Tungsten-Based Plasma Facing Components
- Details
- Category: Tungsten Information
- Published on Thursday, 02 August 2018 18:15
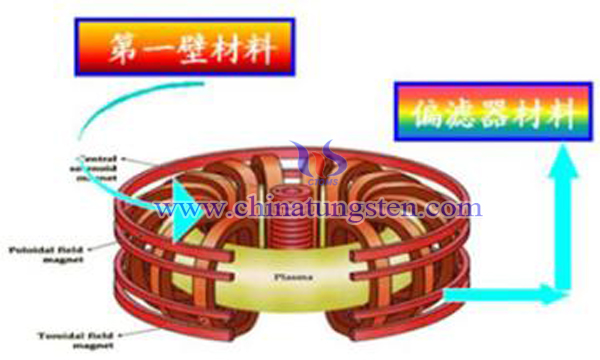
Tungsten materials are considered to be plasma facing components (PFC) for the preparation of the International Thermonuclear Experimental Reactor (ITER) due to its high melting point, high sputtering threshold, high thermal conductivity, low vapor pressure, and low hydrogen isotope retention.
Almonty Industries to Improve Tungsten Concentrate Output at Panasqueira Mine in Portugal
- Details
- Category: Tungsten Information
- Published on Thursday, 02 August 2018 11:22
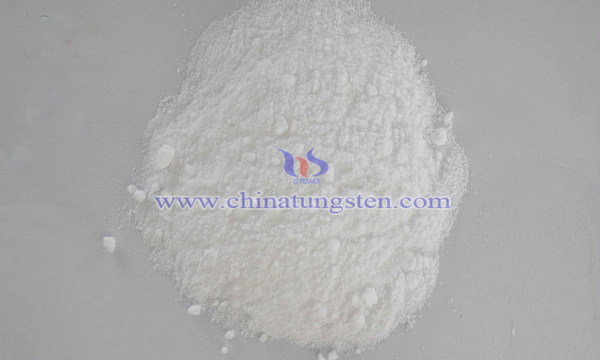
Almonty Industries Inc. is pleased to announce that the ore sorting equipment has arrived at its Panasqueira mine in Portugal. The equipment was released by customs last week and during the 23rd and 24th of July 2018, the entire installation arrived at the mine.
Niobium Tungsten Oxides Help Make Faster-charging Batteries
- Details
- Category: Tungsten Information
- Published on Thursday, 02 August 2018 11:20
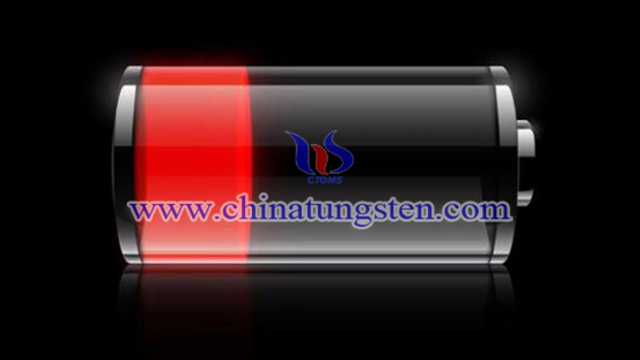
Is there an alternative to nanostructuring electrode materials to speed up ionic diffusion in lithium-ion batteries and so increase their maximum power output and charging rates? Yes, according researchers at the University of Cambridge in the UK, who have shown that two complex niobium tungsten oxides can intercalate large amounts of lithium even when the oxides are microns in size.
Environmentally Friendly Tungsten-Based Catalysts
- Details
- Category: Tungsten Information
- Published on Wednesday, 01 August 2018 18:14
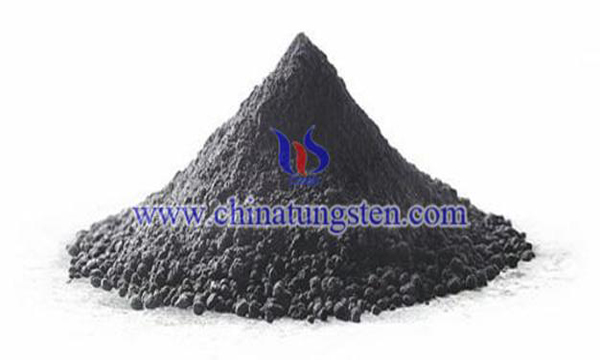
In order to implement the Montreal Protocol to protect the Earth's ozone layer, countries around the world have introduced zero-ODP values of hydrofluorocarbons (HFCs) and hydrofluoroolefins (HFOs) to phase out chlorofluorocarbons (CFCs) and hydrofluorides Chlorocarbons (HCFCs). At present, HFCs and HFOs have been widely used as refrigerants, cleaning agents, foaming agents, fire extinguishing agents, etchants, and etc.
High-Efficiency Method for Separating Tungsten and Molybdenum
- Details
- Category: Tungsten Information
- Published on Wednesday, 01 August 2018 17:38
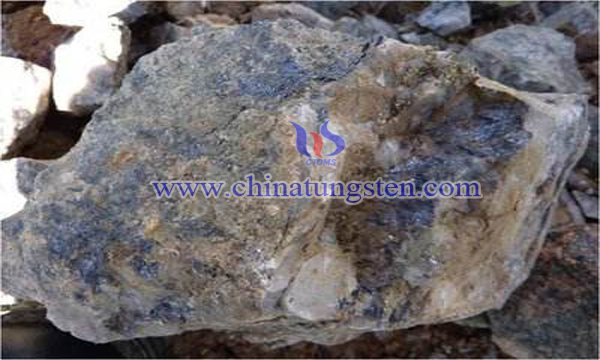
With the continuous exploitation of high-quality tungsten-molybdenum ore resources, complex tungsten-molybdenum symbiotic mineral resources are gradually being consumed. However, the impurity content in tungsten product or molybdenum product seriously affects its performance. The most difficult impurity element to remove from tungsten products is molybdenum, while for molybdenum products, tungsten is the most difficult to separate. In order to improve the performance of tungsten and molybdenum products, separation of tungsten and molybdenum is necessary. Therefore, in order to efficiently utilize these tungsten-molybdenum symbiotic mineral resources, the separation of tungsten and molybdenum is the key.
Tungsten-Nickel Cemented Carbide with Strong Acid and Alkali Resistance
- Details
- Category: Tungsten Information
- Published on Wednesday, 01 August 2018 17:34
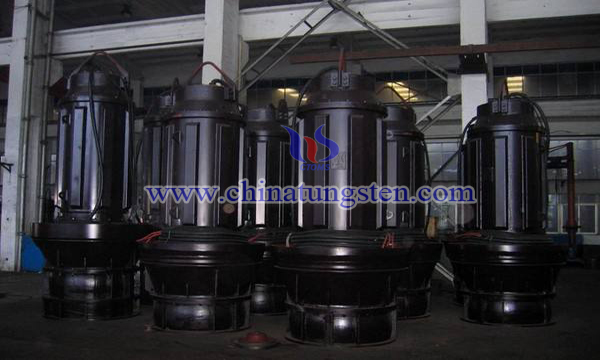
The flow meter is used to measure the flow rate and speed of the liquid when it is flowing. Typically, the movement shaft of a flow meter is made of stainless steel. It is well known that stainless steel has good corrosion resistance. The corrosion resistance of stainless steel depends on the alloying elements contained in the steel. Chromium is the basic element for obtaining corrosion resistance of stainless steel. In addition to chromium, commonly used alloying elements include nickel, molybdenum, titanium, niobium, copper, and nitrogen to meet the requirements of stainless steel structure and properties for various applications.
However, the flow shafts, which are exposed to chemicals such as strong acids and alkalis for a long time, would be corroded. In addition, stainless steel is added with other alloying elements, which makes the steel material impure, so there will be deviations in the magnetic field, resulting in inaccurate measurement. In order to improve the acid-base resistance of the material without magnetic properties, some scholars have proposed a preparation method of tungsten-nickel cemented carbide by:
The raw materials are prepared by weight percentage: 90% tungsten alloy (WC) powder, 9.6% nickel (Ni) powder and 0.4% chromium carbide (Cr3C2) powder; after the raw materials are subjected to mixed ball milling for 36 hours, the material is precipitated for 24 hours and dried for 100 minutes. ± 5 minutes, the temperature is controlled at 85 ° C ± 5 ° C; and then mixed with 10 ml of glue per 1 Kg of mixed raw materials, add SBS-modified binder (0.1Kg of SBS-modified binder per 1Kg of mixed raw materials); finally sintered in a vacuum furnace, control from 300 ° C to 1450 ° C, and then cool down to normal temperature, the product is released.
The WC powder has a particle size of 2.3 to 2.8 μm, the Ni powder has a particle size of 1.5 to 2.0 μm, and the Cr3C2 has a particle size of 2.0 to 2.6 μm.
Because WC powder, Ni powder and Cr3C2 powder are used as alloying elements, the acid and alkali resistance of the material can be improved, the service life is greatly prolonged, and nickel is used instead of the conventional cobalt in the material, so that the material is not magnetic, so it is made. The tungsten-nickel cemented carbide can be used to make the movement shaft of the acid-base flow meter and the movement shaft of the instrument that needs to avoid magnetic interference.
- Tungsten Alloy Manufacturer & Supplier, Chinatungsten Online: www.tungsten-alloy.com
- Tungsten News & Prices of China Tungsten Industry Association: www.ctia.com.cn
- Molybdenum News & Price: news.molybdenum.com.cn
- Tel.: 86 592 5129696; Fax: 86 592 5129797; Email: sales@chinatungsten.com
A Preparation Method of Ultrafine Grain Tungsten-Copper Alloy
- Details
- Category: Tungsten Information
- Published on Wednesday, 01 August 2018 17:30
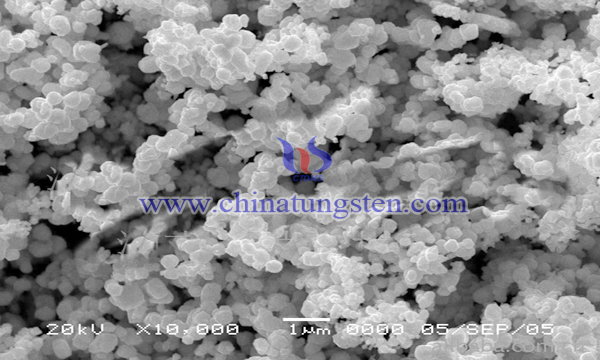
Pure tungsten and tungsten-based high specific gravity alloy materials have the advantages of high melting point, high density, high strength, high hardness and high wear resistance. In addition, it has small thermal expansion coefficient, good corrosion resistance and oxidation resistance, and good electrical and thermal conductivity. Therefore, it has been widely used in semiconductor industry, defense industry and aerospace. It is used as a counterweight and shock absorbing material on aircraft; it is used as armor-piercing projectiles and submunitions in military industry; it is used as an anti-X-ray shielding material in the medical industry; it is used as a high-specific gravity alloy on Vibrator electrode material of mobile phones, etc.
A Method to Separate Tungsten and Tin from High-Tin Tungsten Concentrate
- Details
- Category: Tungsten Information
- Published on Wednesday, 01 August 2018 17:25
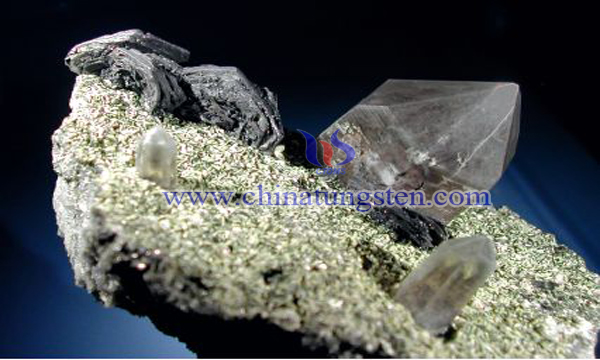
Tungsten is mainly enriched in the granite contact metamorphic zone in the crust, and is more or less symbiotic with tin containing minerals in many tungsten deposits, especially porphyry-type tungsten deposits - such tungsten-containing polymetallic vulcanization ore is often associated with tin-containing minerals.
Composite Lubricant Film of Tungsten Sulfide and Tungsten Nitride
- Details
- Category: Tungsten Information
- Published on Wednesday, 01 August 2018 17:19
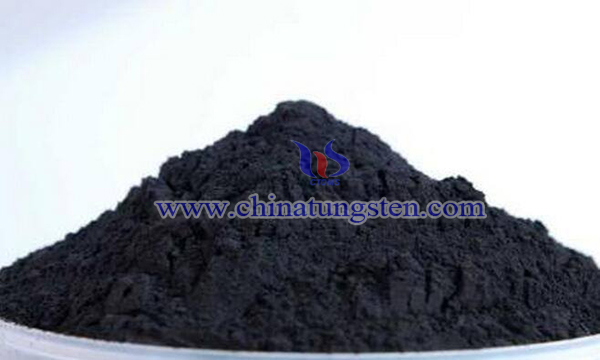
It is well known that the movement of mechanical parts is always accompanied by friction and wear, which is generally lubricated in order to reduce the friction and wear between moving mechanical parts. The solid lubricating film material has been widely used because it has the advantages of avoiding contamination of industrial parts by liquid lubrication, and being able to work under severe conditions such as low temperature and high temperature.
A Preparation Process that Lowers the Production Cost of Tungsten Metallurgy
- Details
- Category: Tungsten Information
- Published on Wednesday, 01 August 2018 17:14
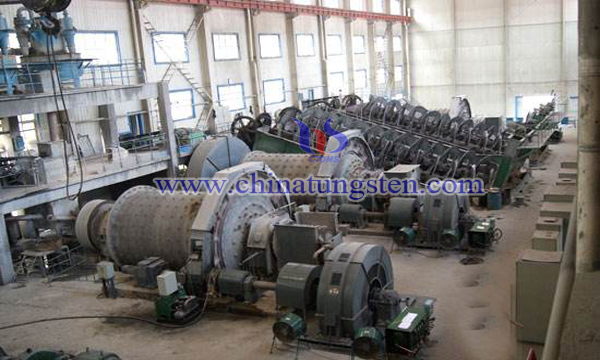
The alkali extraction method is the main method for smelting tungsten concentrate. Due to its strong adaptability to raw materials and high extraction rate, it has become the mainstream process for processing tungsten mineral raw materials. However, in the actual tungsten smelting process, a high tungsten leaching rate is required, and the consumption of NaOH is large. For example, when processing a wolframite concentrate, the NaOH consumption is 1.5 to 2 times the theoretical amount when 99% leaching rate is obtained. When the scheelite concentrate is treated, the NaOH consumption is even 3 to 4 times of the theoretical amount.