MnOx/WO3/TiO2 Denitration Catalyst
- Details
- Category: Tungsten Information
- Published on Wednesday, 06 April 2016 16:16
- Written by chunyan
- Hits: 291
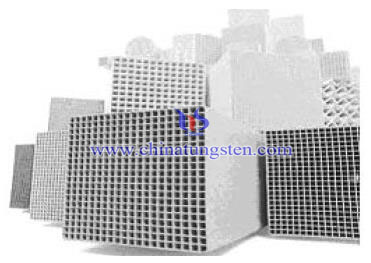
Tungsten Oxide Supplier: Chinatungsten Online www.tungsten-oxide.com | Tel.: 86 592 5129696; Fax: 86 592 5129797;Email:sales@chinatungsten.com |
Tungsten News & Prices, 3G Version: http://3g.chinatungsten.com | Molybdenum News & Molybdenum Price: http://news.molybdenum.com.cn |
WO3 SCR Denitration Catalyst Facing Technical Difficulty--Low Temperature Denitration
- Details
- Category: Tungsten Information
- Published on Wednesday, 06 April 2016 16:12
- Written by chunyan
- Hits: 251
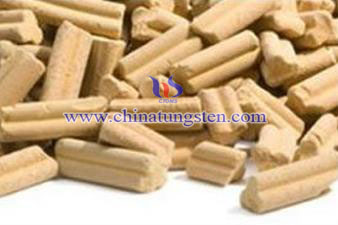
Tungsten Oxide Supplier: Chinatungsten Online www.tungsten-oxide.com | Tel.: 86 592 5129696; Fax: 86 592 5129797;Email:sales@chinatungsten.com |
Tungsten News & Prices, 3G Version: http://3g.chinatungsten.com | Molybdenum News & Molybdenum Price: http://news.molybdenum.com.cn |
Tungsten Copper Sintering Technologies Comparison (2/2)
- Details
- Category: Tungsten Information
- Published on Wednesday, 06 April 2016 16:05
- Written by xiaobin
- Hits: 299
In order to improve mixed-pressing, relevant scholars uses activated agent (Ni, Pd and other activated elements) to increase the solubility of W in liquid phase, which is beneficial for the sintering process. However the additives have a bad influence on the electrical and thermal conductivity of tungsten copper products. Pressure sintering is a kind of secondary processing after sintering, especially for the conditions that one-step forming can not meet the requirements. Although hot pressing, repressing and re-sintering and HIP (Hot Isostatic Pressing) can remarkably improve the properties of tungsten copper composite material, they are limited by the costs and the efficiency. In addition, using hammering or cold rolling of tungsten-copper composite material for secondary processing can greatly increase the density and mechanical properties of the material. But when the content of W is higher, the ductility of tungsten copper will decrease and the difficulty of machining will increase.
Spark Plasma Sintering (SPS), which is also known as Plasma Activated Sintering (PAS) or Field Assisted Sintering Technology (FAST). According to different powder media, SPS can be divided into conductive and non-conductive, there is a big difference in mechanism between them. Generally, conductive SPS will produce a large amount of Joule heat generated by DC pulse current graphite mold; and the current through the powder will induce electric discharge between powder particles and arouse plasma. With the increasing density of plasma, High-speed reverse movement of the particle surface of the particles have a greater impact, so that the gas adsorption of escape or break an oxide film, so that the surface to be purified and activated, will be conducive to sintering. However, instantaneous high temperature generated by the discharge causes evaporation and melting of the grain surface, the grain at the point of contact to form sintered neck.
Tungsten Copper Supplier: Chinatungsten Online tungsten-copper.com | Tel.: 86 592 5129696; Fax: 86 592 5129797;Email:sales@chinatungsten.com |
Tungsten News & Prices, 3G Version: http://3g.chinatungsten.com | Molybdenum News & Molybdenum Price: http://news.molybdenum.com.cn |
Recover Vanadium from WO3 SCR Denitration Catalyst
- Details
- Category: Tungsten Information
- Published on Wednesday, 06 April 2016 16:09
- Written by chunyan
- Hits: 274
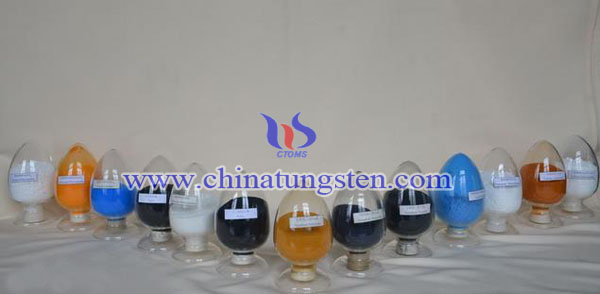
Tungsten Oxide Supplier: Chinatungsten Online www.tungsten-oxide.com | Tel.: 86 592 5129696; Fax: 86 592 5129797;Email:sales@chinatungsten.com |
Tungsten News & Prices, 3G Version: http://3g.chinatungsten.com | Molybdenum News & Molybdenum Price: http://news.molybdenum.com.cn |
Tungsten Copper Sintering Technologies Comparison (1/2)
- Details
- Category: Tungsten Information
- Published on Wednesday, 06 April 2016 16:03
- Written by xiaobin
- Hits: 250
There are many kinds of tungsten copper sintering technologies, such as conventional infiltration, mixed-pressing, pressure sintering and new SPS (Spark Plasma Sintering), etc, which have their own advantages and disadvantages. Next, we analyze these different sintering technologies by the principle and the applications. First of all, infiltration, which is called melt immersion, is the most widely used in tungsten copper products currently. It is obtained by adding a small amount of tungsten powder or copper powder compacts made of tungsten powder and tungsten and copper infiltrated compacts stacked together, and thereafter sintered at a temperature above the melting point of copper and under reducing atmosphere or vacuum.
In the process of sintering, copper in a molten state to rely on capillary action infiltrated tungsten skeleton, two sintering and infiltration step can also be performed separately. Infiltration has many advantages, such as high density, excellent sintering properties and electrical and thermal conductivity, good arc ablation resistance. But liquid copper barely rely on capillary forces infiltrated tungsten skeleton, this will lead to coarse and uneven distribution of copper particles sintered tungsten particles at high temperatures easily grew up together. In addition, after infiltration machined to remove excess copper and will increase costs and reduce the yield.
Mixed - pressing sintering process is one of the most conventional powder metallurgy, which basic process is preparation →ball milling → compacting →sintering. Sintering can be also divided into two parts, one is solid phase sintering (temperature lower than the melting point of Cu), the other is liquid phase sintering (temperature higher than the melting point of Cu). Since the solid solubility in the liquid phase W Cu is small, the material can not be conveyed by dissolution and precipitation particles rounded manner, and tungsten and copper infiltration is poor, it is difficult to achieve densification.
Tungsten Copper Supplier: Chinatungsten Online tungsten-copper.com | Tel.: 86 592 5129696; Fax: 86 592 5129797;Email:sales@chinatungsten.com |
Tungsten News & Prices, 3G Version: http://3g.chinatungsten.com | Molybdenum News & Molybdenum Price: http://news.molybdenum.com.cn |