Cordierite Tungsten Trioxide Denitration Catalyst
- Details
- Category: Tungsten Information
- Published on Wednesday, 30 March 2016 14:51
- Written by chunyan
- Hits: 266
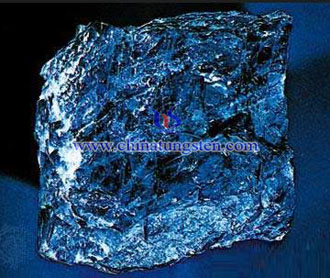
Tungsten Oxide Supplier: Chinatungsten Online www.tungsten-oxide.com | Tel.: 86 592 5129696; Fax: 86 592 5129797;Email:sales@chinatungsten.com |
Tungsten News & Prices, 3G Version: http://3g.chinatungsten.com | Molybdenum News & Molybdenum Price: http://news.molybdenum.com.cn |
Tungsten Trioxide SCR Flue Gas Denitration Catalyst Affecting Factors
- Details
- Category: Tungsten Information
- Published on Wednesday, 30 March 2016 14:48
- Written by chunyan
- Hits: 296
Tungsten Oxide Supplier: Chinatungsten Online www.tungsten-oxide.com | Tel.: 86 592 5129696; Fax: 86 592 5129797;Email:sales@chinatungsten.com |
Tungsten News & Prices, 3G Version: http://3g.chinatungsten.com | Molybdenum News & Molybdenum Price: http://news.molybdenum.com.cn |
Mesoporous Foam Structure WO3 SCR Denitration Catalyst
- Details
- Category: Tungsten Information
- Published on Tuesday, 29 March 2016 18:27
- Written by chunyan
- Hits: 249
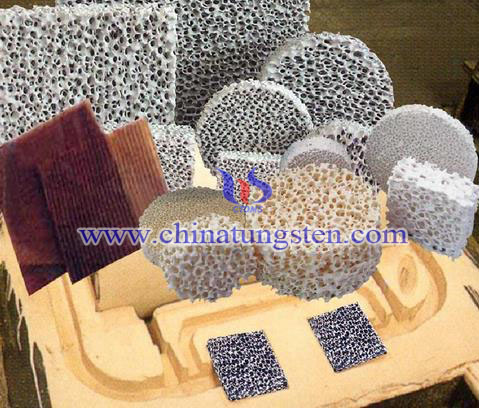
Tungsten Oxide Supplier: Chinatungsten Online www.tungsten-oxide.com | Tel.: 86 592 5129696; Fax: 86 592 5129797;Email:sales@chinatungsten.com |
Tungsten News & Prices, 3G Version: http://3g.chinatungsten.com | Molybdenum News & Molybdenum Price: http://news.molybdenum.com.cn |
Surface Sedimentary Honeycomb WO3 Flue Gas Denitration Catalyst
- Details
- Category: Tungsten Information
- Published on Tuesday, 29 March 2016 18:29
- Written by chunyan
- Hits: 268
Tungsten Oxide Supplier: Chinatungsten Online www.tungsten-oxide.com | Tel.: 86 592 5129696; Fax: 86 592 5129797;Email:sales@chinatungsten.com |
Tungsten News & Prices, 3G Version: http://3g.chinatungsten.com | Molybdenum News & Molybdenum Price: http://news.molybdenum.com.cn |
W-Cu Thermal, Electrical Conductivity Comparison of Different Process (2/2)
- Details
- Category: Tungsten Information
- Published on Tuesday, 29 March 2016 16:59
- Written by xiaobin
- Hits: 340
While for tungsten copper (W-Cu) two phases heat sink material, it has lower coefficient of thermal expansion, which thermal expansion behavior is much more complex than a single-phase material. The experiment shows that t lower temperatures, tungsten-copper composite material showed a negative thermal expansion, but only when the temperature exceeds a certain value showed positive expansion. Tungsten copper sample coefficient of thermal expansion of injection molding and compression molding process under more stable than copper infiltration sample, the magnitude of change is smaller.
This is due to the phase change, as well as the internal organization of the reasons magnetic stretch, thermal expansion of the material will show some special law. By increasing the degree of constraint W phase at elevated temperatures in the expansion phase of Cu, thereby reducing the thermal expansion coefficient of tungsten copper composite material. In addition, since the difference of the coefficient of thermal expansion of the materials, tungsten copper composite material will produce complex stress inside, whose distribution will restrain the thermal expansion behavior.
As for the electrical conductivity, it was detected by eddy current method. When an alternating current is cut coil (also called probes) near the surface of a conductive material, since the coil alternating magnetic field, it has an effect on the material surface and near surface induced swirling current, which called the vortex. Materials and eddy currents generate their own magnetic field coil reacts, which is related to the size of the surface conductivity near the surface. Non-ferromagnetic conductive material can be directly detected by eddy current sensor. After testing found that the sample injection molded tungsten copper has the highest conductivity, reaches 37.43%IACS, which is higher than molding sample (29.85%IACS) and infiltrated sample (33.18%IACS).
Tungsten Copper Supplier: Chinatungsten Online tungsten-copper.com | Tel.: 86 592 5129696; Fax: 86 592 5129797;Email:sales@chinatungsten.com |
Tungsten News & Prices, 3G Version: http://3g.chinatungsten.com | Molybdenum News & Molybdenum Price: http://news.molybdenum.com.cn |