Cobalt Interlayed TiN-coated Tungsten Carbide Cutting Tool’s Performance Ⅱ
- Details
- Category: Tungsten Information
- Published on Thursday, 10 September 2015 09:25
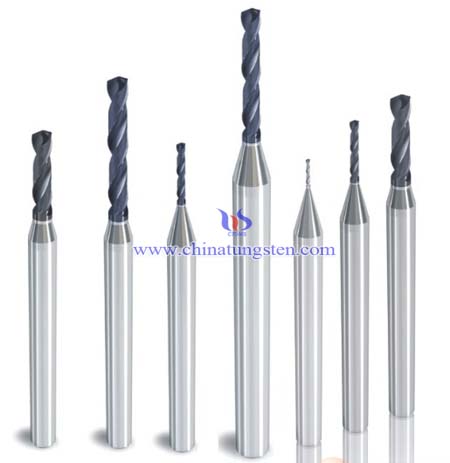
Tungsten Carbide Manufacturer & Supplier: Chinatungsten Online - http://www.tungsten-carbide.com.cn
Tel.: 86 592 5129696; Fax: 86 592 5129797
Email:sales@chinatungsten.com
Tungsten & Molybdenum Information Bank: http://i.chinatungsten.com
Tungsten News & Tungsten Prices, 3G Version: http://3g.chinatungsten.com
Molybdenum News & Molybdenum Price: http://news.molybdenum.com.cn
Atomic Layer Deposition of Tungsten Using Sequential Surface Chemistry with A Sacrificial Stripping Reaction
- Details
- Category: Tungsten Information
- Published on Wednesday, 09 September 2015 17:55
Tungsten (W) films were grown with atomic layer control using a novel sequence of self-limiting surface reactions. The tungsten film growth was achieved by dividing the binary reaction WF6+Si2H6→W+2SiHF3+2H2 into two separate half-reactions. Alternating exposures to WF6 and Si2H6 in an ABAB… sequence produced tungsten deposition at temperatures between 425 and 600 K. The Si2H6 reactant served only a sacrificial role to strip fluorine from tungsten without incorporating into the film. FTIR spectroscopic investigations demonstrated that the WF6 and Si2H6 half-reactions were complete and self-limiting at T>400 K. In situ spectroscopic ellipsometry measurements determined a tungsten growth rate of 2.5 Å/AB cycle with WF6 and Si2H6 reactant exposures sufficient for complete half-reactions. The surface topography of the deposited tungsten films was flat indicating smooth film growth. The tungsten films were either amorphous or composed of very small crystalline grains and contained no measurable silicon or fluorine. These results represent the first demonstration of atomic layer deposition of smooth single-element metal films using sequential surface chemistry.
Tungsten Powder Manufacturer & Supplier: Chinatungsten Online - www.tungsten-powder.com
Tel.: 86 592 5129696; Fax: 86 592 5129797
Email: sales@chinatungsten.com
Tungsten & Molybdenum Information Bank: http://i.chinatungsten.com
Tungsten News & Tungsten Prices, 3G Version: http://3g.chinatungsten.com
Molybdenum News & Molybdenum Price: http://news.molybdenum.com.cn
Tungsten Carbide Ball Process
- Details
- Category: Tungsten Information
- Published on Wednesday, 09 September 2015 17:50
Tungsten carbide ball has high hardness and usually above 87 HRA, which is double than normal steel ball so that the process is also difficult. The main problem is that the low surface energy of tungsten carbide ball, grinding media and abrasive adhesion is poor. Therefore, it has a huge influence on the efficiency and the accuracy or the surface roughness of tungsten carbide ball. Secondly, the rotation of tungsten carbide ball in the grinding plate is poor, which affects the machining accuracy carbide ball to some extent, especially spherical error.
At present, the most of equipments are based on steel ball process, which needs us to improve the equipment and grinding structure, choose proper grinding compounds and grinding plate for optimizing the parameters. In addition, high precision tungsten carbide ball milling mode includes that four-axis ball milling, V-groove grinding, conical grinding, spin rotation control, magnetic grinding and two-way rotation grinding.
Tungsten Carbide Manufacturer & Supplier: Chinatungsten Online - http://www.tungsten-carbide.com.cn
Tel.: 86 592 5129696; Fax: 86 592 5129797
Email: sales@chinatungsten.com
Tungsten & Molybdenum Information Bank: http://i.chinatungsten.com
Tungsten News & Tungsten Prices, 3G Version: http://3g.chinatungsten.com
Molybdenum News & Molybdenum Price: http://news.molybdenum.com.cn
Tungsten Carbide Ball Grades
- Details
- Category: Tungsten Information
- Published on Wednesday, 09 September 2015 17:48
Some main tungsten carbide ball grades table
Grades |
WC contents(%) |
Co contents(%) |
Hardness(HRA) |
Density(g/cm3) |
TRS (N/cm2) |
YG6 |
94 |
6 |
89.5 |
14.5-14.9 |
1380 |
YG6X |
94 |
6 |
91 |
14.6-15.0 |
1500 |
YG8 |
92 |
8 |
89.5 |
14.5-14.9 |
1600 |
YG10 |
90 |
10 |
89.5 |
14.3-14.7 |
2200 |
YG15 |
85 |
15 |
87 |
13.9-14.2 |
2100 |
The table shows that the hardness will decrease by the increasing Co content, while its toughness and bending strength is enhancing. In addition, fine grain has higher density and hardness than coarse grain and other properties are also improving after sintering.
Tungsten Carbide Manufacturer & Supplier: Chinatungsten Online - http://www.tungsten-carbide.com.cn
Tel.: 86 592 5129696; Fax: 86 592 5129797
Email: sales@chinatungsten.com
Tungsten & Molybdenum Information Bank: http://i.chinatungsten.com
Tungsten News & Tungsten Prices, 3G Version: http://3g.chinatungsten.com
Molybdenum News & Molybdenum Price: http://news.molybdenum.com.c
n
Determination of Arsenic,Copper,Manganese,Molybdenum,Phosphorus and Silicon in Ferrotungsten
- Details
- Category: Tungsten Information
- Published on Wednesday, 09 September 2015 17:47
Determination of arsenic,copper,manganese,molybdenum,phosphorus and silicon in ferrotungsten by inductively coupled plasma atomic emission spectrometry.
A simultaneous determination method of arsenic,copper,manganese,molybdenum,phosphorus and silicon in ferrotungsten by inductively coupled plasma-atomic emission spectrometry was established.The samples were dissolved with oxalic acid and hydrogen peroxide.The matrix elements(W and Fe) and other coexisting elements had no interference with the testing elements.Under the optimal conditions,the detection limits of arsenic,copper,manganese,molybdenum,phosphorus and silicon were 0.009,0.006,0.000 1,0.000 3,0.005 and 0.002 μg/mL,respectively.The standard addition recoveries were 95 %-108 %,and the relative standard deviation(RSD,n=3) was 0.1 %-3.3 %.The proposed method has been applied to the determination of certified reference material,the results were in good agreement with the certified values.
Tungsten Powder Manufacturer & Supplier: Chinatungsten Online - www.tungsten-powder.com
Tel.: 86 592 5129696; Fax: 86 592 5129797
Email: sales@chinatungsten.com
Tungsten & Molybdenum Information Bank: http://i.chinatungsten.com
Tungsten News & Tungsten Prices, 3G Version: http://3g.chinatungsten.com
Molybdenum News & Molybdenum Price: http://news.molybdenum.com.cn
Cobalt Interlayed TiN-coated Tungsten Carbide Cutting Tool’s PerformanceⅠ
- Details
- Category: Tungsten Information
- Published on Wednesday, 09 September 2015 10:55
Abstract
To improve the adhesion strength between TiN coatings and WC-Co substrate, interlayer of Co was pre-deposited onto WC-Co substrates prior to the TiN coating process. The thickness and post-annealing effects of Co interlayer on the adhesion property were investigated through scratchtests in this work. The highest critical load of approximately 84 N was obtained for the TiN coating with Co-interlayer sputter-time of 10 min and the critical load increased up to 97 N after post-annealing at 600 °C for 2 h. It was found that the adhesion of TiN coatings was strongly influenced by the thickness of Co interlayer. TiN without Co interlayer and TiN with three kinds of Co interlayer coatings were applied to end-mill tools made of WC-Co material with a hybrid coating technique.
Cutting tests for die steel AISI D2 cold-worked die steel (60 HRC) and their reliability tests were studied. The tool life of TiN-coated tool with Co interlayer having the critical thickness of 0.027 μm was improved for over 36% as compared to only TiN-coated tools. The experimentation was repeatedly performed in order to verify the goodness of fit for tool wear distribution. The flank wear of TiN-coated tool with Co interlayer at given time condition is suitable for normal distribution and log-normal distribution by chi-squared test.
Tungsten Carbide Manufacturer & Supplier: Chinatungsten Online - http://www.tungsten-carbide.com.cn
Tel.: 86 592 5129696; Fax: 86 592 5129797
Email:sales@chinatungsten.com
Tungsten & Molybdenum Information Bank: http://i.chinatungsten.com
Tungsten News & Tungsten Prices, 3G Version: http://3g.chinatungsten.com
Molybdenum News & Molybdenum Price: http://news.molybdenum.com.cn
Cemented Carbide Blades Wear Characteristics in Drilling Limestone Ⅶ
- Details
- Category: Tungsten Information
- Published on Wednesday, 09 September 2015 10:52
4. Conclusions
This paper investigates wear characteristics of the cemented carbide blades in the process of drilling limestone with water jet. The wear mechanism of the blades when water jet is employed in rock drilling process is also studied. The conclusions could be summarized as follows:
1. The pressure of water jet plays an important role in the wear rates of cemented carbide drill bits in rock drilling with water jet. The wear rates decrease with the increasing of the jet pressure. But the decline speed of wear rates is not even. It declines more and more slowly when the jet pressure is over 10 MPa
2. Reasonable nozzle structure can improve the wear resistance of the cemented carbide blades. Moreover, increasing the diameter of the jet nozzle could decrease the wear rates of blades.
3. Surface analysis demonstrated that cemented carbide blades in limestone drilling with water jet shows circular action of brittle fracture, grain pullout and polishing, which induces material removal process.
Tungsten Carbide Manufacturer & Supplier: Chinatungsten Online - http://www.tungsten-carbide.com.cn
Tel.: 86 592 5129696; Fax: 86 592 5129797
Email:sales@chinatungsten.com
Tungsten & Molybdenum Information Bank: http://i.chinatungsten.com
Tungsten News & Tungsten Prices, 3G Version: http://3g.chinatungsten.com
Molybdenum News & Molybdenum Price: http://news.molybdenum.com.cn
Tungsten Carbide Ball Description II
- Details
- Category: Tungsten Information
- Published on Tuesday, 08 September 2015 17:04
At present, the common types of tungsten carbide ball are YG (W and Co), YN (W and Ni), YT (W, Co and Ti) and YW (W, Ti, Ta and Co) and so on. In terms of tungsten carbide grades, it can be specifically divided into YG6, YG6X (fine particles), YG8, YG13, YG20, YN6, YN9, YN12, YT5, YT15, etc. The common specs haveΦ2、Φ4、Φ6、Φ10、Φ50 and so on.
Tungsten carbide nozzle has high hardness and excellent wear resistance so that the prospect and the field of application is broad, such as fine bearing, instrument control, stretching, coating, mechanical parts, water pump, seal components, impact hole, oil field, braking pump, laboratory, hardness measuring (Rockwell hardness), balancing weight and some other high-end field. In addition, according to different requirements and parameters, tungsten carbide ball products include that tungsten carbide ball, tungsten ball, heavy alloy ball and so on. The smallest diameter of tungsten carbide ball is about 0.3.
Tungsten Carbide Manufacturer & Supplier: Chinatungsten Online - http://www.tungsten-carbide.com.cn
Tel.: 86 592 5129696; Fax: 86 592 5129797
Email: sales@chinatungsten.com
Tungsten & Molybdenum Information Bank: http://i.chinatungsten.com
Tungsten News & Tungsten Prices, 3G Version: http://3g.chinatungsten.com
Molybdenum News & Molybdenum Price: http://news.molybdenum.com.cn
Tungsten Carbide Ball Description
- Details
- Category: Tungsten Information
- Published on Tuesday, 08 September 2015 17:01
Tungsten carbide ball, also known as tungsten ball, which is made of cemented carbide. Due to its high hardness (usually ≥ 90.5 HRA), high density (reaches 14.9 g/cm3), excellent bending strength, good wear resistance and anti-corrosion, it can widely take place of steel ball in applications and remarkably improving the properties. Tungsten carbide ball is a kind of powder metallurgy products, which uses refractory metal carbide with high hardness (e.g., WC, TiC) micron powder, and cobalt (Co), molybdenum (Mo) or nickel (Ni) or others as a binder for vacuum sintering other the methods.
The special manufacturing process also increases the cost. However, it not only has excellent physical properties, but also has stable chemical properties, which is non-reactive with other types of acid or alloys at high temperatures.
Tungsten Carbide Manufacturer & Supplier: Chinatungsten Online - http://www.tungsten-carbide.com.cn
Tel.: 86 592 5129696; Fax: 86 592 5129797
Email: sales@chinatungsten.com
Tungsten & Molybdenum Information Bank: http://i.chinatungsten.com
Tungsten News & Tungsten Prices, 3G Version: http://3g.chinatungsten.com
Molybdenum News & Molybdenum Price: http://news.molybdenum.com.cn
Cemented carbide blades Wear Characteristics in Drilling limestoneⅥ
- Details
- Category: Tungsten Information
- Published on Tuesday, 08 September 2015 10:57
3.3. Wear mechanism of cemented carbide blade drill rock with water jet
The failure type of the cemented carbide blades in water jet drilling is not the same as that in dry drilling. Fig. 6 shows the SEM micrographs (500×) of damaged surfaces of blades in the experiments. Fig. 6 (a) is the typical brittle fracture morphology in dry drilling. No serious fractures are detected in the drilling experiments with water jet under the same zoom scope and the surfaces mainly show wear morphology.
There are mainly three reasons to explain the different results. Firstly, water jet can effectively decrease the surface temperature and thermal stress. Secondly, the water jet provides impact force to crack the limestone, and it helps to decrease the mechanical force on the blade. Thus, the sum of thermal stress and mechanical stress which can induce serious brittle fractures could be lower than the material strength of the blade in drilling with water. In the third place, the water jet with higher pressure could form a comparatively cooler water layer to lubricate the blade, and could rush away the hard abrasive particles in the rock like a polisher. Therefore, the surface of the blade in water jet drilling is much smoother than that in dry drilling, and the wear rate will decrease while the water jet pressure increases.
Although wide range of brittle fractures is avoided, but there will still be surface damages on the blades in rock drilling with water jet. Fig. 7 shows micrographs of typical wear surfaces of cemented carbide blades in limestone drilling with water jet. It is obvious that point 1, on the edge of the blade, is rougher than point 2. In fact, the two points could reflect the wearing process of cemented carbide blades in limestone drilling with water jet.
The wearing process of cemented carbide blades in limestone drilling with water jet could be divided into two stages. Initially, under water jet-assisted condition, micro cracks appear on the edge of the blade, probably caused by local mechanical abrasion and thermal stress which is induced by the fl ash temperature. The grain size and its distribution on the surface can be seen in Fig. 7 (d). The Co phase is much softer than the WC phase and it is easy to be worn. So when the blade mills the rock, Co phase is worn firstly and with particles washed away by the water jet, the porosities between grains are larger and the surface of the blade becomes more uneven.
Then, this kind of micro surface damage expands from the edge to the center of the blade surface. While the drill bit is rotating in the rock, the edges and corners of grains will be polished as mentioned before, shown in Fig. 7(e). And this polishing process continues from the edge to the center of the blade surface. When the drill bit drills into the rock continuously, the polished surface on the edges will form new micro cracks which then extend to the center of the blade surface because of mechanical abrasion and thermal stress caused by flash temperature.
Therefore, this roughing-polishing process is repeated from the edge to the center of the blade surface constantly, and the blade will became thinner and thinner until it cannot work.
Tungsten Carbide Manufacturer & Supplier: Chinatungsten Online - http://www.tungsten-carbide.com.cn
Tel.: 86 592 5129696; Fax: 86 592 5129797
Email:sales@chinatungsten.com
Tungsten & Molybdenum Information Bank: http://i.chinatungsten.com
Tungsten News & Tungsten Prices, 3G Version: http://3g.chinatungsten.com
Molybdenum News & Molybdenum Price: http://news.molybdenum.com.cn