Tungsten Oxide/Graphene Composites
- Details
- Category: Tungsten Information
- Published on Tuesday, 13 March 2018 08:41
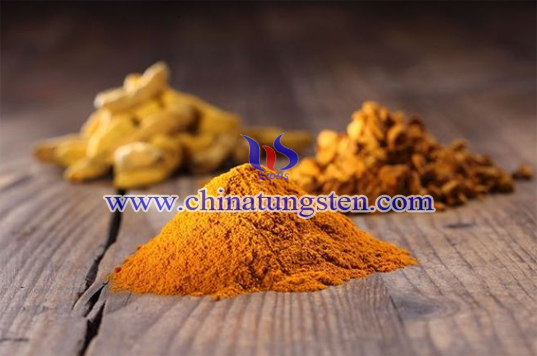
Graphene is a two-dimensional planar material with a six-membered ring structure. Its unique electronic structure and atomic structure have made graphene a widespread concern in the field of gas sensors such as tungsten oxide sensors. Semiconductor materials produced by compounding graphene and tungsten oxide have excellent optical, electrical, and mechanical properties.
Tungsten Oxide Activation Problem
- Details
- Category: Tungsten Information
- Published on Tuesday, 13 March 2018 08:35
With the development of sensor technology, the research direction of semiconductor gas sensors is developing toward normal temperature, integration, and low power consumption. Tungsten oxide has attracted the attention of researchers because of its high sensitivity. Researchers have achieved room temperature detection by changing the activation mode. However, tungsten oxide room temperature sensors still have the disadvantages of low sensitivity, slow response recovery, and poor selectivity and stability. These defects are also the challenges faced by the practical use of room temperature tungsten oxide gas sensors.
Tungsten Oxide Sensor Metal Activation
- Details
- Category: Tungsten Information
- Published on Monday, 12 March 2018 10:55
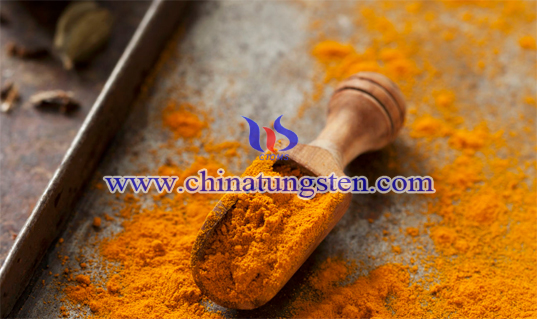
Adding metal elements to the tungsten oxide sensor can significantly improve the sensor response characteristics and reduce the sensor operating temperature. Metal catalysts such as iron and titanium can increase the surface reaction sites of tungsten oxide sensors. However, precious metal catalysts such as silver and platinum can not only provide surface active sites, but also can change the electron concentration of the conduction band of the tungsten oxide sensor by doping, thereby improving the characteristics of the tungsten oxide sensor.
Tungsten Oxide Sensor Gas Sensitivity
- Details
- Category: Tungsten Information
- Published on Monday, 12 March 2018 10:52
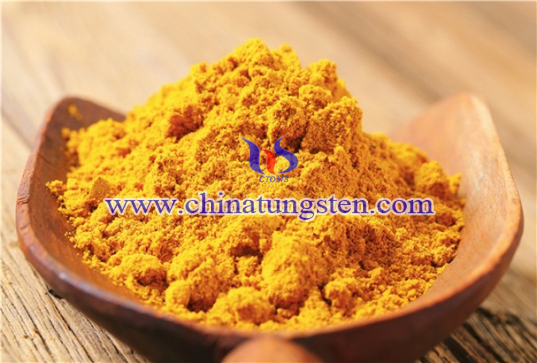
A lead-containing tungsten oxide sensor is prepared by hydrothermal synthesis and the operating temperature is lowered to room temperature. The hydrothermally synthesized tungsten oxide gas-sensitive material has better gas-sensitivity than the tungsten oxide gas-sensitive material prepared by the mechanical mixing method and the pure tungsten oxide gas-sensitive material. The addition of lead effectively changed the response characteristics of the sensor. The sensitivity to hydrogen at room temperature was 34 and the response time was 24 s. And it has very good selectivity and repeatability.
Tungsten Oxide Electrospinning
- Details
- Category: Tungsten Information
- Published on Monday, 12 March 2018 10:48
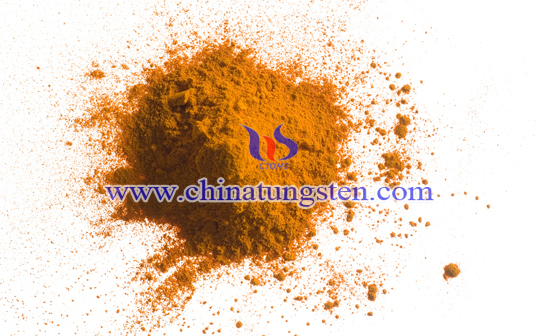
Electrospinning is a special form of tungsten oxide polymer fluid electrostatic atomization. The tungsten oxide split by atomization at this time is not a tiny droplet, but a tiny jet of polymer, which can run for a long distance and eventually solidify into a tungsten oxide fiber.
Tungsten Oxide Ceramics EDS Spectroscopy
- Details
- Category: Tungsten Information
- Published on Monday, 12 March 2018 10:29
The leakage current of the tungsten oxide ceramic varistor under the action of the applied voltage is a decreasing process with time. This shows that the grain boundary barrier model of tungsten oxide varistors is different from conventional varistors such as zinc oxide.
UV Light Affects the Gas Sensitive Properties of Tungsten Oxide
- Details
- Category: Tungsten Information
- Published on Monday, 12 March 2018 08:55
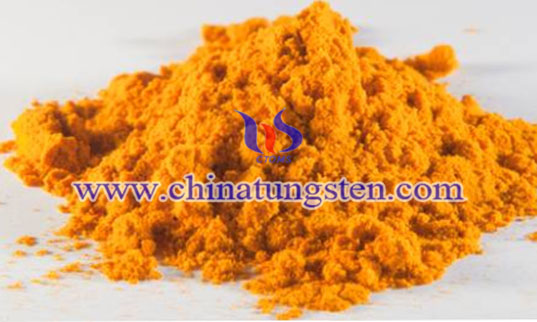
Researchers have found that ultraviolet and visible light can provide energy for the surface chemical reaction of tungsten oxide gas-sensitive materials, thereby accelerating the rate of chemical reactions, thereby improving its gas-sensing properties. The study found that ultraviolet light affects the gas-sensitive properties of tungsten oxide gas mainly through two aspects:
Sintering Densification of Tungsten Carbide
- Details
- Category: Tungsten Information
- Published on Sunday, 11 March 2018 11:06
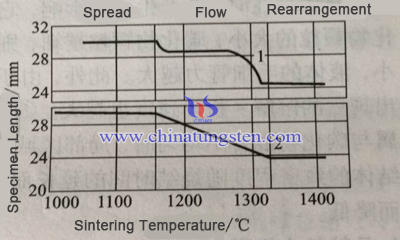
Influence Factors of Sintering Densification
- Details
- Category: Tungsten Information
- Published on Sunday, 11 March 2018 11:03
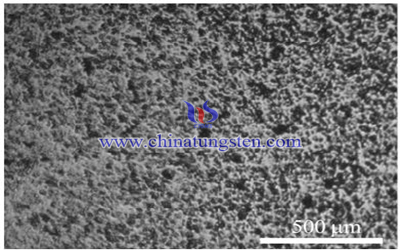
Influence Factors of η Phase
- Details
- Category: Tungsten Information
- Published on Sunday, 11 March 2018 11:00
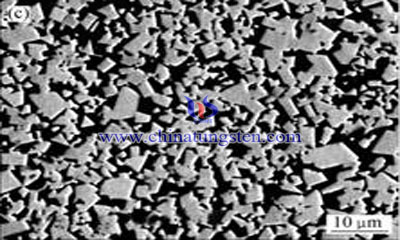