Tungsten Oxide Ceramic XRD Pattern
- Details
- Category: Tungsten Information
- Published on Friday, 09 March 2018 10:08
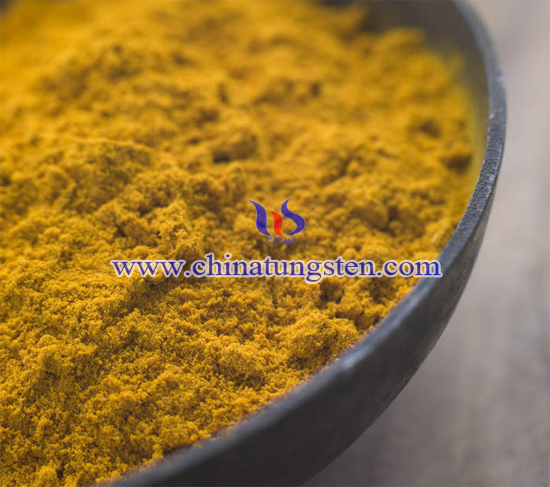
The figure is a diagram of tungsten oxide ceramics sintered at different holding temperatures. Since the crystal structure of tungsten oxide ceramics is very complicated, we narrow down the scanning angle to 20-30 ° to observe the change of the triple peak of tungsten oxide ceramics. From the figure, we can see that the crystal structure of the tungsten oxide ceramic does not change substantially when it is sintered at a temperature of 900-1000°C. However, the XRD peak of the tungsten oxide ceramic moves to a small angle when sintering at a temperature of 1050-1100°C, and the blue shift occurs.
Holding Temperature Affects Tungsten Oxide Ceramics
- Details
- Category: Tungsten Information
- Published on Friday, 09 March 2018 10:02
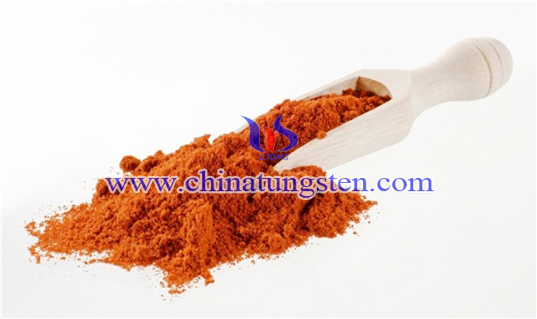
It can be clearly seen from the figure that as the soaking temperature increases, the grain size of the tungsten oxide ceramic increases. When the holding temperature is 900-1000°C, there are many small-sized grains in the sample. When the holding temperature is 1050-1150 ℃, the small grains in the tungsten oxide ceramics disappear, and the grains increase obviously. Also found at 1150 ℃ insulation tungsten oxide ceramics, although the larger grain size. However, its porosity is also significantly increased, the densification of tungsten oxide ceramics worsened.
Equation of Sintering Densification
- Details
- Category: Tungsten Information
- Published on Thursday, 08 March 2018 20:50
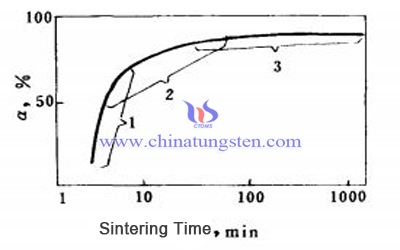
Effect of External Force on Sintering Shrinkage
- Details
- Category: Tungsten Information
- Published on Thursday, 08 March 2018 20:46
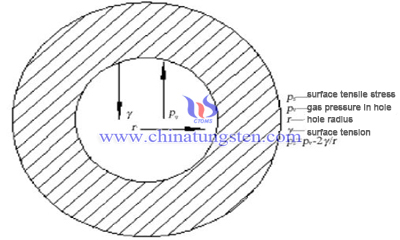
Characteristics of Liquid Phase Sintering
- Details
- Category: Tungsten Information
- Published on Thursday, 08 March 2018 20:43
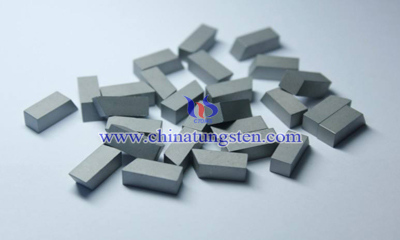
Binary Phase Diagram of WC-Co Tungsten Carbide
- Details
- Category: Tungsten Information
- Published on Thursday, 08 March 2018 20:41
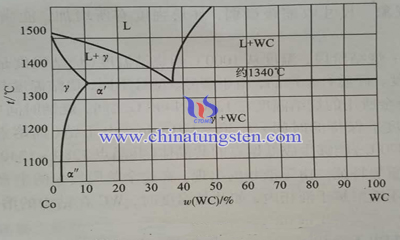
Tungsten Diselenide Preparation
- Details
- Category: Tungsten Information
- Published on Thursday, 08 March 2018 18:36
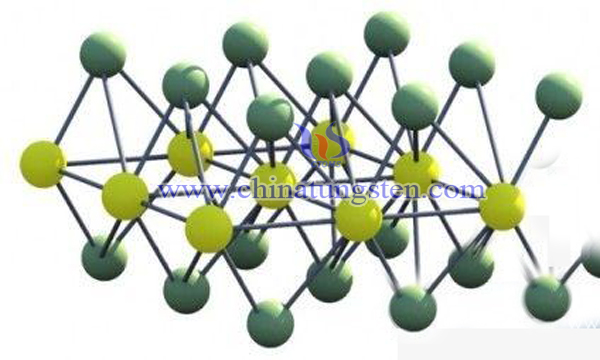
Tungsten diselenide (WSe2) is a kind of semiconductor material with a graphite-like layered structure. It is composed of closely packed Se-W-Se hexagonal crystals, and is based on van der Waals force to form a single layer of two-dimensional material. The WSe2 film has a forbidden band width of 1-2eV and a high visible light absorption efficiency. It can be used as an absorbing layer and photoelectrochemical electrode material for solar cells.
Preparation of Ultrapure Tungsten Powder with Blue Tungsten Oxide
- Details
- Category: Tungsten Information
- Published on Thursday, 08 March 2018 18:00
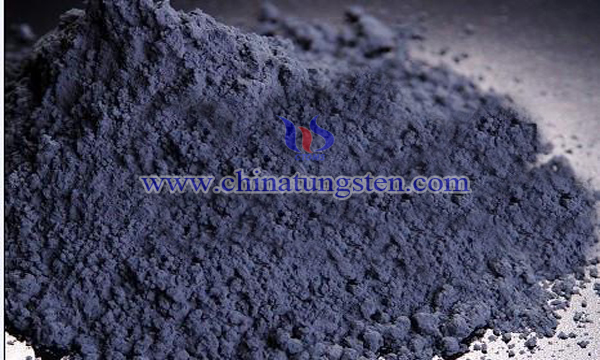
Blue tungsten oxide is the main tungsten oxide product at present. It is the main raw material for making ultra pure and ultra-fine tungsten powder. It uses blue tungsten oxide to restore ultra pure tungsten powder, and its process includes four processes: calcination, reduction, acid washing and anti oxidation.
The Common Road to The Price of Tungsten Rhenium Alloy
- Details
- Category: Tungsten Information
- Published on Thursday, 08 March 2018 17:53
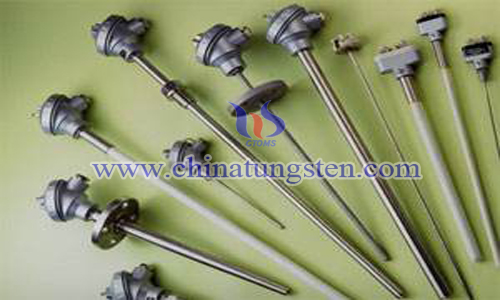
Tungsten, as a high temperature resistant metal material, is used as the filament or electrode of the energy saving lamp and as a variety of electronic emitter. But the tungsten itself has the problem of brittle and low plasticity, which greatly reduces the life of its use. In order to reduce the brittleness of tungsten and to improve its plasticity, the traditional method is to increase its properties by adding rare earth metals in tungsten to form tungsten based alloys.
ITER Plasma Tungsten Coating
- Details
- Category: Tungsten Information
- Published on Thursday, 08 March 2018 17:47
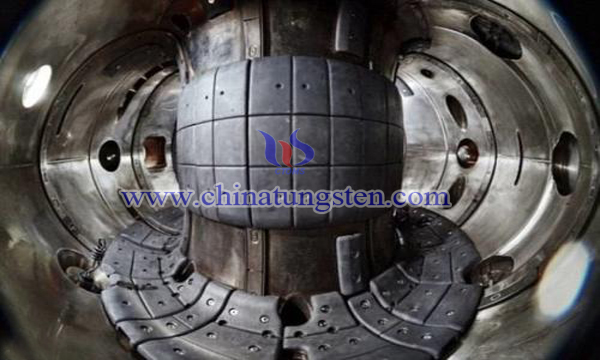
Tungsten has high melting point, excellent thermal conductivity, low sputtering yield and high sputtering threshold, low vapor pressure and low tritium retention property. It is considered as the most promising divertor and first wall plasma facing material for fusion experimental device and fusion reactor in the future.