic, organic / inorganic composite and inorganic nanofibers.
Tungsten trioxide prepared electrospinning nanofibers, the technology can be divided into two steps: preparation and spinning the precursor solution. Precursor gel can be obtained from a mixed polymer solution and tungsten precursor solution. Tungsten precursor is ammonium tungstate solution that was dissolved in dimethylformamide (DMF). Then the two precursor solutions are mixed at room temperature after mixing embrace 15min, then heating it at 50 about ℃24h. Electrospinning process precursor gel is packed in 3ML syringe barrel, adding 21 flat-head stainless steel electrode pin connector to high voltage power supply. The precursor gel pump at 3mL/h during delivery by the injection, the needle and the ground electrode foil target distance is 15cm, where the potential difference is 10kV. Calcinating spun nanofiber 4h at 500 ℃ so that can form tungsten trioxide nanocrystals.
Tungsten Oxide Supplier: Chinatungsten Online www.tungsten-oxide.com | Tel.: 86 592 5129696; Fax: 86 592 5129797;Email:sales@chinatungsten.com |
Tungsten News & Prices, 3G Version: http://3g.chinatungsten.com | Molybdenum News & Molybdenum Price: http://news.molybdenum.com.cn |
Explore Tungsten Trioxide Photocatalytic Property
- Details
- Category: Tungsten Information
- Published on Thursday, 21 January 2016 14:53
Photocatalyst is a general term of nanoscale titanium dioxide that has a photocatalytic function on behalf of the optical semiconductor material, which is applied to the substrate surface. Under the action of ultraviolet light, it can effectively degrade the air poisonous gases; can effectively kill a variety of bacteria. Fungi and bacteria can release toxins decomposition and it is a harmless treatment; it also has a deodorizing, antifouling, air purification and other functions. Photocatalyst materials are nano TiO2, ZnO, CdS, WO3, Fe2O3, PbS, SnO2, ZnS, SrTiO3, SiO2, etc. In all of the photocatalyst material, in addition, the enzyme aldehyde not only has high photocatalytic activity, and has acid corrosion, chemical resistant, non-toxic, etc. Photocatalyst has a high price, and therefore most of the use of Nano-titanium dioxide as the main raw material on the market.
As can be seen from the figure, the atomic weight of tungsten (W) is 74, and titanium element atomic weight is 22, the structure of atomic is more complicated. Tungsten is rare heavy metals. It was found that tungsten trioxide (WO3) and titanium dioxide (TiO2) are similar. However, they are not the same nature. Energy tungsten trioxide (WO3) outer electrons is less active compared to the titanium dioxide, its electron volts insufficient 3.2, that is to say, just 400 nm wavelength of visible light is activated.
Studies have shown that, photocatalyst tungsten trioxide is indeed light catalysis in the indoor environment, which can purify the indoor environment, for example, in fluorescent lamps (also called fluorescent) light irradiation (wavelength 400 nm) occurred photocatalysis. However, the activity is not enough. The cost of tungsten trioxide nanoscale production is too high; the production process is complex, the process requires a large number of civilian photocatalyst tungsten trioxide.
Tungsten Oxide Supplier: Chinatungsten Online www.tungsten-oxide.com | Tel.: 86 592 5129696; Fax: 86 592 5129797;Email:sales@chinatungsten.com |
Tungsten News & Prices, 3G Version: http://3g.chinatungsten.com | Molybdenum News & Molybdenum Price: http://news.molybdenum.com.cn |
Preparing Potassium Doped in Round Tungsten Aluminum Strip from Ammonium Paratungstate—Preparation Method
- Details
- Category: Tungsten Information
- Published on Wednesday, 20 January 2016 20:10
Potassium doped in round aluminum tungsten is the raw materials in electric light manufacturing, electronic devices in ANTIDROOPING tungsten filament and vacuum spray plating tungsten hinge wire and other high-temperature heating body and resistance to high temperature components. A method for preparing potassium doped in round aluminum tungsten strip is introduced in this paper.
Specific steps:
1. Choice of materials: select special size of ammonium paratungstate distribution with crystalline in FSSS for 40 to 50μm and loose density in 2.1~2.5g/cm3 as raw material;
2 Mild reduction ammonium paratungstate: the raw material mild reduction in furnace in seven ranges of temperature to produce special intermediate ammonium tungsten bronze (ATB). Among them: seven ranges of temperature are 300, 360, 400, 420, 430, 450, 420℃, rate of hydrogen flow at 0.2~0.3m3/h,;
3. AKS doping: mix wet ATB with potassium silicate, aluminum nitrate solution dissolved in deionized water, and make potassium, silicon, aluminum adopted in the pores of ATB, doped ATB formed;
4. Direct reduction: ATB directly reduction in seven temperature reduction furnace a and fine grain tungsten powder B with FSSS 2.2 ~ 2.6μm generated; coarse grain tungsten powder D with FSSS 3.3~4.2μm generated in the same way;
5. Pickling: washing fine grain tungsten powder B, coarse tungsten powder D respectively with hydrochloric acid of concentration 6~8%, hydrofluoric acid of 6~8% to remove dopant and impurities;
6. Mixing powder: mixing the fine particles of tungsten powder B, coarse grain tungsten powder D according to a certain weight ratio after pickling;
7. Cool down and static pressure;
8. Pre-sintering: 120 ~45min under temperature of 40℃;
9. Vertical melting: directly electricity to sintering under the protection of hydrogen gas.
APT Supplier: Chinatungsten Online ammonium-paratungstate.com | Tel.: 86 592 5129696; Fax: 86 592 5129797;Email:sales@chinatungsten.com |
Tungsten News&Tungsten Prices, 3G Version: http://3g.chinatungsten.com | Molybdenum News & Molybdenum Price: http://news.molybdenum.com.cn |
Ammonium Metatungstate Prepared from Ammonium Paratungstate
- Details
- Category: Tungsten Information
- Published on Wednesday, 20 January 2016 20:08
Ammonium metatungstate is an important tungsten compound, mainly used in petroleum cracking, organic synthesis, nitration and other industries as a catalyst. The dosage of ammonium metatungstate is increased with the rapid development of oil refining. The traditional way crystallization to prepare ammonium metatungstate from ammonium paratungstate has high investment, energy consumption and unstable quality of the resulting product, poor solubility, can not meet the need of catalyst.
Ammonium paratungstate used as raw material to leaching out the solution, then dilute ammonium metatungstate solution turns into a concentrated solution, and spray and drying the concentrated ammonium metatungstate solution to prepare ammonium metatungstate crystal.
Specific steps are as follows:
1. Leaching out the wet ammonium paratungstate: to wet ammonium paratungstate content 5 ~ 10% water as raw material and mix with nitric acid (HN03) to prepare dilute ammonium metatungstate solution;
2. The dilute ammonium metatungstate prepared by the step 1 goes through many times of static and precipitation, filtration and heat to concentration and then obtain the concentrated ammonium metatungstate solution;
3. Spray and dry, make the material dried quickly into ammonium metatungstate powder.
Its advantages lie in:
1. There is no need to roasting, so the rotary furnace equipment is useless, therefore to reduce investment of fixed;
2. The actual recovery rate of ammonium metatungstate increased;
3. Slowly and continuously feeding overcomes the problem of low solubility of ammonium metatungstate, to get ammonium metatungstate solution with high content of tungsten trioxide;
4. Use wet ammonium paratungstate product as raw material saves the process of drying and packing, to achieve the purpose of saving energy and reducing cost.
APT Supplier: Chinatungsten Online ammonium-paratungstate.com | Tel.: 86 592 5129696; Fax: 86 592 5129797;Email:sales@chinatungsten.com |
Tungsten News&Tungsten Prices, 3G Version: http://3g.chinatungsten.com | Molybdenum News & Molybdenum Price: http://news.molybdenum.com.cn |
Sodium tungstate concentration on Ni-Co-W-P alloy coating influence 2/2
- Details
- Category: Tungsten Information
- Published on Wednesday, 20 January 2016 18:37
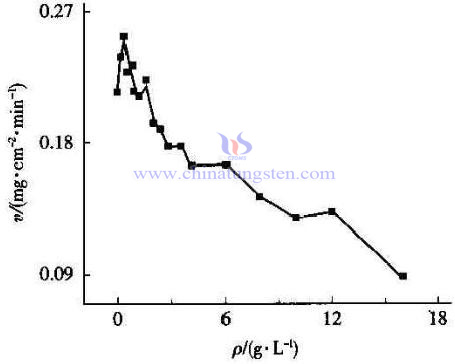
Sodium Tungstate Supplier: Chinatungsten sodium-tungstate.com | Tel.: 86 592 5129696; Fax: 86 592 5129797;Email:sales@chinatungsten.com |
Tungsten News & Prices, 3G Version: http://3g.chinatungsten.com | Molybdenum News & Molybdenum Price: http://news.molybdenum.com.cn |
Sodium tungstate concentration on Ni-Co-W-P alloy coating influence 1/2
- Details
- Category: Tungsten Information
- Published on Wednesday, 20 January 2016 18:34
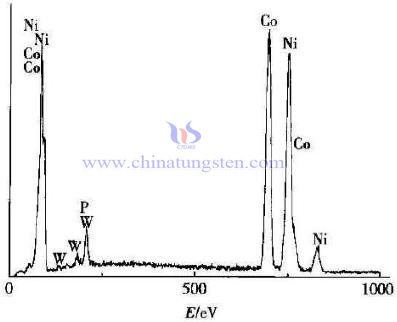
Sodium Tungstate Supplier: Chinatungsten sodium-tungstate.com | Tel.: 86 592 5129696; Fax: 86 592 5129797;Email:sales@chinatungsten.com |
Tungsten News & Prices, 3G Version: http://3g.chinatungsten.com | Molybdenum News & Molybdenum Price: http://news.molybdenum.com.cn |