Suggestions on China’s Tungsten Ore Beneficiation Development
- Details
- Category: Tungsten Information
- Published on Tuesday, 26 January 2016 16:22
- Written by xinyi
- Hits: 258
Tungsten Supplier: Chinatungsten Online www.chinatungsten.com | Tel.: 86 592 5129696; Fax: 86 592 5129797;Email:sales@chinatungsten.com |
Tungsten News & Prices, 3G Version: http://3g.chinatungsten.com | Molybdenum News & Molybdenum Price: http://news.molybdenum.com.cn |
Comparison Between Domestic and Foreign Beneficiation Process and Equipments
- Details
- Category: Tungsten Information
- Published on Tuesday, 26 January 2016 16:15
- Written by xinyi
- Hits: 242
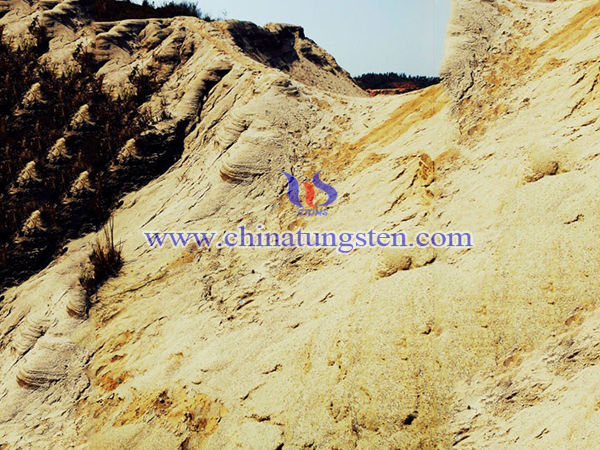
Tungsten Supplier: Chinatungsten Online www.chinatungsten.com | Tel.: 86 592 5129696; Fax: 86 592 5129797;Email:sales@chinatungsten.com |
Tungsten News & Prices, 3G Version: http://3g.chinatungsten.com | Molybdenum News & Molybdenum Price: http://news.molybdenum.com.cn |
Tungsten Trioxide and Tungsten Dioxide
- Details
- Category: Tungsten Information
- Published on Monday, 25 January 2016 18:05
- Written by qiongyao
- Hits: 292
There are four stable tungsten oxides: yellow tungsten oxide (WO3), blue tungsten oxide (WO2.90), violet tungsten oxide (WO2.72) and tungsten dioxide (WO2).
Tungsten trioxide is lemon yellow crystalline powder, its density is 7.2 ~ 7.4g / cm3, its melting point is about 1470 ℃, boiling point is 1700 ~ 2000 ℃. Tungsten trioxide becomes 202.8 cal / mol at 800 ℃ sublimation. Tungsten anhydride can slightly soluble in water (0.2g / L), insoluble in all inorganic acids except hydrofluoric acid. Acid soluble of caustic solution (NaOH or KOH) and ammonia can form tungstate [NaWO4, K2WO4 and (NH4) 2WO4]. In ammonia solution of tungsten trioxide dissolves slowly and dissolves more slowly at a high temperature. At room temperature, even a small amount of organic matter will be able to restore it, and change its color. But in the air, heating time and restore the original color at 700 ~ 900 ℃, the tungsten trioxide can easily restore in hydrogen.
Tungsten dioxide is brown powder, its density is 10.9 ~ 11.1g / cm3, boiling point is about 1700 ℃, generate heat is 134 kcal / mol. The reduction of tungsten trioxide becomes tungsten dioxide with the hydrogen at 575 ~ 600 ℃. Tungsten dioxide is rapidly oxidized tungsten trioxide in the air and heated to blue in the oxide at 500 ℃., tungsten carbon dioxide can be reduced to metallic tungsten at 1020 ℃.
Tungsten Oxide Supplier: Chinatungsten Online www.tungsten-oxide.com | Tel.: 86 592 5129696; Fax: 86 592 5129797;Email:sales@chinatungsten.com |
Tungsten News & Prices, 3G Version: http://3g.chinatungsten.com | Molybdenum News & Molybdenum Price: http://news.molybdenum.com.cn |
Comprehensive Purifying Wastewater from Ammonium Paratungstate Production Process
- Details
- Category: Tungsten Information
- Published on Monday, 25 January 2016 18:28
- Written by chunyan
- Hits: 270
In China, ammonium paratungstate (APT) is mainly produced by method of ion exchange. The wastewater generated from the process of tungsten smelting is composed of two parts: ion exchange and dilute ammonia which can not be recovered. The ammonium and nitrogen contented in dilute ammonia nitrogen is about 3000~4000mg/L; arsenic in solution after exchange is about 2~3.5mg/L, and phosphorus is 10~20mg/L, fluorine is 100~200mg/L, and it’s seriously exceeded the national standard.
At present, NaOH-adding-stripping method is mainly used in dilute ammonia for removing ammonia and nitrogen, but the alkali consumption volume is high, ammonia nitrogen removal is not complete, and low concentration ammonia directly emissions cause secondary pollution; and ion exchange liquid mainly use ferrous sulfate silica fume addition polymerization aluminum iron precipitation of arsenic removal, the method is poor effect for high arsenic content in tungsten liquid and cannot simultaneously remove phosphorus and fluorine.
Test materials: dilute ammonia recovered in ammonium paratungstate crystallization and ammonia liquid after remove ammonia and nitrogen, the tungsten ion exchange liquid, industrial (the content of calcium is 30%) and hydrochloric acid.
Specific steps:
1. Tungsten smelting wastewater ammonia and nitrogen removal, under the condition of normal temperature, the mass ratio of bleaching powder and ammonia nitrogen is 6.9~34.7, pH = 4~12, time for 10min, stirring speed at 600r/min;
2. Deeply remove arsenic, phosphorus and fluorine, under the condition of normal temperature, volume ratio of liquid after removed ammonia.
APT Supplier: Chinatungsten Online ammonium-paratungstate.com | Tel.: 86 592 5129696; Fax: 86 592 5129797;Email:sales@chinatungsten.com |
Tungsten News&Tungsten Prices, 3G Version: http://3g.chinatungsten.com | Molybdenum News & Molybdenum Price: http://news.molybdenum.com.cn |
CVD Diamond Coated Carbide Pretreatment—Mechanical Process (2/2)
- Details
- Category: Tungsten Information
- Published on Monday, 25 January 2016 17:34
- Written by xiaobin
- Hits: 244
Except the mechanical grinding, ultrasonic cleaning is another common mechanical process. Ultrasonic cleaning mainly uses the cavitation of ultrasonic in the liquid (Ultrasonic high frequency changes in the way more than twenty thousand times per second, compression force and reducing stress interactive transmission to liquid, at reduced pressure, vacuum nuclei bubble phenomenon liquid; compression force under vacuum nuclei broken bubble compression have a great impact, and thus the substrate surface dirt peel to achieve precision cleaning purposes.), acceleration effect, direct current effect (a phenomenon of ultrasonic flows with the direction of sound propagation in the liquid, which runs straight into the stream to be cleaned so that the substrate surface dirt is stirred to the surface of the cleaning fluid convection, dissolve dirt solution and mixed with fresh liquid, so that the dissolution rate greatly accelerate and facilitate the removal of impurity.) and the direct or indirect effect of liquid and impurity, which cleaned by the ablation, diffusion and emulsification of the impurity layer.
When it used in the ultrasonic cleaning technology is the use of CVD diamond film crystallite or fine powder of nano-sized diamond suspension (commonly, such as ethanol, acetone, etc.) on the substrate surface is processed, so that not only can be more thoroughly cleaned Carbide the substrate surface, but also can be dispersed diamond powder implanted in the substrate, greatly increase the nucleation rate of diamond films. Therefore, mechanical process is one of the widely used pretreatment of the matrix, which has many advantages, such as easy operation, simple equipment, high efficiency, low cost and so on. In addition, it is suitable for the most of materials of matrix, which only destroys the surface of the matrix slightly and does not has any influence on the other properties so that it has a broad prospect in medical, optics and textile dyeing industries.
Tungsten Carbide Supplier: Chinatungsten Online tungsten-carbide.com.cn | Tel.: 86 592 5129696; Fax: 86 592 5129797;Email:sales@chinatungsten.com |
Tungsten News&Tungsten Prices, 3G Version: http://3g.chinatungsten.com | Molybdenum News & Molybdenum Price: http://news.molybdenum.com.cn |