Nitrogen-Doped Impact on Tungsten Trioxide Structure
- Details
- Category: Tungsten Information
- Published on Monday, 18 January 2016 17:27
- Written by qiongyao
- Hits: 278
Doping is an important method to improve the efficiency of light energy conversion of photocatalytic material. Numerous of studies show that the rare earth and metal ions by doping can significantly enhance the catalytic activity of the photocatalyst, however, it may lead the stability of metal-doped catalysts thermal to decrease and the introduction of photo-generated electron and hole recombination centers to reduce its optical conversion efficiency. Some non-metal-doped semiconductor material may improve their stability, electrical conductivity, and pass through between the conductive and leave with the formation of "middle level" and to improve the material efficiency of absorption of visible light.
Numerous of studies show that, the N-doped can significantly improve the absorption efficiency of TiO2, ZrO2, Ta2O5 and other semiconductor materials belong to visible light, the n-type semiconductor, the same can be improved by N-doped WO3-x of visible light absorption efficiency.
The nitrogen (N) doped tungsten trioxide photocatalyst (WO_ (3-x): N) is prepared by Sol-gel - ammonia oxygen atmosphere firing method. The structural properties of the samples were characterization and analysis by using SEM, XRD, XPS and DRS, comparing the experimental study of nitrogen doping on the tungsten trioxide photolysis aquatic oxygen catalytic activity. The results show that NH_3 / O_2 was mixed atmosphere at 500 ℃ , sintering it 3h , doping N, when N enters tungsten trioxide lattice, it does not change WO_ (3-x) polymorphs and morphology. WO_ (3-x ): N remains monoclinic crystal structure, and are a small amount of an unknown sample new phase that causes thinning size and lattice distortion increases while doping surface W ~ (4+) powder and increase the oxygen vacancy. Certain lattice defects and oxygen vacancies are in favor of catalyst response wavelength red shift. The rate of N average oxygen evolution reaches 66.8μmol / (L • g • h) under UV irradiation 12h, while the rate of photolysis under visible radiation water increase to 24.5% than non-doped sample.
Tungsten Oxide Supplier: Chinatungsten Online www.tungsten-oxide.com | Tel.: 86 592 5129696; Fax: 86 592 5129797;Email:sales@chinatungsten.com |
Tungsten News & Prices, 3G Version: http://3g.chinatungsten.com | Molybdenum News & Molybdenum Price: http://news.molybdenum.com.cn |
Scheelite and Wolframite Mixture Ore and Shizhuyuan Method
- Details
- Category: Tungsten Information
- Published on Monday, 18 January 2016 17:05
- Written by xinyi
- Hits: 268
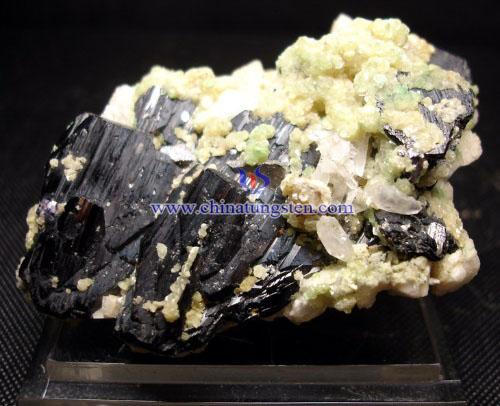
Tungsten Supplier: Chinatungsten Online www.chinatungsten.com | Tel.: 86 592 5129696; Fax: 86 592 5129797;Email:sales@chinatungsten.com |
Tungsten News & Prices, 3G Version: http://3g.chinatungsten.com | Molybdenum News & Molybdenum Price: http://news.molybdenum.com.cn |
Tungsten Copper Electrode and Other Materials Comparison
- Details
- Category: Tungsten Information
- Published on Monday, 18 January 2016 16:44
- Written by xiaobin
- Hits: 237
Tungsten copper powder sintered material having high hardness, high density, high strength, wear resistance, adhesion, excellent electrical and thermal conductivity as well as sweating characteristics, making it ideally suited to withstand high stress resistance welding electrode matching, or as automatic submerged arc welding, carbon dioxide CO2 gas shielded arc welding tip conductive or conductive plate. Tungsten copper flash welding electrode and chromium-copper comparison as follow:
From the table we can see that tungsten copper chromium copper compared to flash welding electrode welding electrode flash at the same working hours, higher welding efficiency, the amount of wear smaller, better weld quality, lower cracking rate life more long, the application is more convenient, and therefore wide range of applications. Vertical automatic welding, soldering conditions when the thickness of 22-28mm, wire directly Φ2.4mm, conductive nozzle aperture when 2.8mm, tungsten, copper and chromium copper conductor conductive nozzle tip wear after welding is very different.
Tungsten copper conductive tip after welding 20m, the aperture remains the prototype, you can still continue to work, in contrast, chromium copper conductive soldering tip less than 2m, its conductivity unilateral eccentric bore wear, maximum diameter enlargement ratio of tungsten copper conductor increases 0.6mm, has been unable to proceed with the welding work. Therefore, resistance welding electrodes and welding conductor tungsten copper powder sintered material having a high hardness, high density, high strength, wear resistance, adhesion, excellent electrical and thermal conductivity and a series of advantages, which has a broad prospect.
Tungsten Copper Supplier: Chinatungsten Online tungsten-copper.com | Tel.: 86 592 5129696; Fax: 86 592 5129797;Email:sales@chinatungsten.com |
Tungsten News & Prices, 3G Version: http://3g.chinatungsten.com | Molybdenum News & Molybdenum Price: http://news.molybdenum.com.cn |
Detinning Process of APT Production- Controlling the Alkali Decomposition Conditions
- Details
- Category: Tungsten Information
- Published on Monday, 18 January 2016 16:59
- Written by xinyi
- Hits: 257
Tungsten Supplier: Chinatungsten Online www.chinatungsten.com | Tel.: 86 592 5129696; Fax: 86 592 5129797;Email:sales@chinatungsten.com |
Tungsten News & Prices, 3G Version: http://3g.chinatungsten.com | Molybdenum News & Molybdenum Price: http://news.molybdenum.com.cn |
New Technology of Tungsten Copper Electrode—Microwave Infiltration
- Details
- Category: Tungsten Information
- Published on Monday, 18 January 2016 16:42
- Written by xiaobin
- Hits: 236
Actually, microwave infiltration is one of new methods, which combines microwave sintering with traditional infiltration. It has many advantages, such as selective heating (the coupling ability of material and microwave, the ability of microwave absorption is related to the properties of itself, such as electrical conductivity, magnetic conductivity and dielectric constant, which will get diverse heating properties when the material is different in a given microwave field. ), volume heating (Each portion of the object in the portion of the material is heated after the heat acquired, so that the part of the material temperature rises.), non-thermal effect (It general refers to compared with traditional sintering under the same thermal dynamic conditions has remarkable superiority in physical, such as the active sintering of powder material and atomic diffusion rate.) , and uniform structure of infiltration processing. Therefore, microwave infiltration has higher speed of increasing temperature, shorter sintering time, higher energy utilization ratio and uniform structure or excellent properties of the products. Microwave infiltration of microwave sintering equipment is produced by DC magnetron microwave waveguide by introducing the heating chamber, the sample is placed in the cavity is heated sintering. The sketch of structure of the equipment as follow:
The major technical parameters of microwave sintering furnace includes work area, the highest working temperature, thermometric, methods, the range of infrared detection, the precision of temperature control, the out power of microwave, vacuum limit of furnace, the leaking of microwave. At present, the use of microwave sintering heating chamber includes a resonant and non-resonant two, while the cavity can be subdivided into single-mode and multi-mode resonant cavity resonator. Under the same electromagnetic power, single-mode resonant cavity having a stronger magnetic field strength is more suitable for low heating medium. The multimode resonator having multiple resonant modes, the electromagnetic field distribution is more uniform, the structure is relatively simple, suitable for a variety of heating load, the more it is difficult to accurately analyze the data.
Tungsten Copper Supplier: Chinatungsten Online tungsten-copper.com | Tel.: 86 592 5129696; Fax: 86 592 5129797;Email:sales@chinatungsten.com |
Tungsten News & Prices, 3G Version: http://3g.chinatungsten.com | Molybdenum News & Molybdenum Price: http://news.molybdenum.com.cn |