Preparing Tungsten Trioxide Contained Denitration Catalyst Active Mother Liquor
- Details
- Category: Tungsten Information
- Published on Friday, 25 March 2016 14:44
- Written by chunyan
- Hits: 245
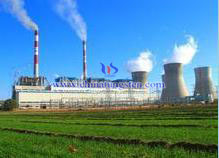
Tungsten Oxide Supplier: Chinatungsten Online www.tungsten-oxide.com | Tel.: 86 592 5129696; Fax: 86 592 5129797;Email:sales@chinatungsten.com |
Tungsten News & Prices, 3G Version: http://3g.chinatungsten.com | Molybdenum News & Molybdenum Price: http://news.molybdenum.com.cn |
Tungsten Trioxide Controls SCR Denitration Catalyst Deactivation
- Details
- Category: Tungsten Information
- Published on Thursday, 24 March 2016 17:26
- Written by chunyan
- Hits: 242
Tungsten Oxide Supplier: Chinatungsten Online www.tungsten-oxide.com | Tel.: 86 592 5129696; Fax: 86 592 5129797;Email:sales@chinatungsten.com |
Tungsten News & Prices, 3G Version: http://3g.chinatungsten.com | Molybdenum News & Molybdenum Price: http://news.molybdenum.com.cn |
Tungsten Carbide Wear Plate — Wear Form(2/2)
- Details
- Category: Tungsten Information
- Published on Thursday, 24 March 2016 17:13
- Written by xiaobin
- Hits: 248
Another failure form of tungsten carbide wear plate is solder peeling bore wear. Under the impact of concrete, the surface of the ring alloy plate glasses has cracks, which is due to poor wear resistance of its internal bore, can not fully resist the impact of concrete and wear. Flowing concrete will has relative movement with internal bore of tungsten carbide wear plate, which makes the solid surface and the material properties of the surrounding surface has changed, easily deformed due to uneven force. Therefore, enhanced tungsten carbide wear plate bore is critical and it has enhanced the protection of surface alloy ring and reduces the deformation effect. In order to improve the service life of tungsten carbide wear plate, we can improve the wear resistance of internal bore of wear plate from material and structure.
We have two choices from the material that welding electrode wear and use tungsten carbide directly. By experimental comparison can be drawn with the following electrode wear carbide abrasive wear table:
From the graph above we can clearly see that the wear resistance of tungsten carbide is 5 times better than the welding electrode so that tungsten carbide as the material for the internal bore is a best choice. For the bore structure of wear plate, in order to avoid high temperatures generated inlaid alloy caused defects, the researchers used a related set of inlaid alloy structure, effectively extends the life of tungsten carbide wear plate.
Tungsten Carbide Supplier: Chinatungsten Online tungsten-carbide.com.cn | Tel.: 86 592 5129696; Fax: 86 592 5129797;Email:sales@chinatungsten.com |
Tungsten News&Tungsten Prices, 3G Version: http://3g.chinatungsten.com | Molybdenum News & Molybdenum Price: http://news.molybdenum.com.cn |
Waste SCR Denitration Catalyst Recycles Tungsten Trioxide - Secondary Alkaline Leaching Method
- Details
- Category: Tungsten Information
- Published on Thursday, 24 March 2016 17:24
- Written by chunyan
- Hits: 258
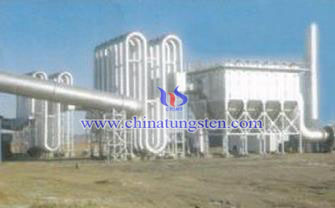
Tungsten Oxide Supplier: Chinatungsten Online www.tungsten-oxide.com | Tel.: 86 592 5129696; Fax: 86 592 5129797;Email:sales@chinatungsten.com |
Tungsten News & Prices, 3G Version: http://3g.chinatungsten.com | Molybdenum News & Molybdenum Price: http://news.molybdenum.com.cn |
Tungsten Carbide Wear Plate — Wear Form(1/2)
- Details
- Category: Tungsten Information
- Published on Thursday, 24 March 2016 17:10
- Written by xiaobin
- Hits: 243
Generally, the medium of tungsten carbide wear plate is concrete, which is composed of cement, water, fine coarse aggregate and other additives and the hardness index converted to a Rockwell hardness of between about HRC40-50. In the process, the main wear forms can be divided into two types, one is in the process of cutting ring reversal, wear plate and floating cutting ring contacts and has grain wear and erosion; the other is in the process of inhaling or pumping, the internal hole of wear plate has low stress wear and erosion.
After concrete pump working for some time, there is a gap between tungsten carbide wear plate and cutting ring. Theoretically, grinding compounds friction and grinding compounds wear of the sliding contact surfaces are generally the form of typical wear. Both wear plate and cutting ring are tungsten carbide and form a pair of friction, the floating cutting ring swings back and forth on tungsten carbide wear plate quickly. Both of them form grain wear by surface contact constantly.
In addition, there are still ore, quartz sand and some other hard particles, and the concrete also belongs to corrosive medium, which will further exacerbate the grinding compounds wear of tungsten carbide wear plate. At present, with the increasing height of the building, pumping height and pressure is also rising, which for carbide glasses plate and cutting ring put forward higher requirements. As time goes by, it will gradually appear larger gaps or partial abrasion between the cutting ring and the wear plate, and leading to failure of the wear plate finally.
Tungsten Carbide Supplier: Chinatungsten Online tungsten-carbide.com.cn | Tel.: 86 592 5129696; Fax: 86 592 5129797;Email:sales@chinatungsten.com |
Tungsten News&Tungsten Prices, 3G Version: http://3g.chinatungsten.com | Molybdenum News & Molybdenum Price: http://news.molybdenum.com.cn |