Tungsten Carbide Wear Plate (1/2)
- Details
- Category: Tungsten Information
- Published on Tuesday, 22 March 2016 16:55
- Written by xiaobin
- Hits: 243
With the rapid development of technology and living standard, a number of skyscrapers and infrastructure requirements are also rising. While it is essential that concrete industry with high strength and high performance involvement, which put forwards the equipments of the concrete. Concrete pump is one of the most critical parts, which consists of the pump and the delivery pipe, is a use of pressure, mechanical concrete continuously conveyed along the pipeline, mainly used in housing construction, bridge and tunnel construction. According to the types of valve, it can be divided into gate valve concrete pump and S-shaped valve concrete pump. Pumping concrete construction has many advantages, such as saving manpower and resources, improving the overall efficiency of construction, ensuring the quality of the construction and clean, which has a broad market prospect.
On the on hand, the height of building is increasing, pumping height is increasing, the pump pressure is increasing so that the requirement of tightness is increasing. On the other hand, the high strength, viscosity and low pumping property is also testing the key parts of the consumable wear resistance. Wear plate is one of the most critical wear parts, which is also known as glass plate because of the glass-like shape. Production of materials currently used are high-chromium alloy cast iron, high manganese steel, alloy tool steel, carbide, alloys and ceramics. Some wear-resistant alloy easily cracked loss and other failure modes, which will affect the pumping efficiency to a large extent.
Tungsten Carbide Supplier: Chinatungsten Online tungsten-carbide.com.cn | Tel.: 86 592 5129696; Fax: 86 592 5129797;Email:sales@chinatungsten.com |
Tungsten News&Tungsten Prices, 3G Version: http://3g.chinatungsten.com | Molybdenum News & Molybdenum Price: http://news.molybdenum.com.cn |
Tungsten Electrode as TIG Cathode Requirements
- Details
- Category: Tungsten Information
- Published on Tuesday, 22 March 2016 15:18
- Written by yiping
- Hits: 227
Tungsten electrode has high melting point, corrosion resistance, good thermal conductivity and electrical conductivity, so it is widely used in the field of welding. With the development of welding technology, tungsten electrode welding performance has gradually improved. Tungsten electrodes doped with the rare earth element to produce rare earth doped tungsten electrodes, so that the welding performance to be further developed. And common rare earth tungsten electrodes are including: cerium tungsten electrode, lanthanum tungsten electrode, zirconium tungsten electrode, and thorium tungsten electrode and so on.
Tungsten electrodes used in TIG should have following basic requirements:
1. High temperature resistance, electrodes should have good high temperature anti burning performance;
2. Electrode should have high electron emission capability;
3. Electrode should easy to arcing and can maintain stable arcing.
Pure tungsten electrode: its electron emission performance and anti-burning performance is poor, and service life is short, therefore less use in TIG welding. Pure tungsten electrode is good for broken in oxide film, so it is mainly used for AC welding of aluminum, magnesium and their alloys.
Thorium tungsten electrode: it has good electron emission properties, and the desired arc voltage is low, easy arcing and stable, with a good overall performance. However, it is radioactive, so people gradually turning to other type rare earth tungsten electrodes.
Cerium tungsten electrodes: Cerium tungsten electrodes have good thermal electron emission capability, stable arcing, heat concentration, long service life, and no radiation. At low current welding environment is the best alternative to thoriated tungsten electrode. Cerium tungsten electrodes commonly used in low current environment, mainly used for fine widget welding.
Lanthanum tungsten electrode: Lanthanum tungsten electrode has good mechanical cut property, creep resistance and high temperature performance, is the most popular electrode material. It is suitable for alternating current, and has excellent performance.
Tungsten Metals Supplier: Chinatungsten Online www.tungsten.com.cn | Tel.: 86 592 5129696; Fax: 86 592 5129797;Email:sales@chinatungsten.com |
Tungsten News & Prices, 3G Version: http://3g.chinatungsten.com | Molybdenum News & Molybdenum Price: http://news.molybdenum.com.cn |
Tungsten Trioxide Prepares Plate SCR Denitration Catalyst
- Details
- Category: Tungsten Information
- Published on Tuesday, 22 March 2016 13:51
- Written by chunyan
- Hits: 247
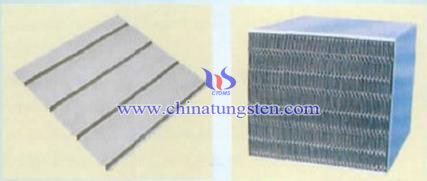
Tungsten Oxide Supplier: Chinatungsten Online www.tungsten-oxide.com | Tel.: 86 592 5129696; Fax: 86 592 5129797;Email:sales@chinatungsten.com |
Tungsten News & Prices, 3G Version: http://3g.chinatungsten.com | Molybdenum News & Molybdenum Price: http://news.molybdenum.com.cn |
Tungsten Electrode Welding Performance
- Details
- Category: Tungsten Information
- Published on Tuesday, 22 March 2016 15:16
- Written by yiping
- Hits: 234
Tungsten electrode is widely used in TIG welding, plasma welding and other welding areas. The welding performance will directly affect their work performance and applications range. With the development of science and technology, not only has more stringent requirements on the electrode property, and environmentally friendly electrode material is an important evaluation criteria.
Compare arcing performance, high temperature burning performance and static characteristic curve of different electrodes to understand the performance of different welding electrodes.
Experimental electrodes are cerium tungsten electrodes (Ce-W electrode), zirconium tungsten electrode (Zr-W electrode), tungsten electrodes doped with three rare earth oxides (La-Ce-Y) and E3 electrode (15% La-0.8% Y-0.8 % Zr).
Arcing performance testing: After arcing performance testing found when I = 30A, tungsten electrodes doped with three rare earth oxides have all arcing. It has the minimum arc current, indicating having low work function, high electron emission capability. Ce-W electrode and Zr-W electrode arcing current is 35A and 40A, having medium work function and electron emission capability. But the E3 electrodes at I = 40A has not been successful arcing, and the data distribution is more dispersed, indicating unstable electron emission capability and high work function.
Burning loss experiment: four kinds of tungsten electrode after 20min arcing occur in varying degrees of oxidation. Ce-W electrode appeared slight rim ring, and E3 electrode tip burned significantly. After 30min minute burning treatment, Ce-W electrode and a Zr-W electrode has varying degrees rim. Pluralistic tungsten electrode has stable morphology. But the original shape of the E3 electrode has been completely destroyed.
After comparison can be found, tungsten electrodes doped with three rare earth oxides has better arcing performance, anti-burning performance and high temperature stability performance than E3 electrode, Zr-W electrode and Ce-W electrode, having better overall performance. The Ce-W and Zr-W has medium welding performance, and E3 electrode welding performance is the worst.
Tungsten Metals Supplier: Chinatungsten Online www.tungsten.com.cn | Tel.: 86 592 5129696; Fax: 86 592 5129797;Email:sales@chinatungsten.com |
Tungsten News & Prices, 3G Version: http://3g.chinatungsten.com | Molybdenum News & Molybdenum Price: http://news.molybdenum.com.cn |
SCR Denitration Catalyst Active Ingredient—Tungsten Trioxide
- Details
- Category: Tungsten Information
- Published on Tuesday, 22 March 2016 13:45
- Written by chunyan
- Hits: 239
Tungsten Oxide Supplier: Chinatungsten Online www.tungsten-oxide.com | Tel.: 86 592 5129696; Fax: 86 592 5129797;Email:sales@chinatungsten.com |
Tungsten News & Prices, 3G Version: http://3g.chinatungsten.com | Molybdenum News & Molybdenum Price: http://news.molybdenum.com.cn |