Tungsten Electrode and Rare Earth Tungsten Electrode
- Details
- Category: Tungsten Information
- Published on Tuesday, 19 January 2016 17:35
- Written by yiping
- Hits: 284
Tungsten Supplier: Chinatungsten Online www.chinatungsten.com | Tel.: 86 592 5129696; Fax: 86 592 5129797;Email:sales@chinatungsten.com |
Tungsten News & Prices, 3G Version: http://3g.chinatungsten.com | Molybdenum News & Molybdenum Price: http://news.molybdenum.com.cn |
Tungsten Electrode
- Details
- Category: Tungsten Information
- Published on Tuesday, 19 January 2016 17:32
- Written by yiping
- Hits: 242
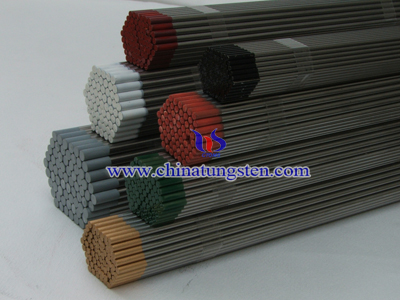
Tungsten Supplier: Chinatungsten Online www.chinatungsten.com | Tel.: 86 592 5129696; Fax: 86 592 5129797;Email:sales@chinatungsten.com |
Tungsten News & Prices, 3G Version: http://3g.chinatungsten.com | Molybdenum News & Molybdenum Price: http://news.molybdenum.com.cn |
Detinning Process of APT Production- Additives in Alkali Decomposition
- Details
- Category: Tungsten Information
- Published on Tuesday, 19 January 2016 17:28
- Written by xinyi
- Hits: 264
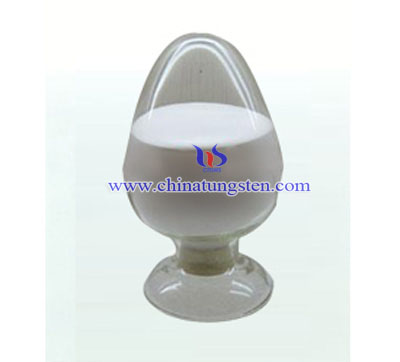
Tungsten Supplier: Chinatungsten Online www.chinatungsten.com | Tel.: 86 592 5129696; Fax: 86 592 5129797;Email:sales@chinatungsten.com |
Tungsten News & Prices, 3G Version: http://3g.chinatungsten.com | Molybdenum News & Molybdenum Price: http://news.molybdenum.com.cn |
Asynchronous flotation of Scheelite and Wolframite Mixture Ore
- Details
- Category: Tungsten Information
- Published on Tuesday, 19 January 2016 17:31
- Written by xinyi
- Hits: 271
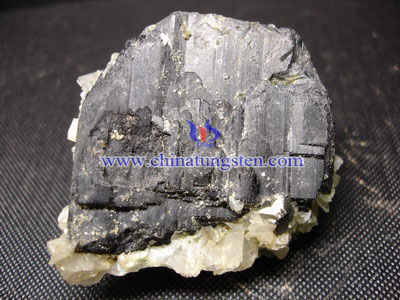
Tungsten Supplier: Chinatungsten Online www.chinatungsten.com | Tel.: 86 592 5129696; Fax: 86 592 5129797;Email:sales@chinatungsten.com |
Tungsten News & Prices, 3G Version: http://3g.chinatungsten.com | Molybdenum News & Molybdenum Price: http://news.molybdenum.com.cn |
Recycling Tungsten Trioxide in Waste SCR Denitration Catalyst
- Details
- Category: Tungsten Information
- Published on Tuesday, 19 January 2016 17:23
- Written by qiongyao
- Hits: 240
The development of SCR denitration catalyst is based on the technology of selective catalytic reduction (SCR), the SCR system is an integral and important part of SCR systems. In performance, the denitration catalyst is the key to success of the project, its components, structure, life and its associated parameters directly affect the health of denitration efficiency and SCR systems. SCR denitration catalyst can be classified according to different raw materials, structure, extent, use and other standards. There are mainly three types in SCR denitration catalyst: 1) precious metal type; 2), metal oxide type; 3), zeolite type of ion exchange. The type of metal oxide is currently the more popular, it is also more widely used, and such catalysts is based on the carrier of titanium dioxide, vanadium pentoxide, tungsten trioxide the active ingredient.
Steps
(1)Crushing SCR denitration catalyst to dry powder, and roasting it in high-temperature;
(2) Adding a solution of soluble tungsten trioxide component and heating it in the above step (1) that the resulting is dry powder;
(3) Collecting the supernatant after fully dissolving, and make the liquid-solid layers clean;
(4) Adding the solid in the step (3) and the composition of tungsten trioxide to the reaction vessel together, and repeating the step (2);
(5) Repeating the step(3) and (4) at least once;
(6) Collecting several components and dissolving tungsten trioxide that was evaporated to dryness and sufficiently, drying to obtain a solid;
(7) Sintering the resulting solid in the step (6) at high temperature, and we can recycle the component of tungsten trioxide in the waste SCR denitration catalyst.
Tungsten Oxide Supplier: Chinatungsten Online www.tungsten-oxide.com | Tel.: 86 592 5129696; Fax: 86 592 5129797;Email:sales@chinatungsten.com |
Tungsten News & Prices, 3G Version: http://3g.chinatungsten.com | Molybdenum News & Molybdenum Price: http://news.molybdenum.com.cn |